- お役立ち記事
- Unlocking Efficiency: The Art of Japanese Manufacturing Material Management
月間77,185名の
製造業ご担当者様が閲覧しています*
*2025年2月28日現在のGoogle Analyticsのデータより
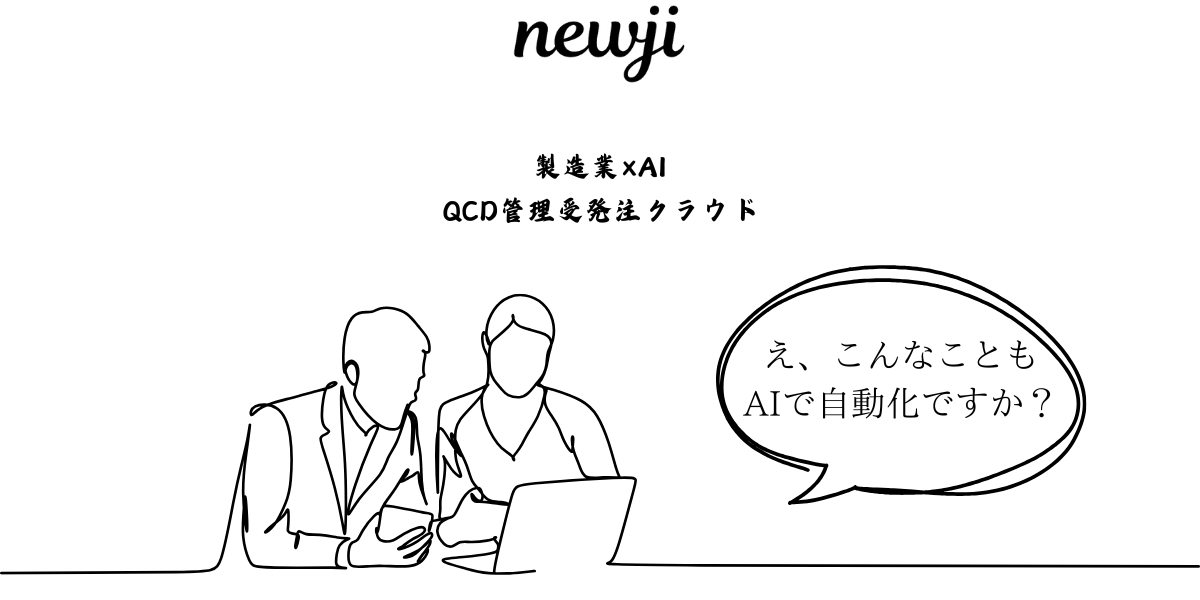
Unlocking Efficiency: The Art of Japanese Manufacturing Material Management
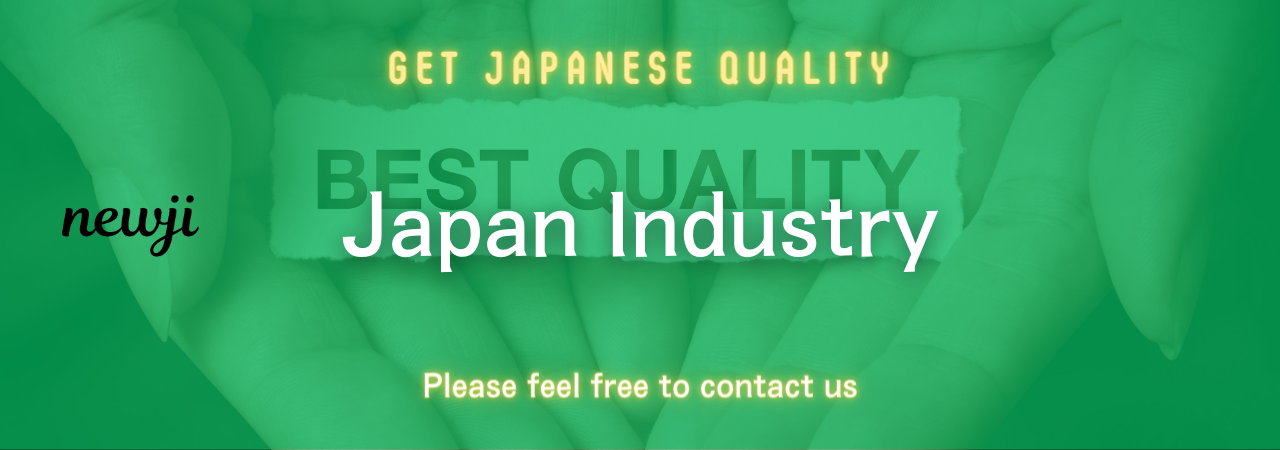
目次
Understanding Japanese Manufacturing Excellence
Japanese manufacturing is renowned globally for its precision, efficiency, and quality.
