- お役立ち記事
- Unlocking Innovation: How Japanese Manufacturing Revolutionizes with Chimeric Sound Identification Systems
Unlocking Innovation: How Japanese Manufacturing Revolutionizes with Chimeric Sound Identification Systems
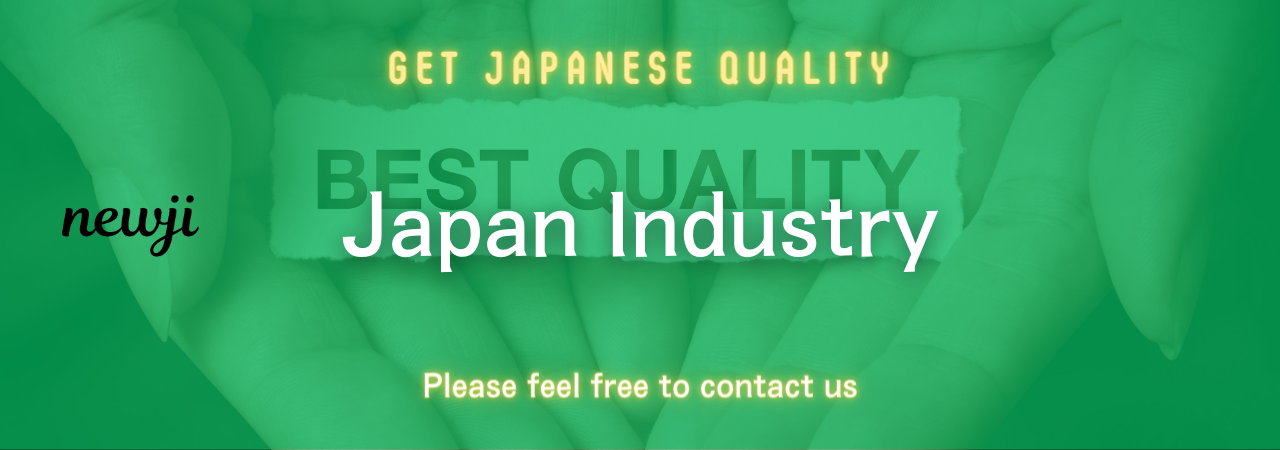
目次
Introduction to Chimeric Sound Identification Systems in Japanese Manufacturing
Japanese manufacturing has long been synonymous with precision, efficiency, and innovation. One of the latest advancements driving this reputation is the integration of Chimeric Sound Identification Systems (CSIS). These systems represent a fusion of cutting-edge technology and traditional manufacturing excellence, revolutionizing how factories operate and enhance their procurement and purchasing processes.
The Role of Chimeric Sound Identification Systems in Modern Manufacturing
Chimeric Sound Identification Systems leverage advanced auditory technologies to monitor and control manufacturing processes. By analyzing sound patterns emitted by machinery, these systems can detect anomalies, predict maintenance needs, and optimize production workflows. This proactive approach not only minimizes downtime but also ensures consistent product quality.
Enhancing Quality Control
Quality control is paramount in manufacturing, and CSIS significantly improve this aspect by providing real-time feedback on production lines. Sound analysis allows for the immediate identification of defects, enabling swift corrective actions. This results in higher product standards and reduced waste, contributing to both economic and environmental sustainability.
Optimizing Production Efficiency
Efficiency is a core objective in manufacturing, and Chimeric Sound Identification Systems play a crucial role in achieving it. By continuously monitoring machinery sounds, these systems can identify inefficiencies and suggest adjustments. This leads to streamlined operations, reduced energy consumption, and improved overall productivity.
Procurement and Purchasing: Leveraging CSIS for Strategic Advantage
In the realm of procurement and purchasing, CSIS offer unique advantages that can transform supply chain management. Japanese manufacturers have effectively integrated these systems to enhance their procurement strategies, leading to more informed decision-making and stronger supplier relationships.
Data-Driven Decision Making
CSIS provide valuable data that informs procurement strategies. By analyzing sound patterns, procurement managers can gain insights into supplier performance, machinery health, and production capabilities. This data-driven approach ensures that purchasing decisions are based on concrete evidence rather than intuition, leading to more reliable and efficient supply chains.
Strengthening Supplier Relationships
Effective supplier negotiation is essential for maintaining strong partnerships. CSIS enable manufacturers to monitor supplier performance accurately, providing a basis for constructive discussions and negotiations. This transparency fosters trust and collaboration, resulting in mutually beneficial relationships that drive continuous improvement and innovation.
Advantages of Implementing Chimeric Sound Identification Systems
Adopting Chimeric Sound Identification Systems offers numerous benefits that enhance manufacturing operations and procurement processes.
Predictive Maintenance
One of the standout advantages of CSIS is their ability to facilitate predictive maintenance. By detecting unusual sound patterns early, these systems predict potential machinery failures before they occur. This proactive maintenance approach reduces unexpected downtime, extends machinery lifespan, and lowers maintenance costs.
