- お役立ち記事
- Unlocking Japanese Manufacturing Potential: Embracing the Latest DX Solutions for Success
月間77,185名の
製造業ご担当者様が閲覧しています*
*2025年2月28日現在のGoogle Analyticsのデータより
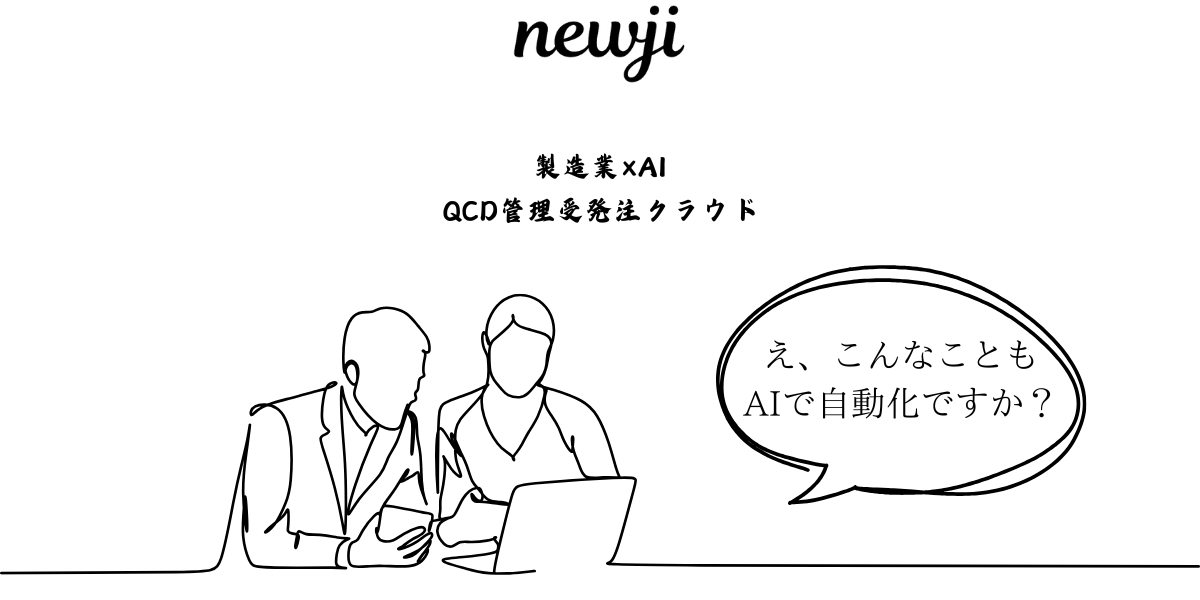
Unlocking Japanese Manufacturing Potential: Embracing the Latest DX Solutions for Success
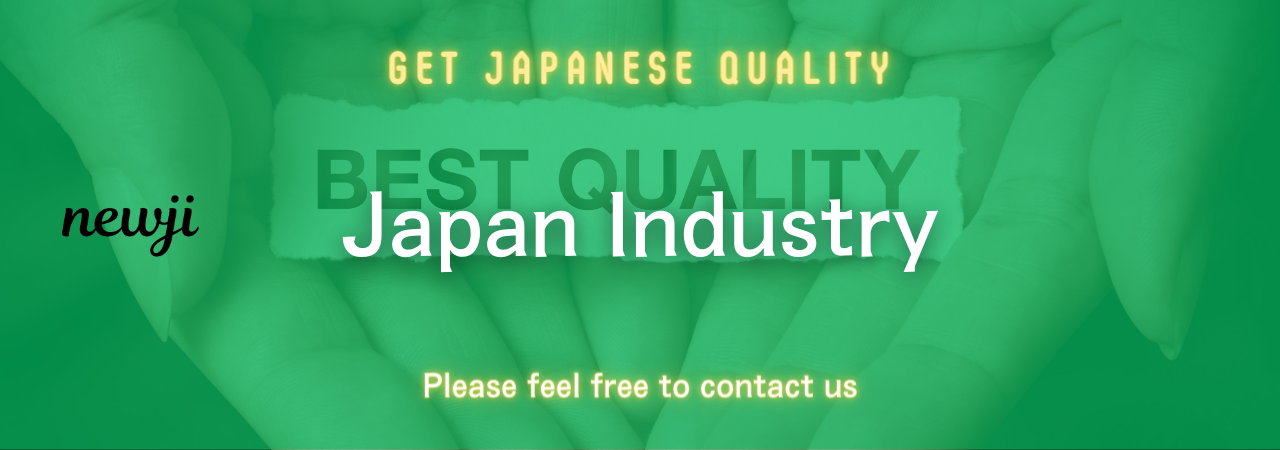
目次
Introduction to Japanese Manufacturing and Digital Transformation
Japanese manufacturing has long been synonymous with quality, precision, and innovation. Renowned for its meticulous attention to detail and commitment to continuous improvement, Japan’s manufacturing sector plays a pivotal role in the global economy. In recent years, the advent of Digital Transformation (DX) has presented both opportunities and challenges for Japanese manufacturers. Embracing the latest DX solutions is crucial for maintaining competitiveness, enhancing efficiency, and unlocking new avenues for growth.
