- お役立ち記事
- Unlocking the Power of Sintered Neodymium: Innovations in Japanese Manufacturing
Unlocking the Power of Sintered Neodymium: Innovations in Japanese Manufacturing
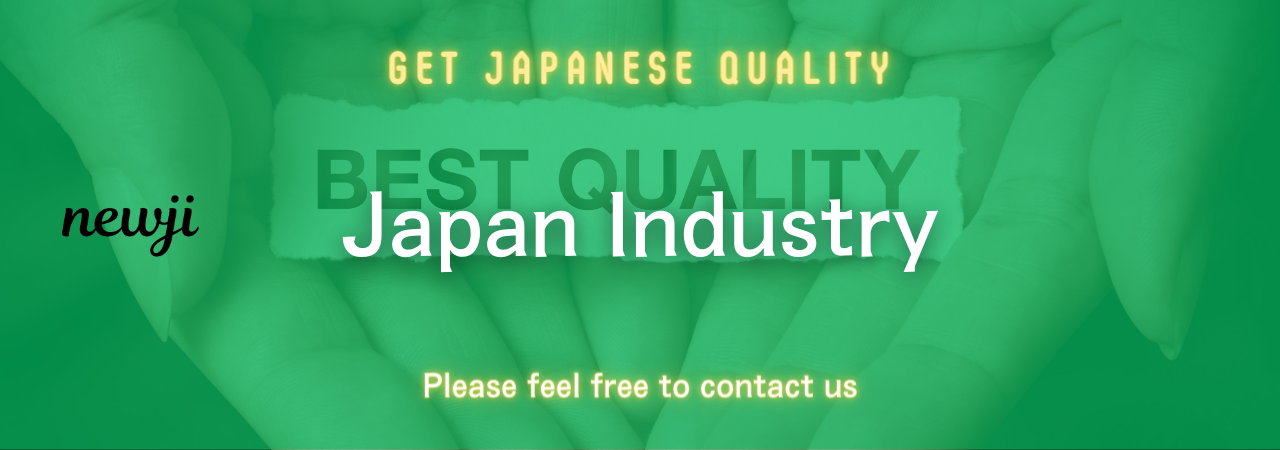
目次
Overview of Sintered Neodymium in Japanese Manufacturing
Sintered neodymium magnets have revolutionized various industries due to their exceptional magnetic properties.
Japan, renowned for its advanced manufacturing capabilities, has been at the forefront of sintered neodymium innovation.
These magnets are integral in applications ranging from electric vehicles to consumer electronics.
The precision and quality associated with Japanese manufacturing make it a preferred source for high-grade sintered neodymium.
Understanding the landscape of sintered neodymium in Japan is crucial for effective procurement and purchasing strategies.
Advancements in Sintered Neodymium Technology
Japanese manufacturers have invested heavily in research and development to enhance the performance of sintered neodymium magnets.
Innovations include improving coercivity and temperature stability, which extend the lifespan and functionality of the magnets.
Advanced manufacturing techniques, such as hot pressing and high-energy milling, contribute to the superior quality of Japanese sintered neodymium.
These technological advancements ensure that Japanese-produced magnets meet the stringent demands of modern applications.
Staying updated with these innovations is essential for procurement professionals to leverage the latest developments.
Market Conditions for Sintered Neodymium in Japan
The demand for sintered neodymium magnets in Japan has been steadily increasing, driven by growth in the electric vehicle and renewable energy sectors.
Supply chain dynamics in Japan are influenced by global market trends and domestic manufacturing capacities.
Fluctuations in raw material prices, particularly neodymium ore, impact the overall cost structure of these magnets.
Japanese manufacturers often maintain a balance between quality and cost, making them competitive in the international market.
Understanding these market conditions helps in making informed purchasing decisions and forecasting future trends.
Procurement and Purchasing Strategies
Effective procurement of sintered neodymium involves understanding both the technical specifications and the supplier landscape.
