- お役立ち記事
- Unlocking Innovation: How Metal Additive Manufacturing is Transforming Japanese Manufacturing
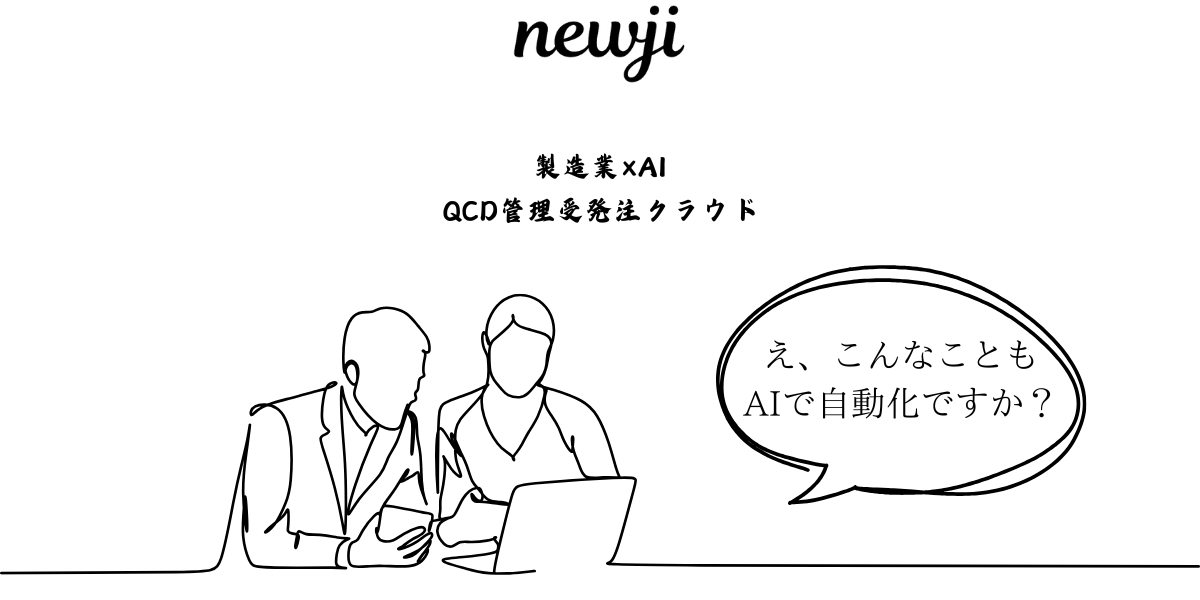
Unlocking Innovation: How Metal Additive Manufacturing is Transforming Japanese Manufacturing
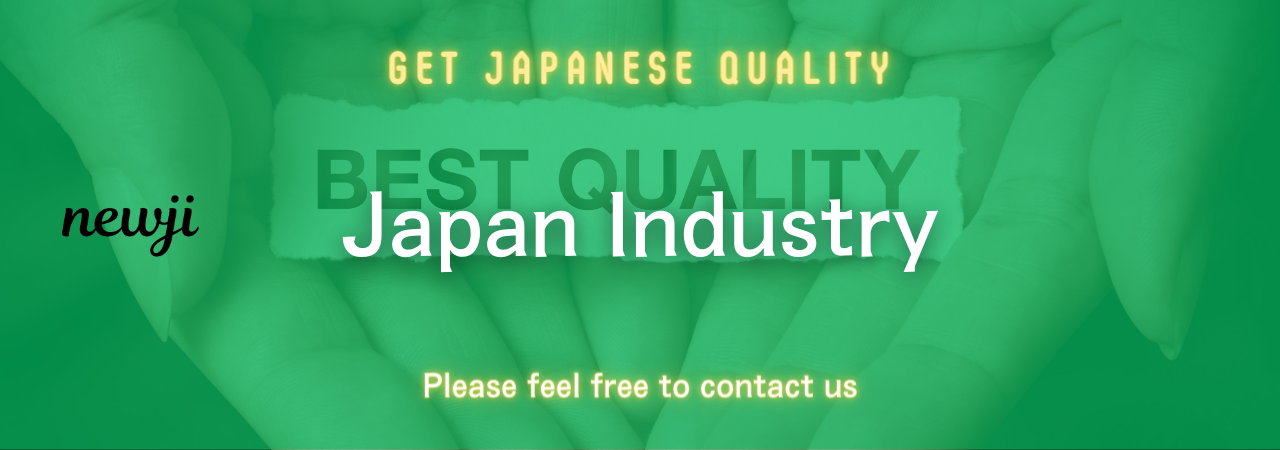
目次
Introduction to Metal Additive Manufacturing in Japan
Metal additive manufacturing, commonly known as 3D printing, has been a game-changer in the global manufacturing landscape.
