- お役立ち記事
- Unveiling Britain’s Glass Masters: How the UK Leads in Innovative Glass Processing Manufacturing
月間76,176名の
製造業ご担当者様が閲覧しています*
*2025年3月31日現在のGoogle Analyticsのデータより
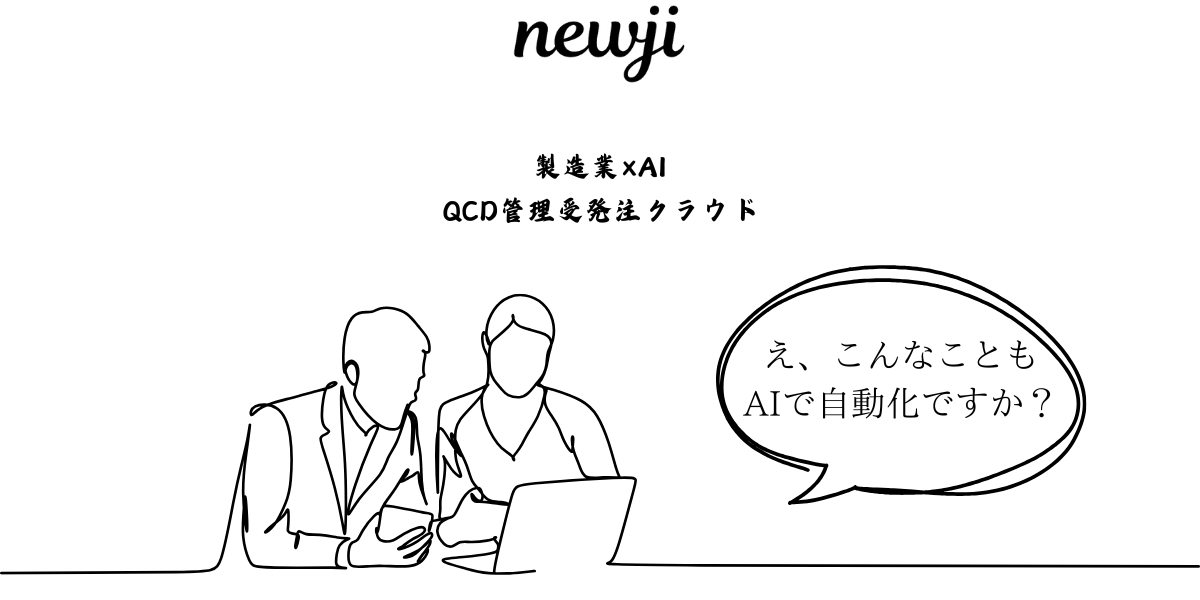
Unveiling Britain’s Glass Masters: How the UK Leads in Innovative Glass Processing Manufacturing
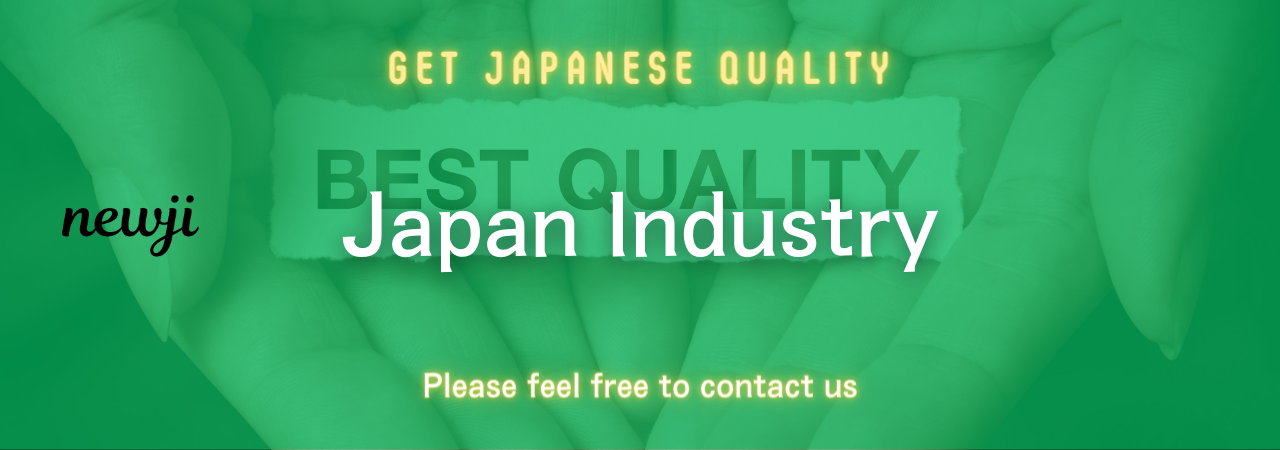
目次
Overview of the UK Glass Manufacturing Industry
The United Kingdom boasts a rich history in glass manufacturing, dating back centuries.
