- お役立ち記事
- “Unlocking Efficiency in Japanese Manufacturing through Innovative Multiplexing Techniques”
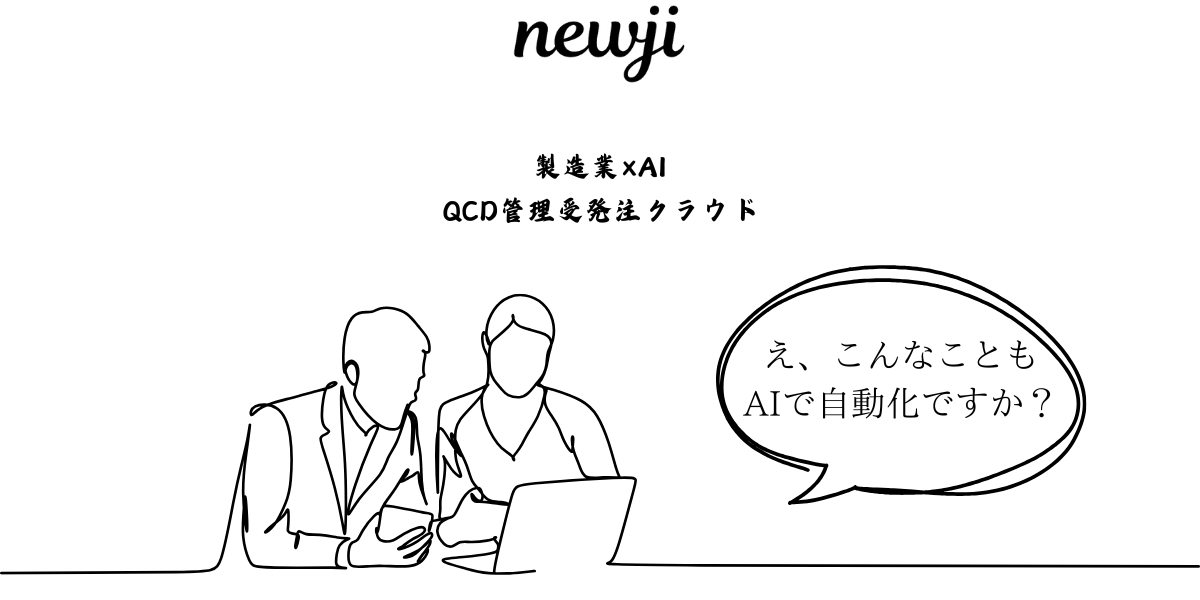
“Unlocking Efficiency in Japanese Manufacturing through Innovative Multiplexing Techniques”
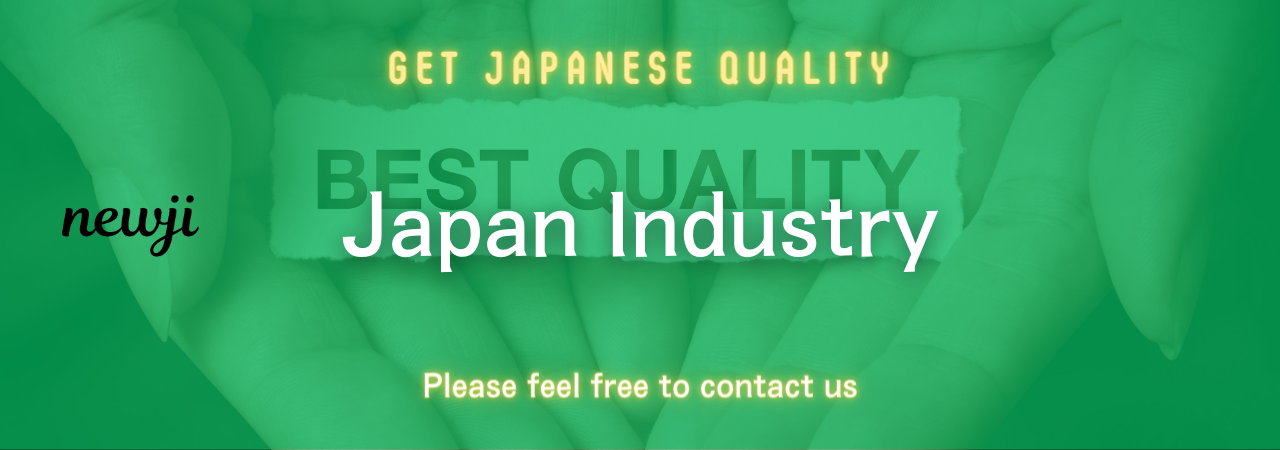
目次
Introduction
Japan has long been renowned for its proficiency in manufacturing, consistently producing high-quality goods and maintaining a dominant position in the global market.
