- お役立ち記事
- Unlocking the Secrets of Japanese Manufacturing: The Art of Failure Analysis (故障解析) in Engineering Excellence
月間77,185名の
製造業ご担当者様が閲覧しています*
*2025年2月28日現在のGoogle Analyticsのデータより
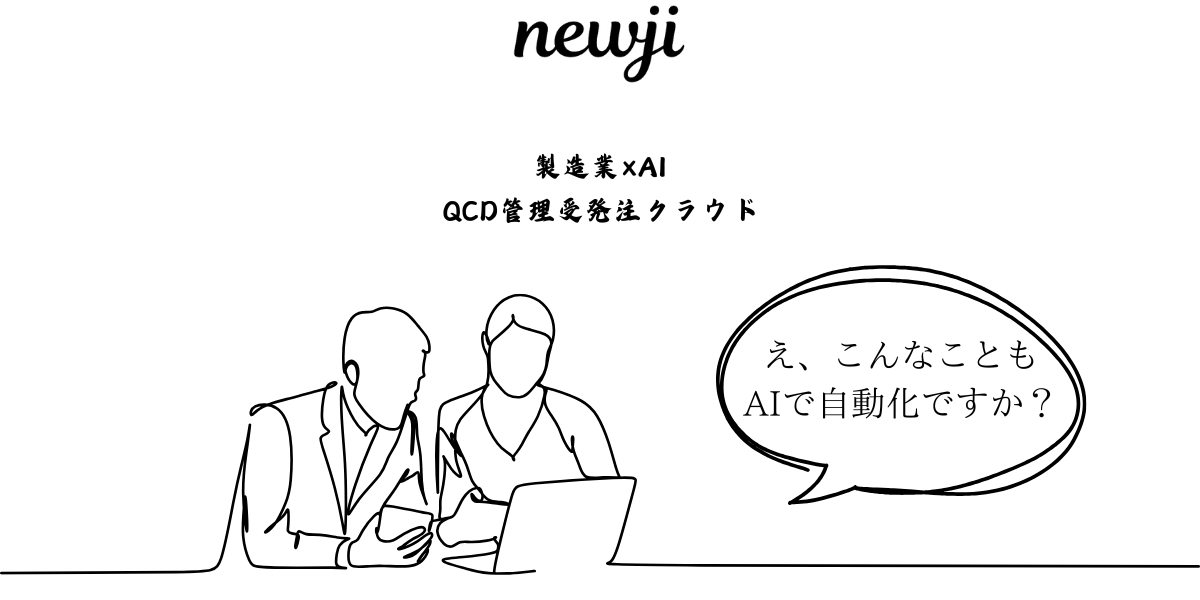
Unlocking the Secrets of Japanese Manufacturing: The Art of Failure Analysis (故障解析) in Engineering Excellence
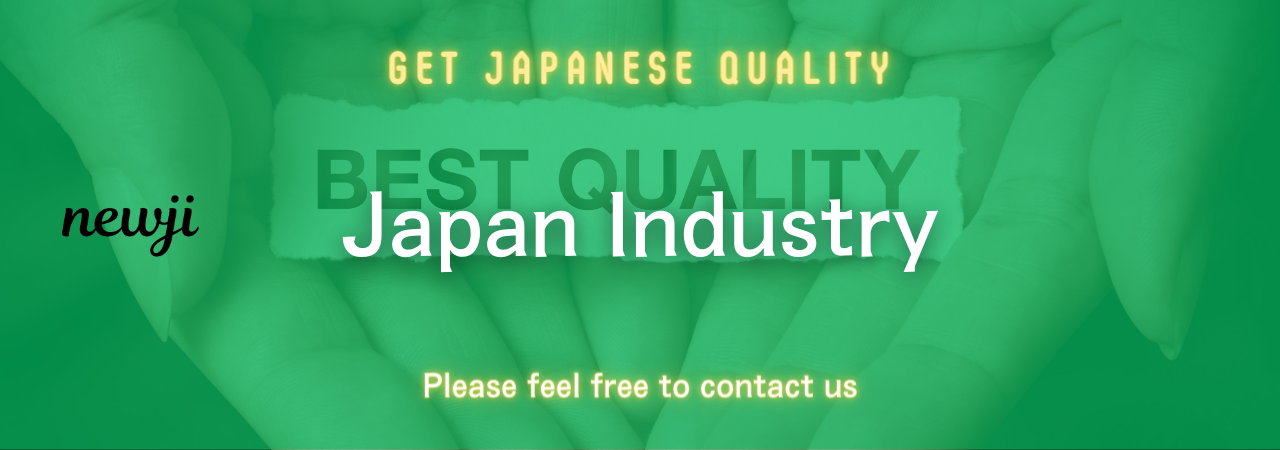
目次
Introduction to Japanese Manufacturing Excellence
Japanese manufacturing is renowned worldwide for its commitment to quality, precision, and continuous improvement. One of the key elements that contribute to this excellence is the systematic approach to failure analysis, known in Japanese as 故障解析 (koshōkaiseki). This article delves into the art of failure analysis in Japanese engineering, exploring its significance, advantages and disadvantages, supplier negotiation techniques, market conditions, and best practices from a procurement and purchasing perspective.
