- お役立ち記事
- Unlocking the Secrets of Japanese Craftsmanship: The Role of Fabric Density in Superior Manufacturing
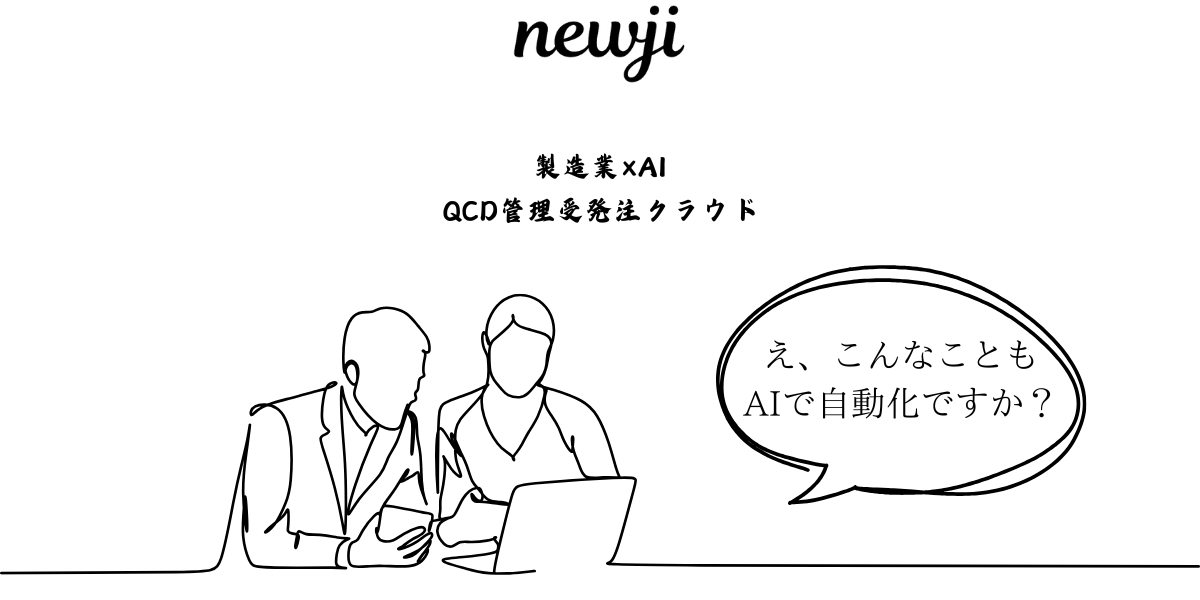
Unlocking the Secrets of Japanese Craftsmanship: The Role of Fabric Density in Superior Manufacturing
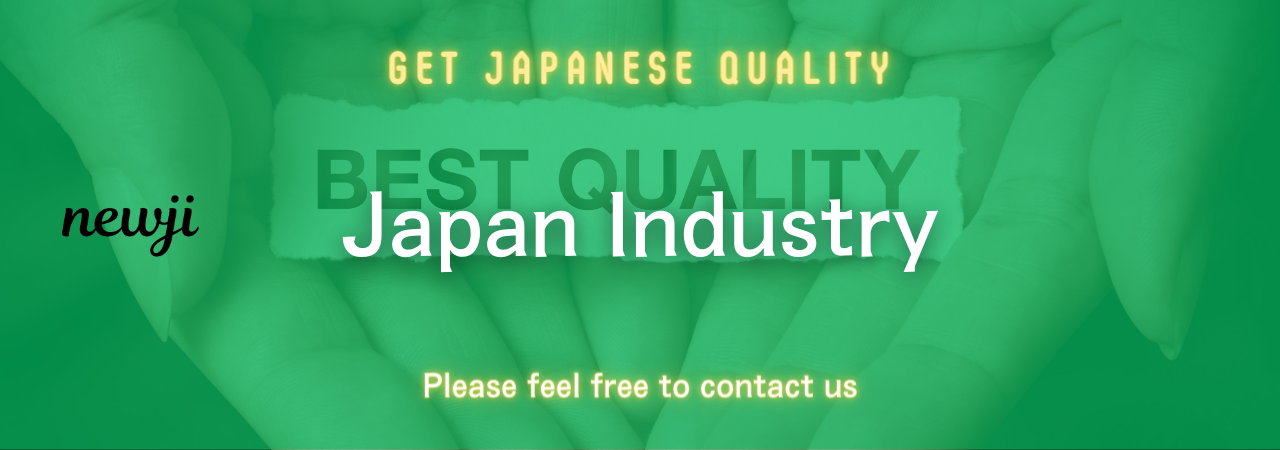
目次
Introduction to Japanese Craftsmanship and Fabric Density
Japanese manufacturing is renowned worldwide for its exceptional quality and precision. One of the key factors contributing to this reputation is the meticulous attention to fabric density in production processes. Fabric density refers to the compactness of materials used in manufacturing, which directly impacts the durability, performance, and overall quality of the final product. Understanding the role of fabric density is essential for companies aiming to enhance their manufacturing standards and achieve superior products.
