- お役立ち記事
- Unlocking Japanese Precision: The Hidden World of Chemical Mechanical Parts OEM
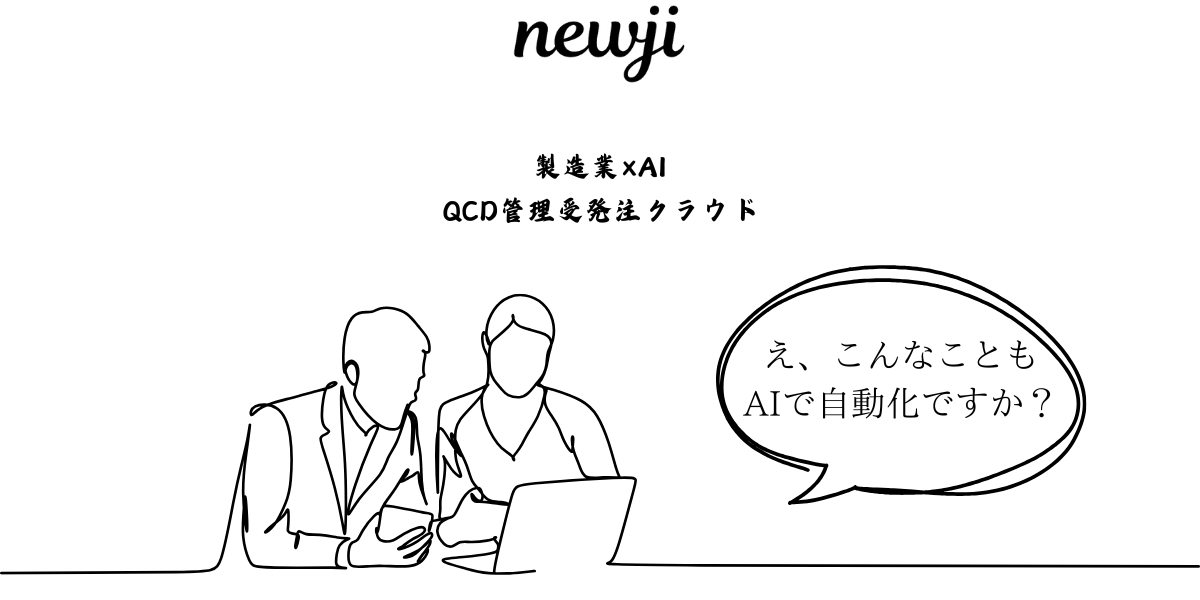
Unlocking Japanese Precision: The Hidden World of Chemical Mechanical Parts OEM
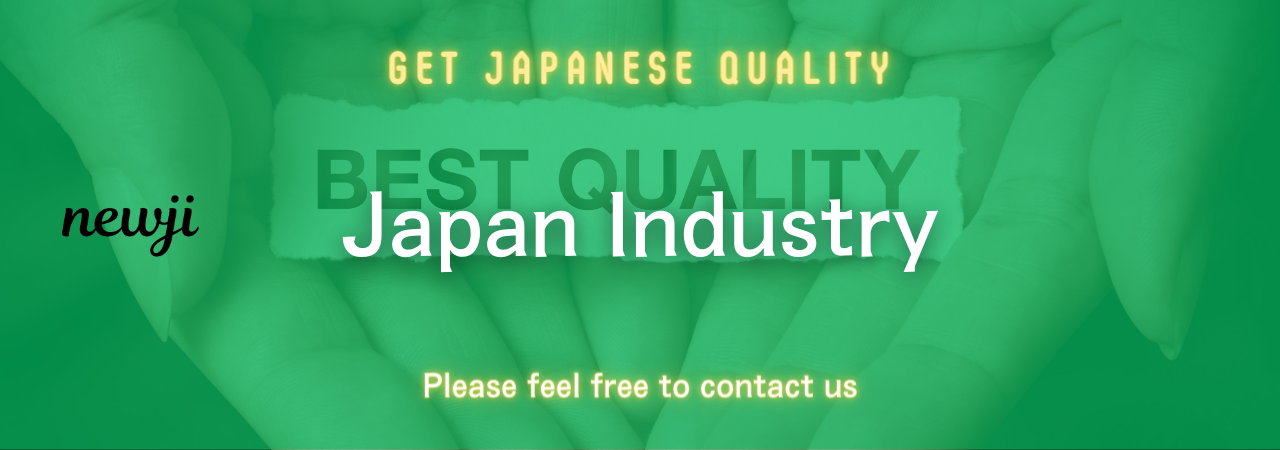
目次
Introduction
In the competitive landscape of manufacturing, precision and reliability are paramount. Japanese manufacturers have long been revered for their exceptional quality and innovative approaches, particularly in the realm of chemical mechanical parts Original Equipment Manufacturing (OEM). Unlocking the intricacies of Japanese precision involves delving into the hidden world of their OEM processes, understanding the benefits and challenges, and mastering the art of procurement and purchasing from these esteemed suppliers.
