- お役立ち記事
- “Unpacking Japan’s Steel Belt OEM: The Backbone of Precision Manufacturing”
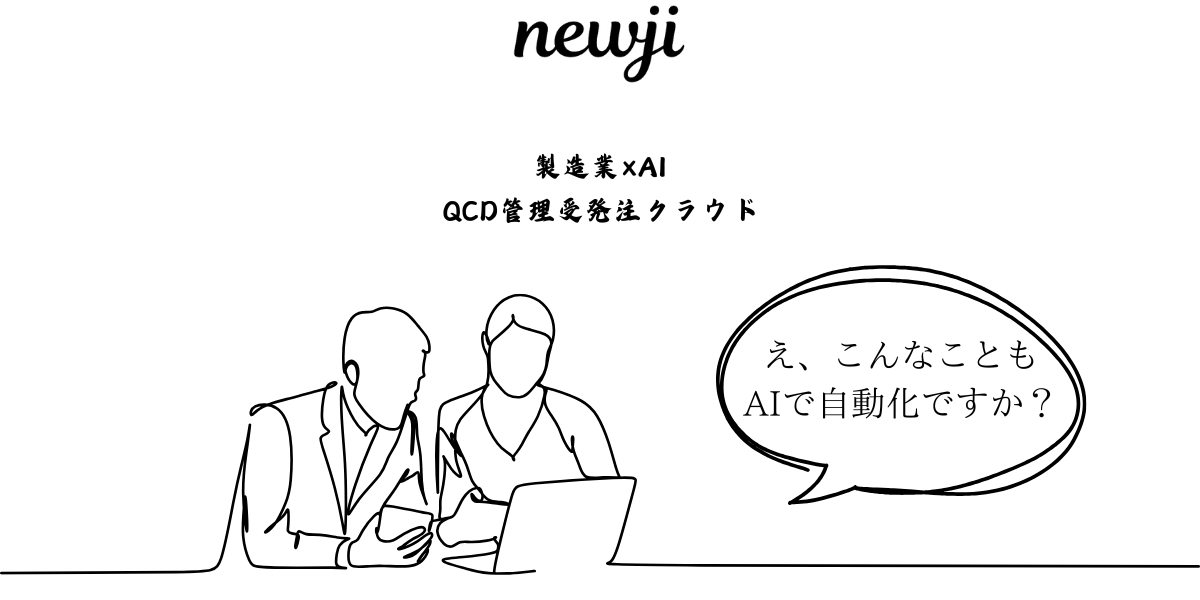
“Unpacking Japan’s Steel Belt OEM: The Backbone of Precision Manufacturing”
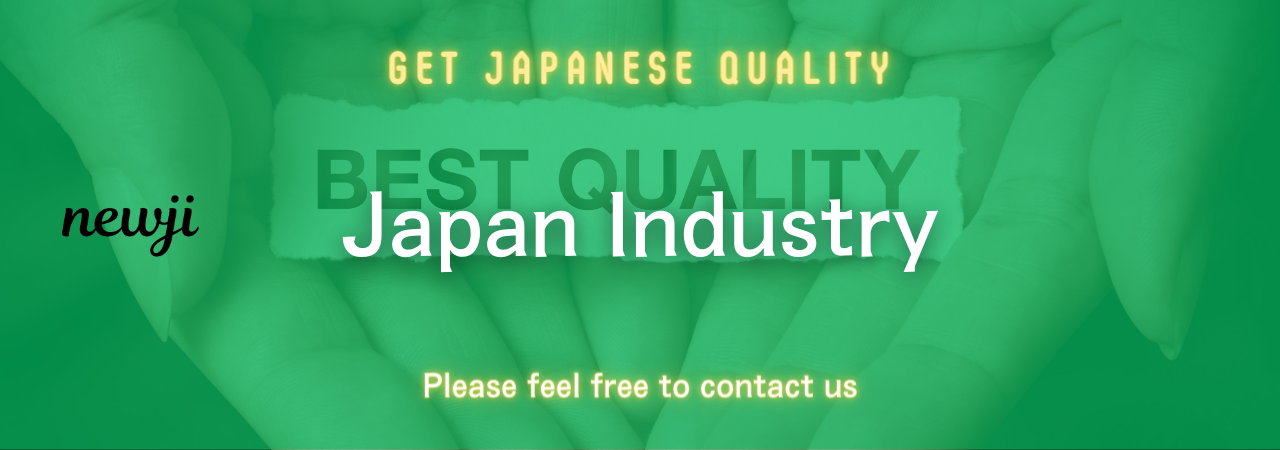
目次
Introduction to Japan’s Steel Belt OEM
Japan’s manufacturing sector is renowned worldwide for its precision and reliability, largely due to the robust network of Original Equipment Manufacturers (OEMs) within the steel belt region. This network serves as the backbone of precision manufacturing, providing essential components and materials that ensure the quality and efficiency of various industries.
