- お役立ち記事
- Unlocking the Future: How Sintering Advances Are Revolutionizing Japanese Manufacturing
月間76,176名の
製造業ご担当者様が閲覧しています*
*2025年3月31日現在のGoogle Analyticsのデータより
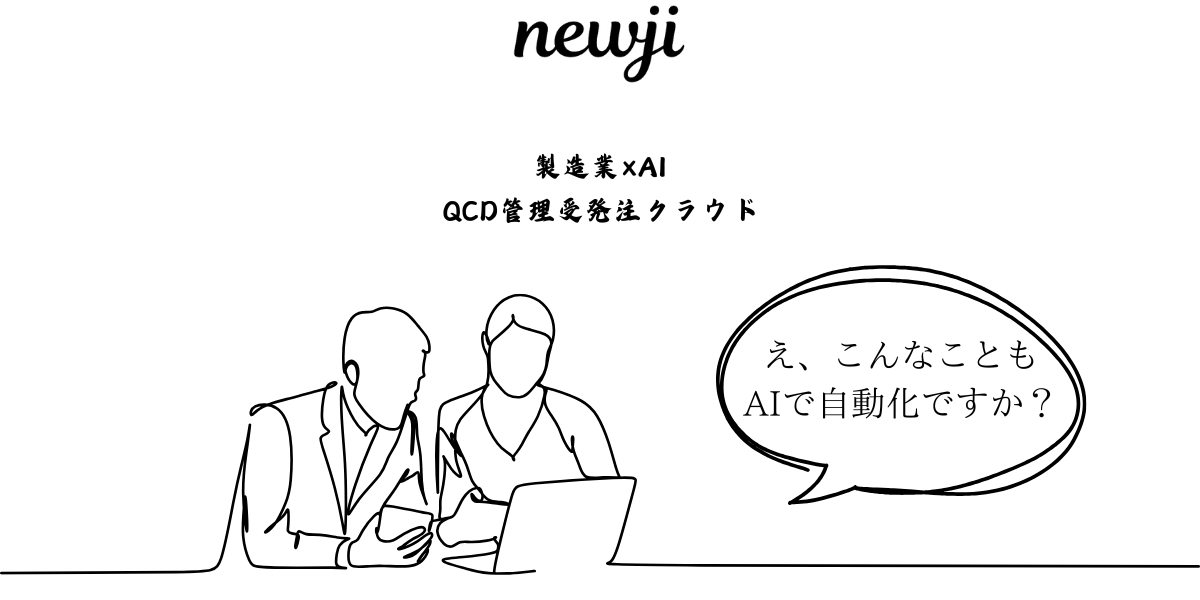
Unlocking the Future: How Sintering Advances Are Revolutionizing Japanese Manufacturing
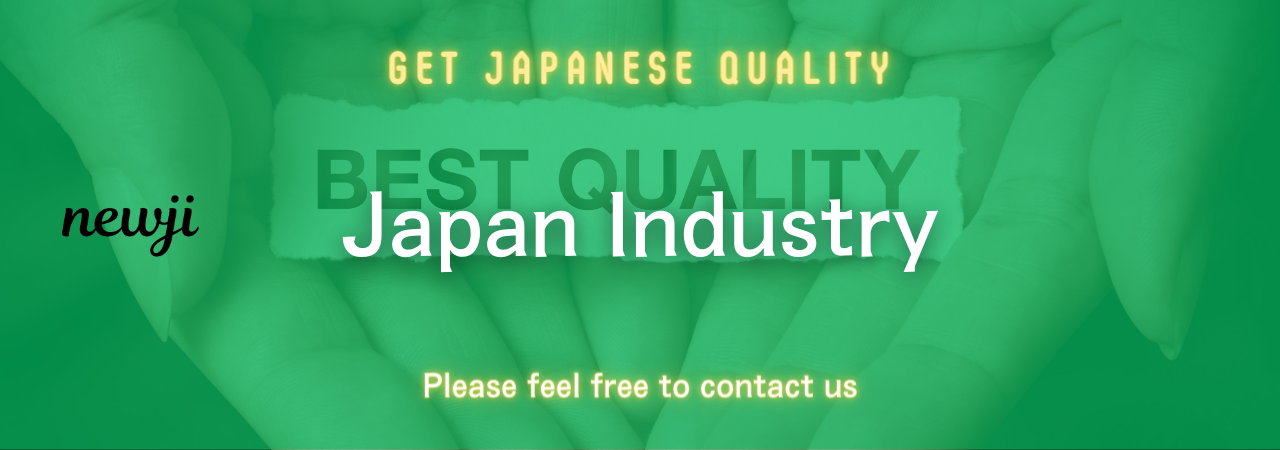
目次
Introduction
The manufacturing landscape is continuously evolving, driven by technological advancements and innovative processes.