Understanding Failure Analysis (故障解析)
Failure analysis is a systematic process used to determine the root causes of defects or failures in products and systems. In the context of Japanese manufacturing, 故障解析 goes beyond mere troubleshooting; it embodies a culture of meticulous investigation and continuous improvement.
The Fundamentals of 故障解析
At its core, 故障解析 involves several key steps:
1. **Data Collection:** Gathering all relevant information about the failure, including operational conditions, usage patterns, and maintenance history.
2. **Failure Identification:** Characterizing the nature and extent of the failure.
3. **Root Cause Analysis:** Employing methodologies like the Five Whys or Fishbone Diagrams to trace the failure to its underlying cause.
4. **Corrective Actions:** Implementing solutions to prevent recurrence.
5. **Verification:** Ensuring that the corrective actions are effective.
The Role of 故障解析 in Japanese Manufacturing
In Japan, 故障解析 is integral to the philosophy of “Kaizen” or continuous improvement. It is not merely a reactive measure but a proactive strategy to enhance product reliability and customer satisfaction. Companies invest in advanced tools and training to ensure that failure analysis is conducted thoroughly and efficiently.
Importance in Japanese Manufacturing
The emphasis on failure analysis has several significant implications for Japanese manufacturers:
Enhancing Product Quality
By systematically analyzing failures, companies can identify and eliminate defects, leading to higher quality products. This proactive approach reduces the incidence of defects and minimizes warranty claims.
Cost Reduction
Identifying the root causes of failures helps in addressing issues at the source, preventing costly recalls and repairs. Additionally, it streamlines production processes by eliminating inefficiencies.
Customer Satisfaction
High product reliability translates to increased customer trust and loyalty. Consistently delivering quality products enhances the brand reputation and fosters long-term customer relationships.
Innovation and Development
Failure analysis provides insights that drive innovation. Understanding why a product failed can inspire new designs and improvements, fostering a culture of innovation.
Advantages and Disadvantages
Like any systematic approach, 故障解析 has its benefits and challenges. Understanding these can help companies effectively implement failure analysis in their operations.
Advantages
1. **Improved Quality Control:** Systematic failure analysis leads to better quality control and product reliability.
2. **Enhanced Problem-Solving Skills:** Teams trained in failure analysis develop strong analytical and problem-solving skills.
3. **Preventive Measures:** Identifying root causes allows companies to implement preventive measures, reducing future failures.
4. **Cost Savings:** By preventing defects and improving processes, companies can save significantly on costs associated with failures.
5. **Regulatory Compliance:** Ensures that products meet regulatory standards by identifying and addressing potential compliance issues.
Disadvantages
1. **Resource Intensive:** Comprehensive failure analysis requires significant time and resources, which can be a challenge for smaller companies.
2. **Complexity:** The process can be complex, especially for intricate products with multiple potential failure points.
