- お役立ち記事
- Unlocking the Secrets of Japanese Manufacturing: Why Zinc is Essential in Japanese Industry
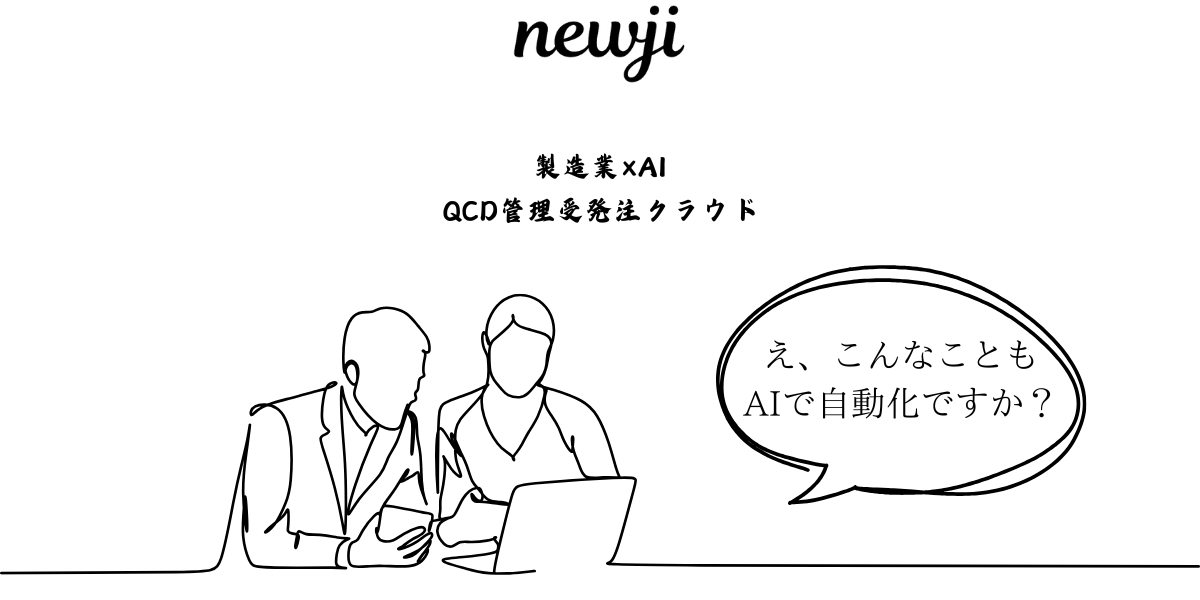
Unlocking the Secrets of Japanese Manufacturing: Why Zinc is Essential in Japanese Industry
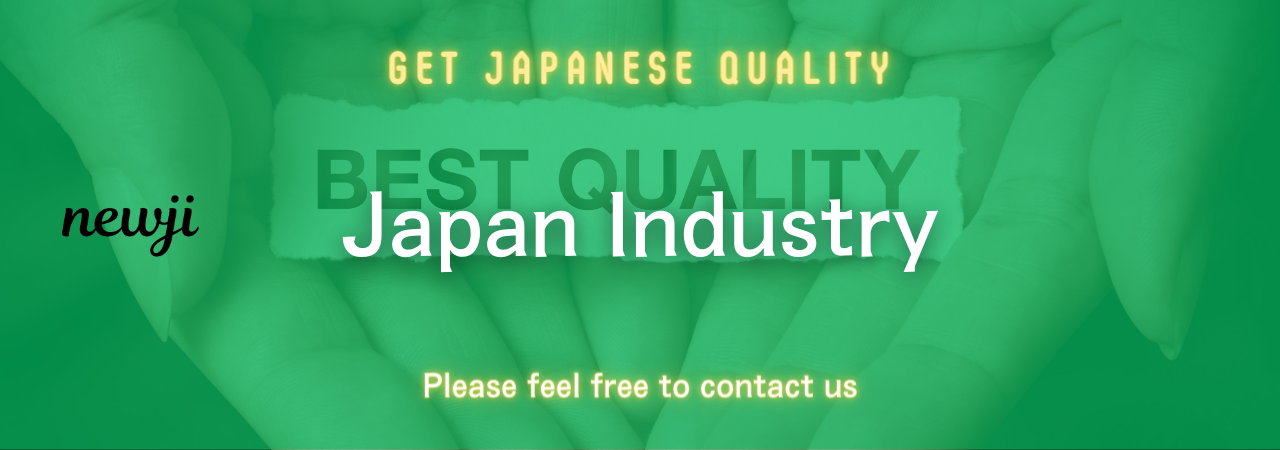
Zinc is a versatile and essential component in many industrial applications, and its significance is especially pronounced in the Japanese manufacturing sector. With a rich history of industrial prowess that prioritizes quality, efficiency, and innovation, Japan has strategically leveraged zinc to bolster various industries, from automotive to electronics. Understanding why zinc plays such a crucial role in Japanese industry requires delving into its properties, applications, and the sophisticated practices employed by Japanese manufacturers.
