- お役立ち記事
- Unlocking Japanese Manufacturing: The Evolution of the Assembly Line in Japan
月間76,176名の
製造業ご担当者様が閲覧しています*
*2025年3月31日現在のGoogle Analyticsのデータより
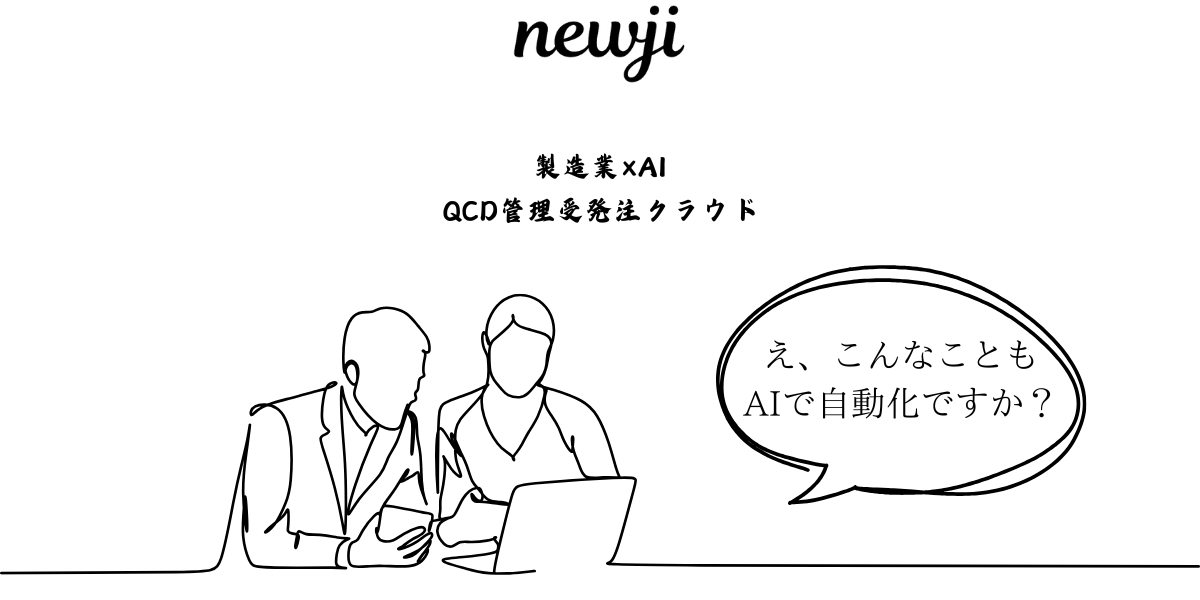
Unlocking Japanese Manufacturing: The Evolution of the Assembly Line in Japan
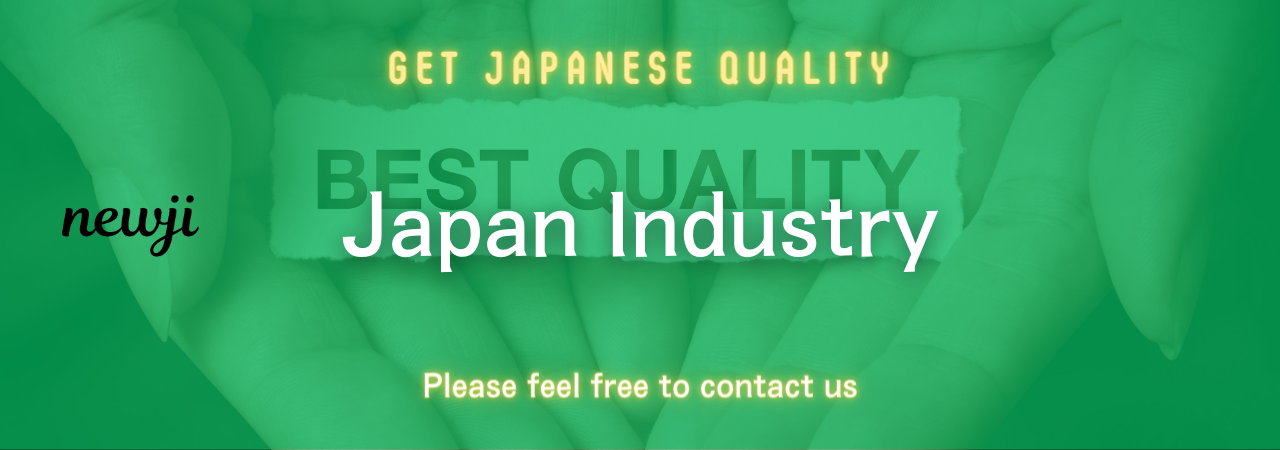
目次
Understanding the Historical Context of Japanese Manufacturing
The idea of “Japanese manufacturing” often evokes images of precision, efficiency, and top-notch quality.