Japanese manufacturers are at the forefront of this revolution, leveraging advanced technologies to enhance production capabilities.
This article explores how metal additive manufacturing is transforming Japanese manufacturing, focusing on procurement and purchasing insights.
We will delve into the advantages and disadvantages, supplier negotiation techniques, market conditions, and best practices in this innovative field.
The Evolution of Metal Addive Manufacturing in Japan
Historical Context and Technological Advancements
Japan has a long history of precision manufacturing and technological innovation.
The adoption of metal additive manufacturing marks a significant milestone in this journey.
Advancements in 3D printing technologies have enabled Japanese companies to produce complex metal parts with high accuracy.
These technological improvements have opened new avenues for manufacturing processes, reducing lead times and costs.
Integration with Traditional Manufacturing Processes
Metal additive manufacturing is not replacing traditional manufacturing but complementing it.
Japanese manufacturers integrate additive techniques with conventional methods like machining and casting.
This hybrid approach optimizes production efficiency and allows for greater design flexibility.
By combining these methods, companies can achieve the best of both worlds, enhancing product quality and performance.
Advantages of Metal Additive Manufacturing in Japanese Manufacturing
Customization and Flexibility
Additive manufacturing allows for high levels of customization without significant cost increases.
Japanese companies can produce bespoke components tailored to specific customer needs.
This flexibility is particularly advantageous in industries like aerospace and automotive, where precision is paramount.
Customizable production also enables rapid prototyping, accelerating the development cycle.
Cost Efficiency and Reduced Waste
Traditional manufacturing often involves substantial material waste.
Metal additive manufacturing uses only the necessary material, minimizing waste and lowering costs.
This efficiency is especially beneficial for high-value materials, reducing overall production expenses.
Moreover, the ability to produce complex geometries without additional costs further enhances cost efficiency.
Improved Supply Chain Management
By adopting additive manufacturing, Japanese companies can streamline their supply chains.
Local production reduces dependency on overseas suppliers and mitigates risks associated with global disruptions.
This localization results in shorter lead times and improved responsiveness to market demands.
Enhanced supply chain management contributes to greater operational resilience and efficiency.
Innovation and Competitive Advantage
Embracing metal additive manufacturing fosters a culture of innovation within organizations.
Japanese manufacturers can develop cutting-edge products that stand out in the global market.
This technological edge provides a competitive advantage, attracting customers seeking advanced solutions.
Continuous innovation ensures sustained growth and leadership in the manufacturing sector.
Disadvantages and Challenges
High Initial Investment
The adoption of metal additive manufacturing requires significant capital investment in equipment and technology.
Japanese companies must allocate substantial resources to procure state-of-the-art 3D printers and related infrastructure.
This financial barrier can be a deterrent for smaller businesses looking to enter the additive manufacturing space.
Moreover, ongoing maintenance and operational costs add to the financial commitment.
Skill Gap and Training Requirements
Effective utilization of metal additive manufacturing demands specialized skills and expertise.
There is a need for continuous training and education to keep the workforce updated with the latest technologies.
