- お役立ち記事
- Unlocking Success in Japanese Manufacturing: The Critical Role of Production Traceability
Unlocking Success in Japanese Manufacturing: The Critical Role of Production Traceability
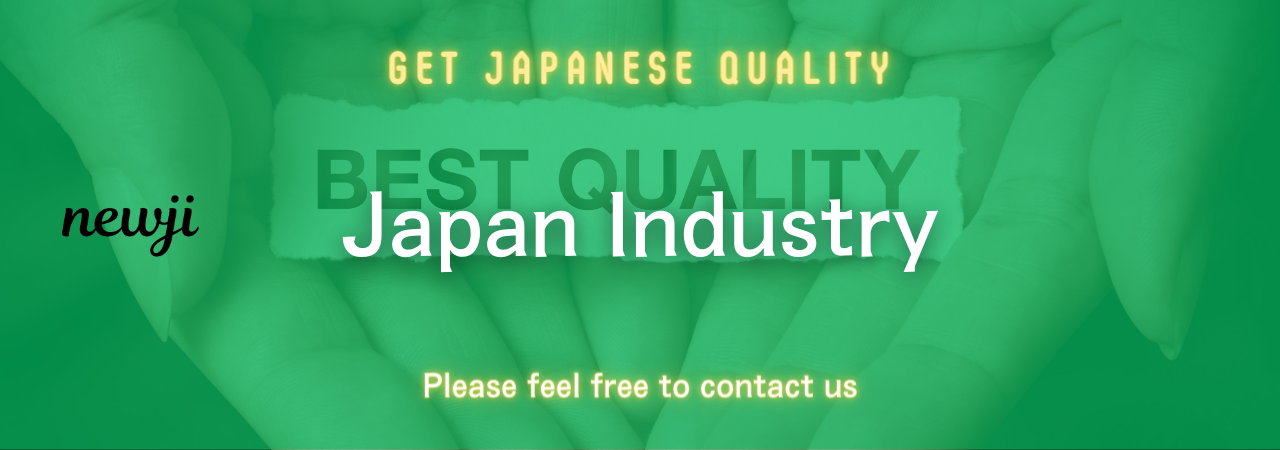
目次
Introduction to Production Traceability
Understanding the importance of production traceability is essential for any manufacturing entity striving for excellence.
Production traceability refers to the ability to track every aspect of the production process from raw materials to finished goods.
In Japanese manufacturing, traceability is not just a compliance requirement but a cornerstone of quality assurance and continuous improvement.
The History and Evolution of Traceability in Japan
Japan’s commitment to quality manufacturing dates back to the post-World War II era, spurred initially by the country’s need to rebuild its economy.
Inspired by the teachings of W. Edwards Deming and others, Japanese companies began to emphasize the importance of continuous improvement, or “Kaizen”.
In this context, traceability evolved as a method to ensure every part of the production process was scrutinized for possible improvements.
Early Adoptors and Pioneers
Companies like Toyota became early adopters of traceability practices in their production lines. The Toyota Production System (TPS) which emphasizes Just-In-Time (JIT) production and total quality management (TQM), relies heavily on the ability to track components throughout the production process.
Modern Innovations
With advancements in technology, Japanese manufacturing now employs sophisticated systems for production traceability.
RFID tags, blockchain technology, and IoT (Internet of Things) devices are some of the modern tools used to ensure that every material can be traced back to its origin.
This helps in identifying precisely where a defect may have occurred, thereby isolating issues quickly and effectively.
Advantages of Production Traceability
Implementing comprehensive traceability solutions confers numerous benefits that extend beyond mere compliance with regulatory requirements.
Quality Control
One of the foremost advantages is the enhancement of quality control. When you can trace every component back to its source, you can easily trace where errors may have occurred. This level of detail helps to maintain high standards consistently.
Cost Reduction
Traceability also allows for effective identification of inefficiencies in the production process, thereby reducing waste and lowering costs.
By knowing precisely what materials are used and where, companies can better manage their resources and reduce excess inventory.
Customer Trust
In today’s market, consumers demand transparency. Production traceability provides the data that allows companies to prove their claims about the origin and quality of their products. This builds customer trust and brand loyalty.
Challenges and Disadvantages
While the advantages are numerous, production traceability also comes with its own set of challenges.