To truly appreciate the evolution of the assembly line in Japan, it’s essential to understand the country’s post-World War II industrial history.
Facing widespread devastation, Japan was committed to rebuilding its economy by focusing heavily on industrial growth.
This period saw the adoption and adaptation of numerous Western manufacturing techniques, which Japanese firms meticulously evolved and perfected over decades.
The Influence of Lean Manufacturing and the Toyota Production System (TPS)
One cannot discuss the evolution of the assembly line in Japan without mentioning Lean Manufacturing and the Toyota Production System (TPS).
Developed by Taiichi Ohno and Eiji Toyoda during the mid-20th century, TPS revolutionized how cars were manufactured.
It introduced concepts such as “Just-in-Time” (JIT) production and “Jidoka” (automation with a human touch), ensuring that workers had greater control over quality.
The JIT technique minimizes inventory costs by receiving goods only as they are needed in the production process.
This reduces waste and increases efficiency.
Jidoka, on the other hand, empowers workers to halt the production line if they identify any defects, ensuring that quality is maintained at every stage.
Practical Application of Lean Manufacturing
The principles of Lean Manufacturing extend beyond the automotive sector.
Companies in various industries, from electronics to pharmaceuticals, have adopted these principles to enhance operational efficiency.
I’ve seen numerous factories where streamlining processes, reducing waste, and embracing a culture of continuous improvement have led to significant productivity gains.
By maximizing value and minimizing waste, Japanese manufacturing has set global benchmarks.
Advantages of Japanese Manufacturing Techniques
The benefits of Japanese manufacturing techniques are well-documented.
Firstly, the emphasis on quality control ensures that products are reliable and meet high customer expectations.
Secondly, the focus on efficiency translates to cost savings, which can be passed on to consumers.
Thirdly, the collaborative nature of Japanese workplace culture fosters innovation.
Employees at all levels are encouraged to suggest improvements, leading to a system of perpetual innovation and operational refinement.
Value Engineering and Target Costing
Japanese manufacturers often employ value engineering and target costing to deliver affordable yet high-quality products.
Value engineering involves finding cost-effective alternatives without compromising functionality.
Target costing, on the other hand, works backward from the product’s market price to ensure that costs remain within acceptable limits.
Both these methods emphasize striking a balance between cost and quality.
Challenges and Disadvantages of Japanese Manufacturing Techniques
While there are numerous advantages, it’s important to recognize the challenges and limitations inherent in Japanese manufacturing techniques.
Implementing such systems may require significant time and investment.
Organizations must foster a culture of continuous improvement, which can be demanding and sometimes resistant to change.
Moreover, the intricate supply chain networks essential for JIT processes are susceptible to disruptions, which can lead to production delays.
Dependency on Supplier Networks
Japanese manufacturers often establish long-term relationships with a limited number of suppliers, fostering mutual trust and reliability.
However, this dependency can be a double-edged sword.
If a key supplier faces operational issues, it can impact the entire production line.
Building a resilient and adaptable supply chain is critical to mitigating such risks.
Negotiation Techniques with Japanese Suppliers
Navigating supplier negotiations in Japan can differ significantly from Western practices.
Japanese business culture places high importance on building long-term relationships based on mutual respect and trust.
Rushing through the negotiation process can be seen as disrespectful.
Thus, it’s essential to exhibit patience, show a genuine interest in the supplier’s needs, and aim for a mutually beneficial agreement.
Building Trust and Long-Term Relationships
Japanese suppliers value consistency and reliability.
The willingness to engage in open, honest communication fosters trust and strengthens partnerships.
Regular face-to-face meetings, though time-consuming, are crucial.
Over time, these efforts translate into more favorable terms and better cooperation.
Understanding “Omotenashi” in Business Meetings
The concept of “Omotenashi” – anticipatory hospitality – is deeply rooted in Japanese culture.
In a business context, this implies going the extra mile to meet the needs of your counterpart.
Demonstrating sincere hospitality and respect during negotiations can significantly enhance the relationship, leading to more successful outcomes.
Current Market Conditions
Japan’s manufacturing sector continues to evolve, driven by advancements in technology and changing global market conditions.
