- お役立ち記事
- Unlocking the Future: How Japanese Manufacturing Pioneers are Revolutionizing with IoT Devices
Unlocking the Future: How Japanese Manufacturing Pioneers are Revolutionizing with IoT Devices
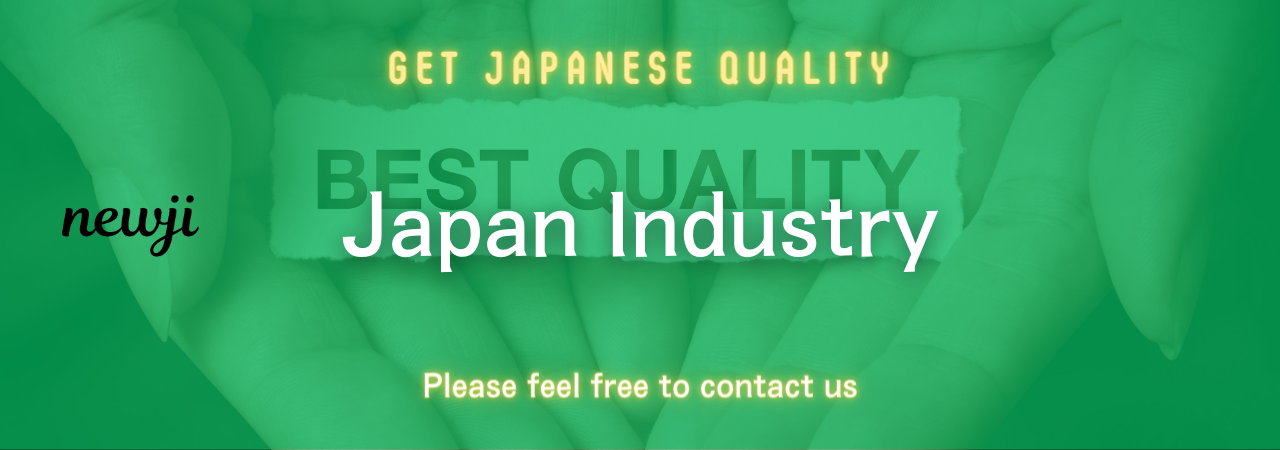
目次
Introduction
As the digital age continues to permeate every industry, the manufacturing sector stands on the precipice of a significant transformation.
Among the frontrunners in this revolution are Japanese manufacturing companies, known for their precision and innovation.
By leveraging the Internet of Things (IoT), these pioneers are unlocking new avenues for efficiency, quality, and productivity.
This article delves deeply into the myriad ways in which IoT devices are revolutionizing Japanese manufacturing, offering a comprehensive perspective on procurement and purchasing strategies, supplier negotiation techniques, market conditions, and best practices.
The Evolution of Japanese Manufacturing
Roots of Excellence
Japan’s manufacturing legacy is deeply rooted in its culture of continuous improvement and relentless pursuit of quality.
Iconic principles like Kaizen (continuous improvement) and Just-In-Time (JIT) production have laid the foundation for a manufacturing ecosystem that thrives on precision and efficiency.
These principles have seamlessly integrated with modern technological advancements, making Japan a natural leader in the adoption of IoT devices in manufacturing.
The Advent of IoT in Manufacturing
The Internet of Things, or IoT, refers to the interconnection of devices through the internet, enabling them to collect and exchange data.
In the context of manufacturing, IoT devices can range from simple sensors that track machine performance to complex systems that manage entire production lines.
The integration of IoT in manufacturing processes facilitates real-time monitoring, predictive maintenance, and enhanced data analytics, leading to unprecedented levels of operational efficiency.
Advantages of IoT in Japanese Manufacturing
Enhanced Operational Efficiency
One of the most significant advantages of IoT in manufacturing is the ability to enhance operational efficiency.
By connecting machines, equipment, and systems, manufacturers can monitor production processes in real-time and identify bottlenecks or inefficiencies.