Today, it stands as a global leader in innovative glass processing.
The UK glass industry is renowned for its quality, precision, and advanced technological integration.
Manufacturers in the UK produce a wide range of glass products, from architectural and automotive glass to specialized industrial applications.
The industry’s success is underpinned by robust procurement and purchasing strategies, ensuring the consistent supply of high-quality materials and components.
British glass manufacturers leverage both domestic and international suppliers to maintain their competitive edge.
The sector is characterized by continuous innovation, with companies investing heavily in research and development to pioneer new glass technologies.
Sustainability is also a key focus, with many manufacturers adopting eco-friendly practices to reduce their environmental footprint.
The UK government’s support through favorable policies and incentives further strengthens the industry’s growth and resilience.
Overall, the UK glass manufacturing industry exemplifies how strategic procurement and purchasing can drive excellence and leadership in a competitive global market.
Procurement and Purchasing in Glass Manufacturing
Effective procurement and purchasing are critical to the success of the UK’s glass manufacturing sector.
These processes ensure the timely acquisition of necessary materials, components, and services, directly impacting production efficiency and product quality.
Procurement in glass manufacturing involves sourcing raw materials such as silica sand, soda ash, and limestone.
Purchasing extends to securing advanced machinery, specialized coatings, and quality control equipment.
The complexity of glass manufacturing demands a meticulous approach to supplier selection and relationship management.
British manufacturers prioritize suppliers who can consistently deliver high-quality materials and demonstrate reliability in their supply chains.
Cost management is also a crucial aspect, with procurement teams negotiating competitive prices without compromising on quality.
The integration of digital procurement systems has streamlined operations, enhancing transparency and traceability in the supply chain.
By adopting strategic procurement and purchasing practices, UK glass manufacturers can maintain their market leadership and adapt to evolving industry demands.
Sourcing Raw Materials
Raw materials are the foundation of glass manufacturing, and sourcing them effectively is paramount.
UK manufacturers source high-purity silica sand, ensuring the clarity and strength of the final glass product.
Soda ash and limestone are procured to achieve the desired chemical composition during the glass melting process.
Local sourcing is often favored to reduce transportation costs and support domestic suppliers.
However, global sourcing is also common, allowing access to specialized materials not readily available locally.
Establishing long-term contracts with reliable suppliers enhances supply security and price stability.
Moreover, sourcing from suppliers with sustainable practices aligns with the industry’s environmental objectives.
The challenge lies in balancing cost, quality, and sustainability when selecting suppliers.
By implementing stringent supplier evaluation criteria, manufacturers can ensure the consistent quality of raw materials.
Advantages
Sourcing raw materials domestically offers several advantages.
It reduces lead times and transportation costs, enhancing overall supply chain efficiency.
Local suppliers are often more responsive to changes in demand, allowing for greater flexibility in procurement.
Additionally, supporting domestic suppliers contributes to the local economy and fosters industry collaboration.
Access to high-quality materials ensures that the final glass products meet stringent quality standards.
UK manufacturers benefit from the proximity to suppliers, facilitating better communication and coordination.
