- お役立ち記事
- Unlocking Innovation: The Evolution of Japanese Manufacturing Excellence
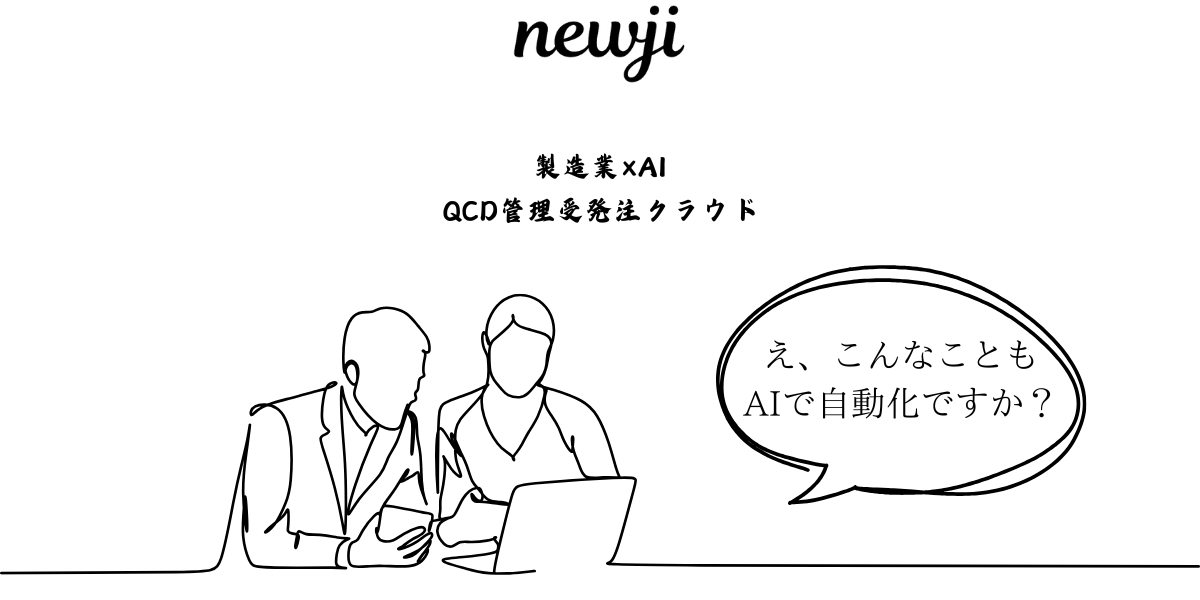
Unlocking Innovation: The Evolution of Japanese Manufacturing Excellence
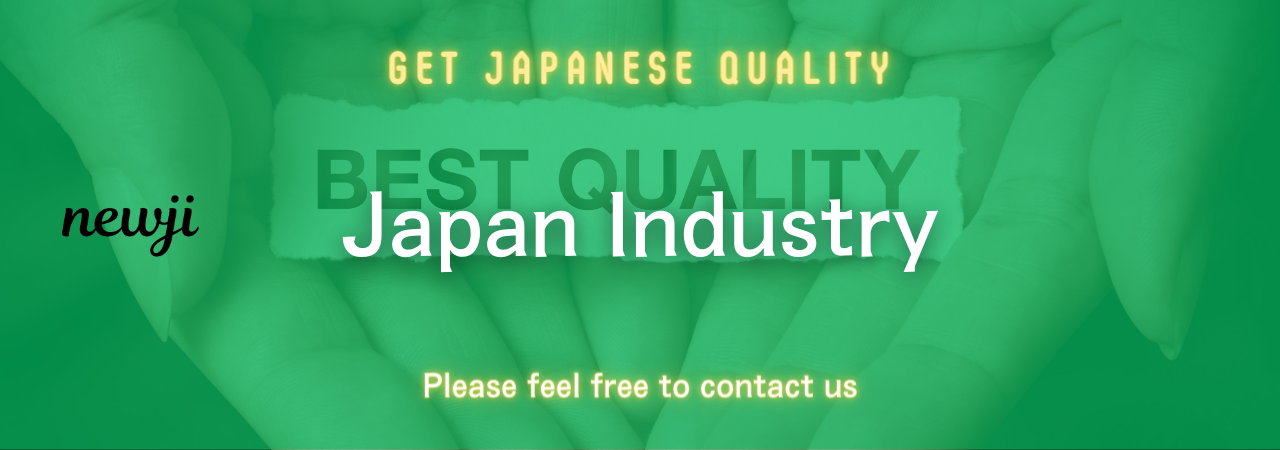
目次
Introduction to Japanese Manufacturing Excellence
Japanese manufacturing has long been synonymous with quality, efficiency, and innovation.
Over the decades, Japanese companies have set benchmarks in various industries, from automotive to electronics.