While domestic challenges such as an aging workforce and economic stagnation persist, Japanese manufacturers are increasingly leveraging automation and artificial intelligence to enhance productivity.
In recent years, there has been a shift towards sustainable manufacturing practices, with companies investing in eco-friendly technologies to reduce their environmental footprint.
Adapting to Technological Advancements
The integration of IoT (Internet of Things) into assembly lines has significantly enhanced operational efficiency.
Real-time monitoring and predictive maintenance help in identifying potential issues before they disrupt production, resulting in significant cost savings.
Innovative technologies such as robotic process automation (RPA) and advanced analytics are increasingly being integrated into manufacturing processes to enhance precision and efficiency.
Best Practices for Engaging with Japanese Manufacturers
In working with Japanese manufacturers, adhering to certain best practices can facilitate smoother interactions and better results.
Understanding cultural nuances and being prepared for the negotiation process are fundamental.
Emphasizing Kaizen Culture
Kaizen, or continuous improvement, is a core tenet of Japanese manufacturing philosophy.
Demonstrate your commitment to this principle by consistently seeking ways to enhance processes and products.
Engage in collaborative problem-solving and encourage feedback from all levels of the organization.
Respecting Hierarchical Structures
Japanese business culture places a strong emphasis on hierarchy and respect for seniority.
Ensure that your communication is appropriate and respectful, particularly in formal settings.
Understanding and respecting these structures will facilitate better relationships and smoother negotiations.
Leveraging Cross-Functional Teams
Japanese manufacturing companies often utilize cross-functional teams to address complex issues.
Embrace this approach by forming diverse teams with varied expertise to tackle challenges collaboratively.
This not only fosters innovation but also ensures comprehensive solutions.
The Future of Japanese Assembly Lines
The future of assembly lines in Japan appears promising, with a continued focus on innovation and efficiency.
Manufacturers are investing in cutting-edge technologies such as AI, robotics, and IoT to stay competitive.
Sustainable practices and green manufacturing are becoming integral to the industry’s development.
Collaborative Robotics (Cobots)
Cobots, or collaborative robots, are increasingly being used to work alongside human operators on the assembly line.
These robots enhance productivity and reduce physical strain on workers, culminating in a more efficient and humane manufacturing process.
With advancements in AI, these cobots are becoming increasingly sophisticated and capable of performing complex tasks.
Smart Manufacturing and Industry 4.0
The concept of Industry 4.0 involves the use of advanced digital technologies to create smart factories.
Japanese manufacturers are at the forefront of this revolution, leveraging big data, IoT, and AI to enhance decision-making and optimize operations.
The integration of these technologies fosters greater agility and responsiveness, which is crucial in a fast-evolving market landscape.
Focus on Sustainability
There is a growing emphasis on sustainable manufacturing practices in Japan.
From reducing waste and carbon emissions to adopting renewable energy sources, manufacturers are actively working towards greener operations.
In conclusion, the evolution of the assembly line in Japan showcases a remarkable journey of innovation, adaptation, and continuous improvement.
By embracing principles such as Lean Manufacturing and Kaizen, Japanese manufacturers have consistently set global benchmarks for quality and efficiency.
Navigating the nuances of Japanese business culture, understanding market conditions, and adopting best practices can unlock significant opportunities in procurement and purchasing from Japan.
資料ダウンロード
QCD管理受発注クラウド「newji」は、受発注部門で必要なQCD管理全てを備えた、現場特化型兼クラウド型の今世紀最高の受発注管理システムとなります。
ユーザー登録
受発注業務の効率化だけでなく、システムを導入することで、コスト削減や製品・資材のステータス可視化のほか、属人化していた受発注情報の共有化による内部不正防止や統制にも役立ちます。
NEWJI DX
製造業に特化したデジタルトランスフォーメーション(DX)の実現を目指す請負開発型のコンサルティングサービスです。AI、iPaaS、および先端の技術を駆使して、製造プロセスの効率化、業務効率化、チームワーク強化、コスト削減、品質向上を実現します。このサービスは、製造業の課題を深く理解し、それに対する最適なデジタルソリューションを提供することで、企業が持続的な成長とイノベーションを達成できるようサポートします。
製造業ニュース解説
製造業、主に購買・調達部門にお勤めの方々に向けた情報を配信しております。
新任の方やベテランの方、管理職を対象とした幅広いコンテンツをご用意しております。
お問い合わせ
コストダウンが利益に直結する術だと理解していても、なかなか前に進めることができない状況。そんな時は、newjiのコストダウン自動化機能で大きく利益貢献しよう!
(β版非公開)