This leads to quicker resolution of any supply issues, minimizing production disruptions.
Moreover, domestic sourcing often involves fewer regulatory hurdles, streamlining the procurement process.
Disadvantages
However, relying solely on domestic suppliers can present challenges.
Local markets may have limited capacity to meet high-volume demands, leading to potential supply shortages.
Price volatility can also be a concern, as domestic suppliers may have higher costs compared to international counterparts.
Moreover, the availability of specialized materials might be restricted, necessitating the inclusion of global suppliers.
Global sourcing introduces its own set of complexities, such as longer lead times and increased logistics costs.
Managing a diverse supplier base requires robust procurement strategies and advanced supply chain management systems.
Additionally, geopolitical factors and trade regulations can impact international sourcing, adding uncertainty to the supply chain.
Supplier Negotiation Techniques
Effective supplier negotiation is essential to securing favorable terms and fostering strong partnerships.
UK glass manufacturers employ various negotiation techniques to achieve optimal outcomes.
Building strong relationships with suppliers is foundational, as trust and mutual respect facilitate smoother negotiations.
Open communication about expectations and requirements helps in aligning objectives and addressing potential issues proactively.
Negotiating long-term contracts can secure better pricing and ensure supply continuity.
Volume discounts and flexible payment terms are also key negotiation points that can enhance cost efficiency.
Understanding the supplier’s business and market conditions allows for more informed negotiation strategies.
Additionally, leveraging competitive bids from multiple suppliers can drive favorable pricing and terms.
By adopting a collaborative approach, manufacturers and suppliers can create win-win scenarios that benefit both parties.
Building Strong Relationships
Building strong relationships with suppliers is crucial for long-term success in procurement.
Trust and reliability are the cornerstones of these relationships, ensuring consistent quality and timely deliveries.
Regular communication and engagement help in understanding each other’s capabilities and constraints.
Collaborative partnerships enable joint problem-solving and innovation, leading to improved products and processes.
Investing in supplier development programs can enhance supplier performance and align their capabilities with the manufacturer’s needs.
Recognition and appreciation of suppliers’ efforts foster loyalty and commitment.
Strong relationships also provide manufacturers with greater flexibility during periods of increased demand or supply chain disruptions.
Ultimately, a robust supplier relationship contributes to a more resilient and responsive supply chain.
Negotiating Terms and Conditions
Negotiating favorable terms and conditions is a key aspect of procurement and purchasing in glass manufacturing.
Key elements include pricing, payment terms, delivery schedules, and quality standards.
Manufacturers aim to secure competitive pricing without compromising on material quality.
Flexible payment terms, such as extended credit periods or early payment discounts, can improve cash flow management.
Delivery schedules must align with production timelines to prevent delays and ensure continuous operations.
Quality standards are negotiated to ensure that materials meet the required specifications and regulatory requirements.
Additionally, manufacturers may negotiate clauses related to returns, warranties, and dispute resolution.
Clear and comprehensive contracts help in preventing misunderstandings and resolving conflicts effectively.
By carefully negotiating terms and conditions, manufacturers can achieve greater control over their supply chain and operational costs.
Market Conditions
Understanding market conditions is vital for strategic procurement and purchasing in glass manufacturing.
Market conditions encompass supply and demand dynamics, material price trends, and economic factors affecting the industry.
Fluctuations in raw material prices can impact procurement budgets and overall cost structures.
Manufacturers must stay informed about global supply chain developments, such as changes in tariffs, trade agreements, and geopolitical events.
Technological advancements and industry innovations also influence market conditions, presenting both opportunities and challenges.
Sustainability trends are reshaping procurement strategies, with increasing demand for eco-friendly materials and practices.
Economic indicators, such as GDP growth and manufacturing output, provide insights into market stability and future demand.
By continuously monitoring market conditions, manufacturers can adapt their procurement strategies to mitigate risks and capitalize on opportunities.
Current Trends in the Glass Industry
The glass industry is undergoing significant transformations driven by technological advancements and changing consumer preferences.
