- お役立ち記事
- Unveiling Japanese Manufacturing: Lessons from Development Defects and Rework Examples
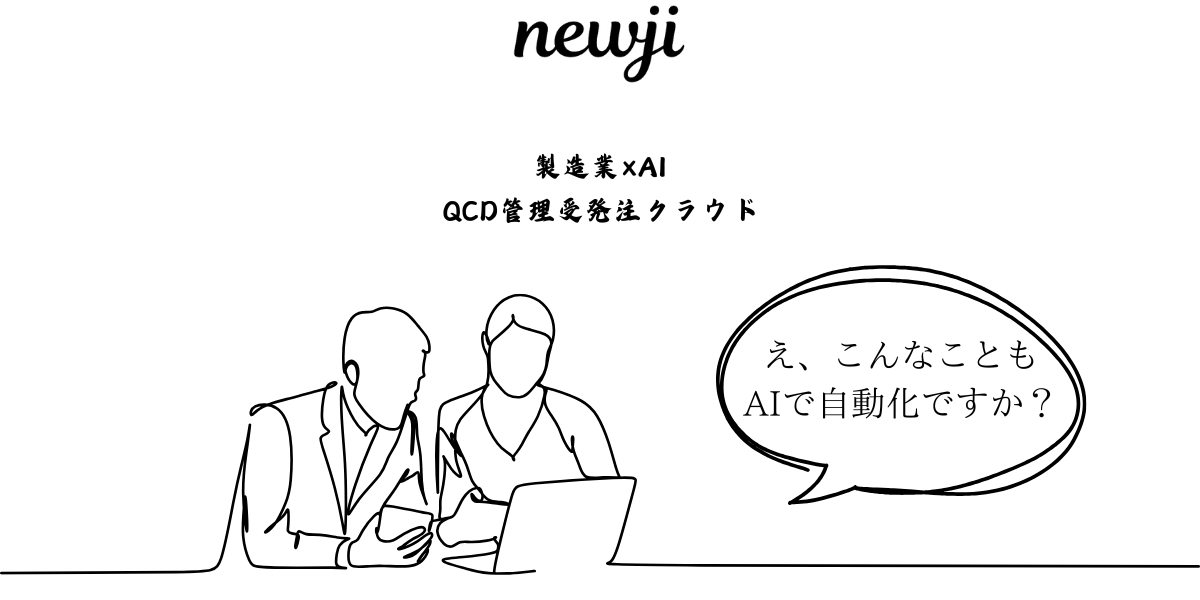
Unveiling Japanese Manufacturing: Lessons from Development Defects and Rework Examples
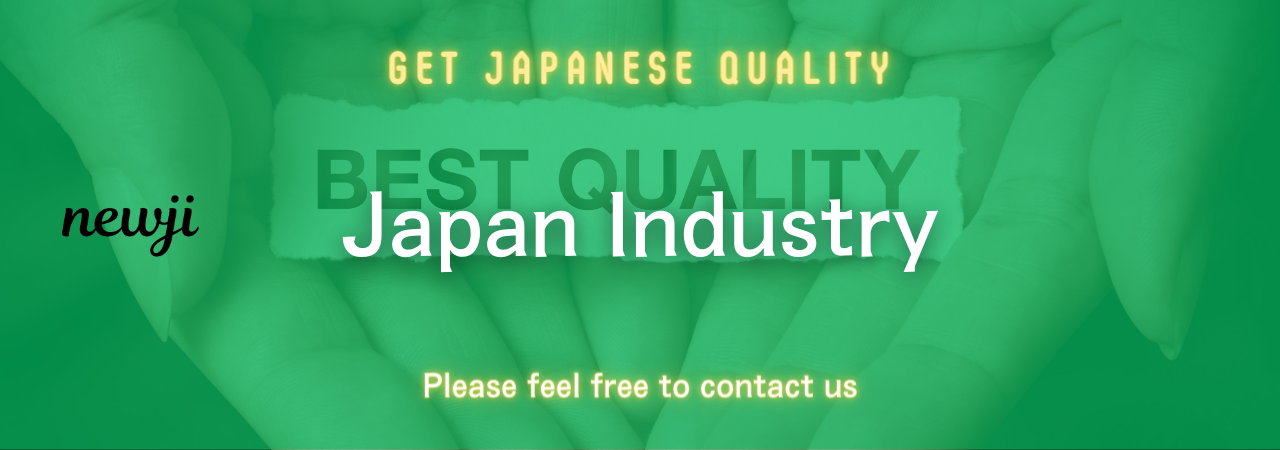
目次
Introduction
Japanese manufacturing has long been revered for its quality, efficiency, and innovation. Companies around the world seek to emulate the success of Japanese manufacturers, particularly in sectors such as automotive, electronics, and machinery. However, achieving similar excellence requires a deep understanding of the challenges and best practices associated with Japanese procurement and purchasing. This article delves into the intricacies of Japanese manufacturing by examining development defects and rework examples, offering valuable lessons for international procurement professionals.
