- お役立ち記事
- Unlocking Efficiency: Understanding “Production Lead Time” in Japanese Manufacturing
月間76,176名の
製造業ご担当者様が閲覧しています*
*2025年3月31日現在のGoogle Analyticsのデータより
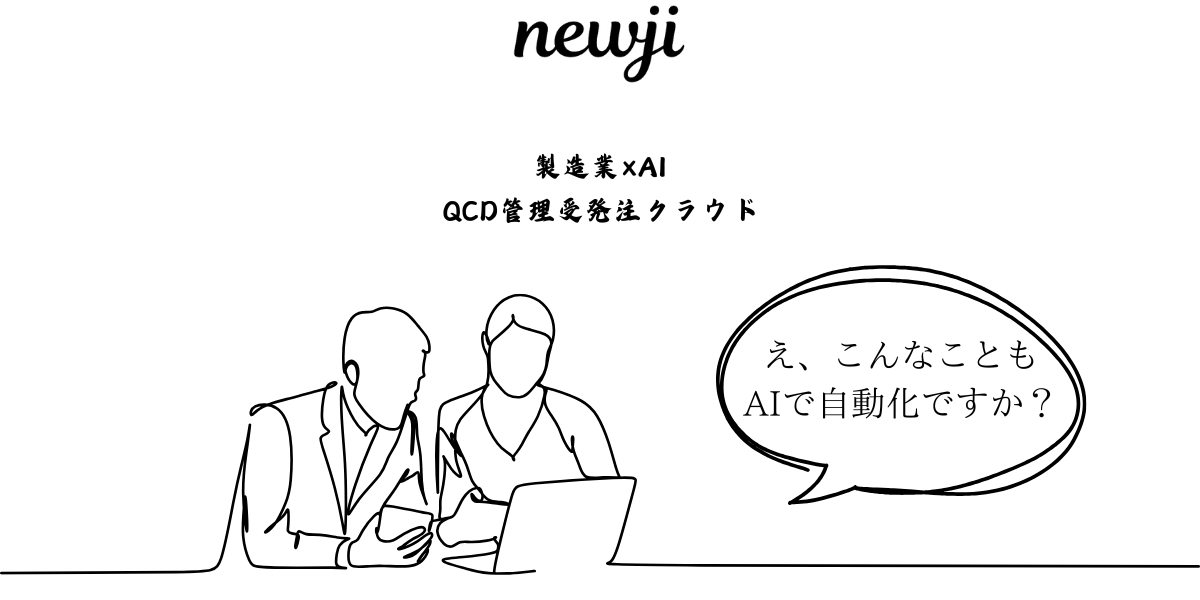
Unlocking Efficiency: Understanding “Production Lead Time” in Japanese Manufacturing
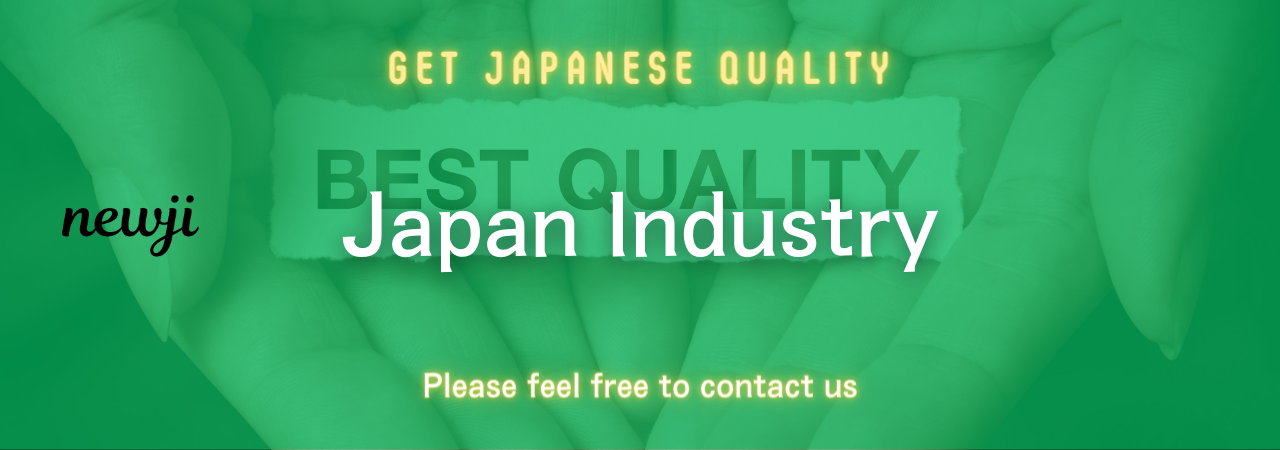
目次
Introduction to Production Lead Time
Production lead time is a fundamental concept in manufacturing that refers to the period required to manufacture a product from the initial stage of design and order placement to the final step of production and delivery.
