- お役立ち記事
- Unlocking the Future: How Electronic Module OEMs are Revolutionizing Japanese Manufacturing
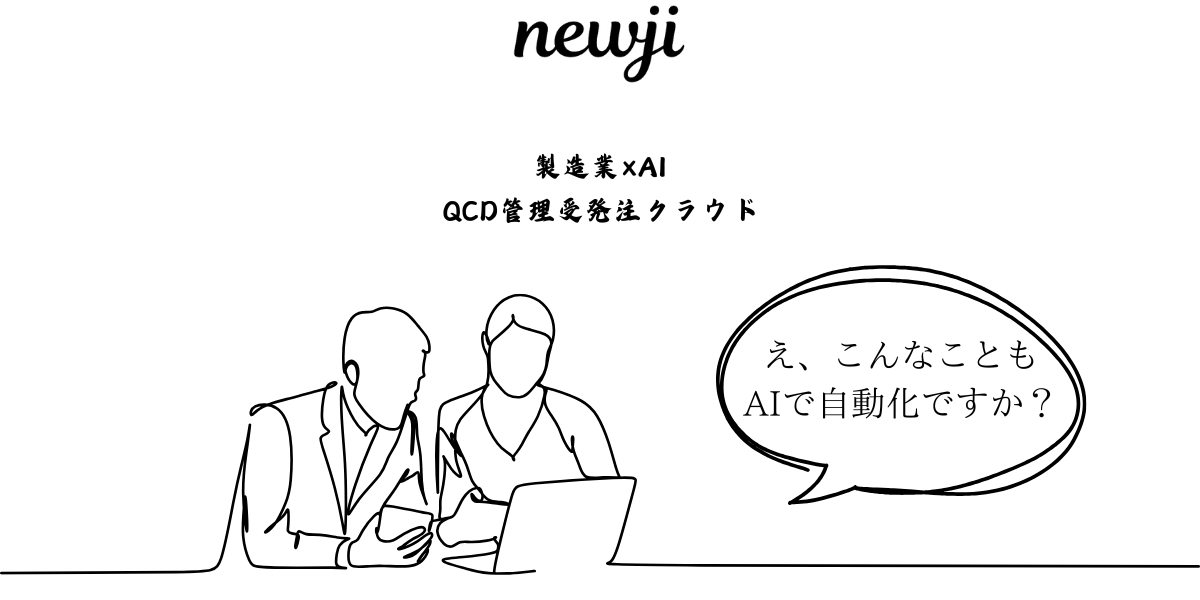
Unlocking the Future: How Electronic Module OEMs are Revolutionizing Japanese Manufacturing
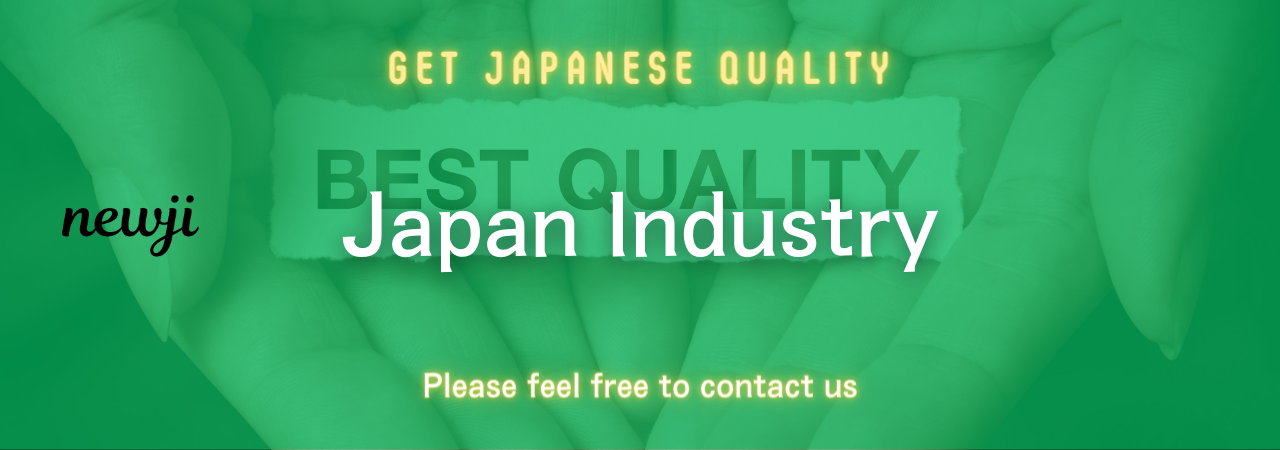
目次
Introduction
In the ever-evolving landscape of manufacturing, innovation remains crucial for staying ahead. For decades, Japanese manufacturing has set benchmarks in efficiency, quality, and technological prowess. Within this context, Electronic Module Original Equipment Manufacturers (OEMs) are playing a transformative role, revolutionizing production processes and supply chains. This article delves deep into the impact of Electronic Module OEMs on Japanese manufacturing, shedding light on their advantages, disadvantages, negotiation techniques, market conditions, and best practices.