Japanese suppliers are known for their stringent quality control measures, ensuring consistency and reliability in their products.
Building strong relationships with suppliers can lead to better pricing, favorable terms, and priority in supply allocations.
Implementing just-in-time (JIT) inventory practices can optimize stock levels and reduce holding costs.
Collaborative planning with suppliers ensures that production schedules align with procurement timelines, minimizing disruptions.
Advantages of Sourcing from Japanese Suppliers
Japanese suppliers offer unmatched quality and precision in sintered neodymium magnets.
The emphasis on continuous improvement and technological innovation ensures that products remain at the cutting edge.
Strong adherence to international standards and certifications provides assurance of product reliability.
Long-term stability and reputation of Japanese manufacturers make them trustworthy partners in the supply chain.
Access to advanced manufacturing technologies and expertise enhances the overall value proposition for buyers.
Disadvantages of Sourcing from Japanese Suppliers
Higher costs compared to suppliers from other regions can be a significant drawback for budget-conscious companies.
Longer lead times due to geographical distances and shipping can affect supply chain agility.
Language and cultural barriers may complicate communication and negotiation processes.
Limited flexibility in order quantities might not suit all business models, especially for smaller orders.
Dependence on a single supplier from Japan can pose risks related to supply disruptions or geopolitical tensions.
Supplier Negotiation Techniques
Negotiating with Japanese suppliers requires a nuanced approach that respects cultural norms and business practices.
Building trust is paramount; engaging in face-to-face meetings and demonstrating commitment can strengthen relationships.
Understanding the supplier’s business and aligning mutual goals fosters a collaborative negotiation environment.
Flexible payment terms and long-term contracts can be leveraged to secure favorable pricing and priority service.
Effective negotiation also involves clear communication of requirements and expectations to avoid misunderstandings.
Cultural Considerations in Negotiations
Japanese business culture emphasizes respect, humility, and consensus-building.
Maintaining professionalism and patience during negotiations reflects positively on the buyer’s reputation.
Avoiding aggressive tactics and focusing on mutual benefits can lead to more successful outcomes.
Acknowledging the supplier’s expertise and contributions fosters goodwill and cooperation.
Building personal relationships outside formal negotiations can enhance trust and collaboration.
Leveraging Long-Term Partnerships
Establishing long-term partnerships with Japanese suppliers can result in better pricing and priority access to new technologies.
Consistent orders and reliable payment practices demonstrate commitment and reliability, encouraging suppliers to invest in the relationship.
Long-term agreements can include clauses for continuous improvement and innovation, benefiting both parties.
Collaborative forecasting and planning improve supply chain efficiency and reduce the risk of stockouts or overstocking.
Mutual support during market fluctuations strengthens the resilience of the partnership.
Best Practices in Procurement and Purchasing
Implementing best practices ensures that procurement processes are efficient, cost-effective, and aligned with organizational goals.
Regularly reviewing supplier performance through metrics such as quality, delivery, and responsiveness maintains high standards.
Diversifying the supplier base can mitigate risks associated with dependency on a single source.
Investing in procurement technology, such as ERP systems, enhances visibility and control over the purchasing process.
Continuous training and development of procurement teams keep skills sharp and adapt to evolving market conditions.
Quality Assurance and Control
Establishing stringent quality assurance protocols ensures that sintered neodymium magnets meet required specifications.
Collaborating with suppliers to implement quality control measures can reduce defects and enhance product reliability.
Regular audits and inspections help identify and address quality issues proactively.
Implementing feedback loops allows for continuous improvement in both procurement practices and supplier performance.
Maintaining documentation and traceability supports compliance with industry standards and regulations.
Cost Management and Optimization
Effective cost management involves negotiating favorable pricing, minimizing waste, and optimizing order quantities.
Bulk purchasing can lead to economies of scale, reducing the per-unit cost of sintered neodymium magnets.
Analyzing total cost of ownership, including transportation and storage, provides a comprehensive view of procurement expenses.
