- お役立ち記事
- Unlocking Innovation in Japanese Manufacturing: How AE Sensors (Acoustic Emission) are Revolutionizing the Industry
Unlocking Innovation in Japanese Manufacturing: How AE Sensors (Acoustic Emission) are Revolutionizing the Industry
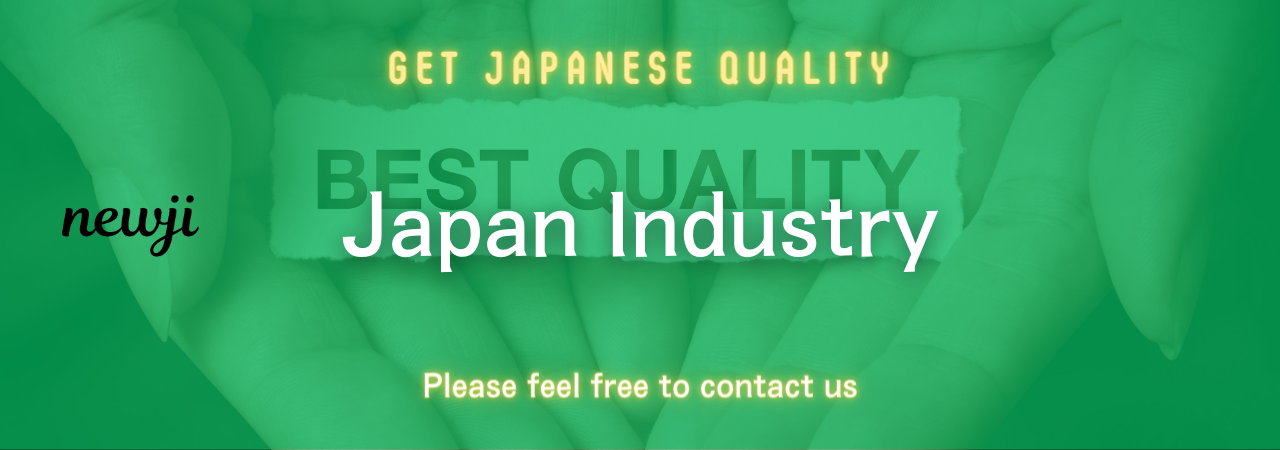
目次
Introduction to AE Sensors in Japanese Manufacturing
Acoustic Emission (AE) sensors have emerged as a pivotal technology in the landscape of Japanese manufacturing. These sensors detect and analyze transient waves generated by the rapid release of energy from localized sources within a material under stress. The integration of AE sensors into manufacturing processes has unlocked new avenues for innovation, quality control, and operational efficiency. This article explores how AE sensors are revolutionizing the Japanese manufacturing industry, with a particular focus on procurement and purchasing dynamics.
The Role of AE Sensors in Enhancing Manufacturing Processes
Japanese manufacturers are renowned for their precision, quality, and efficiency. AE sensors contribute significantly to maintaining and enhancing these attributes by providing real-time monitoring and early detection of potential issues in machinery and materials.
Real-Time Monitoring and Predictive Maintenance
AE sensors facilitate continuous monitoring of equipment, enabling predictive maintenance. By analyzing acoustic emissions, manufacturers can predict equipment failures before they occur, thereby minimizing downtime and reducing maintenance costs. This proactive approach aligns with the Japanese manufacturing ethos of minimizing waste and maximizing efficiency.
Quality Control and Assurance
In sectors such as automotive and electronics, where precision is paramount, AE sensors play a critical role in quality control. They detect defects and inconsistencies in materials and products during various stages of production. This early detection ensures that only products meeting stringent quality standards proceed through the manufacturing process.
Process Optimization
AE sensors provide valuable data that can be used to optimize manufacturing processes. By analyzing the acoustic signatures generated during production, manufacturers can identify inefficiencies and areas for improvement. This data-driven approach supports continuous improvement initiatives, a cornerstone of Japanese manufacturing practices like Kaizen.
Advantages of Integrating AE Sensors in Procurement and Purchasing
From a procurement and purchasing perspective, the adoption of AE sensors offers several advantages that can enhance the overall supply chain and operational effectiveness.
Enhanced Supplier Evaluation
When sourcing components and machinery, procurement teams can utilize AE sensor data to evaluate supplier quality. By assessing the acoustic emissions of potential suppliers’ products, companies can make informed decisions about the reliability and performance of these suppliers.
Cost Savings
The implementation of AE sensors leads to significant cost savings by reducing unplanned downtime and maintenance expenses. Procurement departments can negotiate better contracts with suppliers by demonstrating a commitment to quality and reliability, supported by data from AE sensors.
Improved Supply Chain Transparency
AE sensors provide transparent and real-time data about the condition of machinery and materials. This transparency facilitates better coordination with suppliers, ensuring that all parties have access to the information needed to maintain high standards of quality and efficiency.