One prominent trend is the adoption of smart glass technologies, such as electrochromic and photovoltaic glass, enhancing functionality and energy efficiency.
Manufacturers are investing in automation and digitalization to streamline production processes and improve quality control.
The integration of Industry 4.0 principles, including IoT and data analytics, enables real-time monitoring and optimization of manufacturing operations.
Sustainability is a major focus, with efforts to reduce carbon emissions, increase recycling rates, and develop biodegradable glass alternatives.
Customization and specialization are also gaining traction, with manufacturers catering to niche markets requiring bespoke glass solutions.
Moreover, advancements in glass coating technologies are enhancing the performance and durability of glass products.
These trends necessitate agile procurement strategies that can adapt to evolving market demands and technological innovations.
Impact on Procurement Strategies
Current trends in the glass industry significantly influence procurement strategies.
The rise of smart glass technologies requires sourcing specialized materials and components from technologically advanced suppliers.
Automation and digitalization trends necessitate the procurement of cutting-edge machinery and software solutions.
Manufacturers must prioritize suppliers who can provide high-tech materials and support ongoing innovation efforts.
Sustainability trends compel manufacturers to adopt green procurement practices, sourcing eco-friendly materials and partnering with environmentally responsible suppliers.
Customization and specialization drive the need for flexible and responsive procurement processes to accommodate varying project requirements.
Advancements in glass coatings require procurement teams to stay abreast of the latest material technologies and secure reliable sources for these specialized coatings.
Overall, procurement strategies must be dynamic and forward-thinking to effectively support the industry’s evolving landscape.
Best Practices in Procurement and Purchasing
Implementing best practices in procurement and purchasing is essential for maintaining competitiveness and operational excellence in the UK glass manufacturing industry.
These practices encompass strategic sourcing, supplier management, cost control, and continuous improvement initiatives.
By adhering to best practices, manufacturers can enhance supply chain efficiency, mitigate risks, and drive innovation.
Best practices also support the achievement of sustainability goals and ensure compliance with regulatory standards.
Adopting industry standards and certifications can further bolster procurement processes and supplier credibility.
Moreover, fostering a culture of collaboration and continuous learning within procurement teams promotes adaptability and resilience.
Ultimately, best practices in procurement and purchasing contribute to the overall success and sustainability of glass manufacturing operations.
Leveraging Technology and Automation
Leveraging technology and automation is a cornerstone of modern procurement and purchasing practices in glass manufacturing.
Digital procurement platforms streamline the sourcing process, enabling efficient management of supplier information, orders, and contracts.
Automation tools enhance the accuracy and speed of procurement operations, reducing manual errors and administrative burdens.
Data analytics provide valuable insights into spending patterns, supplier performance, and market trends, informing strategic decision-making.
Integrating IoT devices into the supply chain allows for real-time tracking of materials and inventory levels, improving supply chain visibility.
Artificial intelligence and machine learning algorithms can predict demand fluctuations and optimize inventory management.
Blockchain technology offers enhanced security and transparency in transactions, ensuring data integrity and traceability.
By embracing these technologies, manufacturers can achieve greater efficiency, reduce costs, and enhance the overall effectiveness of their procurement processes.
Ensuring Quality Control
Quality control is paramount in procurement and purchasing, particularly in the high-precision glass manufacturing industry.
Establishing stringent quality standards for suppliers ensures that the raw materials and components meet the required specifications.
Regular supplier audits and assessments help in monitoring adherence to quality protocols and identifying areas for improvement.
Collaborating with suppliers on quality initiatives fosters a shared commitment to excellence and continuous improvement.
Implementing quality management systems, such as ISO certifications, provides a structured approach to maintaining quality standards.
Utilizing advanced quality assurance technologies, such as automated inspection systems, enhances the accuracy and reliability of quality control processes.
Training procurement teams on quality control principles and practices ensures a consistent focus on quality throughout the supply chain.
By prioritizing quality in procurement and purchasing, manufacturers can uphold the integrity of their glass products and meet customer expectations.