Among these, sintering technology has emerged as a pivotal factor in revolutionizing the manufacturing sector, particularly in Japan.
Japanese manufacturers, renowned for their precision and quality, are leveraging advanced sintering techniques to enhance production efficiency and product performance.
This article delves into how sintering advances are transforming Japanese manufacturing.
From procurement and purchasing strategies to supplier negotiations and market conditions, we explore the multifaceted impact of sintering on the industry.
Understanding Sintering Technology
What is Sintering?
Sintering is a manufacturing process that involves compacting and forming materials, typically metals or ceramics, by applying heat without liquefying them.
The process enhances the material’s strength and structural integrity by facilitating particle bonding.
Sintering is widely used in producing complex components with precise specifications, making it invaluable in various industrial applications.
Recent Advances in Sintering
Recent years have witnessed significant advancements in sintering technology.
Innovations such as selective laser sintering (SLS) and microwave sintering have expanded the capabilities of traditional sintering processes.
These advancements allow for greater precision, reduced processing times, and improved material properties.
Moreover, the integration of automation and digital technologies has enhanced the efficiency and scalability of sintering operations, positioning it as a cornerstone in modern manufacturing.
The Role of Sintering in Japanese Manufacturing
Historical Context
Japan’s manufacturing prowess has long been attributed to its commitment to quality and innovation.
Sintering has been integral to various Japanese industries, including automotive, electronics, and aerospace.
Historically, Japanese manufacturers adopted and refined sintering techniques to meet stringent quality standards and optimize production processes.
Current Applications
Today, sintering is employed across diverse sectors in Japan.
In the automotive industry, sintered components are essential for engine parts and transmission systems.
The electronics sector utilizes sintering for the production of semiconductors and circuit boards.
Additionally, aerospace manufacturers rely on sintered materials for lightweight and high-strength components, crucial for performance and fuel efficiency.
Advantages of Advanced Sintering Techniques
Enhanced Material Properties
Advanced sintering techniques improve the mechanical properties of materials, such as tensile strength, hardness, and wear resistance.
This enhancement ensures that components can withstand demanding operational conditions, thereby extending their lifespan and reliability.
In Japanese manufacturing, where precision and durability are paramount, these improved material properties translate to higher quality products.
Cost Efficiency
Modern sintering processes are more cost-effective due to reduced material wastage and lower energy consumption.
Techniques like microwave sintering minimize processing times, leading to increased production rates and lower operational costs.
For Japanese manufacturers operating in competitive markets, these cost efficiencies contribute to maintaining profitability and pricing competitiveness.
Environmental Benefits
Advanced sintering processes are more environmentally friendly.
They consume less energy and produce fewer emissions compared to traditional manufacturing methods.
Moreover, the ability to recycle and reuse materials in sintering aligns with Japan’s commitment to sustainable manufacturing practices, reducing the environmental footprint of its manufacturing sector.
Challenges and Disadvantages
Technical Limitations
Despite its advantages, sintering technology faces technical challenges.
Achieving uniform density and eliminating defects in sintered materials can be difficult, especially for complex geometries.
These technical limitations require continuous research and development to enhance process control and material consistency.
High Initial Investment
Implementing advanced sintering technology entails significant upfront costs.
Investment is required for specialized equipment, training personnel, and optimizing production facilities.
For some manufacturers, particularly smaller enterprises, these initial expenses can pose a barrier to adopting sintering innovations.
Supply Chain Complexities
The intricate nature of sintering processes adds layers of complexity to the supply chain.
Securing high-quality raw materials and maintaining a reliable supply of specialized components is essential.
Moreover, coordination with suppliers to ensure timely delivery and adherence to specifications requires robust supply chain management.
Procurement and Purchasing Insights
Sourcing High-Quality Sintering Materials
Procurement teams must prioritize sourcing materials that meet stringent quality standards.
This involves evaluating suppliers based on their material consistency, reliability, and adherence to industry specifications.
Japanese manufacturers often collaborate closely with suppliers to develop customized materials that align with their specific manufacturing requirements.
Evaluating Supplier Capabilities
Assessing supplier capabilities is crucial for ensuring seamless integration of sintering processes.
This includes evaluating their technological expertise, production capacity, and ability to innovate.
Establishing long-term partnerships with suppliers who can adapt to evolving manufacturing needs is a best practice in procurement.
Negotiation Techniques with Japanese Suppliers
Negotiating with Japanese suppliers requires an understanding of cultural nuances and business practices.
