- お役立ち記事
- Unlocking Precision and Quality: The Rise of Tumbler OEM Manufacturing in Japan
Unlocking Precision and Quality: The Rise of Tumbler OEM Manufacturing in Japan
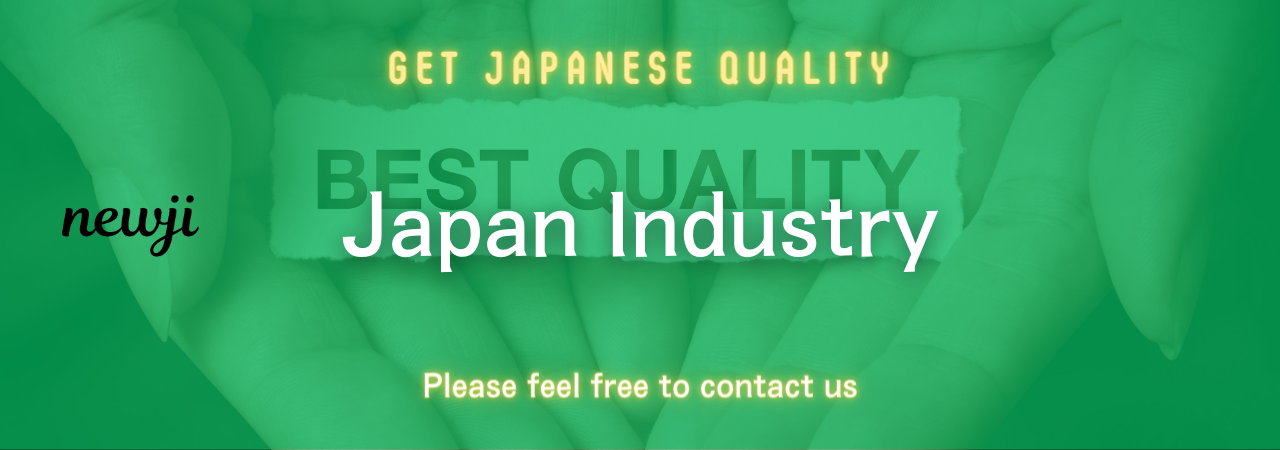
目次
Understanding Tumbler OEM Manufacturing
Definition and Overview
OEM stands for Original Equipment Manufacturer. In the context of tumbler manufacturing, OEM refers to companies in Japan that produce tumblers based on the designs and specifications provided by their clients. These manufacturers leverage their expertise to create high-quality, customized tumblers that meet specific market demands.
OEM manufacturing allows businesses to focus on branding and marketing while relying on established manufacturers to handle production. This collaboration ensures that products are made efficiently and meet stringent quality standards. Japanese OEM manufacturers are renowned for their precision and attention to detail, making them a preferred choice for many international brands.
Importance in the Global Market
The global market for tumblers has seen significant growth due to increasing consumer demand for personalized and high-quality drinkware. OEM manufacturing plays a critical role in meeting this demand by enabling companies to produce a wide range of tumblers without investing heavily in manufacturing infrastructure.
Japanese OEM manufacturers contribute to this global expansion by offering products that align with international standards. Their ability to innovate and adapt to market trends ensures that businesses can stay competitive. Additionally, the reputation of Japanese manufacturing for excellence helps brands establish trust and credibility in new markets.
Advantages of Choosing Japanese OEM Manufacturers
Precision and Quality Standards
Japanese OEM manufacturers are synonymous with high-quality production. Their commitment to precision ensures that every tumbler produced meets strict quality standards. This focus on quality minimizes defects and ensures consistency across product lines, which is essential for maintaining brand reputation.
Japanese manufacturers often implement rigorous quality control processes, including multiple inspection stages during production. This meticulous approach guarantees that the final product is not only aesthetically pleasing but also durable and functional. The emphasis on quality extends to using premium materials, which enhances the overall product value.
Technological Expertise
Japan is a global leader in manufacturing technology. Japanese OEM manufacturers utilize advanced machinery and innovative production techniques to enhance efficiency and product quality. Automation and robotics are commonly integrated into manufacturing processes, allowing for precise and scalable production.
This technological prowess enables manufacturers to offer a wide range of customization options. From intricate designs to unique materials, Japanese OEMs can accommodate diverse client requirements. Their ability to stay at the forefront of technological advancements ensures that they can produce cutting-edge products that meet evolving market needs.