Implementing value engineering strategies can identify opportunities to reduce costs without compromising quality.
Regularly benchmarking prices against market rates ensures competitiveness and informs negotiation strategies.
Logistics and Supply Chain Considerations
Efficient logistics are crucial for timely delivery and overall supply chain performance.
Collaborating with reliable shipping partners and utilizing advanced logistics technologies can streamline transportation processes.
Understanding Japanese shipping protocols and customs regulations ensures smooth import operations.
Implementing inventory management systems helps balance stock levels and reduces the risk of supply chain disruptions.
Contingency planning for potential disruptions, such as natural disasters or transportation delays, enhances supply chain resilience.
Inventory Management Techniques
Adopting inventory management techniques like just-in-time (JIT) reduces holding costs and minimizes excess stock.
Forecasting demand accurately allows for better alignment of procurement with actual needs.
Implementing safety stock levels ensures that supply chain disruptions do not impact production workflows.
Utilizing automated inventory systems provides real-time visibility and control over stock levels.
Regularly reviewing inventory turnover rates helps identify inefficiencies and opportunities for improvement.
Transportation and Distribution Strategies
Selecting the appropriate transportation mode depends on factors like cost, speed, and reliability.
Collaborating with logistics providers that specialize in handling specialized magnets ensures safe and timely delivery.
Implementing track-and-trace systems provides visibility into shipment status and enhances supply chain transparency.
Optimizing distribution centers’ locations relative to production facilities reduces transportation times and costs.
Ensuring compliance with international shipping regulations prevents delays and potential penalties.
Quality Control and Continuous Improvement
Maintaining high quality in sintered neodymium magnets is essential for performance and customer satisfaction.
Japanese manufacturers often implement Total Quality Management (TQM) practices to ensure excellence.
Continuous improvement initiatives, such as Kaizen, drive incremental enhancements in manufacturing processes.
Collaboration with suppliers on quality initiatives fosters a culture of mutual excellence and accountability.
Investing in advanced quality testing and inspection technologies ensures that products meet stringent standards.
Implementing Total Quality Management (TQM)
TQM involves the entire organization in the pursuit of quality, from top management to production floor workers.
Establishing clear quality objectives and standards provides a framework for consistent performance.
Encouraging employee involvement and feedback contributes to identifying and solving quality issues effectively.
Regularly reviewing and assessing quality management systems ensures they remain effective and relevant.
Integrating customer feedback into quality improvement processes aligns product development with market needs.
Adopting Kaizen for Continuous Improvement
Kaizen, the philosophy of continuous improvement, encourages incremental changes that enhance productivity and quality.
Implementing Kaizen practices involves identifying areas for improvement and empowering employees to suggest solutions.
Regular Kaizen events or workshops facilitate focused efforts on specific process enhancements.
Documenting and standardizing successful Kaizen initiatives ensures sustained benefits and scalability.
Fostering a Kaizen culture promotes a proactive approach to problem-solving and innovation within the organization.
Factory Efficiency and Automation
Japanese manufacturing is synonymous with efficiency and automation, particularly in the production of sintered neodymium magnets.
Advanced automation technologies reduce production time and increase precision in magnet fabrication.
Robotic systems and computer-controlled machinery enhance consistency and reduce human error.
Implementing lean manufacturing principles minimizes waste and optimizes resource utilization.
Continuous monitoring and data analysis enable real-time adjustments, maintaining high levels of operational efficiency.
Implementing Lean Manufacturing Principles
Lean manufacturing focuses on eliminating waste and optimizing processes to enhance efficiency.
Value stream mapping identifies non-value-adding activities, enabling targeted improvements.
Standardizing work processes ensures consistency and simplifies training and onboarding.
Employing pull-based systems, such as Kanban, aligns production with actual demand, reducing inventory levels.
Encouraging a culture of continuous improvement supports ongoing efforts to enhance manufacturing efficiency.
