- お役立ち記事
- “Unlocking Precision: How Japanese Manufacturers Utilize Leak Detectors for Superior Quality Control”
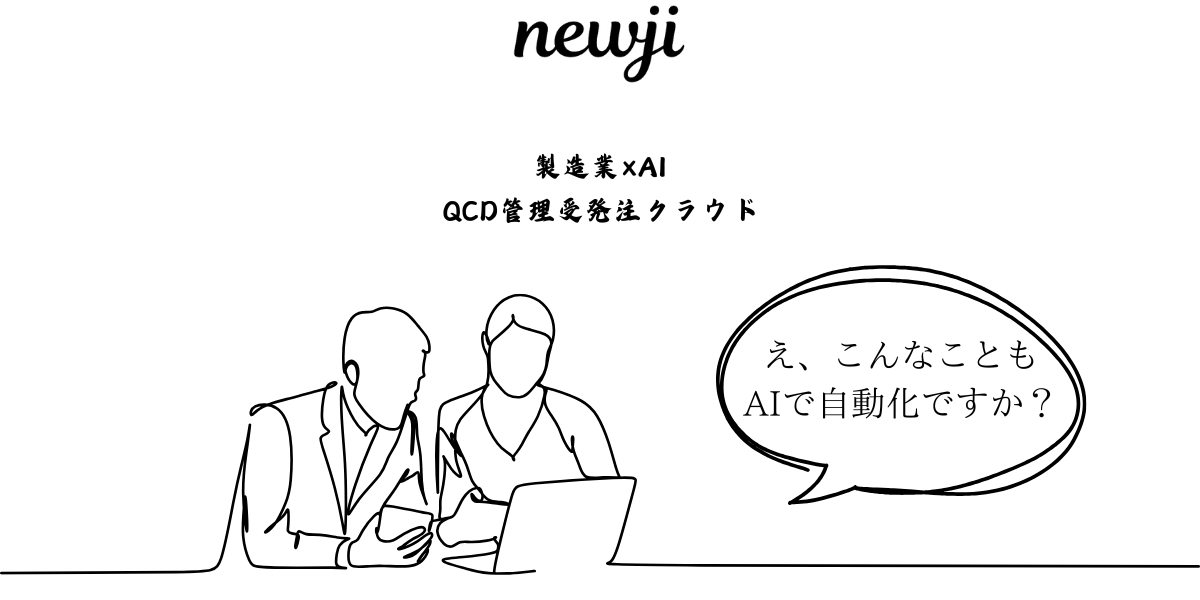
“Unlocking Precision: How Japanese Manufacturers Utilize Leak Detectors for Superior Quality Control”
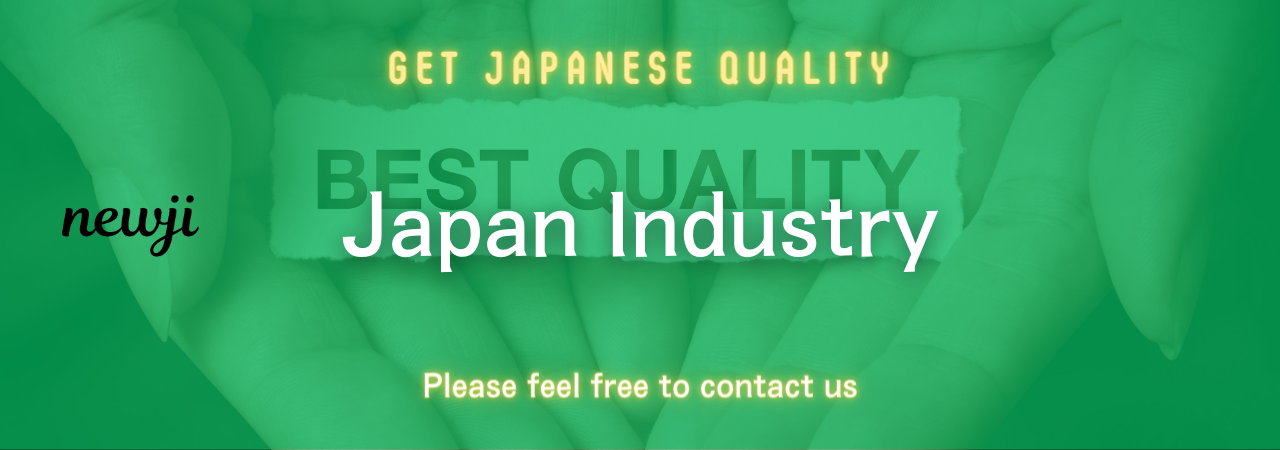
目次
Introduction
In the intricate world of manufacturing, quality control processes are paramount in ensuring product excellence and customer satisfaction.
