- お役立ち記事
- Unlocking the Secrets of Japanese Manufacturing: How Metal Composition Analyzers Revolutionize Quality and Innovation
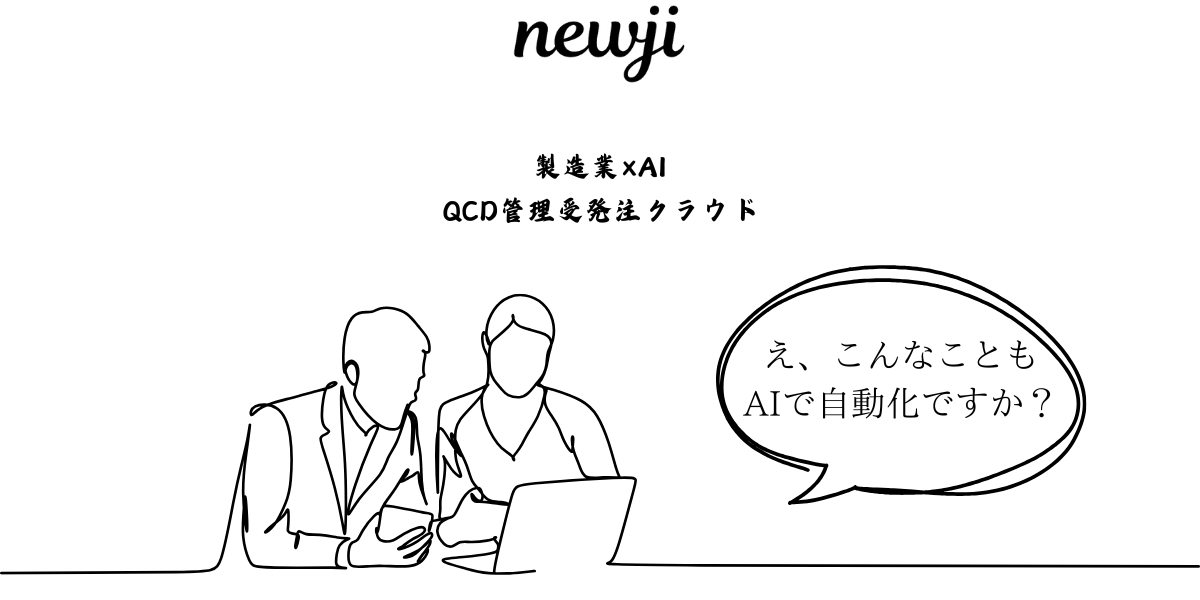
Unlocking the Secrets of Japanese Manufacturing: How Metal Composition Analyzers Revolutionize Quality and Innovation
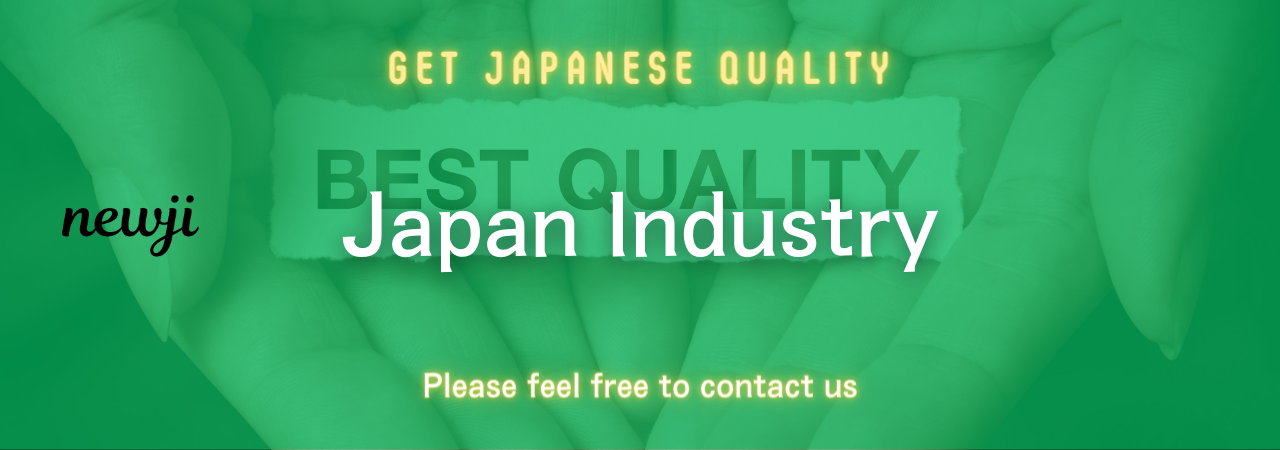
目次
Introduction to Japanese Manufacturing Excellence
Japanese manufacturing has long been renowned for its commitment to quality, precision, and innovation.
Famous for its automotive giants, electronic marvels, and advanced robotics, Japan stands as a paragon of industrial prowess.
Central to this reputation is the meticulous attention to detail and the constant pursuit of perfection.
In this context, the use of metal composition analyzers has emerged as a revolutionary advancement, playing a crucial role in maintaining the high standards of Japanese manufacturing.
The Role of Metal Composition Analyzers
Metal composition analyzers are sophisticated devices used to determine the elemental makeup of metal components.
These tools provide essential information that helps manufacturers ensure their products meet precise specifications.
In Japanese manufacturing, the use of metal composition analyzers is pivotal in quality control processes.