目次
The Role of Zinc in Industry
Zinc’s inherent qualities make it indispensable in many industrial applications. Notably, zinc is highly resistant to corrosion and oxidation, making it a prime material for protective coatings. Also, zinc is highly malleable and ductile, which means it can easily be stretched and shaped without breaking.
Moreover, zinc has excellent thermal and electrical conductivity, which lends itself to applications in various high-tech industries. This combination of properties underscores zinc’s importance in industries that demand durability and reliability, two characteristics that are highly valued in Japanese manufacturing.
Corrosion Resistance
One of the most critical properties of zinc is its natural resistance to corrosion. This characteristic makes it an ideal choice for galvanizing, a process that involves applying a protective zinc coating to steel or iron surfaces to prevent rusting. Japanese manufacturers extensively utilize galvanized steel in construction, automotive manufacturing, and infrastructure projects, ensuring longevity and reduced maintenance costs.
Thermal and Electrical Conductivity
Zinc’s superior thermal and electrical conductivity opens the door to a wide array of applications in the electronics and electrical industries. In Japan, a country renowned for its cutting-edge technology, zinc is used in the production of batteries, particularly zinc-carbon and zinc-air batteries. These batteries power a multitude of devices, underscoring zinc’s pivotal role in driving technological advancement.
Zinc in the Japanese Automotive Industry
The automotive industry is a cornerstone of Japan’s economy, with brands like Toyota, Nissan, and Honda leading the global market. Zinc’s contributions to this sector cannot be overstated. From enhancing vehicle longevity to improving safety and performance, zinc is integrated into the very fabric of automotive manufacturing in Japan.
Galvanized Steel in Automotive Bodies
Corrosion resistance is paramount in vehicle manufacturing, as it directly impacts a car’s lifespan and safety. Japanese automakers extensively use galvanized steel to construct vehicle bodies, ensuring that they remain rust-free even in harsh environments. This not only improves the durability of the vehicles but also reduces the need for frequent repairs, enhancing customer satisfaction and brand reputation.
Die-Casting Components
Another significant application of zinc in the automotive industry is in the creation of die-cast components. Zinc alloys are favored for their strength, toughness, and precision casting capabilities. These alloys are used to manufacture various automotive parts, such as door handles, carburetors, and air-conditioning units. The use of zinc in die-casting allows for the production of complex components with tight tolerances, meeting the high-quality standards set by Japanese manufacturers.
The Electronics and Electrical Sector
Japan’s electronics and electrical sector is synonymous with innovation and high standards. Zinc, due to its electrical conductivity and thermal resistance, plays a vital role in the production of components used in this sector.
Zinc in Battery Technology
Batteries are a critical component of modern electronics, and zinc-based batteries are a popular choice due to their reliability and cost-effectiveness. Zinc-carbon batteries have been a staple for low-drain devices such as remote controls and clocks, while zinc-air batteries are used in hearing aids and other medical devices.
Japanese companies have continued to invest heavily in research and development to enhance the performance of zinc-based batteries, ensuring they remain competitive in the global market.
Zinc Oxide in Semiconductors
Zinc oxide has unique semiconductor properties that are utilized in the manufacturing of electronic devices. It is used in thin-film transistors and light-emitting diodes (LEDs), contributing to the advancements in display technology and energy-efficient lighting solutions.
Japanese manufacturers are at the forefront of developing new applications for zinc oxide, integrating it into sophisticated electronics that drive consumer demand.
Japanese Practices in Zinc Procurement
The procurement of zinc in Japan is a highly strategic process, characterized by meticulous planning and strong relationships with suppliers. Japanese companies prioritize quality, consistency, and reliability, adhering to best practices that have been refined over decades.
Supplier Selection and Evaluation
Japanese manufacturers employ a rigorous supplier selection process, focusing on the supplier’s ability to deliver high-quality raw materials consistently. This involves comprehensive evaluations of the supplier’s production capabilities, quality control measures, and track record. By forging long-term partnerships with reputable suppliers, Japanese companies ensure a stable supply of zinc, which is crucial for maintaining their manufacturing standards.
Price Negotiation Techniques
Negotiating prices effectively is vital for managing procurement costs. Japanese companies prioritize transparency and mutual benefit in their negotiations. They emphasize fair pricing, quality assurance, and reliability over merely achieving the lowest cost. This approach fosters trust and cooperation, leading to beneficial long-term relationships with suppliers.
Furthermore, Japanese manufacturers often enter into long-term contracts with fixed prices, mitigating the impact of market volatility. This strategy provides both the supplier and the manufacturer with predictability and stability, allowing for better financial planning and resource allocation.
Market Conditions and Strategic Procurement
Understanding market conditions is crucial for effective procurement. Japanese companies closely monitor global zinc markets, keeping abreast of trends, price fluctuations, and supply chain disruptions. This knowledge enables them to make informed purchasing decisions and anticipate potential challenges.
Strategic procurement practices, such as bulk purchasing and strategic stockpiling, are employed to mitigate risks associated with supply shortages or price spikes. By maintaining a buffer stock of zinc, Japanese manufacturers can continue production without interruption, ensuring consistency and reliability in their operations.
