- お役立ち記事
- “Unlocking the Secrets of Japanese Manufacturing: How ‘Protocol’ Transforms Production Efficiency”
“Unlocking the Secrets of Japanese Manufacturing: How ‘Protocol’ Transforms Production Efficiency”
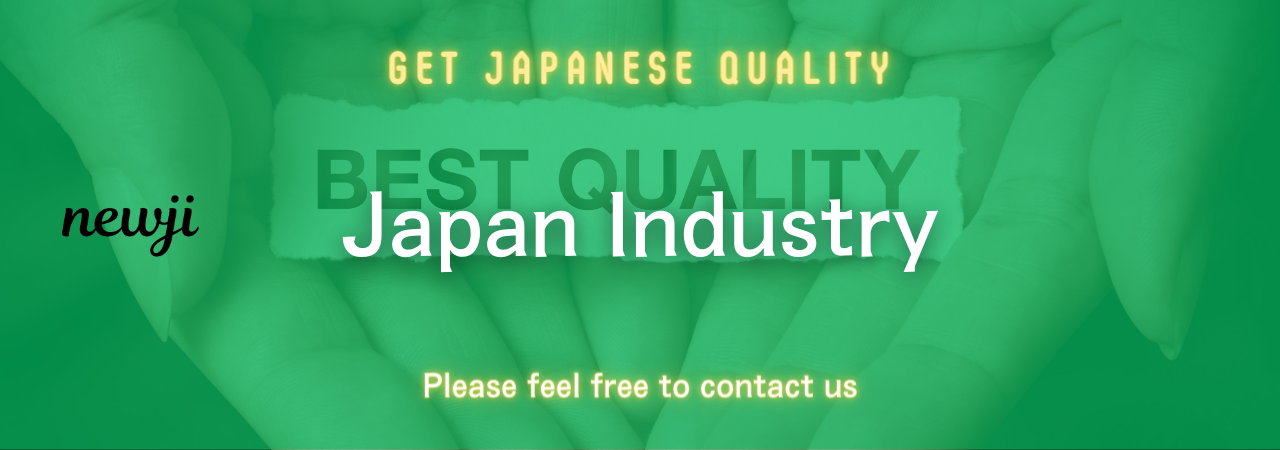
目次
Introduction
Japanese manufacturing has long been admired for its efficiency and quality.
The application of specific protocols has been central to this reputation.
Understanding these protocols can provide valuable insights into enhancing production efficiency.
This article explores how Japanese manufacturing protocols transform production processes.
We delve into procurement and purchasing strategies, supplier negotiations, market conditions, and best practices.
By examining these areas, manufacturers worldwide can adopt techniques that lead to improved efficiency and competitiveness.
Understanding Japanese Manufacturing Protocols
The Philosophy Behind Japanese Manufacturing
At the heart of Japanese manufacturing lies a philosophy focused on continuous improvement and respect for people.
This approach emphasizes efficiency, quality, and flexibility.
The principles of Lean Manufacturing and Just-In-Time (JIT) are integral to this philosophy.
These principles aim to eliminate waste, optimize processes, and ensure products meet high standards.
The cultural emphasis on teamwork and collective responsibility also plays a crucial role.
Key Protocols and Practices
Japanese manufacturing is characterized by several key protocols that contribute to its success.
Kanban is a scheduling system that helps manage production efficiently.
Kaizen involves ongoing efforts to improve processes and eliminate waste.
5S methodology focuses on workplace organization and standardization.
Total Quality Management (TQM) ensures that every aspect of production meets stringent quality standards.
These protocols collectively foster an environment of excellence and continuous improvement.
Enhancing Production Efficiency through Protocols
Lean Manufacturing Techniques
Lean Manufacturing seeks to maximize value while minimizing waste.
By analyzing production processes, manufacturers can identify and eliminate non-value-adding activities.
Techniques such as value stream mapping and waste reduction are essential components.
Implementing Lean practices leads to more streamlined operations and cost savings.
Japanese manufacturers excel in Lean methodologies, setting benchmarks for efficiency.
Just-In-Time Production
JIT production aims to produce only what is needed, when it is needed.
This reduces inventory costs and minimizes waste.
By synchronizing production schedules with demand, companies can respond swiftly to market changes.
JIT requires precise coordination with suppliers and robust supply chain management.
Japanese firms often lead in implementing JIT, ensuring seamless production flows.
Procurement and Purchasing from Japanese Suppliers
Advantages of Sourcing from Japan
Japan is renowned for its high-quality manufacturing and advanced technology.
Sourcing from Japanese suppliers ensures access to superior products and innovations.
Japanese companies prioritize reliability and consistency, reducing the risk of defects.
Furthermore, the strong emphasis on customer satisfaction translates into excellent service and support.
Collaborating with Japanese suppliers can enhance a company’s reputation and product offerings.
Challenges and Considerations
Despite the advantages, sourcing from Japan presents certain challenges.
Language barriers and cultural differences can complicate communication and negotiations.
High standards and rigorous quality requirements may necessitate thorough compliance measures.
Logistical considerations, such as shipping times and costs, must also be managed effectively.