The Evolution of Digital Transformation in Japanese Manufacturing
Digital Transformation refers to the integration of digital technologies into all aspects of a business, fundamentally changing how organizations operate and deliver value to customers. In the context of Japanese manufacturing, DX encompasses the adoption of advanced technologies such as the Internet of Things (IoT), artificial intelligence (AI), robotics, and big data analytics to streamline operations, improve product quality, and foster innovation.
Early Adoption and Technological Prowess
Japanese manufacturers have a history of embracing technological advancements to enhance production capabilities. From the automation revolution led by companies like FANUC and Mitsubishi Electric to the implementation of Just-In-Time (JIT) manufacturing, Japan has consistently leveraged technology to maintain its edge. The integration of DX is a natural progression in this trajectory, aimed at addressing the dynamic challenges of the modern industrial landscape.
Current Trends in DX Implementation
Today, Japanese manufacturers are increasingly adopting smart factories, which utilize interconnected systems and real-time data analytics to optimize production processes. The use of AI and machine learning algorithms enables predictive maintenance, reducing downtime and extending the lifespan of machinery. Additionally, IoT devices facilitate seamless communication between different stages of the supply chain, enhancing transparency and responsiveness.
Advantages of Embracing DX Solutions
Adopting DX solutions offers a multitude of benefits for Japanese manufacturers, ranging from enhanced operational efficiency to improved customer satisfaction.
Increased Operational Efficiency
DX enables the automation of repetitive tasks, reducing the reliance on manual labor and minimizing the risk of human error. Advanced data analytics provide insights into production processes, allowing for the identification and elimination of bottlenecks. This leads to streamlined operations, faster turnaround times, and increased productivity.
Enhanced Quality Control
With the integration of AI and machine vision systems, manufacturers can achieve higher levels of precision in quality control. These technologies can detect defects with greater accuracy and consistency than manual inspections, ensuring that products meet stringent quality standards. This not only reduces waste but also enhances the reputation of Japanese manufacturers for delivering high-quality products.
Improved Supply Chain Management
DX facilitates real-time monitoring of the supply chain, enabling manufacturers to respond swiftly to changes in demand and supply. Enhanced visibility allows for better forecasting and inventory management, reducing the likelihood of stockouts or excess inventory. Moreover, improved communication with suppliers fosters stronger relationships and more efficient procurement processes.
Innovation and Competitive Advantage
Embracing DX fosters a culture of innovation, encouraging the development of new products and services. Manufacturers can leverage data-driven insights to anticipate market trends and customer needs, positioning themselves ahead of competitors. Additionally, the ability to rapidly adapt to technological advancements ensures sustained competitiveness in a rapidly evolving market.
Disadvantages and Challenges of DX Implementation
While the benefits of DX are substantial, the implementation process is fraught with challenges that manufacturers must navigate to realize its full potential.
High Initial Investment
The adoption of advanced digital technologies requires significant upfront capital investment. Costs associated with purchasing equipment, upgrading infrastructure, and training personnel can be prohibitive, especially for small and medium-sized enterprises (SMEs). Securing the necessary funding and justifying the return on investment (ROI) can be challenging.
Technical Complexity and Integration Issues
Integrating new digital systems with existing legacy infrastructure can be complex and time-consuming. Compatibility issues, data migration challenges, and the need for seamless interoperability between different technologies can hinder the implementation process. Ensuring that all components work together cohesively is critical for the success of DX initiatives.
Cybersecurity Risks
The increased connectivity associated with DX exposes manufacturers to heightened cybersecurity threats. Protecting sensitive data and ensuring the integrity of digital systems is paramount. Investing in robust cybersecurity measures and developing comprehensive risk management strategies are essential to mitigate potential vulnerabilities.
Change Management and Workforce Adaptation
Implementing DX often necessitates significant changes in organizational processes and workflows. Resistance to change from employees, coupled with the need for new skill sets, can impede adoption. Effective change management strategies, including training and communication, are vital to ensure a smooth transition and foster employee buy-in.
Supplier Negotiation Techniques in the DX Era
Effective supplier negotiation is a cornerstone of successful procurement and purchasing strategies. In the context of DX, negotiation techniques must evolve to accommodate the complexities and opportunities presented by digital technologies.