One of the key factors behind Japan’s manufacturing success is its innovative approach to production processes, particularly through the use of multiplexing techniques.
These techniques, which involve the simultaneous handling of multiple tasks or operations, have significantly improved efficiency, reduced waste, and enhanced overall productivity.
In this article, we will explore the various facets of multiplexing techniques in Japanese manufacturing.
We will dive into practical applications, advantages and disadvantages, supplier negotiation strategies, market conditions, and best practices.
Drawing upon my extensive experience in procurement and purchasing within the international manufacturing sector, I aim to provide valuable insights that can help organizations harness the full potential of Japanese manufacturing innovations.
Understanding Multiplexing Techniques
What are Multiplexing Techniques?
Multiplexing techniques refer to the process of integrating multiple tasks or operations into a single, cohesive system.
In the context of manufacturing, this means combining various production stages, quality control processes, and assembly operations to streamline workflow and maximize efficiency.
The goal is to enhance productivity, minimize downtime, and ensure a more efficient use of resources.
There are several types of multiplexing techniques, including:
1. Time-division multiplexing (TDM): This involves dividing the production process into discrete time slots, where each task or operation is assigned a specific time interval.
2. Frequency-division multiplexing (FDM): This technique uses different frequency bands to handle multiple tasks simultaneously within the same production system.
3. Space-division multiplexing (SDM): This method involves partitioning the manufacturing space into distinct segments, each dedicated to a specific task or operation.
4. Code-division multiplexing (CDM): This approach assigns unique codes to different tasks or operations, allowing them to be concurrently managed within the same production system.
Benefits of Multiplexing Techniques
Utilizing multiplexing techniques in Japanese manufacturing offers several advantages:
1. **Improved Efficiency**: By handling multiple tasks simultaneously, production processes become more streamlined, reducing idle time and increasing overall productivity.
2. **Cost Reduction**: Multiplexing techniques can lower operational costs by minimizing resource wastage, optimizing labor utilization, and reducing energy consumption.
3. **Enhanced Quality Control**: Integrating quality control measures within the production process ensures real-time monitoring and immediate corrective action, leading to higher product quality.
4. **Flexibility and Scalability**: Multiplexing techniques provide the flexibility to adapt to changing market demands and enable easy scalability of production systems.
5. **Competitive Advantage**: Companies that effectively implement multiplexing techniques can achieve faster production cycles, quicker time-to-market, and a stronger competitive edge in the industry.
Practical Applications of Multiplexing Techniques
Automotive Manufacturing
The automotive industry in Japan has been at the forefront of implementing multiplexing techniques.
Assembly lines in leading automotive factories utilize robotic automation, time-division multiplexing, and real-time data analytics to handle multiple assembly tasks concurrently.
This results in faster production cycles, reduced human error, and improved overall vehicle quality.
Electronics Manufacturing
In the electronics industry, multiplexing techniques are employed to manage the intricate assembly processes of devices such as smartphones, tablets, and laptops.
By using space-division multiplexing, manufacturing facilities can create dedicated workstations for specific tasks like PCB assembly, soldering, and testing.