Strong Supply Chain Networks
Japanese OEM manufacturers benefit from robust supply chain networks that ensure timely delivery of materials and finished products. The efficiency of these supply chains minimizes disruptions and reduces lead times, which is crucial for meeting customer demands promptly.
Moreover, Japan’s strategic location and excellent infrastructure facilitate smooth logistics and distribution. This reliability is a significant advantage for businesses looking to maintain consistent production schedules. The strong supply chain networks also enhance the ability to scale production in response to increasing demand, providing flexibility and resilience in the manufacturing process.
Disadvantages and Challenges
High Manufacturing Costs
One of the primary challenges of partnering with Japanese OEM manufacturers is the higher cost of production. Labor costs in Japan are relatively high compared to other manufacturing hubs, which can result in increased overall expenses. Additionally, the emphasis on quality and precision often involves more expensive materials and advanced technologies, further driving up costs.
For businesses with tight budgets, these higher costs can be a barrier to entry. It’s essential to weigh the benefits of superior quality and reliability against the increased financial investment required. However, many companies find that the long-term benefits of partnering with reputable Japanese manufacturers justify the initial costs.
Cultural and Language Barriers
Navigating cultural and language differences can pose significant challenges in international partnerships. Effective communication is crucial for successful collaboration, and misunderstandings can lead to delays and errors in production. Japanese business practices emphasize formality and respect, which can be unfamiliar to partners from different cultural backgrounds.
To mitigate these challenges, it’s important to establish clear communication channels and possibly engage bilingual representatives or translators. Building strong relationships and taking the time to understand Japanese business etiquette can also enhance collaboration and reduce potential friction.
Long Lead Times
The precision and thoroughness inherent in Japanese manufacturing processes can result in longer lead times compared to other regions. While the emphasis on quality is a significant advantage, it may not align with businesses that require rapid production cycles. Longer lead times can impact the ability to respond quickly to market changes or unexpected demand spikes.
Businesses must plan accordingly and build adequate lead time buffers into their production schedules. Effective forecasting and inventory management can help mitigate the impact of longer lead times, ensuring that supply meets demand without compromising on quality.
Supplier Negotiation Techniques
Building Relationships
In Japanese business culture, building strong personal relationships is fundamental to successful negotiations. Establishing trust and rapport with suppliers can lead to more favorable terms and a better working relationship. Regular communication, face-to-face meetings, and showing respect for Japanese customs can strengthen these relationships.
Investing time in relationship-building activities demonstrates commitment and can result in greater flexibility and cooperation from suppliers. Long-term partnerships are often more beneficial than short-term agreements, as they provide stability and mutual understanding.
Leveraging Cultural Insights
Understanding and respecting Japanese cultural nuances can significantly enhance negotiation outcomes. Japanese business practices emphasize group harmony, indirect communication, and consensus-building. Negotiators should approach discussions with patience and an appreciation for these cultural values.
Avoiding confrontational tactics and instead focusing on collaborative problem-solving can lead to more successful negotiations. Demonstrating cultural awareness and sensitivity helps in aligning objectives and fostering a positive negotiation environment.
Negotiation Strategies
Effective negotiation with Japanese OEM manufacturers requires a strategic approach. Key strategies include:
1. **Preparation:** Thoroughly understand the supplier’s business, market position, and production capabilities. This knowledge enables informed discussions and realistic expectations.
2. **Value Proposition:** Clearly articulate the value your partnership brings to the supplier. Highlighting mutual benefits can create a more compelling case for favorable terms.
3. **Flexibility:** Be open to compromise and alternative solutions. Flexibility in negotiations can lead to creative agreements that satisfy both parties.
4. **Patience:** Recognize that negotiations may take longer due to the thorough and consensus-driven approach of Japanese businesses. Patience can lead to more sustainable agreements.
By implementing these strategies, businesses can navigate negotiations more effectively and establish strong, mutually beneficial partnerships.
Market Conditions for Tumbler OEM in Japan
Current Trends
The tumbler OEM market in Japan is influenced by several key trends that shape production and design. Sustainability is a significant trend, with increasing demand for eco-friendly materials and manufacturing processes. Manufacturers are adopting sustainable practices to meet consumer preferences and regulatory requirements.
Customization is another prominent trend, with consumers seeking personalized and unique designs. Japanese OEM manufacturers are leveraging advanced technologies to offer extensive customization options, catering to diverse customer needs. Additionally, there is a growing emphasis on smart and functional features, such as thermal insulation and integrated technology, enhancing the usability of tumblers.