Leveraging Data-Driven Insights
Access to real-time data enables more informed decision-making during negotiations. Manufacturers can analyze supplier performance metrics, cost structures, and market trends to develop compelling negotiation positions. Data-driven insights enhance transparency and enable the identification of mutually beneficial opportunities.
Collaborative Relationships and Strategic Partnerships
Building collaborative relationships with suppliers fosters trust and openness, facilitating more effective negotiations. Strategic partnerships can lead to joint innovation initiatives, shared risk management, and long-term value creation. Emphasizing partnership over transactional interactions can result in more favorable terms and enhanced collaboration.
Flexible Contractual Agreements
Incorporating flexibility into contractual agreements allows manufacturers to adapt to changing circumstances and technological advancements. Provisions for scalability, performance-based incentives, and options for renegotiation can accommodate evolving business needs and mitigate potential risks.
Utilizing Digital Platforms for Negotiations
Digital negotiation platforms streamline the negotiation process, enabling asynchronous communication, documentation management, and tracking of negotiation milestones. These platforms enhance efficiency, reduce administrative burdens, and provide a centralized repository for negotiation-related information.
Market Conditions Affecting Procurement and Purchasing
Understanding the broader market conditions is essential for effective procurement and purchasing strategies. Various factors influence the procurement landscape, particularly in the realm of Japanese manufacturing.
Global Supply Chain Dynamics
Global supply chain disruptions, such as those caused by geopolitical tensions, natural disasters, or pandemics, can significantly impact procurement activities. Japanese manufacturers must develop resilient supply chain strategies, including diversifying supplier bases and establishing contingency plans to mitigate potential disruptions.
Technological Advancements and Industry 4.0
The rapid pace of technological advancements, particularly in Industry 4.0, necessitates continuous adaptation and innovation. Staying abreast of emerging technologies and integrating them into procurement practices is essential for maintaining competitiveness and meeting evolving market demands.
Regulatory and Compliance Requirements
Compliance with international and regional regulations, including environmental standards and labor laws, is a critical consideration in procurement. Japanese manufacturers must ensure that their procurement practices align with regulatory requirements to avoid legal penalties and maintain their reputation for ethical business conduct.
Economic Factors and Currency Fluctuations
Economic conditions, including inflation rates, interest rates, and currency fluctuations, can impact procurement costs and supplier relationships. Effective financial management and hedging strategies are necessary to navigate economic volatility and protect profit margins.
Best Practices for Unlocking Manufacturing Potential Through DX
To fully realize the benefits of DX, Japanese manufacturers must adopt best practices that ensure successful implementation and sustainable growth.
Develop a Comprehensive Digital Strategy
A well-defined digital strategy provides a roadmap for DX initiatives, outlining objectives, key performance indicators (KPIs), and implementation timelines. Aligning the digital strategy with overall business goals ensures coherence and facilitates the integration of digital technologies across all facets of the organization.
Invest in Workforce Training and Development
Empowering employees with the necessary skills and knowledge is critical for the successful adoption of DX. Comprehensive training programs, continuous learning opportunities, and fostering a culture of innovation encourage workforce engagement and adaptability.
Foster Cross-Functional Collaboration
Encouraging collaboration between different departments and functions promotes the sharing of insights and facilitates the seamless integration of digital technologies. Cross-functional teams can drive innovation, streamline processes, and enhance problem-solving capabilities.
Implement Robust Data Management Practices
Effective data management is foundational to DX. Establishing standards for data collection, storage, and analysis ensures data integrity and usability. Leveraging big data analytics can provide actionable insights, driving informed decision-making and strategic planning.
Prioritize Cybersecurity and Risk Management
Protecting digital assets and ensuring the security of interconnected systems is paramount. Implementing robust cybersecurity measures, conducting regular risk assessments, and developing comprehensive incident response plans mitigate potential threats and safeguard the organization’s digital infrastructure.
Engage with Technology Partners and Innovators
Collaborating with technology partners, startups, and research institutions can provide access to cutting-edge technologies and innovative solutions. Building a network of trusted partners facilitates knowledge exchange, accelerates technology adoption, and fosters a culture of continuous improvement.
Measure and Monitor Progress
Regularly evaluating the progress of DX initiatives against established KPIs enables organizations to assess the effectiveness of their strategies and make necessary adjustments. Continuous monitoring ensures that DX efforts remain aligned with business objectives and deliver tangible results.
Case Studies: Successful DX Implementation in Japanese Manufacturing
Examining real-world examples of successful DX implementation provides valuable insights and lessons for other manufacturers aiming to embark on their digital transformation journey.
