- お役立ち記事
- Unlocking the Secrets of Japanese Manufacturing: How “冷間鍛造” (Cold Forging) Revolutionizes Industrial Production
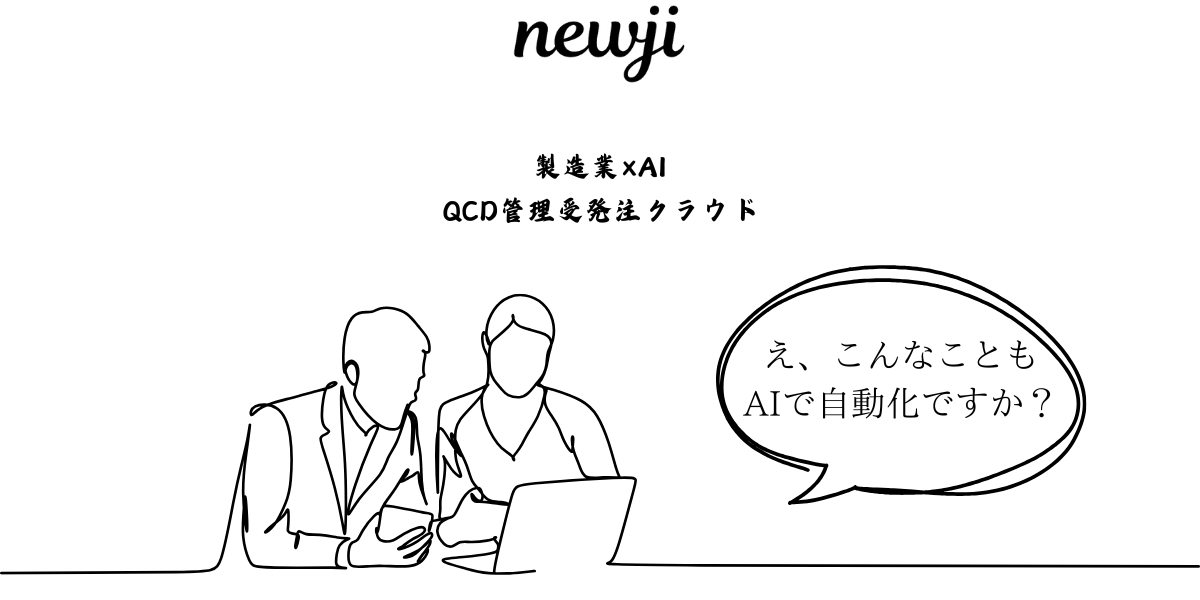
Unlocking the Secrets of Japanese Manufacturing: How “冷間鍛造” (Cold Forging) Revolutionizes Industrial Production
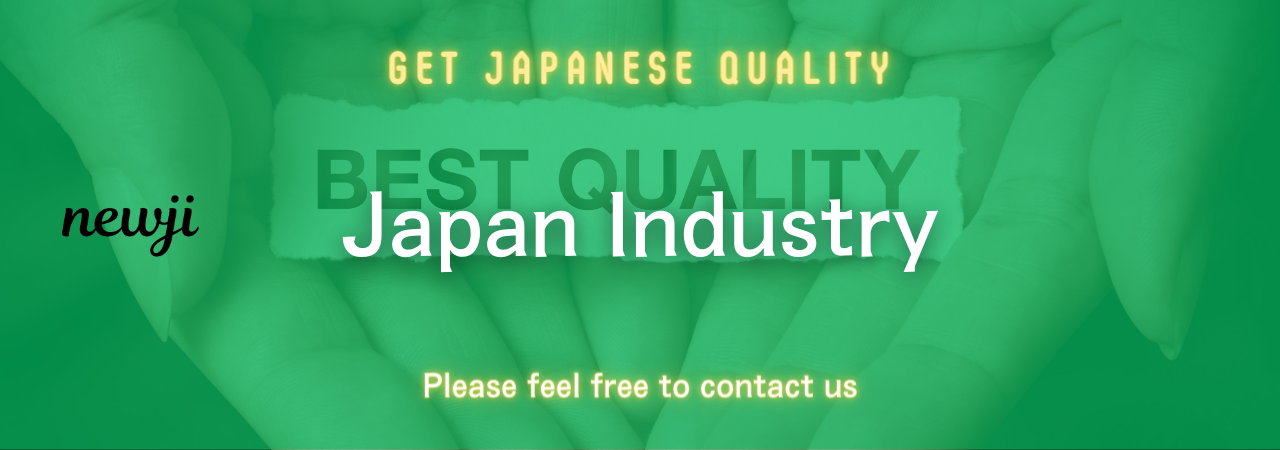
目次
Introduction to 冷間鍛造 (Cold Forging)
In the arena of manufacturing, Japan has consistently set benchmarks for quality, precision, and efficiency.