Understanding Development Defects in Japanese Manufacturing
Development defects are issues that arise during the design and development phase of a product, leading to potential flaws in the final output. In Japanese manufacturing, addressing these defects is crucial to maintaining high standards of quality and reliability.
Root Cause Analysis
Japanese manufacturers emphasize the importance of identifying the root causes of development defects. This approach involves systematic analysis to trace defects back to their origin, whether they stem from design flaws, material issues, or process inefficiencies. Techniques such as the “5 Whys” and fishbone diagrams are commonly used to facilitate this analysis.
Continuous Improvement (Kaizen)
The Kaizen philosophy underpins the Japanese approach to mitigating development defects. By fostering a culture of continuous improvement, manufacturers encourage employees at all levels to identify and implement changes that enhance product quality and process efficiency. This proactive mindset helps prevent defects from recurring and promotes long-term operational excellence.
Integration of Quality Control Systems
Japanese manufacturers integrate comprehensive quality control systems into their development processes. These systems include rigorous testing, quality assurance protocols, and standardized procedures that ensure defects are identified and addressed promptly. Tools such as Six Sigma and Total Quality Management (TQM) are often employed to maintain high quality standards.
Common Rework Examples and Their Implications
Rework refers to the process of correcting defects or deficiencies in a product after its initial production. In Japanese manufacturing, minimizing rework is essential for maintaining efficiency and cost-effectiveness.
Assembly Line Rework
One common area where rework occurs is the assembly line. Defects such as misalignment of components, improper fastening, or incomplete assembly can necessitate rework. Japanese manufacturers address these issues through precise assembly instructions, training programs, and automation technologies that reduce human error.
Material Deficiencies
Rework can also result from material deficiencies, such as substandard raw materials or incorrect specifications. To mitigate this, Japanese manufacturers maintain stringent supplier selection criteria and perform thorough material inspections to ensure compliance with quality standards.
Design Flaws
Design flaws discovered during production can lead to significant rework requirements. Japanese manufacturers employ cross-functional teams that include design engineers, production managers, and quality control specialists to collaboratively identify and rectify design issues before they escalate into costly rework scenarios.
Implications of Rework
Rework has several implications for manufacturing operations, including increased production costs, extended lead times, and reduced overall efficiency. By proactively addressing the root causes of rework, Japanese manufacturers can minimize its impact and maintain their competitive edge in the global market.
Advantages of Japanese Manufacturing Practices
Japanese manufacturing practices offer numerous advantages that contribute to their global reputation for quality and reliability.
Lean Manufacturing
Lean manufacturing focuses on eliminating waste and optimizing processes to enhance efficiency. Japanese manufacturers have perfected lean principles, leading to streamlined operations, reduced costs, and improved product quality.
Supplier Relationships
Strong, collaborative relationships with suppliers are a hallmark of Japanese manufacturing. By fostering trust and open communication, Japanese companies ensure that suppliers adhere to quality standards and contribute to continuous improvement initiatives.
Advanced Technology and Automation
Japanese manufacturers invest heavily in advanced technologies and automation to enhance production capabilities. These investments lead to higher precision, consistency, and scalability in manufacturing processes.
