- お役立ち記事
- Unlocking the Secrets: How Japanese Manufacturing Excellence Translates into Global Success
月間77,185名の
製造業ご担当者様が閲覧しています*
*2025年2月28日現在のGoogle Analyticsのデータより
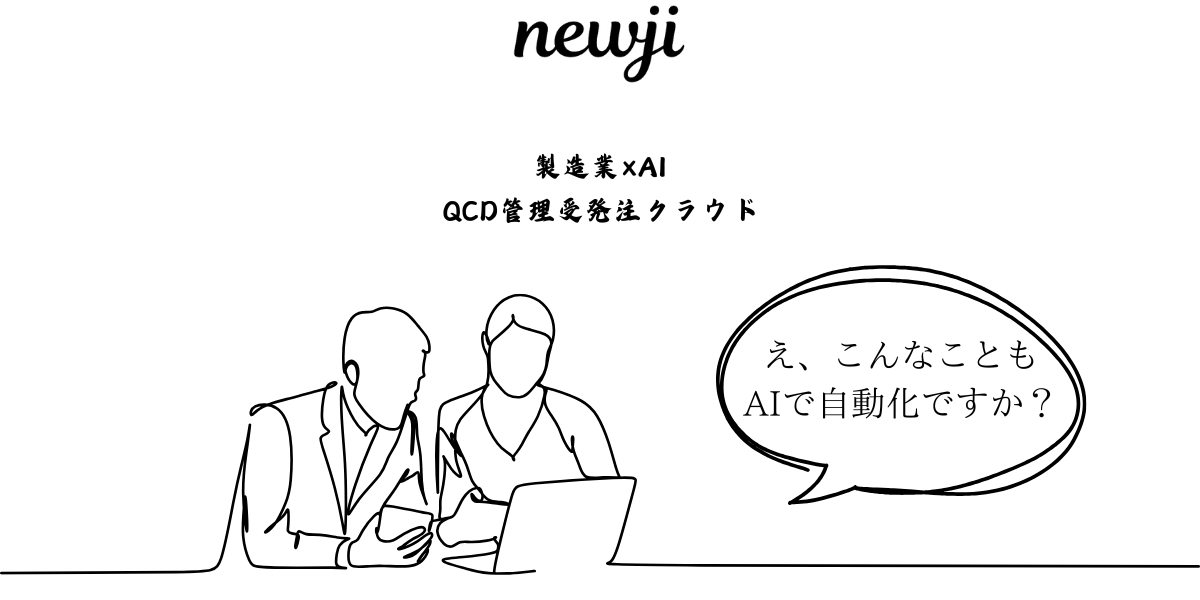
Unlocking the Secrets: How Japanese Manufacturing Excellence Translates into Global Success
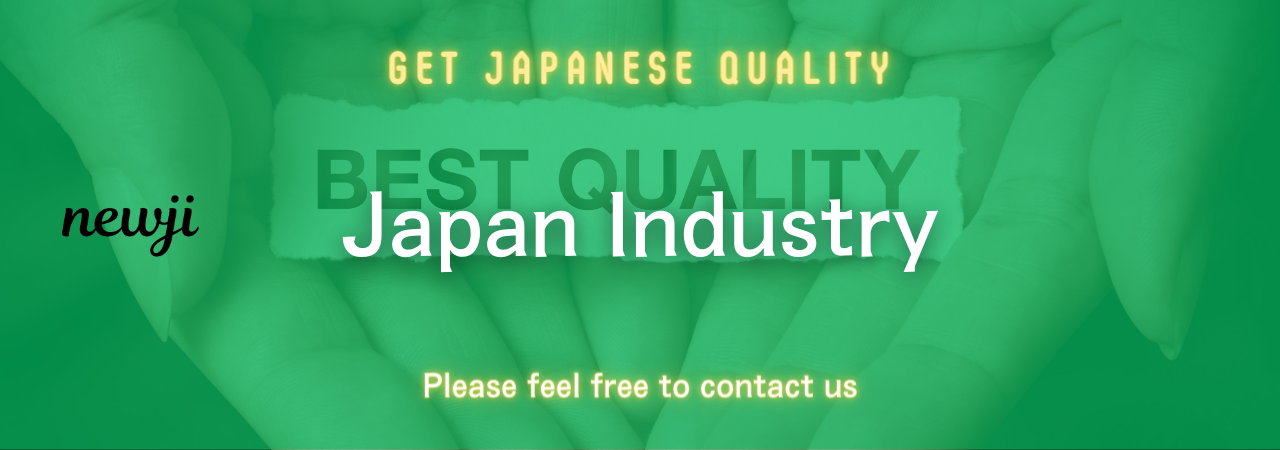
目次
Introduction to Japanese Manufacturing Excellence
Japanese manufacturing has long been synonymous with quality, efficiency, and innovation.