The Importance of Fabric Density in Manufacturing Quality
Fabric density plays a pivotal role in determining the strength and longevity of products. In industries such as automotive, electronics, and textiles, the density of materials can significantly affect performance. Higher fabric density often results in more robust products that can withstand greater stress and wear over time. Additionally, precise control over fabric density ensures consistency in product quality, which is crucial for maintaining brand reputation and customer satisfaction.
Impact on Product Durability
Products with higher fabric density are typically more durable. This is because denser materials offer better resistance to physical stress, reducing the likelihood of damage during use. For example, in the automotive industry, components with higher fabric density can enhance vehicle safety by providing stronger structural support. Similarly, in the textile industry, denser fabrics are more resistant to tearing and wear, ensuring longer-lasting garments.
Enhancing Performance
Fabric density also influences the performance of products. In electronics, densely packed components can lead to more efficient devices with improved functionality. In aerospace, the density of materials used in aircraft construction affects fuel efficiency and overall performance. By optimizing fabric density, manufacturers can achieve products that not only meet but exceed performance expectations.
Advantages and Disadvantages of High Fabric Density
While high fabric density offers several benefits, it is essential to consider its potential drawbacks to make informed procurement and purchasing decisions.
Advantages
1. **Improved Strength and Durability**: As previously mentioned, higher fabric density results in stronger and more durable products, which can lead to increased customer satisfaction and reduced warranty claims.
2. **Consistent Quality**: Maintaining consistent fabric density across production batches ensures uniform product quality, which is vital for brand reliability.
3. **Enhanced Performance**: Products with optimized fabric density often perform better, meeting higher standards and customer expectations.
4. **Long-Term Cost Savings**: Although the initial cost may be higher, durable products reduce the need for frequent replacements, leading to long-term savings.
Disadvantages
1. **Increased Material Costs**: Higher fabric density typically requires more materials, which can increase production costs and impact profit margins.
2. **Production Complexity**: Achieving optimal fabric density requires precise manufacturing processes, which may necessitate advanced machinery and skilled labor.
3. **Longer Production Times**: The additional steps involved in ensuring high fabric density can lead to longer production cycles, affecting overall efficiency.
4. **Potential for Overengineering**: In some cases, excessively high fabric density may not translate to proportional performance benefits, leading to unnecessary costs without significant advantages.
Supplier Negotiation Techniques Related to Fabric Density
Effective supplier negotiation is crucial for securing the best materials at competitive prices. When it comes to fabric density, several strategies can help procurement and purchasing professionals achieve favorable terms.
Understanding Supplier Capabilities
Before entering negotiations, it is essential to assess the supplier’s ability to meet fabric density requirements. This includes evaluating their production facilities, quality control processes, and past performance. Understanding the supplier’s strengths and limitations enables more informed negotiations and reduces the risk of quality issues.
