- お役立ち記事
- Unlocking the World of Die Sets: How Japanese Precision Transforms Global Manufacturing
Unlocking the World of Die Sets: How Japanese Precision Transforms Global Manufacturing
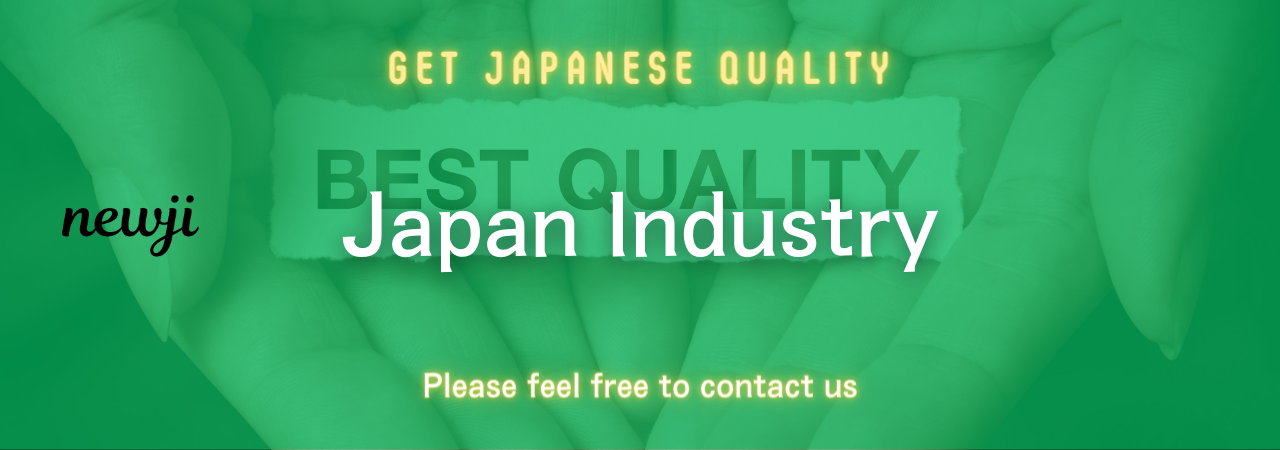
目次
Introduction
In the intricate world of manufacturing, precision die sets play a pivotal role in shaping the components that go into countless products, from automotive parts to consumer electronics. Among the global players in this domain, Japanese suppliers have carved out a reputation for their unmatched precision, quality, and innovation.
For procurement and purchasing professionals in the international manufacturing sector, understanding the value that Japanese precision brings can unlock significant benefits, including cost savings, enhanced product quality, and streamlined production processes.
Why Japanese Die Sets? The Advantages
Unparalleled Precision
Japanese die set manufacturers are synonymous with precision. This stems from a culture that prioritizes meticulous attention to detail and a continuous pursuit of perfection. When working with components that require tight tolerances, such as microelectronic parts or intricate automotive pieces, this level of precision ensures the highest quality and consistency in production.
Quality Control and Assurance
Japanese companies are renowned for their rigorous quality control (QC) processes. The implementation of Total Quality Management (TQM) and other comprehensive QC methodologies ensures that every die set produced meets the highest standards. For international buyers, this means fewer defects, less rework, and ultimately, a more reliable production process.
Innovative Technologies
Japan has long been at the forefront of manufacturing technology advancements. From the adoption of advanced materials to pioneering developments in automation and robotics, Japanese die set suppliers often leverage the latest technologies to deliver superior products. This innovative edge can be a significant advantage for companies looking to stay ahead of the competition.
Longevity and Durability
Due to the superior materials and precise manufacturing processes used, Japanese die sets tend to have a longer lifespan. This durability translates to less frequent replacements and lower maintenance costs, contributing to overall cost savings in the long run.
Challenges and Considerations
Higher Initial Costs
Quality comes at a price. Japanese die sets typically have a higher initial cost compared to those from other regions. However, this should be viewed as an investment rather than an expense. The long-term benefits, such as reduced downtime, fewer defects, and lower maintenance costs, often offset the higher upfront cost.
Logistics and Lead Times
Shipping from Japan can involve longer lead times and higher logistics costs, especially if the die sets are custom-made. Effective planning and coordination with suppliers can mitigate these issues. Moreover, many Japanese suppliers have established distribution networks across the globe, which can help reduce lead times.
Cultural and Language Barriers
While many Japanese businesses are proficient in English, cultural and language differences can sometimes pose challenges in communication and negotiation. Building strong relationships and understanding Japanese business etiquette can go a long way in bridging these gaps.
Effective Supplier Negotiation Techniques
Building Relationships
In Japan, business relationships are built on trust and long-term collaboration. Demonstrating commitment and respect can significantly enhance your negotiations. Regular visits, transparent communication, and showing an understanding of their culture can strengthen these ties.
Understanding Their Value Proposition
Recognize and articulate the specific advantages of their die sets for your production needs. Whether it’s the precision, durability, or innovative aspects, understanding and valuing their strengths can lead to more fruitful negotiations.
Leveraging Volume and Long-Term Contracts
Japanese suppliers value long-term partnerships. Committing to larger volumes or longer-term contracts can often lead to better pricing and priority treatment. Discussing future plans and growth can create a collaborative environment where both parties benefit.