This excellence is not accidental but the result of a unique blend of cultural values, strategic procurement practices, and relentless pursuit of improvement.
In this article, we will explore the evolution of Japanese manufacturing, delving into its core principles, procurement strategies, supplier negotiations, market conditions, and best practices that have enabled Japan to maintain its competitive edge in the global market.
Historical Evolution of Japanese Manufacturing Excellence
The journey of Japanese manufacturing excellence began in the post-World War II era.
Japan faced the daunting task of rebuilding its economy from the ashes of war.
This period was marked by significant government intervention and support for key industries.
Japanese companies adopted methodologies that focused on efficiency, waste reduction, and continuous improvement.
One of the most notable contributions during this time was the development of the Toyota Production System, which introduced concepts like Just-In-Time (JIT) manufacturing and Kaizen (continuous improvement).
The Birth of the Toyota Production System
The Toyota Production System revolutionized manufacturing worldwide.
It emphasized eliminating waste, improving quality, and optimizing processes.
JIT manufacturing ensures that materials are available precisely when needed, reducing inventory costs.
Kaizen fosters a culture where every employee is encouraged to suggest improvements, leading to incremental advancements that accumulate over time.
Influence of Lean Manufacturing
Lean manufacturing, heavily influenced by Japanese methodologies, has been adopted globally.
It focuses on maximizing value for customers while minimizing waste.
Key principles include value stream mapping, flow, pull systems, and pursuit of perfection.
Japanese companies have demonstrated that lean principles lead to enhanced efficiency, better quality products, and increased customer satisfaction.
Core Principles of Japanese Manufacturing
Japanese manufacturing excellence is underpinned by several core principles that guide company operations and decision-making processes.
These principles ensure consistency, quality, and continuous improvement.
Kaizen: Continuous Improvement
Kaizen is the philosophy of continuous improvement.
It involves every employee, from the CEO to the assembly line workers, actively seeking ways to improve processes, products, and services.
This relentless pursuit of improvement ensures that companies remain competitive and adapt to changing market conditions.
Kanban: Workflow Management
Kanban is a scheduling system that visualizes work, limits work-in-progress, and optimizes the flow of tasks.
It helps in identifying bottlenecks and improving efficiency.
In manufacturing, Kanban ensures that production processes are smooth and that resources are utilized optimally.
Jidoka: Automation with a Human Touch
Jidoka refers to the concept of automation with a human touch.
Machines are designed to stop automatically when a defect is detected, preventing the production of faulty products.
This ensures high-quality standards and reduces waste by addressing problems immediately.
Procurement and Purchasing in Japanese Manufacturing
Procurement and purchasing are critical components of Japanese manufacturing excellence.
Japanese companies adopt strategic procurement practices that focus on long-term relationships, quality, and reliability.
Strategic Supplier Relationships
Japanese manufacturers prioritize building long-term relationships with suppliers.
These partnerships are based on mutual trust, transparency, and collaboration.
By fostering strong relationships, companies can ensure a reliable supply of high-quality materials and components.
Just-In-Time (JIT) Procurement
JIT procurement ensures that materials are delivered precisely when needed, reducing inventory costs.
This requires accurate forecasting, efficient logistics, and strong coordination with suppliers.
JIT helps in minimizing waste, optimizing inventory levels, and enhancing responsiveness to market demands.
Emphasis on Quality
Quality is paramount in Japanese manufacturing.
Procurement practices are designed to source the highest quality materials and components.
Strict quality control measures are implemented to ensure that suppliers meet the required standards.
This focus on quality leads to superior end products and greater customer satisfaction.
Advantages and Disadvantages of Partnering with Japanese Suppliers
Partnering with Japanese suppliers offers numerous advantages but also comes with certain challenges.
Advantages
Japanese suppliers are renowned for their commitment to quality and reliability.
They adhere to strict manufacturing standards and invest in continuous improvement.
Partnering with such suppliers ensures consistent product quality and reduces the risk of defects.
Additionally, Japanese companies are often leaders in innovation, providing access to cutting-edge technologies and processes.
Disadvantages
One of the primary challenges in partnering with Japanese suppliers is cultural and language barriers.
Differences in business practices and communication styles can lead to misunderstandings and delays.
Moreover, the preference for long-term relationships may not align with companies seeking quick, transactional interactions.
Additionally, the cost of Japanese suppliers can be higher compared to alternatives from other regions.
Supplier Negotiation Techniques in the Japanese Context
Effective negotiation with Japanese suppliers requires understanding and respecting their cultural norms and business practices.
Building Trust and Relationships
In Japanese business culture, trust and relationships are foundational.
Negotiations are often seen as a process of building long-term partnerships rather than merely transactional exchanges.
Investing time in building rapport and understanding the supplier’s values and objectives is crucial for successful negotiations.