Risk Management
Effective risk management is critical in procurement and purchasing to safeguard the supply chain against disruptions and uncertainties.
Identifying potential risks, such as supplier insolvency, geopolitical instability, and natural disasters, allows manufacturers to develop proactive mitigation strategies.
Diversifying the supplier base reduces dependency on a single source and enhances supply chain resilience.
Implementing contingency plans, such as alternative sourcing options and safety stock policies, ensures continuity of operations during unforeseen events.
Regularly assessing and monitoring supplier performance provides early warning signs of potential risks, enabling timely interventions.
Building strong relationships with suppliers facilitates better communication and collaboration during crises, enhancing the ability to navigate challenges collectively.
Incorporating risk management practices into procurement processes fosters a more robust and adaptable supply chain.
By proactively addressing risks, manufacturers can minimize disruptions and maintain steady production flows.
Innovations in Glass Processing
Innovation is a driving force behind the UK’s leadership in glass processing manufacturing.
British manufacturers are at the forefront of developing cutting-edge technologies and processes that enhance glass performance and functionality.
Advancements in glass coating technologies, such as low-emissivity and self-cleaning coatings, improve energy efficiency and maintenance.
Smart glass innovations, including electrochromic and switchable glass, offer dynamic control over light transmission and privacy.
Additive manufacturing techniques, such as 3D printing of glass components, enable the creation of intricate and customized designs.
Nanotechnology is being leveraged to enhance the strength, durability, and thermal properties of glass products.
Automation and robotics streamline production processes, increasing precision and reducing labor costs.
Digital twins and simulation tools allow for the optimization of glass manufacturing processes, enhancing efficiency and reducing waste.
These innovations not only improve product quality but also open new market opportunities and applications for glass products.
Advantages of the UK’s Approach
The UK’s approach to glass manufacturing offers several advantages that contribute to its global leadership.
Emphasis on innovation ensures that British manufacturers continuously develop advanced products and processes.
Strategic procurement and purchasing practices enable the efficient sourcing of high-quality materials and components.
Strong supplier relationships foster collaboration and reliability, essential for maintaining production continuity.
Investment in technology and automation enhances operational efficiency and product precision.
Commitment to sustainability aligns with global environmental standards and meets the increasing demand for eco-friendly products.
Skilled workforce and expertise in glass engineering drive excellence in manufacturing and quality control.
Supportive government policies and industry incentives facilitate growth and competitiveness in the international market.
The integration of these elements creates a robust and dynamic manufacturing ecosystem that sustains the UK’s prominence in glass processing.
Challenges and Disadvantages
Despite its strengths, the UK glass manufacturing industry faces several challenges and disadvantages.
High operational costs, including labor and energy expenses, can impact profitability and competitiveness.
Access to specialized raw materials may be limited, necessitating reliance on international suppliers and exposing the supply chain to global risks.
Brexit-related trade barriers have increased the complexity of importing and exporting glass products, affecting supply chain efficiency.
Fluctuations in raw material prices can lead to cost unpredictability and impact budget planning.
Intense global competition pressures UK manufacturers to continuously innovate and reduce costs to maintain market share.
Talent acquisition and retention in specialized glass engineering roles remain challenging, potentially hindering innovation and growth.
Regulatory compliance, particularly regarding environmental standards, requires ongoing investment and adaptation.
Addressing these challenges requires strategic planning, investment in technology, and fostering a resilient and adaptable supply chain.
High Operational Costs
High operational costs are a significant challenge for UK glass manufacturers.
Energy-intensive processes, such as glass melting and shaping, contribute to substantial electricity and fuel expenses.
Labor costs in the UK are relatively high compared to some other manufacturing hubs, impacting overall production costs.
Maintaining state-of-the-art equipment and investing in technological upgrades require considerable capital expenditures.
Additionally, complying with stringent environmental and safety regulations necessitates ongoing investment in sustainable practices and equipment.
These high operational costs can erode profit margins and limit the ability to competitively price products in the global market.