Understanding these factors is crucial for successful procurement from Japanese suppliers.
Supplier Negotiation Techniques
Building Strong Relationships
In Japanese business culture, building and maintaining strong relationships is paramount.
Trust and mutual respect are foundational to successful partnerships.
Investing time in relationship-building activities can lead to more favorable negotiations.
Long-term collaboration is often prioritized over immediate gains, fostering stability and reliability.
Japanese suppliers value partners who demonstrate commitment and integrity.
Effective Communication Strategies
Clear and respectful communication is essential in negotiations with Japanese suppliers.
Understanding cultural nuances and communication styles can prevent misunderstandings.
Using formal language and demonstrating professionalism are important.
Listening attentively and being open to feedback fosters a collaborative environment.
Effective communication ensures that both parties’ needs and expectations are aligned.
Market Conditions and Trends
Current State of Japanese Manufacturing
Japanese manufacturing remains a global leader in various industries, including automotive, electronics, and robotics.
The sector continues to innovate, integrating advanced technologies like automation and AI.
Sustainability and environmental responsibility are increasingly prioritized.
Japanese manufacturers are adapting to changing global demands while maintaining high standards.
The resilience and adaptability of the sector ensure its ongoing competitiveness.
Future Outlook
The future of Japanese manufacturing is poised for growth and transformation.
Emerging technologies such as Industry 4.0 and the Internet of Things (IoT) are driving innovation.
There is a growing emphasis on smart manufacturing and digital integration.
Japanese companies are exploring new markets and expanding their global presence.
The focus on sustainability and eco-friendly practices will shape future manufacturing trends.
Best Practices in Collaborating with Japanese Manufacturers
Quality Control and Assurance
Maintaining high-quality standards is crucial when collaborating with Japanese manufacturers.
Implementing rigorous quality control measures ensures that products meet specifications.
Regular audits and inspections can identify and address potential issues promptly.
Collaborative quality management fosters trust and reliability between partners.
Japanese suppliers often have robust quality assurance systems in place, enhancing product integrity.
Continuous Improvement (Kaizen)
Embracing the Kaizen philosophy of continuous improvement can lead to significant enhancements.
Encouraging feedback and suggestions from all levels of the organization promotes innovation.
Regularly reviewing and refining processes ensures ongoing efficiency and effectiveness.
Collaborative efforts in improvement initiatives strengthen partnerships and drive mutual success.
Adopting Kaizen fosters a culture of excellence and adaptability.
Case Studies
Successful Partnerships
Many global companies have successfully partnered with Japanese manufacturers to enhance their operations.
For example, Toyota’s collaboration with international suppliers has set industry standards for Lean Manufacturing.
Apple’s partnership with Japanese electronics firms has been pivotal in developing cutting-edge products.
These partnerships demonstrate the benefits of combining Japanese efficiency with global innovation.
Successful collaborations are built on trust, mutual goals, and effective communication.
Lessons Learned
Lessons from successful collaborations highlight the importance of cultural understanding and flexibility.
Adapting to Japanese business practices can facilitate smoother interactions and negotiations.
Investing in relationship-building leads to more resilient and productive partnerships.
Effective communication and clear expectations are essential for overcoming challenges.
These lessons provide valuable guidance for companies seeking to engage with Japanese suppliers.
Conclusion
Japanese manufacturing protocols offer valuable strategies for enhancing production efficiency and quality.
By understanding and implementing these protocols, companies can achieve significant improvements.
Sourcing from Japanese suppliers provides access to high-quality products and innovative technologies.
Effective supplier negotiation and strong partnerships are key to successful collaborations.
Embracing continuous improvement and best practices ensures ongoing success in the global market.
Japanese manufacturing serves as a model of excellence, inspiring companies worldwide to pursue higher standards and greater efficiency.
資料ダウンロード
QCD調達購買管理クラウド「newji」は、調達購買部門で必要なQCD管理全てを備えた、現場特化型兼クラウド型の今世紀最高の購買管理システムとなります。
ユーザー登録
調達購買業務の効率化だけでなく、システムを導入することで、コスト削減や製品・資材のステータス可視化のほか、属人化していた購買情報の共有化による内部不正防止や統制にも役立ちます。
NEWJI DX
製造業に特化したデジタルトランスフォーメーション(DX)の実現を目指す請負開発型のコンサルティングサービスです。AI、iPaaS、および先端の技術を駆使して、製造プロセスの効率化、業務効率化、チームワーク強化、コスト削減、品質向上を実現します。このサービスは、製造業の課題を深く理解し、それに対する最適なデジタルソリューションを提供することで、企業が持続的な成長とイノベーションを達成できるようサポートします。
オンライン講座
製造業、主に購買・調達部門にお勤めの方々に向けた情報を配信しております。
新任の方やベテランの方、管理職を対象とした幅広いコンテンツをご用意しております。
お問い合わせ
コストダウンが利益に直結する術だと理解していても、なかなか前に進めることができない状況。そんな時は、newjiのコストダウン自動化機能で大きく利益貢献しよう!
(Β版非公開)