3. **Requires Expertise:** Effective failure analysis demands skilled personnel with specialized training and experience.
4. **Potential for Over-Analysis:** There is a risk of over-analyzing minor issues, leading to delays and inefficiencies.
5. **Initial Implementation Costs:** Setting up a robust failure analysis system involves upfront costs in terms of tools, training, and infrastructure.
Supplier Negotiation Techniques
Effective supplier negotiation is crucial in the context of failure analysis. Building strong relationships with suppliers ensures that they are committed to maintaining high-quality standards and supporting continuous improvement efforts.
Building Collaborative Relationships
Japanese companies emphasize long-term partnerships with suppliers. This collaborative approach fosters mutual trust and encourages suppliers to share expertise and resources for failure analysis.
Setting Clear Quality Standards
Establishing clear quality standards and expectations from the outset ensures that suppliers understand the importance of failure analysis. This clarity helps in aligning supplier performance with company goals.
Incentivizing Quality Improvements
Incentive structures can motivate suppliers to prioritize quality and engage actively in failure analysis. Bonuses, preferred supplier status, and long-term contracts are examples of incentives that can be used.
Regular Performance Reviews
Conducting regular performance reviews allows companies to assess supplier performance in failure analysis. Constructive feedback helps suppliers improve and align with quality expectations.
Joint Problem-Solving Sessions
Engaging in joint problem-solving sessions with suppliers facilitates the sharing of knowledge and resources. This collaborative approach enhances the effectiveness of failure analysis efforts.
Market Conditions
Understanding the market conditions is essential for effective procurement and purchasing strategies, especially when dealing with Japanese suppliers. Market dynamics can influence the availability of materials, supply chain stability, and pricing.
Global Supply Chain Trends
Globalization has made supply chains more complex and interconnected. Japanese manufacturers often rely on a network of local and international suppliers. Understanding these dynamics helps in anticipating and mitigating potential disruptions.
Technology Advancements
Advancements in technology, such as automation and digitalization, are transforming manufacturing processes. Staying abreast of these changes is vital for effective procurement and failure analysis.
Economic Factors
Economic conditions, including currency fluctuations and trade policies, impact procurement strategies. Japanese manufacturers are adept at navigating these factors to maintain cost-effectiveness and supply chain resilience.
Sustainability and Environmental Concerns
Increasing focus on sustainability affects procurement practices. Suppliers are expected to adhere to environmental standards, and failure analysis processes incorporate sustainability considerations.
Competitive Landscape
The competitive environment drives Japanese manufacturers to seek continuous improvement. Understanding competitor strategies and market positioning informs procurement and purchasing decisions.
Best Practices in Failure Analysis
Implementing best practices in failure analysis can significantly enhance procurement and purchasing outcomes. These practices ensure that failure analysis is effective, efficient, and aligned with organizational goals.
Standardizing Failure Analysis Procedures
Establishing standardized procedures ensures consistency and reliability in failure analysis. This standardization facilitates easier training, better communication, and more accurate comparisons over time.
Investing in Training and Development
Continuous training and development of personnel are critical for effective failure analysis. Companies should invest in training programs that equip teams with the necessary skills and knowledge.
Leveraging Advanced Tools and Technology
Utilizing advanced tools, such as Failure Modes and Effects Analysis (FMEA), Root Cause Analysis (RCA) software, and data analytics, enhances the accuracy and efficiency of failure analysis.
Fostering a Culture of Open Communication
Encouraging open communication and collaboration among teams promotes the sharing of insights and ideas. A supportive culture makes it easier to identify and address failures promptly.
Integrating Failure Analysis into the Product Lifecycle
Incorporating failure analysis at every stage of the product lifecycle, from design to post-production, ensures that potential issues are identified and addressed early, reducing the likelihood of failures.
Continuous Monitoring and Feedback
Implementing continuous monitoring systems allows for real-time detection of failures. Feedback mechanisms ensure that lessons learned from failure analysis are integrated into future processes.
Practical Content from the Procurement and Purchasing Perspective
From the procurement and purchasing standpoint, failure analysis plays a pivotal role in supplier selection, relationship management, and cost optimization.