Bridging the skill gap is essential for maximizing the benefits of additive manufacturing.
Japanese companies must invest in workforce development to ensure successful implementation.
Material Limitations and Quality Control
While metal additive manufacturing offers versatility, it also has limitations in material properties.
Ensuring consistent quality and performance of printed parts can be challenging.
Japanese manufacturers must implement rigorous quality control measures to maintain high standards.
Addressing material limitations is crucial for the widespread adoption of this technology.
Supplier Negotiation Techniques in Additive Manufacturing
Building Strong Relationships
Establishing strong relationships with suppliers is fundamental in additive manufacturing.
Japanese companies prioritize trust and long-term partnerships to secure reliable supply chains.
Effective communication and mutual understanding foster collaboration and innovation.
Strong relationships enable better negotiation outcomes and ensure consistent quality.
Leveraging Market Knowledge
Having in-depth knowledge of the additive manufacturing market empowers companies during negotiations.
Understanding supplier capabilities, market trends, and pricing dynamics allows for informed decision-making.
Japanese manufacturers can leverage this knowledge to negotiate favorable terms and conditions.
Market insights also help in identifying and mitigating potential risks in the supply chain.
Emphasizing Quality and Precision
Quality and precision are paramount in Japanese manufacturing standards.
During negotiations, companies emphasize the importance of high-quality materials and accurate production.
Setting clear quality expectations ensures that suppliers meet the stringent requirements.
This focus on quality helps maintain the integrity and performance of the final products.
Negotiating Flexible Terms
Flexibility in terms of pricing, delivery schedules, and minimum order quantities can be beneficial.
Japanese companies negotiate terms that align with their production needs and market demands.
Flexible agreements allow for adaptability in response to changing business conditions.
This agility enhances overall supply chain resilience and responsiveness.
Market Conditions and Trends
Growing Demand for Customization
The global trend towards customization is driving the adoption of metal additive manufacturing.
Japanese manufacturers are capitalizing on this by offering tailored solutions to their customers.
The ability to produce customized products enhances customer satisfaction and loyalty.
This trend is particularly prominent in sectors like healthcare, aerospace, and automotive.
Technological Innovations
Continuous advancements in additive manufacturing technologies are shaping the market landscape.
Japanese companies are investing in research and development to stay ahead of the curve.
Innovations in materials, printing techniques, and post-processing methods are expanding capabilities.
Staying abreast of technological trends is essential for maintaining competitiveness.
Sustainability and Environmental Considerations
Sustainability is becoming a key focus in manufacturing practices.
Metal additive manufacturing contributes to environmental sustainability by reducing material waste.
Japanese manufacturers are also exploring eco-friendly materials and energy-efficient processes.
Aligning with global sustainability goals enhances corporate reputation and market positioning.
Competitive Landscape
The additive manufacturing market is highly competitive, with numerous players vying for market share.
Japanese companies must differentiate themselves through innovation, quality, and reliability.
Strategic partnerships and collaborations can provide a competitive edge.
Understanding the competitive landscape helps in formulating effective market strategies.
Best Practices in Metal Additive Manufacturing
Investing in Advanced Technologies
Staying updated with the latest additive manufacturing technologies is crucial for sustained success.
Japanese manufacturers prioritize investments in cutting-edge equipment and software.
Advanced technologies enhance production capabilities and product quality.
Continuous technological upgrades ensure that companies remain competitive in the market.
Implementing Robust Quality Control Systems
Quality control is integral to the success of metal additive manufacturing.
Japanese companies implement stringent quality assurance protocols to maintain high standards.
Regular inspections, testing, and certifications ensure the reliability of printed parts.
Robust quality control systems minimize defects and enhance customer satisfaction.
Fostering a Culture of Innovation
Encouraging a culture of innovation drives continuous improvement and growth.
Japanese manufacturers promote creative problem-solving and experimental approaches.
Investing in research and development fosters innovation and technological advancements.