Manufacturers must seek ways to optimize energy usage, improve operational efficiency, and explore cost-effective procurement strategies to mitigate these challenges.
Supply Chain Complexity
The UK’s glass manufacturing supply chain is complex, involving multiple tiers of suppliers and a variety of materials and components.
Managing this complexity requires robust supply chain management systems and effective coordination among various stakeholders.
Global sourcing introduces challenges such as longer lead times, increased logistics costs, and exposure to geopolitical risks.
Transporting raw materials and finished products across international borders can be affected by customs delays, trade restrictions, and fluctuating exchange rates.
Supply chain disruptions, such as natural disasters or political instability in supplier regions, can have significant impacts on production timelines and costs.
Ensuring visibility and traceability throughout the supply chain is critical for managing risks and maintaining quality standards.
The complexity of the supply chain necessitates comprehensive risk management and agile procurement strategies to respond to unforeseen challenges effectively.
Brexit Impact
Brexit has introduced significant changes to the UK’s trade landscape, affecting the glass manufacturing industry in multiple ways.
The reintroduction of customs checks and tariffs on goods traded between the UK and the European Union has increased the complexity and cost of importing raw materials and exporting finished products.
Regulatory divergences between the UK and EU have created additional compliance requirements, necessitating updates to processes and documentation.
Supply chain disruptions have become more common, with delays in cross-border transportation impacting production schedules.
The uncertainty surrounding post-Brexit trade agreements has complicated long-term procurement planning and supplier relationships.
Manufacturers must navigate these changes by adapting their supply chains, exploring new markets, and renegotiating terms with suppliers to mitigate the impact of Brexit-related challenges.
The ongoing adjustments require strategic agility and proactive management to sustain competitiveness in the new trade environment.
Conclusion
The UK’s leadership in innovative glass processing manufacturing is a testament to its strategic procurement and purchasing practices.
By effectively sourcing high-quality materials, nurturing strong supplier relationships, and embracing technological advancements, British manufacturers maintain their competitive edge in the global market.
Despite facing challenges such as high operational costs, supply chain complexity, and Brexit-related disruptions, the industry’s resilience and commitment to excellence drive continued success.
Emphasizing sustainability and continuous innovation ensures that the UK glass manufacturing sector remains at the forefront of industry developments.
Adopting best practices in procurement and purchasing not only enhances operational efficiency but also supports long-term growth and adaptability.
As the global demand for advanced and sustainable glass products grows, the UK’s glass manufacturing industry is well-positioned to capitalize on emerging opportunities and sustain its leadership role.
Continued investment in technology, talent, and strategic partnerships will further solidify the UK’s status as a master of glass manufacturing, delivering superior products and driving industry innovation forward.
資料ダウンロード
QCD管理受発注クラウド「newji」は、受発注部門で必要なQCD管理全てを備えた、現場特化型兼クラウド型の今世紀最高の受発注管理システムとなります。
ユーザー登録
受発注業務の効率化だけでなく、システムを導入することで、コスト削減や製品・資材のステータス可視化のほか、属人化していた受発注情報の共有化による内部不正防止や統制にも役立ちます。
NEWJI DX
製造業に特化したデジタルトランスフォーメーション(DX)の実現を目指す請負開発型のコンサルティングサービスです。AI、iPaaS、および先端の技術を駆使して、製造プロセスの効率化、業務効率化、チームワーク強化、コスト削減、品質向上を実現します。このサービスは、製造業の課題を深く理解し、それに対する最適なデジタルソリューションを提供することで、企業が持続的な成長とイノベーションを達成できるようサポートします。
製造業ニュース解説
製造業、主に購買・調達部門にお勤めの方々に向けた情報を配信しております。
新任の方やベテランの方、管理職を対象とした幅広いコンテンツをご用意しております。
お問い合わせ
コストダウンが利益に直結する術だと理解していても、なかなか前に進めることができない状況。そんな時は、newjiのコストダウン自動化機能で大きく利益貢献しよう!
(β版非公開)