- お役立ち記事
- “Unlocking Efficiency: How Predictive Maintenance Transforms Japanese Manufacturing”
この記事は、当社の提供するお役立ち記事の一部です。詳しくは公式サイトをご覧ください。
“Unlocking Efficiency: How Predictive Maintenance Transforms Japanese Manufacturing”
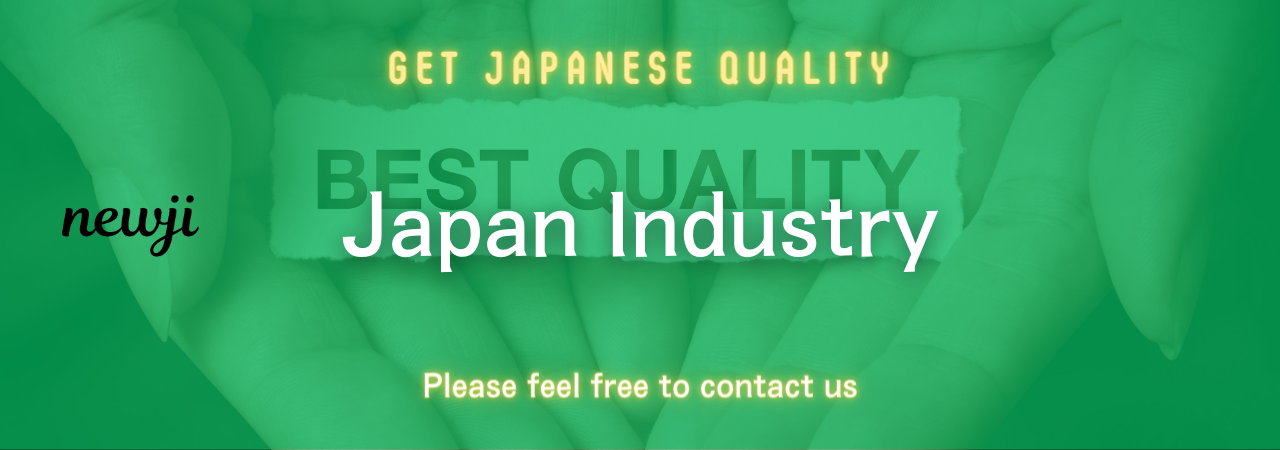
目次
Introduction to Predictive Maintenance in Japanese Manufacturing
Predictive maintenance has become a buzzword in the manufacturing industry, reflecting a significant transformation in how operations are managed.
In Japan, where manufacturing excellence is a longstanding tradition, predictive maintenance has unlocked new levels of efficiency and productivity.
This technique leverages advanced analytics and the Internet of Things (IoT) to anticipate equipment failures before they occur, thereby minimizing downtime and maximizing operational efficiency.
In this article, we’ll delve into the various aspects of predictive maintenance, its applications in Japanese manufacturing, and share insights from real-world scenarios.
The Concept of Predictive Maintenance
What is Predictive Maintenance?
Predictive maintenance is a proactive approach that uses data analytics, machine learning, and IoT technologies to predict when equipment might fail.
Unlike traditional maintenance strategies—reactive maintenance (fix it when it breaks) and preventive maintenance (regularly scheduled fixes)—predictive maintenance aims to predict and therefore prevent failures.
This method relies on sensors and advanced monitoring technologies to gather real-time data.
That data is then analyzed to identify patterns and anomalies, which can indicate potential failures.
Advantages of Predictive Maintenance
Predictive maintenance offers numerous benefits, particularly in the realm of Japanese manufacturing:
– **Reduced Downtime:** By predicting failures before they happen, maintenance can be scheduled at the most convenient times.
– **Cost Savings:** Fewer emergency repairs and extended equipment life contribute to substantial cost savings.
– **Enhanced Safety:** Early detection of issues minimizes the risk of accidents.
– **Improved Productivity:** With machines running more efficiently, output can increase without compromising quality.
Predictive Maintenance in Japanese Manufacturing
The Japanese Approach to Manufacturing Excellence
Japan is renowned for its manufacturing prowess, characterized by high-quality output, stringent quality control measures, and innovative production techniques.