Supplier Selection and Evaluation
Incorporating failure analysis into supplier selection criteria ensures that only those suppliers capable of maintaining high quality standards are chosen. Evaluating suppliers based on their failure analysis capabilities can lead to more reliable partnerships.
Risk Management
Failure analysis helps in identifying potential risks in the supply chain. By understanding the common failure modes of suppliers, procurement teams can develop strategies to mitigate these risks, ensuring supply chain resilience.
Cost Optimization
Effective failure analysis leads to the identification and elimination of inefficiencies, resulting in cost savings. By preventing defects and reducing waste, procurement can negotiate better pricing and optimize budgets.
Enhancing Supplier Performance
Regular failure analysis provides insights into supplier performance. Providing feedback and collaborating on improvements fosters a culture of excellence, enhancing overall supplier performance.
Strategic Sourcing
Incorporating failure analysis into strategic sourcing decisions ensures that procurement strategies are aligned with quality and reliability goals. This alignment helps in building a robust and reliable supply chain.
Advantages of Japanese Failure Analysis Practices in Procurement
Adopting Japanese failure analysis practices offers several advantages for procurement and purchasing teams:
Enhanced Supplier Reliability
Japanese practices emphasize thorough failure analysis, leading to more reliable suppliers. This reliability reduces the risk of supply chain disruptions and ensures consistent product quality.
Improved Negotiation Leverage
Understanding the failure modes and quality standards of suppliers provides procurement with stronger negotiation positions. It allows for more informed discussions on pricing, quality expectations, and contractual terms.
Long-Term Cost Savings
Investing in failure analysis upfront leads to significant long-term savings by preventing defects and reducing the need for costly recalls and repairs.
Competitive Advantage
Implementing robust failure analysis differentiates companies from competitors. It signals a commitment to quality and excellence, attracting customers and partners who value reliability.
Innovation and Continuous Improvement
Failure analysis fosters a culture of continuous improvement and innovation. By learning from failures, procurement teams can drive process enhancements and product innovations.
Challenges and Mitigation Strategies
While the benefits of failure analysis are substantial, there are challenges that need to be addressed to ensure its effective implementation.
Resource Allocation
Failure analysis can be resource-intensive. To mitigate this, companies can prioritize critical components for in-depth analysis and leverage automation tools to streamline the process.
Skill Gaps
A lack of skilled personnel can hinder failure analysis efforts. Investing in training and developing a knowledgeable workforce is essential to overcome this challenge.
Resistance to Change
Introducing systematic failure analysis may face resistance from teams accustomed to traditional practices. Change management strategies, including clear communication of benefits and involving teams in the process, can alleviate resistance.
Data Management
Handling large volumes of data generated during failure analysis can be overwhelming. Implementing effective data management systems and utilizing data analytics can enhance the handling and interpretation of data.
Maintaining Consistency
Ensuring consistent application of failure analysis procedures across the organization is challenging. Standardizing processes and conducting regular audits can help maintain consistency.
Case Studies: Success Stories in Japanese Manufacturing
Examining real-world examples of Japanese companies that have successfully implemented failure analysis provides valuable insights into best practices and effective strategies.
Toyota: Pioneering the Toyota Production System
Toyota is a prime example of integrating failure analysis into its production system. The use of “Andon” cords allows workers to signal issues immediately, enabling rapid failure analysis and corrective actions. This approach minimizes defects and enhances overall quality.
Panasonic: Embracing Total Quality Control
Panasonic’s commitment to total quality control includes rigorous failure analysis protocols. By involving all levels of the organization in quality assurance, Panasonic ensures that failures are promptly identified and addressed, leading to high product reliability.
Honda: Fostering Innovation through Failure Analysis
Honda integrates failure analysis into its innovation processes. By analyzing failures in prototype stages, Honda refines designs before mass production, ensuring superior product performance and reliability.
Integrating Failure Analysis into the Procurement Process
Incorporating failure analysis into the procurement process enhances the effectiveness of purchasing strategies and supplier management.