One manufacturing technique that Japanese companies have mastered is 冷間鍛造, or cold forging.
This advanced process has the potential to revolutionize industrial production by increasing strength, durability, and efficiency in manufactured components.
Considering my extensive experience in procurement and purchasing, I have had numerous opportunities to engage with Japanese suppliers specializing in cold forging.
The advantages, practical applications, and unique methodologies these suppliers bring to the table could significantly benefit any manufacturing enterprise.
Understanding Cold Forging
Cold forging involves deforming metal below its recrystallization temperature, typically at room temperature.
This process relies on stamping, squeezing, or rolling metal into the desired shape without the need for heating.
The result is a finished product with improved mechanical properties and minimal waste.
Advantages of Cold Forging
There are several compelling reasons to consider cold forging as part of your manufacturing process:
1. **Material Efficiency**: Cold forging offers higher material utilization, often approaching 100%.
This reduces raw material wastage, making it more cost-effective.
2. **Superior Strength and Durability**: Components produced through cold forging exhibit superior mechanical properties, including better strength and hardness.
3. **Precision**: The process allows for tighter tolerances and precision, leading to less need for secondary machining operations.
4. **Surface Finish**: Cold forged components often have superior surface finishes, reducing the need for additional finishing processes.
5. **Energy Savings**: Eliminating the heating process saves significant energy costs.
Disadvantages of Cold Forging
While cold forging offers numerous advantages, there are some challenges and drawbacks to be mindful of:
1. **Work Hardening**: The metal hardens as it is deformed at room temperature, which can make it more difficult to work with.
2. **Tooling Costs**: Specialized tooling for cold forging can be expensive to develop and maintain.
3. **Material Limitations**: Not all metals are suitable for cold forging.
Some may require alternative forging methods.
4. **Size and Complexity Constraints**: Cold forging is more suitable for smaller, simpler parts.
More complex or larger components may require different methods.
Supplier Negotiation Techniques
Negotiating with Japanese suppliers who specialize in cold forging can be an intricate process due to cultural nuances and exacting standards. Here are some practical tips for successful negotiations:
Building Relationships
In Japan, personal relationships and trust are paramount.
Gaining the trust of your supplier is critical for a successful partnership.
This often involves face-to-face meetings, regular communication, and a demonstrated commitment to collaboration.
Understanding Cultural Nuances
Japanese business culture values respect, politeness, and formality.
Understanding these cultural nuances can help in creating a positive impression during negotiations.
For instance, always addressing your counterparts with appropriate titles and showing respect for seniority can go a long way.
Emphasizing Long-Term Benefits
Japanese suppliers often prefer long-term commitments over short-term gains.
When negotiating, emphasize the long-term benefits and potential for sustained collaboration.
This aligns with their preference for stable and enduring partnerships.
Technical Expertise
Demonstrating a deep understanding of cold forging can earn the respect of Japanese suppliers.
Being well-prepared and knowledgeable about the process showcases your professionalism and commitment to quality.
Market Conditions and Trends
To effectively utilize cold forging in your manufacturing process, it is essential to understand current market conditions and trends in the industry.
Rising Demand for Precision Components
There is a growing demand for precision components, particularly in industries such as automotive, aerospace, and electronics.
Cold forging’s ability to produce high-quality, precise parts makes it increasingly attractive in these sectors.
Shift Towards Sustainability
Sustainability is becoming a critical focus for manufacturers globally.
Cold forging’s material efficiency and energy savings contribute significantly to sustainable manufacturing practices, aligning with this trend.
Technological Advancements
Advancements in cold forging technologies, such as improved tooling and automation, are making the process more accessible and cost-effective.