This ensures that each stage of production is optimized for efficiency and precision.
Pharmaceutical Manufacturing
Japanese pharmaceutical companies leverage code-division multiplexing to manage the complex production processes involved in drug manufacturing.
By assigning unique codes to different stages of production, such as ingredient mixing, formulation, and packaging, companies can ensure that each step is meticulously monitored and controlled.
Advantages and Disadvantages of Multiplexing Techniques
Advantages
1. **Increased Throughput**: Multiplexing allows for multiple processes to occur simultaneously, significantly boosting overall production throughput.
2. **Resource Optimization**: By integrating various tasks, resources such as labor, machinery, and materials are utilized more efficiently, reducing waste and lowering operational costs.
3. **Quality Improvement**: Real-time monitoring and immediate corrective actions ensure higher product quality and consistency.
4. **Reduced Downtime**: Multiplexing minimizes idle time between tasks, keeping production lines running smoothly and continuously.
5. **Scalability**: Production systems can be easily scaled up or down to meet changing market demands without compromising efficiency.
Disadvantages
1. **Complexity**: Implementing multiplexing techniques requires sophisticated technology and expertise, leading to increased complexity in production planning and execution.
2. **Initial Investment**: The adoption of multiplexing techniques often involves significant upfront costs for advanced machinery, software, and skilled labor.
3. **Maintenance Challenges**: Maintaining and troubleshooting multiplexing systems can be challenging, requiring specialized knowledge and resources.
4. **Dependency on Technology**: Relying heavily on technology exposes manufacturing processes to potential risks, such as system failures or cyber threats.
5. **Training Requirements**: Employees need to be adequately trained to operate and maintain multiplexing systems, which can be time-consuming and costly.
Supplier Negotiation Techniques
Building Strong Relationships
When dealing with Japanese suppliers, fostering strong, long-term relationships is crucial.
Japanese business culture places a high value on trust, loyalty, and mutual respect.
Taking the time to build rapport and establish a solid foundation will facilitate smoother negotiations and collaboration.
Communication and Transparency
Effective communication is key to successful supplier negotiations.
Ensure that all parties are on the same page by maintaining clear, transparent, and open lines of communication.
This includes sharing production schedules, technical specifications, and any potential issues that may arise during the manufacturing process.
Understanding Cultural Nuances
Being aware of and respecting cultural differences is essential when negotiating with Japanese suppliers.
For example, Japanese business culture often emphasizes consensus and group decision-making.
Be patient and demonstrate a willingness to understand and adapt to their preferences and practices.
Leverage Technology
Utilize technology to streamline negotiations and improve collaboration.
Video conferencing, project management software, and real-time data sharing can help bridge geographical gaps and ensure that all stakeholders are well-informed and aligned.
Win-Win Approach
Aim for a win-win outcome in negotiations.
Focus on finding mutually beneficial solutions that address the needs and concerns of both parties.
This approach will foster goodwill and strengthen the partnership over the long term.
Market Conditions in Japanese Manufacturing
Current Trends
Japanese manufacturing is currently experiencing several key trends:
1. **Digital Transformation**: The adoption of Industry 4.0 technologies, such as IoT, AI, and big data, is driving significant changes in manufacturing processes.
2. **Sustainability**: Environmental considerations and sustainable practices are becoming increasingly important in Japanese manufacturing, with companies striving to reduce their carbon footprint and adopt green technologies.
3. **Reshoring**: There is a growing trend towards reshoring production to Japan to mitigate risks associated with global supply chain disruptions.
4. **Robotics and Automation**: The use of advanced robotics and automation is on the rise, enhancing production efficiency and reducing labor costs.
Challenges
Despite its strengths, the Japanese manufacturing sector faces several challenges:
1. **Aging Workforce**: The aging population and shrinking labor force present significant challenges in terms of maintaining productivity and knowledge transfer.