Case Study 1: Toyota’s Smart Factory Initiative
Toyota, a global leader in automotive manufacturing, has embraced DX through its Smart Factory initiative. By integrating IoT sensors and AI-driven analytics, Toyota has optimized its production lines, achieving higher efficiency and reduced waste. The implementation of predictive maintenance has minimized downtime, while real-time data monitoring has enhanced quality control. Toyota’s commitment to continuous improvement and employee training has been pivotal in the success of its DX efforts.
Case Study 2: Panasonic’s Digital Supply Chain Transformation
Panasonic has undertaken a comprehensive digital transformation of its supply chain, leveraging blockchain technology to enhance transparency and traceability. The adoption of AI and machine learning algorithms has improved demand forecasting and inventory management, reducing costs and improving responsiveness. Panasonic’s strategic partnerships with technology providers have facilitated the seamless integration of digital solutions, resulting in a more agile and efficient supply chain.
Case Study 3: Hitachi’s AI-Powered Quality Control
Hitachi has implemented AI-powered quality control systems in its manufacturing processes, utilizing machine vision and deep learning algorithms to detect defects with unparalleled accuracy. This has significantly reduced scrap rates and improved product reliability. Hitachi’s investment in R&D and collaboration with academic institutions has enabled the development of cutting-edge AI solutions, reinforcing its reputation for technological excellence.
The Future of Japanese Manufacturing in the Digital Era
As digital technologies continue to evolve, the future of Japanese manufacturing is poised for further transformation. Embracing the latest DX solutions will be instrumental in addressing emerging challenges and capitalizing on new opportunities.
Integration of Advanced Robotics and Automation
The continued advancement of robotics and automation will play a crucial role in enhancing production capabilities. Collaborative robots (cobots) that work alongside human operators will increase flexibility and efficiency, enabling manufacturers to adapt quickly to changing market demands.
Expansion of AI and Machine Learning Applications
AI and machine learning will increasingly be applied across various aspects of manufacturing, from predictive maintenance and quality control to supply chain optimization and customer service. These technologies will drive smarter decision-making and foster a more agile and responsive manufacturing ecosystem.
Emphasis on Sustainability and Green Manufacturing
Sustainability will become a core focus for Japanese manufacturers, driven by regulatory requirements and consumer demand for environmentally friendly products. DX solutions will facilitate the implementation of green manufacturing practices, such as energy-efficient production processes and waste reduction initiatives.
Enhanced Human-Machine Collaboration
The synergy between human expertise and machine intelligence will be pivotal in driving innovation and maintaining competitive advantage. Enhanced human-machine collaboration will empower employees to focus on value-added activities, fostering a culture of creativity and continuous improvement.
Conclusion: Unlocking the Full Potential of Japanese Manufacturing Through DX
Digital Transformation represents a critical enabler for Japanese manufacturers seeking to maintain their leadership position in the global market. By embracing the latest DX solutions, manufacturers can enhance operational efficiency, improve quality control, and foster innovation. While challenges such as high initial investments, technical complexities, and cybersecurity risks exist, adopting best practices and strategic approaches can mitigate these obstacles. Effective supplier negotiation, informed by data-driven insights, and a deep understanding of market conditions are essential for optimizing procurement and purchasing strategies. Real-world case studies demonstrate the tangible benefits of successful DX implementation, offering valuable lessons for others to follow. As the digital landscape continues to evolve, Japanese manufacturers must remain agile and committed to continuous improvement to unlock their full potential and achieve sustained success in the digital era.
資料ダウンロード
QCD管理受発注クラウド「newji」は、受発注部門で必要なQCD管理全てを備えた、現場特化型兼クラウド型の今世紀最高の受発注管理システムとなります。
ユーザー登録
受発注業務の効率化だけでなく、システムを導入することで、コスト削減や製品・資材のステータス可視化のほか、属人化していた受発注情報の共有化による内部不正防止や統制にも役立ちます。
NEWJI DX
製造業に特化したデジタルトランスフォーメーション(DX)の実現を目指す請負開発型のコンサルティングサービスです。AI、iPaaS、および先端の技術を駆使して、製造プロセスの効率化、業務効率化、チームワーク強化、コスト削減、品質向上を実現します。このサービスは、製造業の課題を深く理解し、それに対する最適なデジタルソリューションを提供することで、企業が持続的な成長とイノベーションを達成できるようサポートします。
製造業ニュース解説
製造業、主に購買・調達部門にお勤めの方々に向けた情報を配信しております。
新任の方やベテランの方、管理職を対象とした幅広いコンテンツをご用意しております。
お問い合わせ
コストダウンが利益に直結する術だと理解していても、なかなか前に進めることができない状況。そんな時は、newjiのコストダウン自動化機能で大きく利益貢献しよう!
(β版非公開)