Competitive Landscape
Japan’s OEM manufacturing sector is highly competitive, with numerous established players vying for market share. Competition drives innovation and excellence, ensuring that manufacturers continuously improve their offerings. Companies differentiate themselves through quality, technological advancements, and the ability to meet specific client requirements.
Collaborations and partnerships are common strategies for gaining a competitive edge. By working closely with clients and understanding their unique needs, OEM manufacturers can tailor their services to stand out in the crowded market. Continuous improvement and responsiveness to market demands are essential for maintaining competitiveness.
Future Outlook
The future of tumbler OEM manufacturing in Japan looks promising, driven by ongoing technological advancements and evolving consumer preferences. The integration of smart technologies and sustainable practices is expected to continue, further enhancing product offerings and market appeal.
As global demand for high-quality, customized tumblers grows, Japanese manufacturers are well-positioned to capitalize on these opportunities. Innovations in materials, design, and production processes will likely shape the future of the industry, ensuring that Japanese OEM manufacturers remain leaders in precision and quality.
Best Practices in Procurement and Purchasing
Due Diligence and Supplier Evaluation
Conducting thorough due diligence is crucial in selecting the right OEM manufacturer. Evaluating potential suppliers involves assessing their production capabilities, quality control processes, financial stability, and compliance with industry standards. Visiting manufacturing facilities and meeting with key personnel can provide deeper insights into their operations and reliability.
Establishing clear criteria for supplier evaluation helps in identifying partners that align with business objectives and quality expectations. Transparency and openness during this process foster trust and set the foundation for successful long-term partnerships.
Contract Management
Effective contract management ensures that all parties adhere to agreed-upon terms and conditions. Contracts should clearly outline specifications, pricing, delivery schedules, quality standards, and responsibilities. Including clauses for handling disputes and ensuring compliance can prevent misunderstandings and protect both parties’ interests.
Regularly reviewing and updating contracts as needed helps in adapting to changing circumstances and maintaining a strong working relationship. Clear communication and documentation are key components of successful contract management.
Quality Control Measures
Implementing robust quality control measures is essential in maintaining the high standards associated with Japanese OEM manufacturing. This includes setting clear quality criteria, conducting regular inspections, and utilizing advanced testing methods to ensure that products meet specified requirements.
Collaborating with manufacturers to establish quality control protocols enhances consistency and reliability. Continuous monitoring and feedback loops allow for the identification and resolution of issues promptly, ensuring that the final products exceed customer expectations.
Conclusion
The rise of tumbler OEM manufacturing in Japan is a testament to the country’s commitment to precision, quality, and innovation. Japanese OEM manufacturers offer significant advantages, including high-quality production, technological expertise, and robust supply chain networks. However, businesses must navigate challenges such as higher costs, cultural barriers, and longer lead times to fully leverage these benefits.
Effective supplier negotiation techniques, understanding market conditions, and adopting best practices in procurement and purchasing are crucial for successful partnerships. As the market continues to evolve, Japanese OEM manufacturers are well-positioned to meet the growing demand for high-quality, customized tumblers, offering businesses the opportunity to enhance their product offerings and achieve sustained success in the global market.
資料ダウンロード
QCD調達購買管理クラウド「newji」は、調達購買部門で必要なQCD管理全てを備えた、現場特化型兼クラウド型の今世紀最高の購買管理システムとなります。
ユーザー登録
調達購買業務の効率化だけでなく、システムを導入することで、コスト削減や製品・資材のステータス可視化のほか、属人化していた購買情報の共有化による内部不正防止や統制にも役立ちます。
NEWJI DX
製造業に特化したデジタルトランスフォーメーション(DX)の実現を目指す請負開発型のコンサルティングサービスです。AI、iPaaS、および先端の技術を駆使して、製造プロセスの効率化、業務効率化、チームワーク強化、コスト削減、品質向上を実現します。このサービスは、製造業の課題を深く理解し、それに対する最適なデジタルソリューションを提供することで、企業が持続的な成長とイノベーションを達成できるようサポートします。
オンライン講座
製造業、主に購買・調達部門にお勤めの方々に向けた情報を配信しております。
新任の方やベテランの方、管理職を対象とした幅広いコンテンツをご用意しております。
お問い合わせ
コストダウンが利益に直結する術だと理解していても、なかなか前に進めることができない状況。そんな時は、newjiのコストダウン自動化機能で大きく利益貢献しよう!
(Β版非公開)