The global success of Japanese products and companies is a testament to the robust frameworks and philosophies ingrained in their manufacturing processes.
This article delves into the key elements that underpin Japanese manufacturing excellence and explores how these principles contribute to their global success.
We will examine procurement and purchasing strategies, supplier negotiation techniques, market conditions, best practices, and discuss the advantages and disadvantages of adopting Japanese manufacturing techniques.
The Foundation of Japanese Manufacturing
Japanese manufacturing excellence is built on a foundation of continuous improvement and respect for people.
Two core philosophies, Kaizen and Just-In-Time (JIT), play pivotal roles in this framework.
These principles not only drive efficiency but also foster a culture of collaboration and proactive problem-solving.
Kaizen: Continuous Improvement
Kaizen, which translates to “change for better,” emphasizes the importance of small, incremental changes that collectively lead to significant improvements over time.
This philosophy encourages every employee, from the shop floor to management, to actively seek ways to enhance processes, reduce waste, and improve quality.
By fostering a culture of continuous improvement, Japanese manufacturers remain agile and adaptable in the face of evolving market demands.
Just-In-Time (JIT) Manufacturing
Just-In-Time manufacturing is a strategy that aligns production schedules closely with demand.
The primary objective of JIT is to minimize inventory costs by receiving goods only as they are needed in the production process.
This approach reduces waste, increases efficiency, and ensures that resources are utilized optimally.
JIT also enhances the ability to respond swiftly to changes in the market, thereby increasing overall competitiveness.
Procurement and Purchasing Strategies
Effective procurement and purchasing are critical components of Japanese manufacturing excellence.
Japanese companies adopt strategic approaches to sourcing materials and managing supplier relationships, which contribute to their high-quality output and operational efficiency.
Strategic Sourcing
Strategic sourcing involves identifying and partnering with suppliers who can consistently deliver quality materials at competitive prices.
Japanese manufacturers prioritize long-term relationships with suppliers, fostering mutual trust and collaboration.
This approach ensures a stable supply chain and encourages suppliers to engage in continuous improvement initiatives, aligning their goals with those of the manufacturer.
Supplier Integration
Integrating suppliers into the manufacturing process is a common practice in Japan.
By involving suppliers early in the product development stage, manufacturers can ensure that materials and components meet necessary specifications and quality standards.
This collaboration also facilitates innovation, as suppliers contribute their expertise and insights to enhance product design and functionality.
Supplier Negotiation Techniques
Negotiating with suppliers is a crucial aspect of procurement and purchasing.
Japanese manufacturers employ specific techniques that balance firmness with respect, fostering mutually beneficial relationships.
Win-Win Negotiation
Japanese negotiation tactics often focus on creating win-win scenarios where both parties benefit.
This approach emphasizes understanding the supplier’s needs and constraints, allowing for compromises that satisfy both sides.
By prioritizing long-term partnerships over short-term gains, Japanese companies build loyalty and ensure reliable supply chains.
Mutual Respect and Communication
Respectful communication is fundamental in Japanese negotiations.
Clear, open dialogue helps build trust and prevents misunderstandings.
Japanese negotiators are trained to listen actively and address concerns thoughtfully, which contributes to more effective and harmonious negotiations.
Market Conditions and Adaptability
Japanese manufacturers thrive in dynamic market conditions by leveraging their adaptability and deep understanding of global trends.
Global Market Integration
Japan’s manufacturing sector is highly integrated into the global economy.
Japanese companies actively participate in international trade, adapting their products to meet diverse market needs.
This global perspective allows them to anticipate changes in consumer preferences and respond proactively.
Technological Innovation
Embracing technological advancements is a hallmark of Japanese manufacturing.