At the heart of this success lies sophisticated material management practices.
These practices ensure that production processes are streamlined, costs are minimized, and product quality is maintained at the highest standards.
The Philosophy Behind Japanese Material Management
Japanese manufacturing emphasizes continuous improvement, known as *Kaizen*.
This philosophy encourages ongoing enhancements in all aspects of production.
Material management is no exception, focusing on eliminating waste, optimizing inventory, and ensuring timely procurement of materials.
Key Components of Japanese Material Management
Effective material management in Japanese manufacturing encompasses several critical components.
These include procurement strategies, inventory control, supplier relationships, and logistics optimization.
Strategic Procurement Practices
Strategic procurement is central to Japanese material management.
It involves selecting suppliers who can consistently deliver high-quality materials at competitive prices.
Japanese companies often engage in long-term partnerships with their suppliers, fostering mutual trust and collaboration.
Inventory Control Techniques
Inventory control in Japanese manufacturing is characterized by minimal stock levels.
Techniques like Just-In-Time (JIT) inventory ensure that materials arrive precisely when needed.
This reduces storage costs and minimizes the risk of overstocking or obsolescence.
Supplier Relationship Management
Maintaining strong relationships with suppliers is crucial.
Japanese companies often integrate their suppliers into their production processes.
This collaboration leads to better communication, quicker problem resolution, and joint innovation initiatives.
Logistics and Supply Chain Optimization
Efficient logistics are vital for timely material delivery.
Japanese manufacturers invest in robust supply chain management systems that track materials from suppliers to the production floor.
This visibility ensures that any disruptions are promptly addressed, maintaining the flow of production.
Advantages of Japanese Material Management
Adopting Japanese material management practices offers numerous benefits.
These include enhanced efficiency, reduced costs, improved quality, and greater flexibility in production processes.
Enhanced Efficiency
Streamlined material management processes lead to significant efficiency gains.
Reduced waste and optimized inventory levels ensure that resources are utilized effectively.
This efficiency translates into faster production cycles and quicker time-to-market.
Cost Reduction
Minimal inventory levels and strategic procurement contribute to cost savings.
By avoiding excess stock, companies reduce storage and handling costs.
Moreover, long-term supplier relationships can result in better pricing and favorable terms.
Improved Quality
Consistent material quality is a hallmark of Japanese manufacturing.
Strict quality control measures and close supplier collaboration ensure that only top-grade materials are used in production.
This commitment to quality enhances the overall product reputation and customer satisfaction.
Greater Flexibility
Japanese material management practices allow for greater flexibility in responding to market changes.
The ability to quickly adjust material orders and production schedules enables companies to adapt to fluctuations in demand without compromising on quality or efficiency.
Challenges in Implementing Japanese Material Management
While Japanese material management practices offer significant advantages, there are challenges in adopting these methods, especially for companies operating in different cultural and operational environments.
Cultural Differences
The success of Japanese material management is deeply rooted in its cultural context.
Implementing similar practices in different cultures may require adjustments to accommodate varying work ethics, communication styles, and business practices.
Initial Implementation Costs
Transitioning to Japanese-style material management may involve initial costs related to training, system upgrades, and process reengineering.
These upfront investments can be a barrier for some companies, particularly smaller enterprises.
Supplier Alignment
Achieving the level of supplier collaboration seen in Japanese manufacturing can be challenging.
Suppliers may need to adjust their processes and operational standards to align with the expectations of Japanese-style material management.
Effective Supplier Negotiation Techniques
Negotiating with suppliers is a critical aspect of material management.
Japanese companies employ specific techniques to secure favorable terms and foster strong supplier relationships.
Building Long-Term Relationships
Japanese firms prioritize long-term relationships over short-term gains.
This approach builds trust and reliability, encouraging suppliers to provide better terms and prioritize the company’s needs.
Transparent Communication
Open and honest communication is fundamental.
Japanese companies share their production plans, forecasts, and quality expectations with suppliers, fostering a collaborative environment.
Mutual Benefits
Negotiations focus on creating win-win scenarios.
By ensuring that both parties benefit, Japanese firms enhance supplier loyalty and motivation to maintain high standards.
Flexibility and Adaptability
Being flexible in negotiations allows for adjustments based on changing circumstances.
Japanese companies are willing to adapt terms and processes to accommodate supplier capabilities and market conditions.
Market Conditions Influencing Japanese Material Management
Understanding market conditions is essential for effective material management.
Japanese manufacturers closely monitor market trends, economic indicators, and technological advancements to inform their procurement and production strategies.
Economic Stability
Economic stability provides a predictable environment for material management.