The Evolution of Electronic Module OEMs in Japan
Historical Context
Japan’s manufacturing sector has long been synonymous with innovation and excellence. Post-World War II, Japanese companies adopted and refined concepts like Just-in-Time (JIT) production and Total Quality Management (TQM). The 1980s and 1990s saw further advancements with the integration of robotics and automation. The introduction of Electronic Module OEMs marks the latest evolution, deeply influencing how products are designed, manufactured, and distributed.
Technological Advancements
Electronic Module OEMs bring cutting-edge technology into the production environment. From advanced Printed Circuit Board (PCB) designs to data-driven manufacturing processes, these OEMs introduce efficiencies that traditional manufacturing could scarcely achieve. For instance, the incorporation of Internet of Things (IoT) technologies allows for real-time monitoring and predictive maintenance, drastically reducing downtime and increasing productivity.
Advantages of Engaging Electronic Module OEMs
Enhanced Quality Control
One of the most compelling advantages of Electronic Module OEMs is their rigorous quality control. Japanese suppliers are known for their commitment to excellence, and OEMs often adhere to stringent international standards such as ISO 9001 and ISO/TS 16949. This ensures that every component meets the highest quality criteria, translating to superior end products.
Cost Efficiency
While initial setups can be costly, the long-term benefits of working with Electronic Module OEMs often outweigh these expenses. Automated processes, bulk production capabilities, and reduced error rates contribute to significant cost savings. Additionally, Japanese OEMs excel in lean manufacturing, minimizing waste and optimizing resource use.
Speed to Market
In today’s fast-paced commercial environment, speed is crucial. Electronic Module OEMs in Japan efficiently manage the time-to-market cycle. Advanced simulations, rapid prototyping, and agile manufacturing methods enable quicker iterations and faster rollout of finished products. This agility is a significant competitive edge, allowing companies to adapt swiftly to market demands.
Challenges and Drawbacks
High Initial Investment
Entering into agreements with Electronic Module OEMs often requires a substantial initial investment. This can be daunting for small to medium enterprises. Advanced machinery, skilled labor, and rigorous quality control measures contribute to high upfront costs. However, these investments usually pay off in the long term.
Complex Supply Chains
Working with Japanese OEMs often involves navigating complex supply chains. Ensuring timely delivery, consistent quality, and efficient communication across international borders can be challenging. Establishing robust logistics and strong supplier relationships is essential to mitigate these complexities.
Cultural Differences
Understanding and aligning with Japanese business culture is crucial for a successful partnership. Japanese companies operate on principles such as “omotenashi” (hospitality) and “kaizen” (continuous improvement). Foreign companies must be willing to invest time and effort in understanding these cultural nuances to build strong, lasting relationships.
Effective Supplier Negotiation Techniques
Preparation is Key
Prior to entering negotiations, thorough preparation is crucial. Familiarize yourself with the supplier’s products, capabilities, and market reputation. Understanding your own company’s needs and limitations also allows for more effective discussions.
Building Relationships
In Japan, business relationships are built on trust and mutual respect. Unlike more transactional practices seen elsewhere, the Japanese approach emphasizes long-term collaboration. Regular visits, respectful communication, and understanding cultural etiquettes can significantly enhance negotiations.