Flexibility and Customization
While Japanese manufacturers excel in standardized products, many also offer customization to meet specific requirements. Be clear about your needs and explore how they can tailor their offerings to suit your needs. This bespoke approach can often lead to innovative solutions that off-the-shelf products cannot provide.
Market Conditions and Trends
Growing Demand for Precision Engineering
As industries like automotive, aerospace, and electronics continue to evolve, the demand for precision-engineered components is on the rise. Japanese die set suppliers, with their focus on accuracy and quality, are well-positioned to meet this growing need.
Adoption of Advanced Materials
There’s a trend towards using advanced materials, such as high-strength alloys and composites, in manufacturing die sets. Japanese manufacturers are at the forefront of this trend, offering products that can withstand higher stresses and have longer lifespans.
Integration of Smart Technologies
The integration of IoT and smart technologies in manufacturing is revolutionizing the industry. Japanese die set producers are incorporating sensors and monitoring systems to provide real-time data, which can optimize the manufacturing process and predict maintenance needs, thus reducing downtime.
Environmental Sustainability
Sustainability is becoming a crucial factor in manufacturing. Japanese suppliers are increasingly focusing on eco-friendly practices, from the materials used in their die sets to the energy efficiency of their production processes. This aligns with the global push towards greener manufacturing.
Best Practices for Procurement and Purchasing
Comprehensive Supplier Evaluation
Before finalizing a supplier, conduct a thorough evaluation. This should include an assessment of their production capabilities, quality control processes, and financial stability. Visiting their production facilities can provide valuable insights into their operations and help build a stronger relationship.
Clear Specifications and Standards
Clearly outline your requirements, including specifications and quality standards. Providing detailed drawings and tolerances ensures that the supplier understands exactly what you need, reducing the risk of errors and miscommunications.
Regular Quality Audits and Reviews
Implement regular quality audits and reviews to ensure that the supplier’s products meet your standards. This can include site visits, sample inspections, and reviewing their quality control processes. Continuous feedback helps maintain high standards and addresses any issues promptly.
Strategic Inventory Management
Managing inventory effectively can mitigate the impact of longer lead times. This might involve maintaining a buffer stock of critical components or scheduling deliveries in such a way as to avoid production disruptions. Close coordination with the supplier ensures a steady flow of materials.
Case Studies: Success Stories
Automotive Manufacturer
An international automotive manufacturer collaborated with a Japanese die set supplier to improve the precision and reliability of their engine components. By leveraging the supplier’s advanced materials and precision engineering capabilities, they achieved a 20% reduction in defects and a 15% improvement in production speed. The initial higher costs were quickly offset by these savings, leading to a more profitable and efficient production line.
Consumer Electronics Producer
A leading consumer electronics company partnered with a Japanese die set manufacturer to produce high-precision components for their latest smartphone model. The collaboration resulted in components that met stringent quality standards and improved the overall durability of the final product. This partnership also provided the company with innovative solutions that they leveraged in their marketing campaigns, boosting their brand reputation.
Aerospace Industry Example
In the aerospace industry, where precision and reliability are paramount, a global aerospace company sourced die sets from a Japanese supplier. They benefited from the supplier’s cutting-edge technology and stringent quality controls, which contributed to higher safety standards and enhanced performance of their aerospace components. The collaboration was so successful that it led to a long-term strategic partnership, with the Japanese supplier becoming a key player in their supply chain.
Conclusion: The Path Forward
Engaging with Japanese die set suppliers can unlock significant advantages for manufacturers across various industries. From unparalleled precision and quality control to innovative technologies and long-term cost savings, the benefits are substantial. However, it is essential to consider the challenges and implement best practices to maximize these advantages.
Building strong, long-term relationships, understanding market trends, and adopting strategic procurement practices are key to successful collaborations with Japanese suppliers. As global manufacturing continues to evolve, leveraging the precision and expertise of Japanese die set manufacturers can be a pivotal factor in maintaining competitiveness and achieving production excellence.
資料ダウンロード
QCD調達購買管理クラウド「newji」は、調達購買部門で必要なQCD管理全てを備えた、現場特化型兼クラウド型の今世紀最高の購買管理システムとなります。
ユーザー登録
調達購買業務の効率化だけでなく、システムを導入することで、コスト削減や製品・資材のステータス可視化のほか、属人化していた購買情報の共有化による内部不正防止や統制にも役立ちます。
NEWJI DX
製造業に特化したデジタルトランスフォーメーション(DX)の実現を目指す請負開発型のコンサルティングサービスです。AI、iPaaS、および先端の技術を駆使して、製造プロセスの効率化、業務効率化、チームワーク強化、コスト削減、品質向上を実現します。このサービスは、製造業の課題を深く理解し、それに対する最適なデジタルソリューションを提供することで、企業が持続的な成長とイノベーションを達成できるようサポートします。
オンライン講座
製造業、主に購買・調達部門にお勤めの方々に向けた情報を配信しております。
新任の方やベテランの方、管理職を対象とした幅広いコンテンツをご用意しております。
お問い合わせ
コストダウンが利益に直結する術だと理解していても、なかなか前に進めることができない状況。そんな時は、newjiのコストダウン自動化機能で大きく利益貢献しよう!
(Β版非公開)