The Importance of OEMs in Precision Manufacturing
OEMs play a critical role in the manufacturing ecosystem by supplying specialized parts and materials that are integral to the production process. In Japan’s steel belt, these OEMs are known for their meticulous attention to detail and adherence to high-quality standards, which are pivotal in maintaining the integrity of the final products.
Key Functions of OEMs
OEMs in the steel belt area are responsible for:
– **Supplying high-precision components**: Ensuring that every part meets exact specifications.
– **Maintaining quality control**: Implementing stringent quality assurance processes to prevent defects.
– **Facilitating innovation**: Collaborating with manufacturers to develop new materials and technologies.
Impact on Various Industries
The precision provided by steel belt OEMs directly impacts multiple sectors, including:
– **Automotive**: High-precision components are crucial for vehicle safety and performance.
– **Electronics**: Precision parts contribute to the functionality and durability of electronic devices.
– **Aerospace**: The aerospace industry relies on OEMs for components that must withstand extreme conditions.
Advantages of Partnering with Japanese Steel Belt OEMs
Collaborating with OEMs in Japan’s steel belt offers numerous benefits that enhance the overall manufacturing process.
Unparalleled Quality Standards
Japanese OEMs are synonymous with high quality, thanks to their rigorous quality control measures. This commitment ensures that manufacturers receive components that are reliable and long-lasting.
Advanced Technology and Innovation
Japanese companies invest heavily in research and development, leading to continuous innovation. This results in the availability of cutting-edge materials and manufacturing techniques that can improve product performance.
Efficient Supply Chain Management
Japanese OEMs are known for their efficient supply chains, which minimize lead times and reduce the risk of delays. This reliability is crucial for maintaining production schedules and meeting market demands.
Strong Supplier Relationships
The emphasis on long-term relationships fosters trust and collaboration between manufacturers and OEMs. This partnership approach facilitates better communication and problem-solving.
Challenges and Considerations
While there are significant advantages, partnering with Japanese steel belt OEMs also presents certain challenges.
Higher Costs
Japanese OEMs often come with higher price points due to their quality standards and advanced technologies. Manufacturers must weigh these costs against the benefits of superior components.
Cultural and Communication Barriers
Differences in business practices and communication styles can pose challenges. Effective cross-cultural communication strategies are essential to overcome these barriers.
Dependency Risks
Relying heavily on a single OEM or region can create supply chain vulnerabilities. Diversifying suppliers can mitigate this risk.
Supplier Negotiation Techniques
Effective negotiation with Japanese OEMs requires a nuanced approach that respects cultural norms and business practices.
Building Trust and Relationships
Japanese business culture places a high value on trust and long-term relationships. Investing time in relationship-building activities can lead to more favorable negotiation outcomes.
Understanding Cultural Nuances
Being aware of and respecting Japanese business etiquette can enhance negotiations. This includes practices such as punctuality, formal communication, and modesty.
Emphasizing Mutual Benefits
Focus on creating win-win scenarios where both parties gain value. Highlight how the partnership can lead to mutual growth and success.
Leveraging Quality and Reliability
Use the superior quality and reliability of the OEM’s products as a bargaining chip. Demonstrating the long-term benefits of their components can justify higher costs.
Market Conditions and Trends
Staying informed about the current market conditions and trends is vital for making strategic procurement decisions.
Global Supply Chain Dynamics
Global supply chain disruptions have highlighted the importance of resilient supply networks. Japanese OEMs’ reliability can be a stabilizing factor in uncertain times.
Sustainability and Environmental Standards
There is a growing emphasis on sustainable manufacturing practices. Japanese OEMs are leading in implementing eco-friendly processes and materials, aligning with global sustainability goals.
Technological Advancements
Advancements in technology, such as automation and smart manufacturing, are shaping the future of precision manufacturing. Collaborating with technologically advanced OEMs ensures access to the latest innovations.
Best Practices for Procurement and Purchasing
Adopting best practices in procurement and purchasing can maximize the benefits of partnering with Japanese OEMs.
Comprehensive Supplier Evaluation
Conduct thorough evaluations of potential OEM partners, considering factors such as quality standards, financial stability, and technological capabilities.
Clear Contract Agreements
Establish clear and detailed contracts that outline expectations, responsibilities, and terms. This helps prevent misunderstandings and ensures alignment between parties.
Continuous Performance Monitoring
Implement systems to monitor supplier performance regularly. Use key performance indicators (KPIs) to assess quality, delivery times, and other critical metrics.
Collaborative Innovation
Work closely with OEMs to develop new products and improve existing ones. Collaborative innovation can lead to competitive advantages and enhanced product features.
Strategies for Enhancing Factory Efficiency and Automation
Improving factory efficiency and embracing automation are crucial for maintaining competitiveness in precision manufacturing.
Integrating Advanced Manufacturing Technologies
Adopt technologies such as robotics, IoT, and artificial intelligence to streamline production processes and reduce manual labor.