Improved Product Quality
Consistent and high-quality products are essential for maintaining a competitive edge. CSIS contribute to this by ensuring that all machinery operates optimally, minimizing variations that could lead to defects. The resulting stable production environment upholds product integrity and customer satisfaction.
Cost Savings
The integration of CSIS can lead to significant cost savings across various aspects of manufacturing. Reduced downtime, lower maintenance expenses, and minimized waste all contribute to a more cost-effective production process. Additionally, enhanced efficiency leads to better resource utilization, further driving down operational costs.
Enhanced Safety
Safety is a critical concern in manufacturing environments. CSIS help identify potentially hazardous conditions by monitoring unusual sounds that may indicate equipment malfunctions. Early detection of these issues allows for prompt intervention, reducing the risk of accidents and ensuring a safer workplace for all employees.
Challenges and Considerations in Implementing CSIS
While the benefits of Chimeric Sound Identification Systems are substantial, manufacturers must also navigate certain challenges during implementation.
Initial Investment and Costs
The upfront costs associated with acquiring and integrating CSIS can be significant. This includes not only the purchase of the necessary hardware and software but also the training of personnel to effectively utilize the systems. Manufacturers must carefully assess the return on investment to ensure that the long-term benefits justify the initial expenditures.
Integration with Existing Systems
Seamlessly integrating CSIS with existing manufacturing and procurement systems can be complex. Compatibility issues may arise, requiring additional customization or upgrades. A thorough evaluation of current infrastructure and careful planning are essential to mitigate integration challenges.
Data Management and Security
The extensive data generated by CSIS necessitates robust data management practices. Manufacturers must implement secure storage solutions and establish protocols for data analysis and access. Protecting sensitive information is paramount to prevent data breaches and maintain trust with suppliers and customers.
Training and Skill Development
Effective utilization of CSIS requires specialized knowledge and skills. Manufacturers must invest in training programs to equip their workforce with the necessary expertise. Ongoing education and support are also essential to keep up with technological advancements and ensure sustained system effectiveness.
Best Practices for Maximizing the Benefits of CSIS
To fully capitalize on the advantages of Chimeric Sound Identification Systems, manufacturers should adopt best practices that enhance system performance and integration.
Comprehensive Planning and Assessment
Begin by conducting a thorough assessment of current manufacturing processes and procurement strategies. Identify specific areas where CSIS can add value and develop a detailed implementation plan. Comprehensive planning ensures that the integration of CSIS aligns with overall business objectives and addresses key operational needs.
Collaboration with Suppliers
Engage suppliers early in the implementation process. Collaborative efforts can lead to better alignment of systems and processes, ensuring that both parties benefit from the technology. Open communication and joint problem-solving foster stronger partnerships and drive mutual success.
Continuous Monitoring and Evaluation
Implementing CSIS is not a one-time event but an ongoing process. Continuously monitor system performance and evaluate its impact on manufacturing and procurement operations. Regular assessments enable manufacturers to make informed adjustments, optimize system settings, and address any emerging issues promptly.
Investing in Training and Development
Prioritize the training and development of employees to ensure they are proficient in using CSIS. Provide ongoing educational opportunities to keep the workforce updated on the latest technological advancements and best practices. A knowledgeable and skilled team is crucial for maximizing the effectiveness of CSIS.
Embracing Technological Advancements
Stay abreast of new developments in sound identification technology and related fields. Embracing advancements allows manufacturers to enhance their CSIS capabilities, maintain a competitive edge, and continuously improve their manufacturing and procurement processes.
Supplier Negotiation Techniques Enhanced by CSIS
Chimeric Sound Identification Systems provide unique leverage in supplier negotiations by offering objective data on supplier performance and machinery efficiency.
Data-Driven Negotiations
Utilize the data collected by CSIS to inform negotiation strategies. Objective evidence of supplier performance can be used to negotiate better terms, discounts, or improvements in service quality. Data-driven negotiations are more effective and foster fairness and transparency in supplier relationships.
Performance Benchmarking
Establish performance benchmarks based on CSIS data to evaluate supplier capabilities. Use these benchmarks to compare different suppliers objectively, ensuring that negotiations are based on clear and measurable criteria. Benchmarking promotes healthy competition and encourages suppliers to meet or exceed performance standards.
Collaborative Problem Solving
When issues arise, use the insights from CSIS to engage suppliers in collaborative problem-solving. Discussing specific data points can help identify root causes and develop joint solutions. This cooperative approach strengthens partnerships and leads to sustainable improvements in the supply chain.
Long-Term Partnership Building
Leverage the transparency provided by CSIS to build long-term partnerships with suppliers. Consistent data sharing and mutual understanding of performance metrics create a foundation of trust and reliability. Long-term partnerships are beneficial for both parties, fostering stability and continuous innovation.
Market Conditions and the Adoption of CSIS in Japan
Japan’s manufacturing sector operates within a dynamic market environment that drives the adoption of innovative technologies like Chimeric Sound Identification Systems.