Understanding the Japanese Precision in OEM Chemical Mechanical Parts
The Legacy of Japanese Manufacturing
Japanese manufacturing boasts a rich heritage characterized by meticulous attention to detail and a relentless pursuit of excellence. Rooted in principles such as Kaizen, or continuous improvement, Japanese companies prioritize iterative enhancements, fostering a culture where quality and efficiency are ingrained in every aspect of production. This legacy has established Japan as a global leader in manufacturing, particularly in high-precision industries.
Technological Advances in Chemical Mechanical Parts
The advancements in technology within Japan’s chemical mechanical sectors are noteworthy. Japanese OEMs leverage cutting-edge machinery, automation, and advanced materials to produce components that meet stringent specifications. These technological innovations enable the creation of parts that perform reliably under demanding conditions, ensuring that end products maintain their integrity and functionality over extended periods.
Advantages of Partnering with Japanese Suppliers
Superior Quality and Reliability
Japanese suppliers are synonymous with high-quality production standards. Rigorous quality control measures are embedded throughout the manufacturing process, resulting in products that exhibit exceptional reliability and longevity. This commitment to quality minimizes defects and reduces the need for costly recalls or rework, ultimately enhancing the reputation of the purchasing company.
Advanced Technology and Innovation
Partnering with Japanese OEMs provides access to state-of-the-art technologies and innovative manufacturing techniques. These suppliers invest heavily in research and development, continuously pushing the boundaries of what is possible. This technological prowess enables purchasing companies to incorporate the latest advancements into their own products, maintaining a competitive edge in the market.
Efficient Supply Chain Management
Japanese suppliers excel in supply chain efficiency, ensuring timely delivery of components and minimizing disruptions. Their streamlined logistics and inventory management systems facilitate smooth operations, allowing purchasing companies to maintain optimal inventory levels and respond swiftly to market demands. This efficiency translates to reduced lead times and enhanced overall operational performance.
Strong Emphasis on Continuous Improvement (Kaizen)
The Kaizen philosophy, deeply embedded in Japanese manufacturing, emphasizes ongoing, incremental improvements. This focus on continuous enhancement leads to consistently higher standards of production, fostering innovation and adaptability. As a result, purchasing companies benefit from suppliers who are committed to refining their processes, ensuring sustained quality and efficiency.
Disadvantages of Partnering with Japanese Suppliers
Higher Costs Compared to Other Markets
One of the primary challenges of sourcing from Japanese OEMs is the higher cost structure. Labor costs, advanced technology investments, and the premium placed on quality contribute to elevated prices. While the long-term benefits of superior quality may offset initial expenses, companies must carefully assess their budgets and cost-benefit ratios when considering Japanese suppliers.
Language and Cultural Barriers
Navigating language differences and cultural nuances can pose significant challenges in procurement and purchasing. Effective communication is crucial for clear specifications, timely responses, and successful collaborations. Misunderstandings arising from language barriers or differing business practices can lead to delays, errors, and strained relationships if not properly managed.
Longer Lead Times
Japanese manufacturing processes, while thorough and precise, may result in longer lead times compared to suppliers from regions with faster turnaround capabilities. This extended timeline can impact the agility of purchasing companies, especially in industries where rapid market changes demand swift adjustments in production and supply chain operations.
Rigorous Quality Standards
While Japan’s stringent quality standards are a significant advantage, they can also be a double-edged sword. The rigorous testing and verification processes may introduce additional steps and time into the procurement cycle. Additionally, suppliers with high standards may have less flexibility in accommodating customizations or last-minute changes, potentially limiting responsiveness to specific needs.
Supplier Negotiation Techniques
Building Trust and Long-term Relationships
Establishing trust is fundamental in negotiations with Japanese suppliers. Emphasize reliability, transparency, and a commitment to mutual growth. Long-term relationships are highly valued, and demonstrating a willingness to engage in ongoing partnerships can lead to more favorable terms and collaborative problem-solving.
Understanding Cultural Nuances
Familiarize yourself with Japanese business etiquette and cultural practices. Respect for hierarchy, consensus-based decision-making, and indirect communication styles are integral to successful negotiations. Showing an understanding and appreciation of these cultural elements can enhance rapport and facilitate smoother interactions.
Effective Communication Strategies
Clear and concise communication is essential. Ensure that all specifications, expectations, and contractual terms are meticulously documented and shared. Utilize translators or bilingual personnel when necessary to bridge language gaps. Regular updates and open lines of communication help prevent misunderstandings and keep negotiations on track.
Negotiating Terms and Conditions Favorably
Approach negotiations with a clear understanding of your company’s objectives and the supplier’s capabilities. Highlight the mutual benefits of the partnership and seek terms that align with both parties’ interests. Flexibility and creativity in structuring agreements can lead to win-win outcomes, such as volume discounts, favorable payment terms, or collaborative development initiatives.