Leveraging Volume for Better Pricing
Negotiating prices based on order volume can lead to significant cost savings. Suppliers often offer discounts for bulk purchases, making it advantageous to consolidate orders. Additionally, long-term contracts can provide stability and leverage for better pricing over time.
Emphasizing Quality Standards
Highlighting the importance of fabric density and its impact on product quality can motivate suppliers to prioritize meeting specifications. Establishing clear quality standards and insisting on rigorous testing ensures that suppliers understand the critical nature of fabric density in the manufacturing process.
Building Strong Relationships
Fostering strong relationships with suppliers can lead to more collaborative and flexible negotiations. Trust and mutual respect encourage suppliers to go the extra mile in meeting fabric density requirements and accommodating any special requests or adjustments.
Market Conditions Affecting Fabric Density in Japanese Manufacturing
The global market dynamics significantly influence fabric density practices in Japanese manufacturing. Understanding these conditions is vital for effective procurement and purchasing strategies.
Technological Advancements
Advancements in manufacturing technologies have made it easier to control and optimize fabric density. Innovations such as computer-aided design (CAD) and automation have increased precision, allowing manufacturers to achieve higher fabric densities without compromising efficiency.
Supply Chain Factors
Global supply chain disruptions, such as those caused by geopolitical tensions or natural disasters, can impact the availability and cost of materials. Japanese manufacturers often emphasize robust supply chain management to ensure consistent access to high-quality materials needed for optimal fabric density.
Environmental Regulations
Increasing environmental regulations require manufacturers to adopt sustainable practices, which can influence fabric density choices. Eco-friendly materials and processes may affect the density requirements, necessitating adjustments in procurement and production strategies.
Competitive Landscape
The highly competitive nature of the global market drives Japanese manufacturers to continuously improve product quality. Maintaining superior fabric density is a key differentiator that helps companies stay ahead of competitors by offering more reliable and high-performing products.
Best Practices for Procurement and Purchasing
Implementing best practices in procurement and purchasing is essential for harnessing the benefits of Japanese craftsmanship and fabric density.
Collaborative Planning
Working closely with suppliers during the planning phase ensures that fabric density requirements are clearly communicated and understood. Collaborative planning helps align expectations and reduces the risk of miscommunication, leading to more successful outcomes.
Quality Assurance Programs
Establishing comprehensive quality assurance programs is crucial for maintaining high fabric density standards. Regular inspections, testing, and audits help identify and address any deviations from specifications, ensuring consistent product quality.
Continuous Improvement
Adopting a culture of continuous improvement encourages ongoing evaluation and enhancement of fabrication processes. This approach helps identify opportunities to optimize fabric density, reduce costs, and improve overall manufacturing efficiency.
Supplier Diversity
Maintaining a diverse supplier base mitigates risks associated with relying on a single source. By working with multiple suppliers, companies can ensure a steady supply of materials with the desired fabric density, even in the face of market fluctuations or unexpected disruptions.
Training and Development
Investing in training and development for procurement and purchasing teams enhances their ability to negotiate effectively and manage supplier relationships. Well-trained professionals are better equipped to understand technical specifications related to fabric density and make informed decisions.
Case Studies: Success Stories in Japanese Manufacturing
Examining real-world examples of successful implementation of fabric density optimization in Japanese manufacturing provides valuable insights.
Automotive Industry
A leading Japanese automotive manufacturer achieved significant improvements in vehicle safety and performance by increasing the fabric density of critical components. This enhancement resulted in stronger structural integrity, better crash resistance, and overall enhanced vehicle durability, leading to increased consumer trust and market share.
Electronics Sector
A prominent Japanese electronics company optimized the fabric density of its printed circuit boards (PCBs), resulting in more efficient devices with higher performance capabilities. The increased density allowed for more components to be housed within the same space, improving product functionality without increasing size or cost.
Textile Industry
A Japanese textile manufacturer implemented fabric density controls to produce high-quality, durable fabrics for the fashion industry. The enhanced density improved the wear resistance and longevity of garments, attracting premium customers and establishing the brand as a leader in quality.