Competitive Landscape
The intense competition in Japanese manufacturing necessitates continuous innovation and efficiency improvements. CSIS offer a strategic advantage by enhancing production quality and operational efficiency, helping manufacturers stay ahead in a highly competitive market.
Technological Leadership
Japan is a global leader in technological advancements, and the adoption of CSIS aligns with this reputation. Embracing such cutting-edge systems reinforces Japan’s position as an innovator and attracts international partners seeking high-quality manufacturing solutions.
Global Supply Chain Integration
As global supply chains become more interconnected, the need for advanced procurement and purchasing systems grows. CSIS facilitate seamless integration by providing accurate data and fostering transparent supplier relationships, essential for managing complex international supply chains.
Regulatory Environment
Japanese manufacturing is subject to stringent quality and safety regulations. CSIS help manufacturers comply with these standards by ensuring consistent product quality and safe operating conditions. Adherence to regulatory requirements is critical for maintaining market access and reputation.
Case Studies: Success Stories of CSIS Implementation in Japanese Manufacturing
Examining real-world examples of CSIS implementation highlights their transformative impact on Japanese manufacturing operations.
Automotive Industry
A leading Japanese automotive manufacturer integrated CSIS into its production lines to monitor engine assembly processes. The system detected subtle variations in sound patterns, enabling early identification of component misalignments. As a result, the manufacturer reduced assembly defects by 15% and enhanced overall vehicle reliability.
Electronics Manufacturing
In the electronics sector, a prominent manufacturer adopted CSIS to oversee soldering stations. The system’s ability to detect irregularities in soldering sounds allowed for immediate adjustments, reducing product rework by 20% and increasing production throughput without compromising quality.
Precision Machinery
A Japanese precision machinery company implemented CSIS to monitor CNC machines. The system provided detailed insights into machine performance, facilitating predictive maintenance and preventing unexpected downtimes. This led to a 25% improvement in machine utilization and significant cost savings in maintenance operations.
Future Trends: The Evolution of CSIS in Japanese Manufacturing
The future of Chimeric Sound Identification Systems in Japanese manufacturing is poised for continued growth and innovation.
Integration with Artificial Intelligence
Advancements in artificial intelligence (AI) will enhance the capabilities of CSIS, enabling more accurate sound analysis and predictive analytics. AI-driven CSIS can learn from historical data, improve anomaly detection, and provide deeper insights into manufacturing processes.
IoT and Connectivity
The Internet of Things (IoT) will further integrate CSIS into the broader manufacturing ecosystem. Enhanced connectivity will allow for real-time data sharing across various systems, facilitating comprehensive monitoring and more informed decision-making throughout the supply chain.
Customization and Scalability
Future CSIS will offer greater customization and scalability to meet the diverse needs of different manufacturing sectors. Flexible systems can be tailored to specific applications, ensuring that manufacturers of all sizes can benefit from the advanced sound identification capabilities.
Sustainable Manufacturing
CSIS will play a vital role in sustainable manufacturing practices by optimizing resource usage and minimizing waste. By ensuring efficient operations and reducing defects, these systems contribute to environmentally responsible production methods and support sustainability goals.
Conclusion: Embracing Innovation with Chimeric Sound Identification Systems
Chimeric Sound Identification Systems represent a significant leap forward in Japanese manufacturing, offering unparalleled benefits in quality control, efficiency, and procurement strategies. By adopting CSIS, manufacturers can unlock new levels of innovation, strengthen supplier relationships, and maintain a competitive edge in the global market. As technology continues to evolve, the integration of CSIS will remain a cornerstone of advanced manufacturing practices, driving sustained growth and excellence in the industry.
資料ダウンロード
QCD調達購買管理クラウド「newji」は、調達購買部門で必要なQCD管理全てを備えた、現場特化型兼クラウド型の今世紀最高の購買管理システムとなります。
ユーザー登録
調達購買業務の効率化だけでなく、システムを導入することで、コスト削減や製品・資材のステータス可視化のほか、属人化していた購買情報の共有化による内部不正防止や統制にも役立ちます。
NEWJI DX
製造業に特化したデジタルトランスフォーメーション(DX)の実現を目指す請負開発型のコンサルティングサービスです。AI、iPaaS、および先端の技術を駆使して、製造プロセスの効率化、業務効率化、チームワーク強化、コスト削減、品質向上を実現します。このサービスは、製造業の課題を深く理解し、それに対する最適なデジタルソリューションを提供することで、企業が持続的な成長とイノベーションを達成できるようサポートします。
オンライン講座
製造業、主に購買・調達部門にお勤めの方々に向けた情報を配信しております。
新任の方やベテランの方、管理職を対象とした幅広いコンテンツをご用意しております。
お問い合わせ
コストダウンが利益に直結する術だと理解していても、なかなか前に進めることができない状況。そんな時は、newjiのコストダウン自動化機能で大きく利益貢献しよう!
(Β版非公開)