Employee Training and Development
A well-trained workforce is crucial to the success of Japanese manufacturing. Companies prioritize employee training and development, ensuring that workers possess the skills and knowledge required to maintain high standards of quality and efficiency.
Challenges and Disadvantages in Japanese Manufacturing
While Japanese manufacturing practices offer significant advantages, they are not without challenges and potential disadvantages.
High Initial Investment
Implementing advanced technologies and establishing comprehensive quality control systems require substantial initial investment. This can be a barrier for smaller companies or those with limited financial resources.
Cultural Barriers
Cultural differences can pose challenges in international procurement and purchasing. Understanding and adapting to Japanese business etiquette, communication styles, and decision-making processes is essential for successful collaboration.
Rigidity in Processes
The emphasis on standardized procedures and meticulous planning can lead to rigidity, making it difficult to adapt quickly to changing market conditions or unexpected disruptions.
Supply Chain Dependence
Japanese manufacturers often rely on tightly controlled supply chains. While this ensures quality, it can also lead to vulnerabilities if key suppliers experience disruptions or fail to meet expectations.
Effective Supplier Negotiation Techniques with Japanese Manufacturers
Negotiating with Japanese suppliers requires a nuanced approach that respects cultural norms and fosters collaborative relationships.
Building Trust and Rapport
Establishing trust is fundamental in Japanese business culture. Taking time to build personal relationships through face-to-face meetings, social interactions, and consistent communication can facilitate smoother negotiations.
Understanding Cultural Norms
Familiarity with Japanese cultural practices, such as hierarchy, indirect communication, and consensus-driven decision-making, can enhance negotiation effectiveness. Demonstrating respect for these norms is crucial for successful outcomes.
Emphasizing Long-Term Partnerships
Japanese manufacturers value long-term relationships over short-term gains. Highlighting the potential for sustained collaboration and mutual benefits can strengthen negotiation leverage.
Clear and Detailed Proposals
Providing clear, detailed, and well-structured proposals helps convey professionalism and credibility. Including comprehensive information about requirements, expectations, and objectives reduces misunderstandings and builds confidence in the partnership.
Flexibility and Patience
Negotiations with Japanese suppliers may take longer due to the emphasis on thorough deliberation and consensus. Demonstrating patience and flexibility can facilitate a more amicable and productive negotiation process.
Market Conditions Affecting Japanese Procurement
Understanding the broader market conditions is essential for effective procurement from Japanese manufacturers.
Economic Factors
Economic stability, exchange rates, and inflation rates influence procurement strategies. Fluctuations in the Japanese yen can impact the cost of goods and overall procurement budgets.
Technological Advancements
Rapid advancements in technology drive continuous innovation in Japanese manufacturing. Staying abreast of these developments ensures that procurement strategies align with the latest industry standards and technological capabilities.
Global Trade Policies
Trade policies, tariffs, and international trade agreements can affect procurement operations. Understanding the implications of these policies on cross-border transactions and supply chain dynamics is critical for strategic planning.
Competitive Landscape
The competitive landscape within Japanese manufacturing influences procurement decisions. Assessing the strengths and weaknesses of Japanese suppliers relative to competitors can inform supplier selection and negotiation strategies.
Sustainability and Regulatory Compliance
Increasing emphasis on sustainability and regulatory compliance affects procurement practices. Japanese manufacturers are increasingly adopting environmentally friendly processes and adhering to stringent regulatory standards, which can influence procurement requirements and partnerships.
Best Practices for Engaging with Japanese Suppliers
Adopting best practices can enhance the effectiveness and efficiency of procurement and purchasing operations when dealing with Japanese manufacturers.
Comprehensive Supplier Evaluation
Conducting thorough evaluations of potential suppliers ensures alignment with quality standards, operational capabilities, and strategic objectives. This includes assessing financial stability, production capacity, and past performance.
Clear Communication Channels
Establishing clear and open communication channels facilitates effective information exchange, issue resolution, and collaboration. Utilizing multiple communication methods, such as email, video conferencing, and in-person meetings, can enhance connectivity.