Challenges and Solutions
While optimizing fabric density offers numerous benefits, manufacturers often face challenges in its implementation. Addressing these challenges requires strategic solutions.
Balancing Cost and Quality
One of the primary challenges is balancing the increased costs associated with higher fabric density against the benefits of improved quality. To address this, manufacturers can explore cost-effective materials that offer the desired density without significantly raising expenses. Additionally, optimizing production processes to reduce waste can help mitigate cost increases.
Maintaining Consistency
Ensuring consistent fabric density across production batches can be challenging, especially when scaling up operations. Implementing strict quality control measures and utilizing advanced manufacturing technologies can help maintain uniform density standards.
Adapting to Market Changes
Market demands and preferences can shift, requiring manufacturers to adjust fabric density levels accordingly. Staying attuned to market trends and maintaining flexible production processes enable companies to adapt quickly to changing requirements.
Supplier Reliability
Dependence on reliable suppliers is critical for maintaining fabric density standards. Developing strong supplier partnerships and having contingency plans in place can help mitigate risks associated with supplier unreliability.
Future Trends in Fabric Density and Japanese Manufacturing
The future of fabric density in Japanese manufacturing is influenced by several emerging trends, shaping the way companies approach production and procurement.
Smart Manufacturing
The integration of smart technologies, such as the Internet of Things (IoT) and artificial intelligence (AI), is revolutionizing fabric density management. These technologies enable real-time monitoring and precise control of material density, enhancing quality and efficiency.
Sustainable Materials
As sustainability becomes increasingly important, the demand for eco-friendly materials with optimized fabric density is rising. Manufacturers are exploring innovative materials that offer high density while minimizing environmental impact, aligning with global sustainability goals.
Customization and Flexibility
Customers are seeking more personalized products, driving the need for flexible manufacturing processes that can accommodate varying fabric density requirements. Advanced manufacturing techniques, such as additive manufacturing, are enabling greater customization without compromising on density and quality.
Global Collaboration
Global collaboration among manufacturers, suppliers, and research institutions is fostering innovation in fabric density management. Sharing knowledge and best practices across borders enhances the collective ability to develop superior manufacturing techniques.
Conclusion
Fabric density is a critical factor in Japanese craftsmanship and superior manufacturing. By understanding its role and implementing strategic procurement and purchasing practices, companies can leverage the advantages of high fabric density to produce durable, high-performing products. While challenges exist, adopting best practices and staying abreast of future trends ensures that manufacturers can maintain their competitive edge. Embracing the principles of Japanese manufacturing not only enhances product quality but also fosters long-term business success.
資料ダウンロード
QCD調達購買管理クラウド「newji」は、調達購買部門で必要なQCD管理全てを備えた、現場特化型兼クラウド型の今世紀最高の購買管理システムとなります。
ユーザー登録
調達購買業務の効率化だけでなく、システムを導入することで、コスト削減や製品・資材のステータス可視化のほか、属人化していた購買情報の共有化による内部不正防止や統制にも役立ちます。
NEWJI DX
製造業に特化したデジタルトランスフォーメーション(DX)の実現を目指す請負開発型のコンサルティングサービスです。AI、iPaaS、および先端の技術を駆使して、製造プロセスの効率化、業務効率化、チームワーク強化、コスト削減、品質向上を実現します。このサービスは、製造業の課題を深く理解し、それに対する最適なデジタルソリューションを提供することで、企業が持続的な成長とイノベーションを達成できるようサポートします。
オンライン講座
製造業、主に購買・調達部門にお勤めの方々に向けた情報を配信しております。
新任の方やベテランの方、管理職を対象とした幅広いコンテンツをご用意しております。
お問い合わせ
コストダウンが利益に直結する術だと理解していても、なかなか前に進めることができない状況。そんな時は、newjiのコストダウン自動化機能で大きく利益貢献しよう!
(Β版非公開)