Japanese manufacturers leverage stable economic conditions to plan long-term procurement and production schedules.
Technological Advancements
Embracing technology is key to maintaining competitive advantage.
Japanese companies invest in advanced materials management systems and automation to enhance efficiency and accuracy.
Global Supply Chain Dynamics
Global supply chain dynamics, including geopolitical factors and international trade policies, impact material management.
Japanese manufacturers develop strategies to mitigate risks associated with supply chain disruptions and ensure the continuity of material supply.
Best Practices in Japanese Material Management
Implementing best practices from Japanese material management can lead to significant improvements in procurement and purchasing processes.
Adopting Just-In-Time (JIT) Inventory
JIT inventory minimizes waste and reduces storage costs by ensuring that materials are delivered exactly when needed.
Implementing JIT requires precise coordination with suppliers and robust logistics systems.
Embracing Lean Manufacturing Principles
Lean manufacturing focuses on eliminating non-value-added activities.
By adopting lean principles, companies can streamline their material management processes, enhance efficiency, and reduce costs.
Implementing Total Quality Management (TQM)
TQM ensures that quality is maintained at every stage of the material management process.
This comprehensive approach involves continuous monitoring, employee training, and collaborative problem-solving.
Investing in Advanced Technology
Utilizing advanced technologies such as Enterprise Resource Planning (ERP) systems and automation tools can significantly enhance material management efficiency.
These technologies provide real-time visibility into inventory levels, supplier performance, and production schedules.
Case Studies: Success Stories in Japanese Material Management
Examining real-world examples provides valuable insights into the effectiveness of Japanese material management practices.
Toyota Production System
The Toyota Production System (TPS) is a benchmark in material management.
TPS integrates JIT inventory, lean manufacturing, and continuous improvement to achieve unparalleled efficiency and quality levels.
Panasonic’s Supplier Integration
Panasonic excels in supplier integration, collaboratively developing materials and processes with its suppliers.
This approach has resulted in reduced lead times, improved material quality, and increased innovation.
Honda’s Flexible Production Strategy
Honda employs a flexible production strategy that allows for quick adjustments in material orders and production schedules.
This flexibility has enabled Honda to respond swiftly to market changes and maintain a competitive edge.
Implementing Japanese Material Management in Your Organization
Adopting Japanese material management practices requires a strategic approach and commitment across the organization.
Assessing Current Processes
Begin by evaluating existing material management processes.
Identify areas of inefficiency, waste, and opportunities for improvement.
Training and Development
Invest in training programs to educate employees about Japanese material management principles.
Encourage a culture of continuous improvement and collaboration.
Building Strong Supplier Relationships
Foster long-term partnerships with suppliers.
Communicate openly, set clear expectations, and work collaboratively to achieve mutual goals.
Leveraging Technology
Implement advanced material management systems to enhance visibility and control.
Utilize data analytics to make informed decisions and optimize inventory levels.
Continuous Improvement
Adopt a Kaizen mindset, continually seeking ways to enhance material management processes.
Regularly review performance metrics and implement incremental improvements.
Conclusion
Japanese manufacturing material management offers a robust framework for enhancing efficiency, reducing costs, and maintaining high-quality standards.
By embracing strategic procurement, effective inventory control, strong supplier relationships, and advanced logistics, companies can unlock significant benefits.
While challenges exist, the adoption of Japanese best practices, supported by a culture of continuous improvement and technological investment, can lead to sustained success in the competitive global manufacturing landscape.
資料ダウンロード
QCD管理受発注クラウド「newji」は、受発注部門で必要なQCD管理全てを備えた、現場特化型兼クラウド型の今世紀最高の受発注管理システムとなります。
ユーザー登録
受発注業務の効率化だけでなく、システムを導入することで、コスト削減や製品・資材のステータス可視化のほか、属人化していた受発注情報の共有化による内部不正防止や統制にも役立ちます。
NEWJI DX
製造業に特化したデジタルトランスフォーメーション(DX)の実現を目指す請負開発型のコンサルティングサービスです。AI、iPaaS、および先端の技術を駆使して、製造プロセスの効率化、業務効率化、チームワーク強化、コスト削減、品質向上を実現します。このサービスは、製造業の課題を深く理解し、それに対する最適なデジタルソリューションを提供することで、企業が持続的な成長とイノベーションを達成できるようサポートします。
製造業ニュース解説
製造業、主に購買・調達部門にお勤めの方々に向けた情報を配信しております。
新任の方やベテランの方、管理職を対象とした幅広いコンテンツをご用意しております。
お問い合わせ
コストダウンが利益に直結する術だと理解していても、なかなか前に進めることができない状況。そんな時は、newjiのコストダウン自動化機能で大きく利益貢献しよう!
(β版非公開)