Investment in research and development leads to innovative products and production methods, keeping Japanese manufacturers at the forefront of their industries.
Technological innovation also enhances efficiency and quality, providing a competitive edge in the global market.
Best Practices in Japanese Manufacturing
Japanese manufacturers employ several best practices that contribute to their efficiency, quality, and global success.
Total Quality Management (TQM)
Total Quality Management is a comprehensive approach to quality control that involves every aspect of the organization.
TQM emphasizes customer satisfaction, continuous improvement, and the involvement of all employees in maintaining high standards.
By prioritizing quality at every stage, Japanese manufacturers ensure that their products consistently meet or exceed customer expectations.
Lean Manufacturing
Lean Manufacturing focuses on eliminating waste and optimizing processes.
Japanese manufacturers implement lean principles to streamline production, reduce costs, and increase efficiency.
By continuously analyzing and refining their operations, they achieve higher productivity and maintain competitive pricing.
Employee Empowerment and Training
Investing in employee development is crucial for maintaining manufacturing excellence.
Japanese companies provide extensive training and empower employees to take initiative in problem-solving and process improvement.
This approach not only enhances individual skills but also fosters a sense of ownership and accountability across the organization.
Advantages of Japanese Manufacturing Excellence
Adopting Japanese manufacturing principles offers numerous advantages that contribute to sustained global success.
High Quality and Reliability
The emphasis on quality control and continuous improvement ensures that Japanese products are reliable and of high quality.
This reputation for excellence builds consumer trust and loyalty, driving repeat business and positive brand recognition.
Operational Efficiency
Japanese manufacturing practices are designed to maximize efficiency and minimize waste.
Techniques like JIT and Lean Manufacturing enable companies to produce more with fewer resources, reducing costs and increasing profitability.
Strong Supplier Relationships
By fostering long-term partnerships with suppliers, Japanese manufacturers ensure a stable and reliable supply chain.
These strong relationships facilitate collaboration, innovation, and mutual growth, enhancing the overall competitiveness of the manufacturing network.
Disadvantages and Challenges
While Japanese manufacturing excellence offers many benefits, there are also challenges and potential drawbacks to consider.
Cultural Differences
Adopting Japanese manufacturing practices in non-Japanese environments can be challenging due to cultural differences.
The emphasis on hierarchy, consensus-building, and long-term relationships may not align with the corporate cultures in other countries, potentially hindering implementation.
High Implementation Costs
Implementing advanced manufacturing practices and maintaining high-quality standards can be costly.
Investments in training, technology, and infrastructure are necessary to sustain Japanese manufacturing excellence, which may be a barrier for some companies.
Resistance to Change
Organizational resistance to change can impede the adoption of Japanese manufacturing principles.
Employees and management accustomed to traditional methods may resist new practices, requiring effective change management strategies to overcome.
Adapting Japanese Practices to Global Contexts
Successfully integrating Japanese manufacturing excellence into global operations requires careful adaptation to local contexts.
Understanding Local Market Dynamics
Companies must thoroughly understand the unique characteristics and demands of their local markets.
This understanding allows for the customization of Japanese practices to fit the specific needs and expectations of different regions.
Flexibility in Implementation
While core principles like Kaizen and JIT are universal, their implementation should be flexible to accommodate local conditions.
Adapting these practices to align with local business environments and cultural norms ensures more effective integration and sustainability.
Building Cross-Cultural Teams
Effective cross-cultural collaboration is essential for blending Japanese manufacturing excellence with local practices.
Building teams with diverse cultural backgrounds fosters innovation and ensures that Japanese principles are applied in a manner that resonates with the local workforce.
Case Studies of Japanese Manufacturing Success
Examining real-world examples of Japanese companies that have achieved global success provides valuable insights into the effectiveness of their manufacturing strategies.
Toyota Motor Corporation
Toyota is a prime example of Japanese manufacturing excellence.
The company’s implementation of the Toyota Production System (TPS), which incorporates JIT and Kaizen, has set industry standards for efficiency and quality.
Toyota’s focus on continuous improvement and employee empowerment has enabled the company to remain competitive globally, maintaining its reputation for reliable and high-quality vehicles.
Panasonic Corporation
Panasonic has leveraged its commitment to innovation and quality to achieve global success in the electronics industry.