Best Practices in Zinc Utilization
To maximize the benefits of using zinc in manufacturing, Japanese companies adhere to several best practices that optimize its application and enhance overall production efficiency.
Quality Control and Testing
Quality control is a cornerstone of Japanese manufacturing, and this extends to the utilization of zinc. Comprehensive testing and inspection procedures are implemented at every stage of the production process to ensure that zinc components meet stringent quality standards.
Advanced testing methods, such as X-ray fluorescence (XRF) and inductively coupled plasma (ICP) spectroscopy, are employed to analyze the composition and purity of zinc materials. By maintaining high quality control standards, Japanese manufacturers produce reliable and durable products that meet customer expectations.
Sustainable Practices
Sustainability is increasingly becoming a priority in global manufacturing, and Japanese companies are no exception. They are committed to minimizing the environmental impact of their operations by adopting sustainable practices in zinc procurement and utilization.
Recycling is a key component of these efforts. Zinc is highly recyclable, and Japanese manufacturers have established efficient recycling systems to recover zinc from end-of-life products and manufacturing scrap. This not only reduces the demand for virgin zinc but also minimizes waste and conserves natural resources.
Moreover, Japanese companies are investing in research and development to improve the environmental performance of zinc-based products. For instance, they are exploring ways to enhance the energy efficiency of zinc-air batteries and reduce the environmental impact of the galvanizing process.
Innovation and Continuous Improvement
Innovation and continuous improvement are ingrained in the culture of Japanese manufacturing. Companies are constantly seeking new ways to leverage zinc’s properties to develop advanced materials and technologies.
Collaborative research and development initiatives with academic institutions and industry partners play a crucial role in driving innovation. By staying at the forefront of technological advancements, Japanese manufacturers can maintain their competitive edge in the global market.
Challenges and Future Outlook
Despite the numerous advantages of using zinc, there are challenges that Japanese manufacturers must navigate to maintain their leadership position in the global market.
Supply Chain Disruptions
Supply chain disruptions, such as those caused by geopolitical tensions or natural disasters, can impact the availability and cost of zinc. Japanese companies must develop robust risk management strategies to mitigate these disruptions and ensure a stable supply of raw materials.
Environmental Regulations
Stringent environmental regulations, both domestic and international, are another challenge for Japanese manufacturers. Companies must comply with regulations related to emissions, waste management, and resource conservation, which can add complexity to their operations.
However, these challenges also present opportunities for innovation. By developing environmentally friendly processes and products, Japanese manufacturers can differentiate themselves in the market and meet the growing demand for sustainable solutions.
Technological Advancements
The rapid pace of technological advancements presents both opportunities and challenges. Japanese manufacturers must stay abreast of emerging technologies and trends to remain competitive. This requires continuous investment in research and development and a willingness to adapt to changing market conditions.
Conclusion
Zinc is an essential material in Japanese manufacturing, playing a pivotal role in various industries, from automotive to electronics. Its unique properties, such as corrosion resistance, thermal and electrical conductivity, and malleability, make it indispensable in a range of applications.
Japanese manufacturers have perfected the art of zinc utilization through meticulous procurement practices, stringent quality control, and a commitment to innovation and sustainability. By maintaining strong relationships with suppliers, monitoring market conditions, and adopting best practices, they ensure the consistent and efficient use of zinc in their operations.
As the global market continues to evolve, Japanese manufacturers must navigate challenges such as supply chain disruptions, environmental regulations, and technological advancements. However, with their culture of continuous improvement and innovation, they are well-positioned to overcome these challenges and maintain their leadership in the global manufacturing landscape.
In conclusion, the secrets of Japanese manufacturing success lie in their ability to harness the properties of materials like zinc to create high-quality, reliable, and sustainable products. By understanding and applying these principles, other manufacturers can unlock the potential of zinc and achieve similar success in their respective industries.
資料ダウンロード
QCD調達購買管理クラウド「newji」は、調達購買部門で必要なQCD管理全てを備えた、現場特化型兼クラウド型の今世紀最高の購買管理システムとなります。
ユーザー登録
調達購買業務の効率化だけでなく、システムを導入することで、コスト削減や製品・資材のステータス可視化のほか、属人化していた購買情報の共有化による内部不正防止や統制にも役立ちます。
NEWJI DX
製造業に特化したデジタルトランスフォーメーション(DX)の実現を目指す請負開発型のコンサルティングサービスです。AI、iPaaS、および先端の技術を駆使して、製造プロセスの効率化、業務効率化、チームワーク強化、コスト削減、品質向上を実現します。このサービスは、製造業の課題を深く理解し、それに対する最適なデジタルソリューションを提供することで、企業が持続的な成長とイノベーションを達成できるようサポートします。
オンライン講座
製造業、主に購買・調達部門にお勤めの方々に向けた情報を配信しております。
新任の方やベテランの方、管理職を対象とした幅広いコンテンツをご用意しております。
お問い合わせ
コストダウンが利益に直結する術だと理解していても、なかなか前に進めることができない状況。そんな時は、newjiのコストダウン自動化機能で大きく利益貢献しよう!
(Β版非公開)