Building trust and fostering mutual respect are foundational to successful negotiations.
Emphasizing long-term collaboration, transparent communication, and aligning on shared goals can lead to favorable terms and strong supplier relationships.
Market Conditions Impacting Sintering in Japan
Global Demand Trends
Global demand for high-precision and durable components drives the adoption of advanced sintering technologies.
As industries like automotive, aerospace, and electronics grow, the need for superior sintered materials increases, positioning Japanese manufacturers to capitalize on these trends.
Technological Competition
The competitive landscape is intensifying with advancements in additive manufacturing and other manufacturing technologies.
Japanese manufacturers must continuously innovate to maintain a competitive edge, integrating sintering with other technologies to enhance product offerings and operational efficiency.
Regulatory Environment
Regulatory standards related to quality, safety, and environmental impact influence sintering practices.
Compliance with both domestic and international regulations ensures that Japanese manufacturers meet global standards, facilitating market access and reducing legal risks.
Best Practices for Leveraging Sintering Advances
Building Strong Supplier Relationships
Cultivating strong partnerships with suppliers fosters innovation and reliability.
Collaborative efforts in research and development can lead to the creation of superior sintering materials and processes, benefiting both manufacturers and suppliers.
Investing in R&D Collaboration
Investing in joint R&D initiatives with suppliers and research institutions accelerates the development of advanced sintering technologies.
These collaborations enable manufacturers to stay at the forefront of innovation, adapting to changing market demands and technological advancements.
Implementing Quality Control Measures
Robust quality control systems are essential for maintaining the integrity of sintered components.
Implementing rigorous testing and inspection protocols ensures that products meet the highest standards, reducing defects and enhancing customer satisfaction.
Case Studies
Successful Implementation in Japanese Manufacturing
One prominent example is a leading Japanese automotive manufacturer that integrated selective laser sintering into its production process.
This adoption resulted in reduced component weight, improved durability, and accelerated production cycles, enhancing overall vehicle performance and market competitiveness.
Lessons Learned from Industry Leaders
Industry leaders emphasize the importance of continuous innovation and supplier collaboration.
They highlight the need for flexibility in adapting sintering processes to different applications and the value of investing in employee training to maximize the benefits of advanced technologies.
Future Outlook
Emerging Trends in Sintering Technology
Emerging trends include the integration of artificial intelligence and machine learning in sintering processes, enabling predictive maintenance and optimization.
Nanotechnology advancements are also poised to enhance material properties, further expanding the applications of sintering in high-tech industries.
Potential Impacts on the Manufacturing Landscape
As sintering technologies continue to advance, they will play a critical role in shaping the future of manufacturing.
Japanese manufacturers, with their emphasis on quality and innovation, are well-positioned to lead in this domain, driving advancements that enhance global manufacturing standards and capabilities.
Conclusion
Sintering advances are undeniably revolutionizing Japanese manufacturing, offering enhanced material properties, cost efficiencies, and environmental benefits.
Despite challenges such as technical limitations and high initial investments, the strategic procurement and purchasing approaches, coupled with robust supplier relationships, enable manufacturers to harness the full potential of sintering technologies.
As the global manufacturing landscape evolves, sintering will remain a key driver of innovation and excellence, solidifying Japan’s position as a leader in advanced manufacturing.
資料ダウンロード
QCD管理受発注クラウド「newji」は、受発注部門で必要なQCD管理全てを備えた、現場特化型兼クラウド型の今世紀最高の受発注管理システムとなります。
ユーザー登録
受発注業務の効率化だけでなく、システムを導入することで、コスト削減や製品・資材のステータス可視化のほか、属人化していた受発注情報の共有化による内部不正防止や統制にも役立ちます。
NEWJI DX
製造業に特化したデジタルトランスフォーメーション(DX)の実現を目指す請負開発型のコンサルティングサービスです。AI、iPaaS、および先端の技術を駆使して、製造プロセスの効率化、業務効率化、チームワーク強化、コスト削減、品質向上を実現します。このサービスは、製造業の課題を深く理解し、それに対する最適なデジタルソリューションを提供することで、企業が持続的な成長とイノベーションを達成できるようサポートします。
製造業ニュース解説
製造業、主に購買・調達部門にお勤めの方々に向けた情報を配信しております。
新任の方やベテランの方、管理職を対象とした幅広いコンテンツをご用意しております。
お問い合わせ
コストダウンが利益に直結する術だと理解していても、なかなか前に進めることができない状況。そんな時は、newjiのコストダウン自動化機能で大きく利益貢献しよう!
(β版非公開)