Initial Investment
Implementing a traceability system can require significant initial investment. Costs can be high for acquiring new technologies, training staff, and updating processes.
Complexity
Another challenge is the complexity of integrating traceability systems into existing production lines. Coordination among various departments—such as procurement, production, and quality control—is crucial and often requires a cultural shift within the organization.
Data Management
The vast amount of data generated through traceability efforts also requires proper management. Without robust data analytics tools, the data collected can become overwhelming and difficult to interpret.
Effective Supplier Negotiation Tactics
Negotiating with Japanese suppliers can be unique compared to other markets. Understanding cultural nuances and prioritizing long-term relationships are often key to success.
Building Relationships
Japanese business culture places a high value on relationships. Before diving into negotiations, it is often beneficial to spend time building rapport.
Face-to-face meetings, formal introductions, and a sincere interest in mutual success can go a long way in establishing a strong foundation for negotiations.
Focus on Quality
Pricing is important, but quality often takes precedence in Japanese manufacturing. Emphasize your commitment to quality and continuous improvement as these are values deeply ingrained in Japanese business practices.
Patience and Persistence
Japanese negotiations can often be slower than in other countries. It’s important to remain patient and persistent, showing that you are committed to a long-term, mutually beneficial relationship.
Market Conditions and Trends
Understanding the market conditions and current trends can provide a significant advantage in procurement and purchasing.
Demand for Traceability
With increasing consumer awareness, the demand for traceability is growing. Companies that can demonstrate full transparency in their production processes are often valued higher, both by consumers and investors.
Sustainability
Sustainability is becoming a critical factor in procurement decisions. Japanese suppliers are increasingly focusing on eco-friendly practices, and companies that align with these values are more likely to succeed.
Technological Advancements
The integration of AI, blockchain, and IoT in traceability processes is on the rise. These advancements not only improve traceability but also offer opportunities for predictive maintenance, better quality control, and enhanced resource planning.
Best Practices in Implementing Traceability Systems
Successfully implementing a traceability system involves more than just technology; it also requires comprehensive strategy and execution.
Choosing the Right Technology
Invest in technologies that are scalable and flexible. Whether you opt for RFID, blockchain, or IoT, ensure that the system can adapt to evolving needs.
Staff Training
A well-trained workforce is critical for the success of any traceability system. Provide comprehensive training programs to ensure that staff at all levels understand the importance of traceability and how to use the systems effectively.
Continuous Monitoring and Improvement
Traceability is not a set-it-and-forget-it endeavor. Continuous monitoring and regular audits will help identify areas for improvement, ensuring that the system remains effective and reliable over time.
Conclusion
The role of production traceability in Japanese manufacturing cannot be overstated.
Its importance extends beyond regulatory compliance and cost reduction, influencing everything from quality control to customer trust and supplier relationships.
While the challenges are significant, the benefits outweigh the drawbacks.
By adopting best practices and continuously striving for improvement, companies can unlock the full potential of traceability systems, setting the stage for long-term success and competitiveness in the market.
資料ダウンロード
QCD調達購買管理クラウド「newji」は、調達購買部門で必要なQCD管理全てを備えた、現場特化型兼クラウド型の今世紀最高の購買管理システムとなります。
ユーザー登録
調達購買業務の効率化だけでなく、システムを導入することで、コスト削減や製品・資材のステータス可視化のほか、属人化していた購買情報の共有化による内部不正防止や統制にも役立ちます。
NEWJI DX
製造業に特化したデジタルトランスフォーメーション(DX)の実現を目指す請負開発型のコンサルティングサービスです。AI、iPaaS、および先端の技術を駆使して、製造プロセスの効率化、業務効率化、チームワーク強化、コスト削減、品質向上を実現します。このサービスは、製造業の課題を深く理解し、それに対する最適なデジタルソリューションを提供することで、企業が持続的な成長とイノベーションを達成できるようサポートします。
オンライン講座
製造業、主に購買・調達部門にお勤めの方々に向けた情報を配信しております。
新任の方やベテランの方、管理職を対象とした幅広いコンテンツをご用意しております。
お問い合わせ
コストダウンが利益に直結する術だと理解していても、なかなか前に進めることができない状況。そんな時は、newjiのコストダウン自動化機能で大きく利益貢献しよう!
(Β版非公開)