Among various quality control tools, leak detectors have become a cornerstone, particularly within Japanese manufacturing.
In this article, we delve into how Japanese manufacturers leverage leak detectors to achieve superior quality control, offering a comprehensive guide that includes practical insights, advantages and disadvantages, negotiation techniques, market conditions, and best practices.
The Importance of Leak Detection in Manufacturing
Leak detection is a critical aspect of quality control in manufacturing, ensuring that products meet the stringent standards required in industries such as automotive, aerospace, electronics, and pharmaceuticals.
A leak, no matter how small, can compromise product integrity, safety, and functionality.
For this reason, Japanese manufacturers use advanced leak detection equipment to identify and rectify these issues before products leave the factory.
What is Leak Detection?
Leak detection involves various methodologies and equipment designed to identify and measure the presence of leaks in a system, component, or product.
Techniques can range from simple bubble tests to highly sophisticated helium mass spectrometry.
Each method has its own set of pros and cons, applicable to different scenarios depending on the level of sensitivity and precision required.
Common Methods Used in Japan
1. **Helium Mass Spectrometry**: Known for its precision, helium mass spectrometry is frequently used in Japanese manufacturing.
It involves introducing helium into the system and using a mass spectrometer to detect its presence.
This method is highly sensitive and capable of detecting extremely small leaks, making it ideal for high-stakes industries.
2. **Pressure Decay Testing**: This method measures the pressure drop in a sealed system over time.
It is widely used in applications where a larger leak would cause significant issues.
Japanese manufacturers often employ pressure decay testing for its simplicity and effectiveness.
3. **Bubble Testing**: A more traditional method, bubble testing involves immersing the component in water and looking for bubbles that indicate a leak.
Although less precise, it remains useful for quick, on-the-spot assessments and is still deployed in various stages of manufacturing.
Advantages of Leak Detectors in Japanese Manufacturing
The application of leak detectors in Japan is deeply rooted in the country’s manufacturing ethos of precision, reliability, and continuous improvement.
Enhanced Product Reliability
By employing rigorous leak detection methods, Japanese manufacturers ensure that their products are reliable and meet the highest standards of quality.
This reliability translates into a strong reputation and customer trust, which are invaluable in highly competitive markets.
Cost Reduction
Early detection of leaks prevents costly recalls and repairs down the line.
Addressing potential issues during the manufacturing process is far more economical than dealing with them post-production.
Japanese companies have long understood that investing in quality control measures like leak detection pays off in the long run.
Compliance and Regulatory Adherence
Manufacturers in Japan are often required to comply with stringent national and international regulations.
Leak detection helps them meet these requirements, avoiding legal complications and ensuring seamless entry into global markets.
Innovation and Continuous Improvement
Leak detectors enable manufacturers to continuously monitor and improve their processes.
This aligns with the Japanese philosophy of ‘Kaizen’, which focuses on continuous improvement through incremental changes.
By using leak detectors, companies can identify areas for improvement and implement solutions to enhance overall efficiency.
Disadvantages and Challenges
While the advantages are significant, there are also challenges associated with using leak detectors in manufacturing.
High Initial Investment
The upfront cost of advanced leak detection equipment can be considerable.
For smaller manufacturers, this initial investment may be a barrier.
However, Japanese companies often weigh this cost against the long-term benefits of reduced defect rates and improved product reliability.
Complexity and Training
Sophisticated leak detection methods, such as helium mass spectrometry, require specialized training to operate effectively.
The complexity of these systems can be daunting, especially for new employees.
Japanese manufacturers invest heavily in training programs to ensure their workforce is proficient in using these technologies.
False Positives and Negatives
No system is flawless, and leak detectors can sometimes produce false positives or negatives.
This can lead to unnecessary rework or, worse, undetected leaks.
Japanese companies mitigate this risk by employing multiple testing methods and rigorous verification processes.
Negotiation Techniques with Japanese Suppliers
When dealing with Japanese suppliers of leak detection equipment, it’s crucial to understand the cultural nuances and negotiation strategies that can lead to successful outcomes.
Emphasis on Relationships
Japanese business culture places a high value on building long-term relationships.
Entering negotiations with a focus on creating a mutually beneficial partnership can be more effective than a purely transactional approach.
Show respect, patience, and a genuine interest in your supplier’s concerns and business practices.
Prepare Thoroughly
Japanese suppliers appreciate detailed preparation.