Challenges and Considerations in Deploying AE Sensors
While AE sensors offer numerous benefits, there are challenges and considerations that procurement and purchasing departments must address to ensure successful implementation.
Initial Investment and Cost
The adoption of AE sensor technology requires an upfront investment in hardware, software, and training. Procurement teams must evaluate the return on investment (ROI) to justify these initial costs. Engaging in thorough cost-benefit analysis is essential to demonstrate the long-term savings and efficiency gains.
Integration with Existing Systems
Integrating AE sensors with existing manufacturing systems and processes can be complex. Procurement departments need to collaborate with IT and engineering teams to ensure seamless integration. Selecting AE sensor solutions that are compatible with current infrastructure can mitigate compatibility issues.
Data Management and Analysis
The volume of data generated by AE sensors can be overwhelming. Effective data management and analysis are crucial to extracting actionable insights. Investing in robust data analytics tools and training personnel to interpret AE sensor data is necessary for maximizing the technology’s benefits.
Supplier Negotiation Techniques for AE Sensors
Effective negotiation with AE sensor suppliers is critical to securing favorable terms and ensuring the successful deployment of the technology in manufacturing processes.
Understanding Supplier Capabilities
Before entering negotiations, procurement teams must thoroughly understand the capabilities and limitations of potential AE sensor suppliers. Evaluating the technical specifications, reliability, and support services of suppliers helps in assessing their suitability for the company’s specific needs.
Leveraging Volume and Long-Term Partnerships
Japanese manufacturers often engage in long-term partnerships with suppliers. By committing to larger volumes and extended contracts, procurement teams can negotiate better pricing and more favorable terms. Emphasizing the potential for ongoing business can incentivize suppliers to offer discounts and enhanced support.
Demanding Customization and Support
Customization of AE sensor solutions to fit specific manufacturing requirements is often necessary. Procurement departments should negotiate for tailored solutions that address the unique challenges of their production processes. Additionally, ensuring that suppliers provide comprehensive support and training is essential for the successful implementation of AE sensors.
Quality Assurance and Warranty Terms
Ensuring that AE sensors meet stringent quality standards is paramount. Procurement teams should negotiate robust quality assurance and warranty terms to protect against defects and performance issues. Clear agreements on maintenance, replacement, and support services help mitigate risks associated with technology deployment.
Market Conditions Influencing AE Sensor Procurement
Understanding the current market conditions is essential for procurement and purchasing departments when sourcing AE sensors. Several factors influence the availability, pricing, and innovation of AE sensor technologies.
Technological Advancements
Continuous advancements in sensor technology drive the evolution of AE sensors. Staying abreast of the latest innovations helps procurement teams identify suppliers offering cutting-edge solutions that can provide competitive advantages in manufacturing processes.
Supply Chain Dynamics
Global supply chain dynamics, including material shortages and geopolitical factors, can impact the availability and cost of AE sensors. Procurement departments must develop strategies to navigate these challenges, such as diversifying suppliers and securing long-term contracts to stabilize pricing.
Economic Factors
Economic conditions, including inflation and exchange rates, affect the cost of AE sensors. Japanese manufacturers exporting products may also consider the impact of currency fluctuations on procurement costs. Effective financial planning and currency risk management are crucial to maintaining cost-effective procurement strategies.
Regulatory Environment
Compliance with industry standards and regulations is mandatory for AE sensor deployments. Procurement teams must ensure that suppliers adhere to relevant standards and certifications. Staying informed about regulatory changes helps in selecting compliant and reliable suppliers.
Best Practices for Procuring AE Sensors in Japanese Manufacturing
To maximize the benefits of AE sensors, procurement and purchasing departments should adopt best practices that ensure effective sourcing, integration, and utilization of the technology.
Comprehensive Needs Assessment
Conducting a thorough needs assessment is the first step in procuring AE sensors. Identifying the specific applications, performance requirements, and integration points within the manufacturing process helps in selecting the most suitable sensor solutions.
Collaborative Supplier Relationships
Building collaborative relationships with AE sensor suppliers fosters trust and mutual understanding. Open communication channels and regular performance reviews enable continuous improvement and innovation, benefiting both parties.
Investing in Training and Development
Educating procurement teams and end-users about AE sensor technology is essential for successful implementation. Investing in training programs ensures that personnel can effectively utilize the sensors and interpret the data they generate.
Continuous Performance Monitoring
After procurement, continuous monitoring of AE sensor performance is necessary to ensure they meet the desired objectives. Regular assessments and feedback loops help in identifying areas for enhancement and maintaining optimal sensor performance.
Emphasizing Sustainability
Sustainability is increasingly important in manufacturing. Procuring AE sensors from suppliers committed to sustainable practices aligns with corporate social responsibility goals and can enhance the company’s reputation in the market.