Staying abreast of these technological trends can provide a competitive edge.
Global Supply Chain Dynamics
The global supply chain is becoming more complex, and securing reliable suppliers is crucial.
Japanese suppliers renowned for their quality and reliability in cold forging can provide a dependable source for high-quality components.
Best Practices for Implementing Cold Forging
Integrating cold forging into your manufacturing process requires strategic planning and execution. Here are some best practices to consider:
Supplier Selection
Carefully select suppliers with a proven track record in cold forging.
Consider factors such as their expertise, reputation, and commitment to quality.
Conduct thorough audits and assessments to ensure alignment with your standards.
Collaborative Development
Work closely with your supplier during the development phase.
Collaborative design and engineering can help optimize the cold forging process for your specific requirements.
This partnership approach can lead to better outcomes and innovation.
Invest in Tooling
While tooling costs can be high, investing in high-quality tooling is essential for achieving the desired results.
Work with your supplier to design and develop tooling that meets your specific needs and ensures durability and precision.
Quality Control
Establish robust quality control measures to monitor and maintain the quality of cold forged components.
Regular inspections and testing can help identify and address issues early in the production process.
Continuous Improvement
Adopt a mindset of continuous improvement.
Regularly review and assess your cold forging processes, seeking opportunities for enhancement and efficiency.
Collaborate with your supplier to implement best practices and innovative solutions.
Real-World Applications of Cold Forging
Cold forging finds applications in a wide range of industries, exemplifying its versatility and value.
Automotive Industry
Cold forging is extensively used in the automotive industry to produce high-strength, precise components such as gears, shafts, and fasteners.
Its ability to meet stringent quality and durability standards makes it indispensable.
Aerospace Industry
In the aerospace sector, cold forging is employed to manufacture critical components that require exceptional strength and reliability.
Examples include turbine blades, brackets, and fasteners.
Electronics Industry
Miniaturization and precision are crucial in the electronics industry.
Cold forging enables the production of small, intricate components with high accuracy, essential for devices such as smartphones and consumer electronics.
Industrial Machinery
Cold forging is utilized in the production of various industrial machinery components, including bearings, gears, and tools.
Its ability to produce durable and high-performance parts is highly valued in this sector.
Conclusion
冷間鍛造, or cold forging, represents a transformative manufacturing process that offers numerous benefits, from superior strength and precision to material efficiency and energy savings.
By understanding the advantages, navigating supplier negotiations, staying informed about market trends, and implementing best practices, manufacturers can harness the full potential of cold forging.
Integrating this advanced technique into your production process can lead to significant improvements in quality, cost-effectiveness, and sustainability.
As someone with extensive experience in procurement and purchasing, I can attest to the value that Japanese suppliers specializing in cold forging bring to the table.
Their expertise, commitment to quality, and innovative solutions can help elevate your manufacturing operations to new heights.
Embrace the secrets of Japanese manufacturing and unlock the potential of cold forging to revolutionize your industrial production.
資料ダウンロード
QCD調達購買管理クラウド「newji」は、調達購買部門で必要なQCD管理全てを備えた、現場特化型兼クラウド型の今世紀最高の購買管理システムとなります。
ユーザー登録
調達購買業務の効率化だけでなく、システムを導入することで、コスト削減や製品・資材のステータス可視化のほか、属人化していた購買情報の共有化による内部不正防止や統制にも役立ちます。
NEWJI DX
製造業に特化したデジタルトランスフォーメーション(DX)の実現を目指す請負開発型のコンサルティングサービスです。AI、iPaaS、および先端の技術を駆使して、製造プロセスの効率化、業務効率化、チームワーク強化、コスト削減、品質向上を実現します。このサービスは、製造業の課題を深く理解し、それに対する最適なデジタルソリューションを提供することで、企業が持続的な成長とイノベーションを達成できるようサポートします。
オンライン講座
製造業、主に購買・調達部門にお勤めの方々に向けた情報を配信しております。
新任の方やベテランの方、管理職を対象とした幅広いコンテンツをご用意しております。
お問い合わせ
コストダウンが利益に直結する術だと理解していても、なかなか前に進めることができない状況。そんな時は、newjiのコストダウン自動化機能で大きく利益貢献しよう!
(Β版非公開)