A proactive innovation culture contributes to long-term sustainability and market leadership.
Enhancing Collaboration and Communication
Effective collaboration and communication are key to successful additive manufacturing projects.
Japanese companies foster teamwork across departments and with external partners.
Transparent communication channels facilitate information sharing and efficient decision-making.
Enhanced collaboration leads to better project outcomes and operational efficiency.
Optimizing Supply Chain Management
Efficient supply chain management is essential for the smooth operation of additive manufacturing.
Japanese manufacturers optimize their supply chains by integrating additive processes with traditional methods.
Localizing suppliers and reducing lead times enhance supply chain resilience.
Optimization efforts contribute to cost savings and improved production timelines.
The Role of Procurement and Purchasing in Additive Manufacturing
Strategic Sourcing of Materials
Procurement plays a critical role in sourcing high-quality materials for additive manufacturing.
Japanese companies adopt strategic sourcing practices to secure reliable and cost-effective suppliers.
Evaluating supplier capabilities and material specifications ensures the suitability of materials.
Strategic sourcing contributes to consistent production quality and operational efficiency.
Cost Management and Budgeting
Effective cost management is vital for maintaining profitability in additive manufacturing.
Procurement teams oversee budget allocations and monitor spending on materials and services.
Negotiating favorable terms with suppliers helps in controlling costs.
Cost management practices ensure that additive manufacturing projects remain financially viable.
Supplier Relationship Management
Maintaining strong relationships with suppliers is essential for successful additive manufacturing.
Japanese manufacturers emphasize trust, transparency, and collaboration with their suppliers.
Regular performance evaluations and feedback mechanisms enhance supplier relationships.
Effective supplier relationship management leads to improved service quality and reliability.
Risk Management and Mitigation
Procurement teams assess and mitigate risks associated with additive manufacturing supply chains.
Identifying potential disruptions, such as material shortages or supplier insolvency, allows for proactive measures.
Diversifying supplier bases and maintaining contingency plans enhance risk resilience.
Risk management practices safeguard the continuity of additive manufacturing operations.
Conclusion
Metal additive manufacturing is revolutionizing the Japanese manufacturing landscape, offering unparalleled opportunities for innovation and efficiency.
Japanese manufacturers are leveraging this technology to enhance customization, reduce costs, and streamline supply chains.
While challenges such as high initial investments and skill gaps exist, strategic approaches in procurement and purchasing can mitigate these issues.
By adopting best practices and fostering strong supplier relationships, Japanese companies are well-positioned to lead the additive manufacturing revolution.
The ongoing advancements and market trends further underscore the transformative impact of metal additive manufacturing on Japanese industry.
資料ダウンロード
QCD調達購買管理クラウド「newji」は、調達購買部門で必要なQCD管理全てを備えた、現場特化型兼クラウド型の今世紀最高の購買管理システムとなります。
ユーザー登録
調達購買業務の効率化だけでなく、システムを導入することで、コスト削減や製品・資材のステータス可視化のほか、属人化していた購買情報の共有化による内部不正防止や統制にも役立ちます。
NEWJI DX
製造業に特化したデジタルトランスフォーメーション(DX)の実現を目指す請負開発型のコンサルティングサービスです。AI、iPaaS、および先端の技術を駆使して、製造プロセスの効率化、業務効率化、チームワーク強化、コスト削減、品質向上を実現します。このサービスは、製造業の課題を深く理解し、それに対する最適なデジタルソリューションを提供することで、企業が持続的な成長とイノベーションを達成できるようサポートします。
オンライン講座
製造業、主に購買・調達部門にお勤めの方々に向けた情報を配信しております。
新任の方やベテランの方、管理職を対象とした幅広いコンテンツをご用意しております。
お問い合わせ
コストダウンが利益に直結する術だと理解していても、なかなか前に進めることができない状況。そんな時は、newjiのコストダウン自動化機能で大きく利益貢献しよう!
(Β版非公開)