Understanding production lead time is essential for effective supply chain management, optimizing production processes, and ensuring timely product delivery.
In Japanese manufacturing, this concept is not only meticulously measured but also continuously optimized to uphold the highest standards of efficiency and quality.
The Importance of Production Lead Time in Japanese Manufacturing
Japanese manufacturing stands out for its emphasis on precision, timeliness, and quality.
Production lead time in this context is a vital metric that impacts overall productivity, customer satisfaction, inventory management, and operational costs.
Reducing production lead time can lead to quicker turnarounds, lower holding costs, and greater responsiveness to market demands.
Conversely, extended lead times can result in missed opportunities and increased inventory expenses.
Thus, effective management of production lead time is crucial for maintaining a competitive edge.
Components of Production Lead Time
Understanding production lead time in Japanese manufacturing requires dissecting its various components:
1. Order Processing Time
This includes the time taken to process a customer’s order from the moment it is received.
In Japanese companies, this phase is often streamlined with the use of sophisticated order management systems that ensure accuracy and speed.
2. Manufacturing Lead Time
This is the core of production lead time and involves the period spent on actual manufacturing activities.
In Japanese manufacturing, this segment is continuously analyzed for potential improvements using methodologies like Kaizen (continuous improvement) and Jidoka (automation with a human touch).
3. Quality Control Time
Quality control is pivotal in Japanese manufacturing.
Every product undergoes rigorous inspections and tests to meet stringent quality standards.
While this ensures high-quality output, it also adds to the lead time.
Efficient quality control practices are essential to maintain a balance.
4. Assembly and Packaging Time
Once the product passes quality control, it moves to assembly and packaging.
In Japan, these processes are often highly automated but still require careful oversight to ensure consistency and quality.
5. Transportation and Delivery Time
Finally, the product is transported and delivered to the customer.
Japanese manufacturers often partner with reliable logistics providers to ensure timely delivery.
Advanced logistics planning and the use of real-time tracking systems further enhance efficiency.
Advantages of Japanese Production Lead Time Management
Japanese manufacturers’ approach to managing production lead time offers several distinct advantages:
1. Superior Quality Control
Japanese companies are renowned for their commitment to quality.
Effective lead time management ensures that every product undergoes thorough QC checks without unnecessary delays.
This results in fewer defects and higher customer satisfaction.
2. Enhanced Efficiency
By breaking down the production lead time into its components and continuously optimizing each part, Japanese manufacturers achieve higher levels of efficiency.
Techniques such as Just-In-Time (JIT) and lean manufacturing minimize waste and maximize productivity.
3. Competitive Edge
Shorter production lead times allow Japanese companies to respond swiftly to market demands and customer needs.
This agility provides a competitive advantage, especially in industries where product lifecycles are short.
4. Cost Reduction
Effective lead time management reduces holding costs and minimizes the risk of overproduction and excess inventory.
This contributes to overall cost savings and boosts profitability.
5. Innovation and Continuous Improvement
Japanese manufacturing’s focus on continuous improvement ensures that production processes are constantly refined.
This culture of innovation not only shortens lead times but also adapts to emerging technologies and methodologies.
Challenges and Disadvantages
Though Japanese manufacturing practices are exemplary, they also face certain challenges:
1. High Initial Investment
Implementing advanced systems for lead time management often requires significant upfront investment.
This includes the cost of technology, training, and infrastructure.
2. Complexity in Implementation
The intricacies of Japanese quality control and efficiency methodologies can make implementation complex.
Companies need to commit to continuous learning and adaptation.
3. Dependence on Supplier Reliability
Short lead times are achievable only if suppliers are equally reliable and efficient.
This dependence necessitates strong partnerships and thorough vetting processes.
4. Limited Flexibility
While optimizing for efficiency, there can sometimes be a trade-off with flexibility.
Highly streamlined processes may struggle to adapt to sudden, unforeseen changes in demand.