Before entering negotiations, ensure you have a comprehensive understanding of your requirements, the technical specifications of the equipment, and the market conditions.
Being well-prepared demonstrates your seriousness and commitment.
Quality Over Price
While cost is always a consideration, Japanese suppliers are often more focused on quality and reliability.
Emphasize how the equipment’s features and performance align with your quality objectives rather than just negotiating for the lowest price.
Highlighting your commitment to quality can resonate well with Japanese counterparts.
Patience and Politeness
Negotiations in Japan can take time, as companies often deliberate thoroughly before making decisions.
Being patient and maintaining politeness throughout the process is essential.
Aggressive or overly assertive tactics can be counterproductive and may damage the relationship.
Market Conditions for Leak Detectors in Japan
Understanding the market conditions can help you make informed decisions when procuring leak detection equipment from Japan.
Strong Technological Leadership
Japan is a global leader in technology and innovation, reflected in its leak detection industry.
Japanese manufacturers continually invest in R&D to improve the sensitivity, reliability, and user-friendliness of their equipment.
This innovation makes Japanese leak detectors among the most advanced in the world.
Growing Demand Across Industries
The demand for leak detection equipment is increasing across various industries, including automotive, healthcare, and electronics.
As products become smaller and more complex, the need for precise leak detection becomes more critical.
Japanese manufacturers are well-positioned to meet this growing demand with their cutting-edge technologies.
Competitive Landscape
The market for leak detectors in Japan is competitive, with numerous players offering a range of solutions.
This competition drives innovation and helps ensure high standards of quality.
For international buyers, this competitive landscape can lead to better pricing and more options to choose from.
Best Practices for Utilizing Leak Detectors
To maximize the benefits of using leak detectors, it’s essential to follow best practices tailored to your specific manufacturing context.
Regular Calibration and Maintenance
Ensure that your leak detection equipment is regularly calibrated and maintained according to the manufacturer’s guidelines.
Accurate calibration is crucial for obtaining reliable results, and routine maintenance can prevent unexpected breakdowns and prolong the lifespan of the equipment.
Train Your Workforce
Provide comprehensive training for your employees on the use and interpretation of leak detection equipment.
Well-trained personnel can operate the devices more effectively, reducing the likelihood of errors and enhancing overall quality control.
Integrate with Other Quality Control Systems
Leak detectors should be integrated into your broader quality control framework.
Coordinate leak detection with other quality checks, such as visual inspections and functional testing, to create a robust, multi-layered approach to quality assurance.
Use Data Analytics
Leverage data analytics to monitor and analyze leak detection results over time.
By identifying patterns and trends, you can gain insights into potential problem areas and take proactive steps to address them.
Data-driven decision-making can lead to continuous improvements in both processes and product quality.
Conclusion
Japanese manufacturers’ use of leak detectors exemplifies their commitment to precision, reliability, and continuous improvement.
Although the initial investment and complexity can be significant, the long-term benefits in terms of cost reduction, product reliability, and regulatory compliance make it an invaluable tool in the manufacturing sector.
By understanding the nuances of supplier negotiations, staying abreast of market conditions, and adhering to best practices, industries worldwide can unlock the full potential of leak detection equipment.
Embracing these strategies not only enhances quality control but also fosters innovation and positions companies for long-term success in an increasingly competitive global market.
資料ダウンロード
QCD調達購買管理クラウド「newji」は、調達購買部門で必要なQCD管理全てを備えた、現場特化型兼クラウド型の今世紀最高の購買管理システムとなります。
ユーザー登録
調達購買業務の効率化だけでなく、システムを導入することで、コスト削減や製品・資材のステータス可視化のほか、属人化していた購買情報の共有化による内部不正防止や統制にも役立ちます。
NEWJI DX
製造業に特化したデジタルトランスフォーメーション(DX)の実現を目指す請負開発型のコンサルティングサービスです。AI、iPaaS、および先端の技術を駆使して、製造プロセスの効率化、業務効率化、チームワーク強化、コスト削減、品質向上を実現します。このサービスは、製造業の課題を深く理解し、それに対する最適なデジタルソリューションを提供することで、企業が持続的な成長とイノベーションを達成できるようサポートします。
オンライン講座
製造業、主に購買・調達部門にお勤めの方々に向けた情報を配信しております。
新任の方やベテランの方、管理職を対象とした幅広いコンテンツをご用意しております。
お問い合わせ
コストダウンが利益に直結する術だと理解していても、なかなか前に進めることができない状況。そんな時は、newjiのコストダウン自動化機能で大きく利益貢献しよう!
(Β版非公開)