Early Supplier Involvement
Involving suppliers early in the product development process facilitates better failure analysis. Collaborative efforts in design and manufacturing can preempt potential failures, leading to more robust products.
Supplier Audits and Assessments
Regular audits and assessments focused on failure analysis capabilities help in monitoring supplier performance. These evaluations ensure that suppliers adhere to quality standards and continuously improve their processes.
Incorporating Failure Analysis in Contracts
Including failure analysis requirements in supplier contracts formalizes expectations. It ensures that suppliers are committed to maintaining high-quality standards and support failure analysis initiatives.
Data Sharing and Transparency
Sharing failure analysis data with suppliers promotes transparency and collaborative problem-solving. This openness helps in identifying common issues and developing joint solutions.
Continuous Feedback Loops
Establishing continuous feedback loops with suppliers ensures that failure analysis insights are integrated into procurement strategies. This integration fosters ongoing improvement and alignment with quality objectives.
The Future of Failure Analysis in Japanese Manufacturing
As technology evolves and market dynamics shift, the role of failure analysis in Japanese manufacturing continues to adapt and grow.
Integration of Artificial Intelligence and Machine Learning
AI and machine learning are revolutionizing failure analysis by enabling predictive analytics and automated root cause identification. These technologies enhance the speed and accuracy of failure analysis, allowing for proactive quality management.
Digital Twins and Simulation
The use of digital twins and simulation tools allows for virtual testing and failure analysis. This approach reduces the need for physical prototypes and accelerates the identification of potential failures during the design phase.
Enhanced Data Analytics
Advanced data analytics tools facilitate the processing and interpretation of vast amounts of failure data. These tools provide deeper insights into failure trends and patterns, supporting more informed decision-making.
Sustainable Manufacturing Practices
Sustainability is becoming increasingly important in manufacturing. Failure analysis practices are evolving to incorporate environmental impact assessments, ensuring that products are not only reliable but also environmentally friendly.
Global Collaboration
With the globalization of supply chains, Japanese manufacturers are enhancing their failure analysis practices through global collaboration. Sharing knowledge and best practices across international teams strengthens the overall quality and reliability of products.
Conclusion
Failure analysis, or 故障解析, is a cornerstone of Japanese manufacturing excellence. Its systematic approach to identifying and addressing failures fosters a culture of continuous improvement, leading to high-quality, reliable products. From procurement and purchasing perspectives, integrating failure analysis enhances supplier relationships, optimizes costs, and mitigates risks. While challenges exist, adopting best practices and leveraging advanced technologies can overcome these obstacles, ensuring the sustained success of Japanese manufacturing in the global market. Embracing the art of failure analysis not only unlocks the secrets of engineering excellence but also paves the way for innovation and long-term competitiveness.
資料ダウンロード
QCD管理受発注クラウド「newji」は、受発注部門で必要なQCD管理全てを備えた、現場特化型兼クラウド型の今世紀最高の受発注管理システムとなります。
ユーザー登録
受発注業務の効率化だけでなく、システムを導入することで、コスト削減や製品・資材のステータス可視化のほか、属人化していた受発注情報の共有化による内部不正防止や統制にも役立ちます。
NEWJI DX
製造業に特化したデジタルトランスフォーメーション(DX)の実現を目指す請負開発型のコンサルティングサービスです。AI、iPaaS、および先端の技術を駆使して、製造プロセスの効率化、業務効率化、チームワーク強化、コスト削減、品質向上を実現します。このサービスは、製造業の課題を深く理解し、それに対する最適なデジタルソリューションを提供することで、企業が持続的な成長とイノベーションを達成できるようサポートします。
製造業ニュース解説
製造業、主に購買・調達部門にお勤めの方々に向けた情報を配信しております。
新任の方やベテランの方、管理職を対象とした幅広いコンテンツをご用意しております。
お問い合わせ
コストダウンが利益に直結する術だと理解していても、なかなか前に進めることができない状況。そんな時は、newjiのコストダウン自動化機能で大きく利益貢献しよう!
(β版非公開)