Best Practices for Managing Production Lead Time
Several best practices can enhance lead time management in Japanese manufacturing:
1. Lean Manufacturing
Adopt lean manufacturing principles to minimize waste and enhance efficiency.
Techniques like 5S (Sort, Set in order, Shine, Standardize, Sustain) and Kanban (visual workflow management) are integral.
2. Use of Technology
Leverage advanced technologies such as ERP (Enterprise Resource Planning) systems for real-time monitoring and control.
Automation and AI-driven analytics can predict bottlenecks and optimize workflows.
3. Continuous Improvement (Kaizen)
Foster a culture of continuous improvement.
Encourage employees at all levels to identify inefficiencies and propose solutions.
4. Effective Supplier Management
Develop strong relationships with suppliers.
Use Vendor Managed Inventory (VMI) programs and regular audits to ensure suppliers meet quality and timeliness standards.
5. Comprehensive Training Programs
Invest in training programs that educate employees about the importance of lead time management and the techniques used.
Well-trained staff can identify issues early and contribute to smoother operations.
Techniques for Negotiating with Japanese Suppliers
Building and maintaining strong relationships with Japanese suppliers are critical for managing production lead time effectively:
1. Cultural Understanding
Respect and understand Japanese business culture.
Hierarchical respect, patience, and politeness are essential.
This fosters trust and smooth communication.
2. Clear Communication
Ensure all communications are clear and precise.
Language barriers can cause misunderstandings.
Using bilingual staff or professional translation services can be advantageous.
3. Focus on Long-Term Relationships
Building long-term relationships is highly valued in Japan.
Show commitment to a lasting partnership rather than seeking short-term gains.
4. Emphasize Quality and Reliability
Japanese suppliers prioritize quality and reliability.
Negotiate on these terms, emphasizing mutual benefits and shared standards.
5. Regular Visits and Audits
Conduct regular visits and audits to understand suppliers’ operations better.
Face-to-face meetings in Japan can build stronger relationships and resolve issues efficiently.
Adapting to Market Conditions
Understanding and adapting to market conditions is essential:
1. Stay Informed
Keep abreast of market trends, economic conditions, and technological advancements.
Subscribe to industry publications and participate in relevant trade shows.
2. Flexibility in Planning
Maintain flexibility in production scheduling and inventory management.
This allows for quick adjustments to changes in market demand.
3. Risk Management
Implement robust risk management strategies.
Identify potential disruptions and plan contingencies to mitigate adverse impacts on lead times.
Conclusion
Production lead time is a critical component of Japanese manufacturing that embodies the principles of precision, efficiency, and quality.
Through effective management and optimization of lead time, Japanese manufacturers ensure superior product quality, cost efficiency, and customer satisfaction.
While there are challenges in implementing these methodologies, the benefits far outweigh the hurdles.
Companies worldwide can unlock substantial improvements by learning from and adapting Japanese best practices in production lead time management.
Understanding this aspect of Japanese manufacturing not only provides a competitive edge but also paves the way for sustained growth and innovation in the global marketplace.
With the right strategies and a commitment to continuous improvement, any manufacturer can achieve remarkable success.
資料ダウンロード
QCD管理受発注クラウド「newji」は、受発注部門で必要なQCD管理全てを備えた、現場特化型兼クラウド型の今世紀最高の受発注管理システムとなります。
ユーザー登録
受発注業務の効率化だけでなく、システムを導入することで、コスト削減や製品・資材のステータス可視化のほか、属人化していた受発注情報の共有化による内部不正防止や統制にも役立ちます。
NEWJI DX
製造業に特化したデジタルトランスフォーメーション(DX)の実現を目指す請負開発型のコンサルティングサービスです。AI、iPaaS、および先端の技術を駆使して、製造プロセスの効率化、業務効率化、チームワーク強化、コスト削減、品質向上を実現します。このサービスは、製造業の課題を深く理解し、それに対する最適なデジタルソリューションを提供することで、企業が持続的な成長とイノベーションを達成できるようサポートします。
製造業ニュース解説
製造業、主に購買・調達部門にお勤めの方々に向けた情報を配信しております。
新任の方やベテランの方、管理職を対象とした幅広いコンテンツをご用意しております。
お問い合わせ
コストダウンが利益に直結する術だと理解していても、なかなか前に進めることができない状況。そんな時は、newjiのコストダウン自動化機能で大きく利益貢献しよう!
(β版非公開)