Kaizen, the Japanese philosophy of continuous improvement, is deeply ingrained in the manufacturing culture.
With such an emphasis on efficiency and optimization, predictive maintenance is a natural fit for the Japanese manufacturing landscape.
Implementation of Predictive Maintenance in Japanese Factories
Japanese factories have been quick to adopt predictive maintenance, incorporating it with traditional methods such as Total Productive Maintenance (TPM) and Six Sigma.
Factories rely on a combination of sensors, data analytics platforms, and predictive algorithms to monitor machinery.
For instance, in automotive manufacturing—one of Japan’s most critical industries—predictive maintenance algorithms monitor everything from assembly line robots to engine performance.
These algorithms detect anomalies like abnormal vibration patterns or temperature spikes, prompting preemptive actions to avoid breakdowns.
Supplier Relationship in the Context of Predictive Maintenance
Importance of Supplier Collaboration
Effective predictive maintenance requires robust collaboration with suppliers.
Japanese manufacturers prioritize strong supplier relationships, often involving suppliers in the maintenance strategy.
Collaboration typically involves:
– **Data Sharing:** Providing suppliers with access to performance data can help identify and address potential issues more efficiently.
– **Joint Development:** Co-creating maintenance solutions ensures that both parties understand the equipment and its quirks.
– **Training and Support:** Suppliers often provide training to factory personnel on predictive maintenance tools and techniques.
Negotiation Techniques with Suppliers
When negotiating with suppliers on predictive maintenance, transparency and alignment on objectives are crucial.
Here are some effective negotiation techniques:
– **Clear Expectations:** Define performance expectations and maintenance requirements upfront.
– **Long-Term Contracts:** Secure long-term contracts to ensure stability and commitment from suppliers.
– **Performance-Based Incentives:** Tie incentive structures to the performance and reliability of the supplied equipment.
– **Collaborative Problem-Solving:** Foster a partnership mindset where both parties work together to resolve issues.
Challenges and Considerations
Data Management and Analysis
One of the significant challenges in predictive maintenance is managing and analyzing vast amounts of data.
Japanese manufacturers invest heavily in data infrastructure and employ data scientists to ensure accurate and actionable insights.
However, smaller companies may struggle with these resources, necessitating partnerships or outsourcing to specialized firms.
Integration with Existing Systems
Another challenge is integrating predictive maintenance systems with existing production and ERP systems.
Seamless integration is essential for leveraging predictive insights across the organization.
Adoption of open protocols and standards can facilitate smoother integration.
Contracting with technology providers experienced in the local manufacturing landscape can also ease the process.
Cybersecurity Concerns
With the increased reliance on IoT and connected devices, cybersecurity has become a pressing issue.
Japanese manufacturers must implement strong cybersecurity measures to protect sensitive data and ensure the integrity of their predictive maintenance systems.
Real-World Examples of Predictive Maintenance in Japanese Manufacturing
Automotive Industry: Toyota’s Predictive Maintenance Strategy
Toyota, a global leader in automotive manufacturing, has implemented predictive maintenance across its production lines.
By using IoT sensors and AI algorithms, Toyota can predict potential failures in assembly line robots.
This foresight allows Toyota to schedule maintenance during planned production downtimes, thereby minimizing disruptions.
Electronics Industry: Panasonic’s Approach
Panasonic has integrated predictive maintenance in its consumer electronics manufacturing facilities.
By monitoring critical parameters of soldering machines and circuit board manufacturing equipment, Panasonic ensures high-quality output and reduces the incidence of defective products.
Heavy Machinery Industry: Komatsu’s Predictive Maintenance Success
Komatsu, a major player in construction and mining equipment, utilizes predictive maintenance to monitor the health of its machinery deployed globally.
Komatsu’s predictive maintenance system gathers data from equipment sensors and uses advanced analytics to predict and prevent breakdowns.
This approach not only enhances equipment uptime but also improves customer satisfaction by ensuring reliable operation in the field.