By fostering strong supplier relationships and investing in research and development, Panasonic consistently delivers cutting-edge products that meet diverse consumer needs.
Their dedication to sustainability and environmental responsibility has further strengthened their global market position.
Honda Motor Co., Ltd.
Honda’s emphasis on engineering excellence and adaptability has allowed it to thrive in various international markets.
The company’s focus on performance, fuel efficiency, and innovation has resulted in a strong global presence.
Honda’s collaborative approach with suppliers and commitment to continuous improvement contribute to its sustained success.
Implementing Japanese Manufacturing Excellence in Your Organization
Organizations looking to adopt Japanese manufacturing principles can follow a structured approach to ensure successful implementation.
Assess Current Processes
Begin by evaluating existing manufacturing processes to identify areas for improvement.
Understanding current strengths and weaknesses allows for the targeted application of Japanese practices where they can have the most significant impact.
Invest in Training and Development
Provide comprehensive training programs to educate employees about Japanese manufacturing principles.
Empowering employees with the necessary knowledge and skills is crucial for fostering a culture of continuous improvement and operational excellence.
Foster a Collaborative Culture
Encourage collaboration and open communication across all levels of the organization.
Creating an environment where employees feel valued and empowered to contribute ideas is essential for the successful adoption of Japanese manufacturing practices.
Implement Incremental Changes
Adopt a phased approach to implementing Japanese practices, starting with small, manageable changes.
Gradual implementation allows for adjustments and minimizes resistance, ensuring a smoother transition and long-term sustainability.
Measuring Success and Continuous Improvement
To ensure that the adoption of Japanese manufacturing excellence yields the desired outcomes, organizations must establish metrics and continuously monitor performance.
Key Performance Indicators (KPIs)
Identify and track KPIs that align with Japanese manufacturing principles, such as production efficiency, defect rates, and supplier performance.
Regularly reviewing these metrics helps identify areas for further improvement and ensures that the organization remains on track to achieve its goals.
Feedback Mechanisms
Establish robust feedback mechanisms to gather input from employees, suppliers, and customers.
Feedback provides valuable insights into the effectiveness of implemented practices and highlights opportunities for refinement and enhancement.
Continuous Learning and Adaptation
Commit to a culture of continuous learning and adaptation, as advocated by the Kaizen philosophy.
Encouraging ongoing education and staying abreast of industry trends ensures that the organization remains innovative and responsive to changing market conditions.
Conclusion
Japanese manufacturing excellence offers a wealth of strategies and practices that can drive global success.
By embracing principles such as continuous improvement, strategic sourcing, and efficient production methods, organizations can enhance quality, reduce costs, and build strong supplier relationships.
While challenges exist in adapting these practices to different cultural and operational contexts, the benefits of Japanese manufacturing excellence are substantial.
Through careful implementation, ongoing training, and a commitment to collaboration and innovation, companies can unlock the secrets of Japanese manufacturing excellence and achieve sustained global success.
資料ダウンロード
QCD管理受発注クラウド「newji」は、受発注部門で必要なQCD管理全てを備えた、現場特化型兼クラウド型の今世紀最高の受発注管理システムとなります。
ユーザー登録
受発注業務の効率化だけでなく、システムを導入することで、コスト削減や製品・資材のステータス可視化のほか、属人化していた受発注情報の共有化による内部不正防止や統制にも役立ちます。
NEWJI DX
製造業に特化したデジタルトランスフォーメーション(DX)の実現を目指す請負開発型のコンサルティングサービスです。AI、iPaaS、および先端の技術を駆使して、製造プロセスの効率化、業務効率化、チームワーク強化、コスト削減、品質向上を実現します。このサービスは、製造業の課題を深く理解し、それに対する最適なデジタルソリューションを提供することで、企業が持続的な成長とイノベーションを達成できるようサポートします。
製造業ニュース解説
製造業、主に購買・調達部門にお勤めの方々に向けた情報を配信しております。
新任の方やベテランの方、管理職を対象とした幅広いコンテンツをご用意しております。
お問い合わせ
コストダウンが利益に直結する術だと理解していても、なかなか前に進めることができない状況。そんな時は、newjiのコストダウン自動化機能で大きく利益貢献しよう!
(β版非公開)