Case Studies: Successful Implementation of AE Sensors in Japanese Manufacturing
Examining real-world examples of AE sensor implementation provides valuable insights into best practices and the tangible benefits of the technology.
Automotive Industry: Enhancing Vehicle Safety
A leading Japanese automotive manufacturer integrated AE sensors into their assembly lines to monitor the integrity of welds and structural components. The sensors detected minute acoustic emissions indicative of potential defects, allowing for immediate corrective actions. This proactive approach reduced defects by 30% and improved overall vehicle safety, showcasing the significant impact of AE sensors on quality control.
Electronics Manufacturing: Improving Component Reliability
In the electronics sector, a Japanese manufacturer utilized AE sensors to monitor the production of printed circuit boards (PCBs). The sensors identified inconsistencies and defects during the soldering process. By addressing these issues in real-time, the company reduced scrap rates by 25% and enhanced the reliability of their electronic components, leading to increased customer satisfaction and reduced warranty claims.
Heavy Machinery: Optimizing Equipment Performance
A Japanese heavy machinery manufacturer deployed AE sensors to monitor the performance of critical machinery components such as engines and hydraulics. The sensors provided early warnings of wear and tear, enabling scheduled maintenance before major failures occurred. This strategy extended the lifespan of equipment, reduced maintenance costs by 20%, and minimized operational downtime.
Future Trends in AE Sensor Technology and Procurement
The landscape of AE sensor technology continues to evolve, presenting new opportunities and challenges for Japanese manufacturers and their procurement teams.
Integration with IoT and Smart Manufacturing
AE sensors are increasingly being integrated with Internet of Things (IoT) platforms, enabling smarter manufacturing environments. This integration allows for enhanced data collection, real-time analytics, and more sophisticated predictive maintenance strategies, further improving operational efficiency and product quality.
Advancements in Data Analytics and AI
The incorporation of artificial intelligence (AI) and machine learning into AE sensor data analysis is set to revolutionize manufacturing processes. These technologies can identify complex patterns and correlations within the data, leading to more accurate predictions and deeper insights into machinery performance and product quality.
Wireless and Remote Monitoring Solutions
Wireless AE sensors offer greater flexibility and ease of installation, particularly in large or complex manufacturing facilities. Remote monitoring capabilities enable procurement teams to manage and oversee multiple facilities from centralized locations, enhancing oversight and control.
Sustainability and Energy Efficiency
Future AE sensor developments will likely focus on sustainability and energy efficiency. Lightweight, low-power sensors can reduce the overall energy consumption of manufacturing operations, aligning with global sustainability goals and regulatory requirements.
Conclusion
AE sensors are playing a transformative role in Japanese manufacturing, driving innovation, enhancing quality control, and optimizing operational efficiency. For procurement and purchasing departments, the adoption of AE sensor technology offers numerous advantages, including improved supplier evaluation, cost savings, and enhanced supply chain transparency. However, successful implementation requires careful consideration of initial investments, integration challenges, and data management strategies.
By employing effective supplier negotiation techniques, understanding market conditions, and adhering to best practices, Japanese manufacturers can fully leverage the benefits of AE sensors. As technology continues to advance, the integration of AE sensors with IoT, AI, and wireless solutions will further revolutionize manufacturing processes, ensuring that Japanese manufacturing remains at the forefront of global industry standards.
Embracing AE sensor technology not only enhances the technical capabilities of manufacturing operations but also aligns with the strategic objectives of procurement and purchasing departments to drive quality, efficiency, and sustainability. As the industry evolves, continuous investment in and adaptation to AE sensor advancements will be essential for maintaining competitive advantage and achieving long-term success in the dynamic landscape of Japanese manufacturing.
資料ダウンロード
QCD調達購買管理クラウド「newji」は、調達購買部門で必要なQCD管理全てを備えた、現場特化型兼クラウド型の今世紀最高の購買管理システムとなります。
ユーザー登録
調達購買業務の効率化だけでなく、システムを導入することで、コスト削減や製品・資材のステータス可視化のほか、属人化していた購買情報の共有化による内部不正防止や統制にも役立ちます。
NEWJI DX
製造業に特化したデジタルトランスフォーメーション(DX)の実現を目指す請負開発型のコンサルティングサービスです。AI、iPaaS、および先端の技術を駆使して、製造プロセスの効率化、業務効率化、チームワーク強化、コスト削減、品質向上を実現します。このサービスは、製造業の課題を深く理解し、それに対する最適なデジタルソリューションを提供することで、企業が持続的な成長とイノベーションを達成できるようサポートします。
オンライン講座
製造業、主に購買・調達部門にお勤めの方々に向けた情報を配信しております。
新任の方やベテランの方、管理職を対象とした幅広いコンテンツをご用意しております。
お問い合わせ
コストダウンが利益に直結する術だと理解していても、なかなか前に進めることができない状況。そんな時は、newjiのコストダウン自動化機能で大きく利益貢献しよう!
(Β版非公開)