Best Practices for Successful Predictive Maintenance
Establish a Strong Data Foundation
The effectiveness of predictive maintenance relies on high-quality data.
Manufacturers should invest in sensors and IoT devices capable of capturing accurate and relevant data.
Regular calibration and maintenance of these devices are crucial to ensure data accuracy.
Engage Stakeholders and Train Personnel
Predictive maintenance is not just a technological shift but also a cultural one.
Engage all stakeholders, including management, engineers, and operators, in the predictive maintenance journey.
Provide comprehensive training on the principles and tools of predictive maintenance to ensure its successful implementation.
Leverage Advanced Analytics
Invest in advanced analytics platforms that can process and analyze large volumes of data.
Machine learning and AI algorithms can uncover patterns that human analysts might miss, delivering more accurate predictions.
Focus on Continuous Improvement
Embrace the Kaizen philosophy of continuous improvement.
Regularly review and refine predictive maintenance strategies based on performance data and feedback.
This iterative approach will help in optimizing maintenance processes and achieving better outcomes over time.
Future Trends in Predictive Maintenance for Japanese Manufacturing
AI and Machine Learning
The future of predictive maintenance will be heavily influenced by advancements in AI and machine learning.
These technologies will enable more accurate predictions and automated decision-making, further enhancing maintenance efficiency.
Edge Computing
Edge computing, which involves processing data closer to where it is generated, will play a vital role in predictive maintenance.
By reducing latency and bandwidth requirements, edge computing ensures faster and more reliable analysis of equipment data.
Integration with Digital Twins
Digital twins—virtual replicas of physical assets—will become increasingly integrated with predictive maintenance systems.
These digital models will allow manufacturers to simulate and analyze different maintenance scenarios, leading to more informed decisions.
Sustainability Considerations
Sustainability will be a key focus in future predictive maintenance strategies.
Manufacturers will aim to reduce energy consumption and carbon emissions by optimizing equipment performance and extending the life of machinery.
Conclusion
Predictive maintenance represents a significant leap forward in the quest for manufacturing excellence.
By harnessing the power of data and advanced analytics, Japanese manufacturers can achieve unprecedented levels of efficiency, reliability, and productivity.
The successful implementation of predictive maintenance relies on a combination of technological investment, strong supplier relationships, and a culture of continuous improvement.
As the manufacturing landscape evolves, predictive maintenance will undoubtedly remain a cornerstone of Japan’s manufacturing strategy, driving innovation and maintaining its competitive edge on the global stage.
In summary, the benefits of predictive maintenance in Japanese manufacturing are clear: reduced downtime, cost savings, enhanced safety, and improved productivity.
For manufacturers and suppliers alike, embracing this transformative approach promises to unlock new levels of operational efficiency and success.
資料ダウンロード
QCD調達購買管理クラウド「newji」は、調達購買部門で必要なQCD管理全てを備えた、現場特化型兼クラウド型の今世紀最高の購買管理システムとなります。
ユーザー登録
調達購買業務の効率化だけでなく、システムを導入することで、コスト削減や製品・資材のステータス可視化のほか、属人化していた購買情報の共有化による内部不正防止や統制にも役立ちます。
NEWJI DX
製造業に特化したデジタルトランスフォーメーション(DX)の実現を目指す請負開発型のコンサルティングサービスです。AI、iPaaS、および先端の技術を駆使して、製造プロセスの効率化、業務効率化、チームワーク強化、コスト削減、品質向上を実現します。このサービスは、製造業の課題を深く理解し、それに対する最適なデジタルソリューションを提供することで、企業が持続的な成長とイノベーションを達成できるようサポートします。
オンライン講座
製造業、主に購買・調達部門にお勤めの方々に向けた情報を配信しております。
新任の方やベテランの方、管理職を対象とした幅広いコンテンツをご用意しております。
お問い合わせ
コストダウンが利益に直結する術だと理解していても、なかなか前に進めることができない状況。そんな時は、newjiのコストダウン自動化機能で大きく利益貢献しよう!
(Β版非公開)