Leveraging Technology
Digital communication tools and platforms can facilitate smoother negotiations, especially when dealing with international suppliers. Real-time data sharing, virtual meetings, and collaborative platforms can overcome time zone differences and geographic barriers.
Current Market Conditions
High Demand and Competition
The market for Electronic Module OEMs is highly competitive, influenced by the growing demand for advanced electronics in various industries, from automotive to healthcare. This high demand creates opportunities but also necessitates strategic planning to stand out.
Technological Innovations
Emerging technologies such as 5G, artificial intelligence, and augmented reality are driving the need for more sophisticated electronic modules. OEMs that can quickly adapt to these technologies and integrate them into their products will likely lead the market.
Global Supply Chain Disruptions
The COVID-19 pandemic has exposed vulnerabilities in global supply chains. It has become evident that resilient, flexible, and diversified supply chains are vital. Many companies are reevaluating their procurement strategies, focusing on risk management and supply chain robustness.
Best Practices for Working with Japanese Electronic Module OEMs
Engage in Continuous Improvement
Adopting the Japanese principle of “kaizen” emphasizes continuous improvement. Regularly review processes and seek incremental enhancements. This collaborative approach not only improves product quality but also strengthens the supplier relationship.
Invest in Training and Development
Technological advancements necessitate a skilled workforce. Investing in training programs for your team ensures they are proficient in the latest technologies and manufacturing practices. This investment pays dividends in the long run through increased efficiency and reduced errors.
Implement Robust Quality Assurance Programs
Quality should never be compromised. Implementing stringent quality assurance programs, inspired by the high standards of Japanese OEMs, ensures that products consistently meet or exceed expectations. Regular audits, supplier evaluations, and setting up a corrective action system can help maintain this high-quality standard.
Maintain Open Communication
Transparency and regular communication form the backbone of a successful partnership with Japanese suppliers. Regular updates, frequent meetings, and an open feedback loop help in identifying and resolving issues promptly. This proactive approach prevents small problems from escalating into bigger challenges.
Diversify Supplier Base
Relying on a single supplier can be risky. Diversifying your supplier base while maintaining core strategic suppliers ensures continuity even if one supplier faces disruptions. This approach adds flexibility and resilience to your supply chain.
Conclusion
Electronic Module OEMs are undeniably revolutionizing Japanese manufacturing. By embracing advanced technologies, rigorous quality control measures, and cost-efficient processes, they are setting new benchmarks in the industry. However, navigating the initial investment, complex supply chains, and cultural nuances requires strategic planning and a commitment to long-term collaboration.
The future of manufacturing lies in leveraging these advancements while maintaining strong, trust-based relationships with suppliers. By adopting best practices, engaging in continuous improvement, and investing in training, companies can unlock untold potential in their production processes.
The evolution of Japanese manufacturing, driven by Electronic Module OEMs, represents a significant opportunity for companies worldwide. Those who can effectively merge technological prowess with cultural understanding and strategic planning will undoubtedly lead the way in this new era of manufacturing excellence.
資料ダウンロード
QCD調達購買管理クラウド「newji」は、調達購買部門で必要なQCD管理全てを備えた、現場特化型兼クラウド型の今世紀最高の購買管理システムとなります。
ユーザー登録
調達購買業務の効率化だけでなく、システムを導入することで、コスト削減や製品・資材のステータス可視化のほか、属人化していた購買情報の共有化による内部不正防止や統制にも役立ちます。
NEWJI DX
製造業に特化したデジタルトランスフォーメーション(DX)の実現を目指す請負開発型のコンサルティングサービスです。AI、iPaaS、および先端の技術を駆使して、製造プロセスの効率化、業務効率化、チームワーク強化、コスト削減、品質向上を実現します。このサービスは、製造業の課題を深く理解し、それに対する最適なデジタルソリューションを提供することで、企業が持続的な成長とイノベーションを達成できるようサポートします。
オンライン講座
製造業、主に購買・調達部門にお勤めの方々に向けた情報を配信しております。
新任の方やベテランの方、管理職を対象とした幅広いコンテンツをご用意しております。
お問い合わせ
コストダウンが利益に直結する術だと理解していても、なかなか前に進めることができない状況。そんな時は、newjiのコストダウン自動化機能で大きく利益貢献しよう!
(Β版非公開)