Advancements in Automation Technologies
Automation technologies, including robotics and artificial intelligence, play a crucial role in modern manufacturing.
Robotic systems handle repetitive and precision-dependent tasks, increasing production speed and accuracy.
Artificial intelligence algorithms optimize production schedules and predictive maintenance, reducing downtime.
Integrating automation with IoT devices facilitates real-time monitoring and data-driven decision-making.
Investing in automation enhances scalability and adaptability, allowing manufacturers to respond swiftly to market changes.
Trade Practices and Regulatory Compliance
Navigating trade practices and ensuring regulatory compliance are critical for successful procurement of sintered neodymium from Japan.
Understanding international trade agreements and tariffs affects the overall cost and feasibility of sourcing.
Compliance with environmental regulations ensures sustainable manufacturing practices and reduces legal risks.
Adhering to product safety standards and certifications maintains market access and customer trust.
Staying informed about changes in trade policies and regulations allows for proactive adjustments in procurement strategies.
Understanding International Trade Agreements
Awareness of trade agreements between Japan and other countries can provide benefits like reduced tariffs and expedited customs processing.
Leveraging free trade agreements (FTAs) optimizes cost advantages and enhances competitive positioning.
Monitoring geopolitical developments helps anticipate changes in trade policies that may impact procurement.
Collaborating with trade experts or legal advisors ensures compliance with all relevant trade laws and regulations.
Strategic sourcing decisions consider the implications of trade agreements on long-term procurement plans.
Ensuring Environmental and Safety Compliance
Japanese manufacturers often implement stringent environmental management systems to minimize their ecological footprint.
Sourcing from compliant suppliers ensures that sintered neodymium production adheres to sustainable practices.
Environmental certifications, such as ISO 14001, provide assurance of a supplier’s commitment to environmental responsibility.
Safety compliance in manufacturing processes protects workers and reduces the risk of accidents and associated costs.
Incorporating sustainability criteria into procurement policies aligns purchasing practices with corporate social responsibility goals.
Conclusion
Unlocking the power of sintered neodymium through Japanese manufacturing requires a comprehensive understanding of the technological advancements, market conditions, and procurement strategies specific to this sector.
Japanese suppliers offer unparalleled quality and innovation, making them valuable partners in the global supply chain.
By implementing best practices in procurement, negotiation, and quality control, organizations can effectively leverage the benefits of sourcing sintered neodymium from Japan.
Staying informed about market trends and continuously improving procurement processes ensures sustained success and competitiveness in the ever-evolving manufacturing landscape.
Embracing the strengths of Japanese manufacturing can drive operational excellence and foster long-term growth and innovation.
資料ダウンロード
QCD調達購買管理クラウド「newji」は、調達購買部門で必要なQCD管理全てを備えた、現場特化型兼クラウド型の今世紀最高の購買管理システムとなります。
ユーザー登録
調達購買業務の効率化だけでなく、システムを導入することで、コスト削減や製品・資材のステータス可視化のほか、属人化していた購買情報の共有化による内部不正防止や統制にも役立ちます。
NEWJI DX
製造業に特化したデジタルトランスフォーメーション(DX)の実現を目指す請負開発型のコンサルティングサービスです。AI、iPaaS、および先端の技術を駆使して、製造プロセスの効率化、業務効率化、チームワーク強化、コスト削減、品質向上を実現します。このサービスは、製造業の課題を深く理解し、それに対する最適なデジタルソリューションを提供することで、企業が持続的な成長とイノベーションを達成できるようサポートします。
オンライン講座
製造業、主に購買・調達部門にお勤めの方々に向けた情報を配信しております。
新任の方やベテランの方、管理職を対象とした幅広いコンテンツをご用意しております。
お問い合わせ
コストダウンが利益に直結する術だと理解していても、なかなか前に進めることができない状況。そんな時は、newjiのコストダウン自動化機能で大きく利益貢献しよう!
(Β版非公開)