Optimizing Supply Chain Management
Use data analytics and supply chain management software to optimize inventory levels, forecast demand, and improve logistics operations.
Implementing Lean Manufacturing Principles
Embrace lean manufacturing techniques to eliminate waste, improve workflow, and enhance overall efficiency.
Training and Development
Invest in training programs to equip employees with the skills needed to operate advanced machinery and adapt to new technologies.
Quality Control and Assurance
Maintaining high-quality standards is non-negotiable in precision manufacturing. Implementing robust quality control and assurance practices is essential.
Standardized Quality Processes
Develop and adhere to standardized quality processes that ensure consistency and reliability in every component produced.
Regular Audits and Inspections
Conduct regular audits and inspections of both internal processes and OEM suppliers to identify and address potential quality issues.
Feedback Loops
Establish feedback mechanisms to gather input from customers and stakeholders. Use this information to continuously improve quality standards.
Certification and Compliance
Ensure compliance with relevant industry standards and obtain necessary certifications to demonstrate commitment to quality.
Logistics and Supply Chain Optimization
Efficient logistics and supply chain management are critical for timely production and delivery of products.
Strategic Sourcing
Identify and source materials from suppliers who can provide quality components at competitive prices while ensuring timely delivery.
Inventory Management
Implement effective inventory management systems to balance stock levels, reduce holding costs, and prevent shortages.
Transportation and Distribution
Optimize transportation routes and distribution networks to minimize delays and reduce shipping costs.
Risk Management
Develop risk management strategies to handle potential disruptions in the supply chain, such as natural disasters or geopolitical tensions.
Case Studies: Successful Partnerships with Japanese OEMs
Examining real-world examples can provide valuable insights into successful procurement strategies.
Automotive Industry Collaboration
A leading automotive manufacturer partnered with a Japanese OEM to source high-precision engine components. Through close collaboration and quality control measures, the partnership resulted in improved engine performance and reduced production costs.
Electronics Manufacturing Success
An electronics company worked with a Japanese OEM to develop customized circuit boards. The collaboration leveraged the OEM’s advanced technology, leading to the launch of a highly competitive product in the market.
Aerospace Industry Advancement
An aerospace firm partnered with a Japanese OEM for the supply of specialized materials used in aircraft construction. The partnership ensured the highest quality standards, contributing to safer and more durable aircraft.
Future Outlook for Japan’s Steel Belt OEMs
The future of Japan’s steel belt OEMs looks promising, with ongoing advancements and evolving market demands shaping the landscape.
Embracing Digital Transformation
Japanese OEMs are increasingly adopting digital technologies to enhance manufacturing processes, improve product traceability, and facilitate better decision-making.
Focus on Sustainability
There is a growing emphasis on sustainable manufacturing practices, with OEMs investing in eco-friendly materials and reducing their environmental footprint.
Global Expansion
Japanese OEMs are expanding their presence globally, establishing partnerships and facilities in key markets to better serve their international clients.
Innovation and R&D Investment
Continued investment in research and development ensures that OEMs remain at the forefront of technological advancements, driving innovation in precision manufacturing.
Conclusion
Japan’s steel belt OEMs are the cornerstone of precision manufacturing, offering unparalleled quality, advanced technology, and reliable supply chains. While challenges such as higher costs and cultural barriers exist, the advantages of partnering with these OEMs far outweigh the drawbacks. By adopting effective procurement strategies, fostering strong supplier relationships, and embracing innovation, manufacturers can leverage the strengths of Japan’s steel belt OEMs to enhance their own production capabilities and achieve long-term success in the global market.
資料ダウンロード
QCD調達購買管理クラウド「newji」は、調達購買部門で必要なQCD管理全てを備えた、現場特化型兼クラウド型の今世紀最高の購買管理システムとなります。
ユーザー登録
調達購買業務の効率化だけでなく、システムを導入することで、コスト削減や製品・資材のステータス可視化のほか、属人化していた購買情報の共有化による内部不正防止や統制にも役立ちます。
NEWJI DX
製造業に特化したデジタルトランスフォーメーション(DX)の実現を目指す請負開発型のコンサルティングサービスです。AI、iPaaS、および先端の技術を駆使して、製造プロセスの効率化、業務効率化、チームワーク強化、コスト削減、品質向上を実現します。このサービスは、製造業の課題を深く理解し、それに対する最適なデジタルソリューションを提供することで、企業が持続的な成長とイノベーションを達成できるようサポートします。
オンライン講座
製造業、主に購買・調達部門にお勤めの方々に向けた情報を配信しております。
新任の方やベテランの方、管理職を対象とした幅広いコンテンツをご用意しております。
お問い合わせ
コストダウンが利益に直結する術だと理解していても、なかなか前に進めることができない状況。そんな時は、newjiのコストダウン自動化機能で大きく利益貢献しよう!
(Β版非公開)