This real-time data allows for immediate intervention, reducing downtime and optimizing production schedules.
Japanese firms, known for their meticulous attention to detail, can harness IoT to refine their already efficient processes further.
Predictive Maintenance
Predictive maintenance is another critical aspect where IoT demonstrates its value.
IoT sensors can continuously monitor the condition of machinery and predict potential failures before they occur.
By analyzing data such as vibration, temperature, and humidity, these sensors can alert maintenance teams to issues that require attention.
Japanese manufacturers can thus convert unplanned downtime into scheduled maintenance, minimizing production interruptions and extending the lifespan of machinery.
Quality Assurance
Maintaining high standards of quality is a hallmark of Japanese manufacturing.
IoT devices offer robust tools for quality assurance by enabling precise monitoring of production parameters.
Data from IoT sensors can be used to detect deviations from set standards, ensuring that products meet stringent quality criteria.
This not only reduces the risk of defective products but also minimizes waste, contributing to sustainable manufacturing practices.
Supply Chain Optimization
The interconnectivity provided by IoT extends beyond the factory floor to the entire supply chain.
Japanese manufacturers can utilize IoT to enhance transparency and traceability in their supply chains.
Sensors and RFID tags can track the movement of raw materials and finished goods in real-time, allowing for better inventory management and demand forecasting.
This level of control and visibility can significantly reduce lead times and optimize procurement and purchasing decisions.
Disadvantages and Challenges
High Initial Investment
The adoption of IoT in manufacturing is not without its challenges.
One of the primary barriers is the high initial investment required for the integration of IoT devices.
Costs associated with acquiring and installing sensors, upgrading IT infrastructure, and training personnel can be substantial.
For smaller manufacturers or those with tight budgets, these costs may pose significant hurdles.
Data Security Concerns
The increased interconnectivity brought about by IoT also raises concerns regarding data security.
With numerous devices connected to a common network, the risk of cyber-attacks and data breaches escalates.
Japanese manufacturers, known for their meticulousness, must implement robust cybersecurity measures to protect sensitive data and ensure the integrity of their operations.
Complexity in Implementation
Implementing IoT in manufacturing environments can be complex, requiring a thorough understanding of both operational requirements and technological capabilities.
Integration with existing systems and processes may pose challenges, necessitating the involvement of skilled professionals.
Japanese companies must navigate these complexities to ensure a smooth and effective transition to IoT-enabled manufacturing.
Supplier Negotiation Techniques for IoT Devices
Understanding Supplier Capabilities
When negotiating with IoT device suppliers, it is crucial to have a comprehensive understanding of their capabilities.
Japanese manufacturers should evaluate potential suppliers based on their technical expertise, product quality, and ability to offer customized solutions.
Building strong relationships with reliable suppliers can ensure the timely and successful implementation of IoT devices.
Focusing on Long-term Partnerships
Establishing long-term partnerships with IoT suppliers can be mutually beneficial.
Such relationships foster collaboration and enable continuous improvement in products and services.
Japanese firms can leverage these partnerships to stay ahead of technological advancements and ensure that their IoT implementations remain cutting-edge.
Flexibility and Scalability
Negotiations should also emphasize the importance of flexibility and scalability in IoT solutions.
Manufacturers must ensure that the IoT devices procured can adapt to evolving production needs and support future expansions.
Suppliers that offer scalable solutions and responsive customer support can add significant value to Japanese manufacturing operations.
Current Market Conditions
Growing Adoption of IoT
The global market for IoT in manufacturing is witnessing rapid growth, driven by the pursuit of digital transformation and industry 4.0 initiatives.
Japanese manufacturers are at the forefront of this trend, leveraging IoT to enhance competitiveness and operational excellence.
The increasing availability of affordable and versatile IoT devices is further fueling this adoption.
Technological Advancements
Continuous advancements in IoT technology, including improved sensors, enhanced connectivity, and advanced data analytics, are driving market growth.