Collaborative Planning and Forecasting
Engaging in collaborative planning and forecasting with Japanese suppliers ensures alignment of production schedules, inventory levels, and demand forecasts. This collaboration minimizes supply chain disruptions and optimizes inventory management.
Joint Continuous Improvement Initiatives
Partnering with suppliers on continuous improvement initiatives fosters mutual growth and operational excellence. Implementing joint Kaizen projects or Six Sigma programs can drive shared advancements in quality and efficiency.
Performance Monitoring and Feedback
Regularly monitoring supplier performance and providing constructive feedback promotes accountability and continuous improvement. Key performance indicators (KPIs) such as on-time delivery, defect rates, and responsiveness should be established and tracked.
Risk Management Strategies
Developing robust risk management strategies mitigates potential disruptions in the supply chain. This includes diversification of suppliers, maintaining safety stock levels, and establishing contingency plans for unforeseen events.
Case Studies: Successful Procurement from Japanese Manufacturers
Examining real-world examples of successful procurement from Japanese manufacturers can provide valuable insights and practical lessons.
Automotive Industry Collaboration
A major automotive company partnered with a Japanese supplier to enhance the quality of engine components. Through joint Kaizen initiatives and regular performance reviews, the supplier improved defect rates by 30%, resulting in significant cost savings and increased customer satisfaction.
Electronics Sector Innovation
An electronics manufacturer collaborated with a Japanese supplier to develop advanced assembly technologies. By investing in shared research and development, both companies achieved breakthroughs in automation, reducing production time and enhancing product reliability.
Aerospace Supply Chain Optimization
A global aerospace firm engaged a Japanese supplier to streamline its supply chain processes. Implementing lean manufacturing principles and adopting synchronized production schedules led to a 25% increase in operational efficiency and a reduction in lead times.
Medical Equipment Quality Assurance
A medical device company worked closely with a Japanese supplier to establish stringent quality control protocols. Through comprehensive training programs and regular audits, the supplier achieved compliance with international quality standards, ensuring the safety and efficacy of medical products.
Conclusion
Japanese manufacturing exemplifies a commitment to quality, efficiency, and continuous improvement. By understanding the challenges associated with development defects and rework, procurement and purchasing professionals can glean valuable lessons that enhance their own operations. Effective supplier negotiation techniques, awareness of market conditions, and the adoption of best practices are critical for successful engagement with Japanese suppliers. Case studies demonstrate that collaboration and mutual investment in improvement initiatives can lead to significant benefits, including cost savings, enhanced product quality, and increased operational efficiency. Embracing the principles and strategies inherent in Japanese manufacturing can empower international companies to achieve excellence in their procurement and purchasing endeavors.
資料ダウンロード
QCD調達購買管理クラウド「newji」は、調達購買部門で必要なQCD管理全てを備えた、現場特化型兼クラウド型の今世紀最高の購買管理システムとなります。
ユーザー登録
調達購買業務の効率化だけでなく、システムを導入することで、コスト削減や製品・資材のステータス可視化のほか、属人化していた購買情報の共有化による内部不正防止や統制にも役立ちます。
NEWJI DX
製造業に特化したデジタルトランスフォーメーション(DX)の実現を目指す請負開発型のコンサルティングサービスです。AI、iPaaS、および先端の技術を駆使して、製造プロセスの効率化、業務効率化、チームワーク強化、コスト削減、品質向上を実現します。このサービスは、製造業の課題を深く理解し、それに対する最適なデジタルソリューションを提供することで、企業が持続的な成長とイノベーションを達成できるようサポートします。
オンライン講座
製造業、主に購買・調達部門にお勤めの方々に向けた情報を配信しております。
新任の方やベテランの方、管理職を対象とした幅広いコンテンツをご用意しております。
お問い合わせ
コストダウンが利益に直結する術だと理解していても、なかなか前に進めることができない状況。そんな時は、newjiのコストダウン自動化機能で大きく利益貢献しよう!
(Β版非公開)