Market Conditions for Chemical Mechanical Parts OEM in Japan
Current Trends and Developments
The Japanese chemical mechanical parts market is influenced by several key trends, including the integration of Industry 4.0 technologies, increased automation, and a focus on sustainable manufacturing practices. These developments drive the demand for more sophisticated and environmentally friendly components, shaping the strategies of OEM suppliers.
Competitive Landscape
Japan’s OEM market is highly competitive, with numerous well-established firms competing on quality, innovation, and reliability. This competitive environment fosters continuous improvement and encourages suppliers to differentiate themselves through specialized capabilities, advanced technologies, and exceptional customer service.
Regulatory Environment
Compliance with stringent regulatory standards is a critical aspect of operating within Japan’s OEM market. Suppliers must adhere to international and domestic regulations pertaining to safety, environmental impact, and quality. Understanding and navigating these regulatory frameworks is essential for successful procurement and ensures that components meet necessary compliance requirements.
Economic Factors Affecting the Market
Economic stability in Japan supports a robust manufacturing sector, but companies must remain cognizant of potential fluctuations. Factors such as exchange rates, inflation, and global economic conditions can impact the cost and availability of components. Staying informed about economic trends enables purchasing companies to make informed decisions and anticipate market shifts.
Best Practices for Successful Procurement and Purchasing
Conducting Thorough Supplier Assessments
Before entering into partnerships, perform comprehensive assessments of potential suppliers. Evaluate their financial stability, production capabilities, quality control systems, and reputation in the industry. Site visits and third-party audits can provide valuable insights into a supplier’s operations and reliability.
Leveraging Local Expertise and Partnerships
Collaborate with local experts or establish partnerships with Japanese firms to navigate the complexities of the market. Local knowledge can facilitate better communication, cultural understanding, and adherence to regional business practices, enhancing the overall procurement process.
Implementing Effective Quality Control Measures
Integrate stringent quality control protocols into the procurement process. Establish clear quality standards and regularly monitor supplier performance through audits and inspections. Utilizing advanced quality management systems aids in maintaining consistent product quality and addressing issues proactively.
Utilizing Technology for Supply Chain Optimization
Adopt technology solutions such as Enterprise Resource Planning (ERP) systems, supply chain management software, and data analytics to streamline procurement operations. These tools enhance visibility, improve forecasting accuracy, and enable more efficient inventory management, contributing to overall supply chain optimization.
Case Studies: Successful Partnerships with Japanese OEM Suppliers
Case Study 1
A leading automotive manufacturer partnered with a Japanese OEM supplier to integrate advanced chemical mechanical parts into their vehicle assembly line. By leveraging the supplier’s expertise in precision manufacturing, the company achieved significant improvements in component performance and durability. The collaboration also introduced innovative production techniques that enhanced overall manufacturing efficiency.
Case Study 2
An electronics company sought to source high-precision parts for their new line of consumer devices. After an extensive search, they established a partnership with a Japanese supplier known for their excellence in chemical mechanical component manufacturing. The partnership resulted in the successful launch of the product line, characterized by superior quality and reliability, solidifying the company’s reputation in the market.
Conclusion
Unlocking Japanese precision in the realm of chemical mechanical parts OEM offers substantial benefits, from unparalleled quality and advanced technology to efficient supply chain management. However, navigating the associated challenges such as higher costs, cultural barriers, and longer lead times requires strategic planning and adept negotiation. By understanding market conditions, implementing best practices, and fostering strong supplier relationships, purchasing companies can harness the strengths of Japanese OEM suppliers to drive innovation, enhance product quality, and achieve long-term success in the competitive manufacturing landscape.
資料ダウンロード
QCD調達購買管理クラウド「newji」は、調達購買部門で必要なQCD管理全てを備えた、現場特化型兼クラウド型の今世紀最高の購買管理システムとなります。
ユーザー登録
調達購買業務の効率化だけでなく、システムを導入することで、コスト削減や製品・資材のステータス可視化のほか、属人化していた購買情報の共有化による内部不正防止や統制にも役立ちます。
NEWJI DX
製造業に特化したデジタルトランスフォーメーション(DX)の実現を目指す請負開発型のコンサルティングサービスです。AI、iPaaS、および先端の技術を駆使して、製造プロセスの効率化、業務効率化、チームワーク強化、コスト削減、品質向上を実現します。このサービスは、製造業の課題を深く理解し、それに対する最適なデジタルソリューションを提供することで、企業が持続的な成長とイノベーションを達成できるようサポートします。
オンライン講座
製造業、主に購買・調達部門にお勤めの方々に向けた情報を配信しております。
新任の方やベテランの方、管理職を対象とした幅広いコンテンツをご用意しております。
お問い合わせ
コストダウンが利益に直結する術だと理解していても、なかなか前に進めることができない状況。そんな時は、newjiのコストダウン自動化機能で大きく利益貢献しよう!
(Β版非公開)