2. **Global Competition**: Intense competition from other manufacturing powerhouses, such as China and South Korea, puts pressure on Japanese manufacturers to continually innovate and improve.
3. **Supply Chain Disruptions**: Global events, such as pandemics and geopolitical tensions, can disrupt supply chains and impact production schedules.
4. **Technological Gaps**: Some traditional manufacturers may struggle to keep up with rapid technological advancements, necessitating investment in training and upskilling.
Best Practices for Implementing Multiplexing Techniques
Conduct a Thorough Analysis
Before implementing multiplexing techniques, conduct a comprehensive analysis of your production processes.
Identify areas where multiplexing could yield the greatest benefits and assess the feasibility of integrating multiple tasks or operations.
This analysis should include a cost-benefit evaluation to ensure that the potential gains outweigh the investment required.
Invest in Technology and Training
Successful implementation of multiplexing techniques requires advanced technology and skilled labor.
Invest in state-of-the-art machinery, software, and automation tools that can support multiplexing processes.
Additionally, provide ongoing training and development for employees to ensure they have the necessary skills and knowledge to operate and maintain the new systems.
Implement Gradually
Introducing multiplexing techniques should be done gradually to minimize disruption and ensure a smooth transition.
Start with pilot projects or small-scale implementations to test the effectiveness of the techniques and identify any potential issues.
Once the pilot projects have proven successful, gradually scale up the implementation across the entire production system.
Monitor and Optimize
Continuous monitoring and optimization are essential for maximizing the benefits of multiplexing techniques.
Utilize real-time data analytics to track performance, identify bottlenecks, and make data-driven decisions.
Regularly review and refine the processes to ensure they remain efficient and aligned with organizational goals.
Foster a Culture of Innovation
Encourage a culture of innovation within your organization to drive continuous improvement and embrace new technologies.
Empower employees to contribute ideas and solutions for enhancing production efficiency and overcoming challenges.
By fostering a collaborative and forward-thinking environment, you can stay ahead of industry trends and maintain a competitive edge.
Conclusion
Multiplexing techniques have revolutionized Japanese manufacturing by significantly enhancing efficiency, reducing costs, and improving product quality.
While there are challenges associated with their implementation, the potential benefits far outweigh the drawbacks.
By understanding the intricacies of multiplexing techniques, leveraging effective supplier negotiation strategies, and staying attuned to market conditions, organizations can unlock new levels of efficiency and competitiveness.
Drawing on my extensive experience in the field, I hope this article has provided valuable insights and practical guidance for harnessing the power of Japanese manufacturing innovations through multiplexing techniques.
By embracing these best practices and continuously striving for improvement, organizations can achieve sustained success in an increasingly competitive global market.
資料ダウンロード
QCD調達購買管理クラウド「newji」は、調達購買部門で必要なQCD管理全てを備えた、現場特化型兼クラウド型の今世紀最高の購買管理システムとなります。
ユーザー登録
調達購買業務の効率化だけでなく、システムを導入することで、コスト削減や製品・資材のステータス可視化のほか、属人化していた購買情報の共有化による内部不正防止や統制にも役立ちます。
NEWJI DX
製造業に特化したデジタルトランスフォーメーション(DX)の実現を目指す請負開発型のコンサルティングサービスです。AI、iPaaS、および先端の技術を駆使して、製造プロセスの効率化、業務効率化、チームワーク強化、コスト削減、品質向上を実現します。このサービスは、製造業の課題を深く理解し、それに対する最適なデジタルソリューションを提供することで、企業が持続的な成長とイノベーションを達成できるようサポートします。
オンライン講座
製造業、主に購買・調達部門にお勤めの方々に向けた情報を配信しております。
新任の方やベテランの方、管理職を対象とした幅広いコンテンツをご用意しております。
お問い合わせ
コストダウンが利益に直結する術だと理解していても、なかなか前に進めることができない状況。そんな時は、newjiのコストダウン自動化機能で大きく利益貢献しよう!
(Β版非公開)