Consensus-Based Decision Making
Japanese companies often use a consensus-based approach to decision-making.
This means that decisions are made collectively, with input from various stakeholders.
Patience is essential, as this process can take longer but ensures commitment and alignment among all parties involved.
Focus on Mutual Benefits
Negotiations should emphasize mutual benefits and win-win outcomes.
Highlighting how the partnership can lead to shared success fosters a collaborative environment and strengthens the relationship.
Respect for Hierarchy and Formality
Understanding and respecting the hierarchical structure of Japanese companies is important.
Formalities such as proper titles, business card exchanges, and polite communication are essential.
Demonstrating respect and professionalism can positively impact negotiation outcomes.
Market Conditions and Trends in Japanese Manufacturing
The Japanese manufacturing sector is dynamic, influenced by various market conditions and global trends.
Technological Advancements
Japan is at the forefront of technological innovation, particularly in robotics, automation, and smart manufacturing.
Companies are continuously investing in research and development to stay ahead in the competitive landscape.
Global Supply Chain Integration
Japanese manufacturers are increasingly integrating their supply chains globally.
This approach enhances flexibility, reduces costs, and improves access to diverse markets.
However, it also requires robust logistics and risk management strategies to handle complexities.
Environmental Sustainability
Sustainability has become a significant focus in Japanese manufacturing.
Companies are adopting eco-friendly practices, reducing emissions, and utilizing sustainable materials.
This shift not only complies with global environmental standards but also meets the growing consumer demand for sustainable products.
Aging Workforce
Japan faces the challenge of an aging workforce, impacting manufacturing sectors that rely on skilled labor.
To address this, companies are investing in automation and training programs to ensure that the workforce adapts to new technologies and processes.
Best Practices for Collaborating with Japanese Manufacturers
To maximize the benefits of collaborating with Japanese manufacturers, certain best practices should be followed.
Effective Communication
Clear and consistent communication is vital.
Using translators or bilingual employees can bridge language gaps.
Regular meetings and updates ensure that both parties are aligned and can address issues promptly.
Cultural Sensitivity
Understanding and respecting Japanese culture enhances collaboration.
This includes being punctual, showing respect in communication, and adhering to formal business etiquettes.
Cultural sensitivity fosters trust and smoothens interactions between partners.
Commitment to Quality
Aligning with the Japanese emphasis on quality is essential.
Implementing stringent quality control measures and continuously seeking improvement reflects a shared commitment to excellence.
Flexibility and Adaptability
Being flexible and adaptable to changing circumstances and feedback is important.
Japanese manufacturers value partners who can respond swiftly to market changes and contribute to the joint pursuit of innovation.
Long-Term Vision
Adopting a long-term vision rather than focusing solely on short-term gains aligns with the Japanese approach to business.
This perspective supports sustainable growth and strengthens the partnership over time.
Conclusion: Embracing Japanese Manufacturing Excellence
Japanese manufacturing excellence is a blend of strategic procurement, unwavering commitment to quality, cultural values, and continuous improvement.
By understanding the evolution, core principles, and best practices of Japanese manufacturing, companies can unlock innovation and achieve sustained success.
Partnering with Japanese suppliers offers access to top-tier quality, advanced technologies, and a collaborative partnership model.
However, navigating cultural differences and embracing a long-term vision are crucial for maximizing the benefits of such collaborations.
As global markets evolve, the lessons from Japanese manufacturing continue to offer valuable insights for companies striving for excellence and innovation in their operations.
資料ダウンロード
QCD調達購買管理クラウド「newji」は、調達購買部門で必要なQCD管理全てを備えた、現場特化型兼クラウド型の今世紀最高の購買管理システムとなります。
ユーザー登録
調達購買業務の効率化だけでなく、システムを導入することで、コスト削減や製品・資材のステータス可視化のほか、属人化していた購買情報の共有化による内部不正防止や統制にも役立ちます。
NEWJI DX
製造業に特化したデジタルトランスフォーメーション(DX)の実現を目指す請負開発型のコンサルティングサービスです。AI、iPaaS、および先端の技術を駆使して、製造プロセスの効率化、業務効率化、チームワーク強化、コスト削減、品質向上を実現します。このサービスは、製造業の課題を深く理解し、それに対する最適なデジタルソリューションを提供することで、企業が持続的な成長とイノベーションを達成できるようサポートします。
オンライン講座
製造業、主に購買・調達部門にお勤めの方々に向けた情報を配信しております。
新任の方やベテランの方、管理職を対象とした幅広いコンテンツをご用意しております。
お問い合わせ
コストダウンが利益に直結する術だと理解していても、なかなか前に進めることができない状況。そんな時は、newjiのコストダウン自動化機能で大きく利益貢献しよう!
(Β版非公開)