Japanese manufacturers are capitalizing on these advancements to unlock new possibilities in their production processes.
Staying abreast of technological developments is essential for maintaining a competitive edge.
Regulatory Environment
The regulatory environment also plays a significant role in the adoption of IoT in manufacturing.
Government initiatives and policies that promote digital transformation and smart manufacturing can incentivize investments in IoT technology.
Japanese manufacturers must navigate regulatory frameworks to leverage potential benefits and comply with relevant standards.
Best Practices for Implementing IoT in Manufacturing
Conduct Thorough Needs Assessment
Before embarking on the implementation of IoT devices, Japanese manufacturers should conduct a thorough needs assessment.
This involves identifying specific areas where IoT can deliver the most value and defining clear objectives.
Understanding the unique requirements of the manufacturing process will guide the selection and deployment of appropriate IoT solutions.
Invest in Training and Skill Development
Implementing IoT technology necessitates a workforce that is proficient in utilizing and maintaining these devices.
Japanese manufacturers should invest in training programs to upskill their employees.
By enhancing the technical capabilities of their workforce, manufacturers can maximize the benefits of IoT and ensure smooth operations.
Ensure Robust Data Management
Effective data management is critical to harnessing the power of IoT.
Manufacturers must implement robust data collection, storage, and analysis mechanisms to extract actionable insights from IoT devices.
Japanese firms should prioritize data accuracy, security, and integration with existing systems to enable seamless information flow.
Establish a Collaborative Ecosystem
A successful IoT implementation often requires collaboration among various stakeholders, including IoT device manufacturers, system integrators, and IT service providers.
Japanese manufacturers should foster a collaborative ecosystem that encourages knowledge sharing and innovation.
Leveraging external expertise can accelerate the deployment of IoT solutions and enhance their effectiveness.
Continuous Monitoring and Improvement
IoT implementation is not a one-time effort but an ongoing process of continuous monitoring and improvement.
Japanese manufacturers should regularly assess the performance of IoT devices and make necessary adjustments to optimize their operations.
By embracing a culture of continuous improvement, they can stay ahead in the rapidly evolving manufacturing landscape.
Conclusion
The integration of IoT devices in manufacturing is revolutionizing the way Japanese companies operate, offering significant advantages in terms of efficiency, quality, and productivity.
While challenges such as high initial investments and data security concerns exist, the benefits far outweigh the drawbacks.
By adopting effective procurement and purchasing strategies, negotiating with suppliers for flexible solutions, and implementing best practices, Japanese manufacturers can fully unlock the potential of IoT technology.
As the digital era progresses, the pioneers of Japanese manufacturing will continue to lead the charge, setting new benchmarks for innovation and excellence in the industry.
資料ダウンロード
QCD調達購買管理クラウド「newji」は、調達購買部門で必要なQCD管理全てを備えた、現場特化型兼クラウド型の今世紀最高の購買管理システムとなります。
ユーザー登録
調達購買業務の効率化だけでなく、システムを導入することで、コスト削減や製品・資材のステータス可視化のほか、属人化していた購買情報の共有化による内部不正防止や統制にも役立ちます。
NEWJI DX
製造業に特化したデジタルトランスフォーメーション(DX)の実現を目指す請負開発型のコンサルティングサービスです。AI、iPaaS、および先端の技術を駆使して、製造プロセスの効率化、業務効率化、チームワーク強化、コスト削減、品質向上を実現します。このサービスは、製造業の課題を深く理解し、それに対する最適なデジタルソリューションを提供することで、企業が持続的な成長とイノベーションを達成できるようサポートします。
オンライン講座
製造業、主に購買・調達部門にお勤めの方々に向けた情報を配信しております。
新任の方やベテランの方、管理職を対象とした幅広いコンテンツをご用意しております。
お問い合わせ
コストダウンが利益に直結する術だと理解していても、なかなか前に進めることができない状況。そんな時は、newjiのコストダウン自動化機能で大きく利益貢献しよう!
(Β版非公開)