They help identify any deviations from expected material properties, supporting the creation of flawless products.
How They Work
These analyzers operate using various technologies, including X-ray fluorescence (XRF), optical emission spectroscopy (OES), and inductively coupled plasma (ICP).
Each technology has its benefits and is chosen based on the specific requirements of the manufacturing process.
XRF is often praised for its non-destructive testing capabilities, whereas OES is favored for its speed and accuracy in detecting elemental impurities.
Advantages in Quality Assurance
Incorporating metal composition analyzers in the manufacturing process ensures that the raw materials used in production meet the required standards.
This leads to consistent product quality and helps in maintaining the reputation of Japanese products in global markets.
Moreover, early detection of impurities reduces waste by preventing defective products from progressing through the production line.
Impact on Innovation and Production Efficiency
Beyond quality assurance, metal composition analyzers enhance the innovation landscape in Japanese manufacturing.
By providing detailed insights into material characteristics, these analyzers allow engineers to experiment with new alloys and compounds, driving innovation.
They also contribute to improved production efficiency by streamlining the material selection process and reducing the need for extensive manual inspections.
Cost-Effectiveness and Waste Reduction
One of the notable advantages is the cost-effectiveness achieved through the reduction of material waste.
Early detection of composition anomalies enables manufacturers to address problems swiftly, minimizing the impact on subsequent production phases.
This proactive approach not only preserves resources but also contributes to a more sustainable manufacturing environment.
Challenges and Disadvantages
While the benefits of metal composition analyzers are significant, they are not without challenges.
The cost of acquiring and maintaining these advanced analyzers can be substantial, particularly for smaller manufacturers.
Additionally, skilled technicians are required to operate these sophisticated machines, necessitating investment in training and development.
Technological Limitations
Different types of analyzers have their limitations.
For example, while XRF is excellent for surface analysis, it may not accurately assess the composition of thicker samples.
Manufacturers need to select the right technology for their specific applications, balancing cost against the required precision and capabilities.
Best Practices in Utilizing Metal Composition Analyzers
To maximize the benefits, manufacturers should adhere to certain best practices.
Regular calibration of analyzers ensures accuracy and reliability of results.
Furthermore, integrating these tools within a comprehensive quality management system, inclusive of other checks and balances, provides a robust framework for maintaining high standards.
Supplier Collaboration
Manufacturers can work closely with suppliers to ensure the materials provided meet necessary specifications.
By sharing analyzer results, both parties can engage in open communication to address any discrepancies.
This collaboration fosters stronger partnerships and ensures a consistent supply of high-quality materials.
Negotiation Techniques with Japanese Suppliers
When procuring materials from Japanese suppliers, understanding cultural nuances and negotiation etiquette is crucial.
Japanese business culture prioritizes long-term relationships, mutual respect, and commitment to quality.
Emphasizing Quality over Price
While cost is an important factor, placing a higher emphasis on quality can be more beneficial in the long run.
Japanese suppliers appreciate buyers who recognize the value of materials that meet exacting standards.
Patience and Relationship Building
Building trust with Japanese suppliers often takes time and patience.
Engage in face-to-face meetings when possible, as these interactions help deepen the business relationship.
Demonstrating a genuine interest and understanding of their operations can lead to more favorable terms and conditions.
Understanding Japanese Market Conditions
The state of the Japanese market plays a key role in procurement decisions.
Currently, Japan continues to focus on high-value industries like automotive and electronics, influencing the demand for precision materials.
Raw Material Preferences
Japanese manufacturers tend to favor suppliers who can provide comprehensive details on the material sourcing and composition.
Having metal composition data ready can enhance your credibility and competitiveness when dealing with Japanese companies.
Conclusion
The integration of metal composition analyzers in Japanese manufacturing has undeniably revolutionized quality and innovation.
These tools not only uphold the prestigious standards associated with Japanese products but also contribute by fostering new technological advancements.
By understanding the advantages and challenges of these analyzers, and adopting best practices in procurement, manufacturers can better navigate the complex landscape of Japanese industry.
This not only ensures consistent quality but also opens the door to fresh opportunities for innovation in manufacturing.
資料ダウンロード
QCD調達購買管理クラウド「newji」は、調達購買部門で必要なQCD管理全てを備えた、現場特化型兼クラウド型の今世紀最高の購買管理システムとなります。
ユーザー登録
調達購買業務の効率化だけでなく、システムを導入することで、コスト削減や製品・資材のステータス可視化のほか、属人化していた購買情報の共有化による内部不正防止や統制にも役立ちます。
NEWJI DX
製造業に特化したデジタルトランスフォーメーション(DX)の実現を目指す請負開発型のコンサルティングサービスです。AI、iPaaS、および先端の技術を駆使して、製造プロセスの効率化、業務効率化、チームワーク強化、コスト削減、品質向上を実現します。このサービスは、製造業の課題を深く理解し、それに対する最適なデジタルソリューションを提供することで、企業が持続的な成長とイノベーションを達成できるようサポートします。
オンライン講座
製造業、主に購買・調達部門にお勤めの方々に向けた情報を配信しております。
新任の方やベテランの方、管理職を対象とした幅広いコンテンツをご用意しております。
お問い合わせ
コストダウンが利益に直結する術だと理解していても、なかなか前に進めることができない状況。そんな時は、newjiのコストダウン自動化機能で大きく利益貢献しよう!
(Β版非公開)