- お役立ち記事
- Unveiling Japanese Precision: The Craftsmanship Behind OEM Battery Chargers
月間76,176名の
製造業ご担当者様が閲覧しています*
*2025年3月31日現在のGoogle Analyticsのデータより
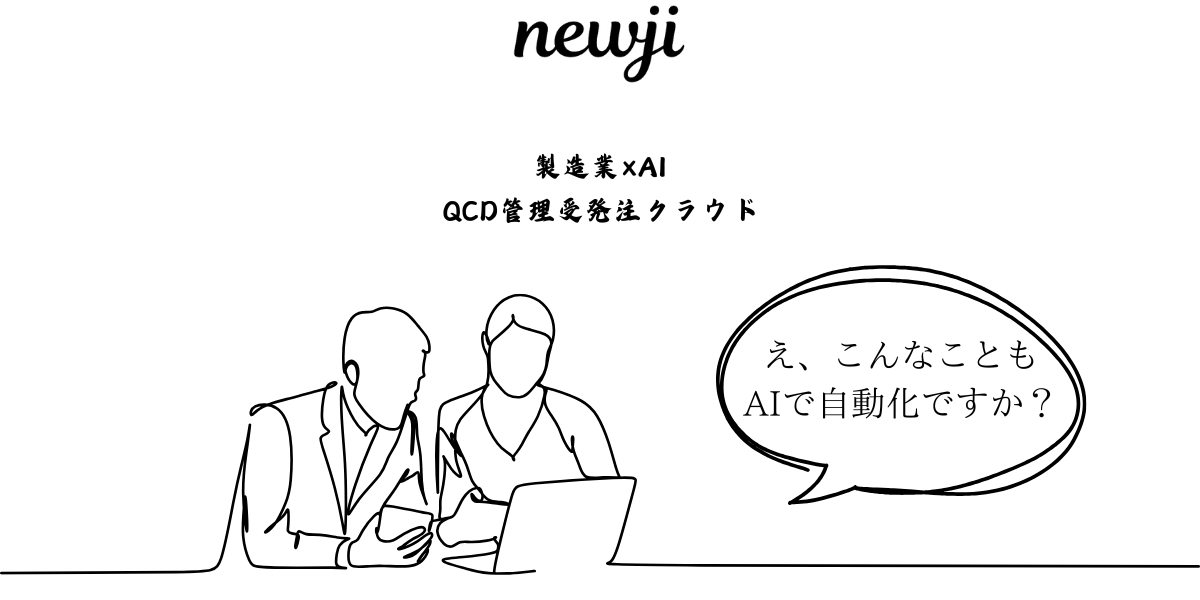
Unveiling Japanese Precision: The Craftsmanship Behind OEM Battery Chargers
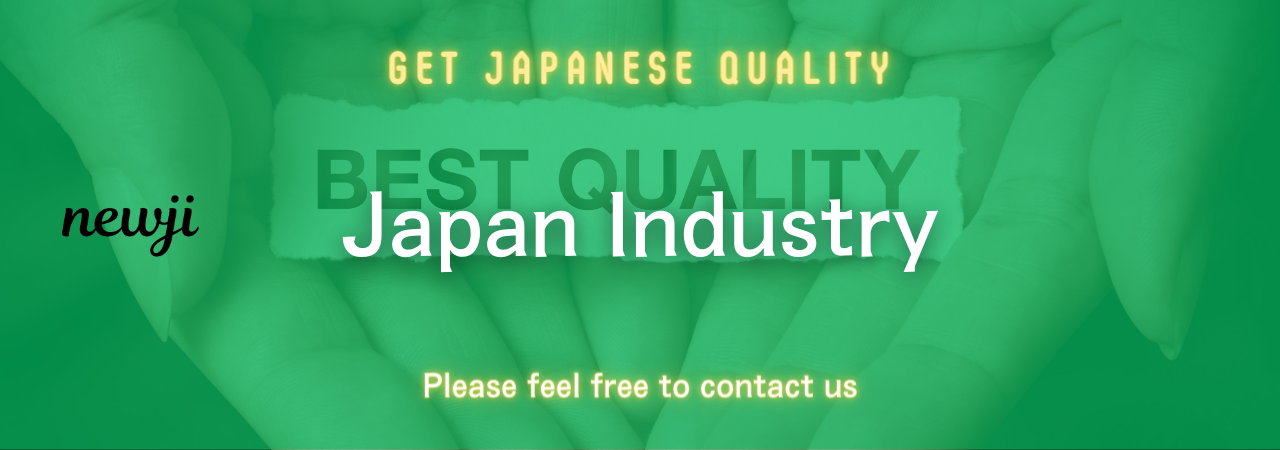
目次
Introduction to Japanese OEM Battery Charger Craftsmanship
Japanese manufacturing is renowned globally for its precision and quality. This reputation is particularly evident in the field of Original Equipment Manufacturer (OEM) battery chargers. These chargers are pivotal components in a wide range of devices, from consumer electronics to industrial machinery. Understanding the craftsmanship behind these products provides valuable insights into the strengths and complexities of Japanese procurement and manufacturing processes.
Japanese OEM battery chargers are not just about powering devices. They embody a blend of advanced technology, meticulous engineering, and efficient manufacturing practices. The dedication to excellence in every step, from design to production, ensures that these chargers meet the highest standards of performance and reliability.
Advantages of Partnering with Japanese Suppliers
Collaborating with Japanese suppliers for OEM battery chargers offers numerous advantages that can significantly benefit manufacturing companies.
Superior Quality Control
One of the standout features of Japanese manufacturing is its rigorous quality control systems. Suppliers adhere to strict standards, ensuring that every battery charger produced meets the required specifications. This commitment to quality minimizes defects and enhances the longevity and performance of the final product.
Advanced Technology and Innovation
Japanese suppliers are at the forefront of technological advancements in battery charging solutions. They invest heavily in research and development, resulting in innovative features such as faster charging times, improved energy efficiency, and enhanced safety mechanisms. This technological edge allows manufacturers to offer cutting-edge products to their customers.
Reliability and Consistency
Japanese manufacturers are known for their reliability and consistency in production. They ensure timely delivery and maintain steady production rates to meet demand. This reliability is crucial for manufacturers who depend on consistent supply chains to maintain their operations and meet market demands.
Strong Supplier Relationships
Japanese business culture emphasizes long-term relationships and trust. Suppliers are committed to building strong partnerships with their clients, providing personalized service, and being responsive to their needs. This approach fosters collaborative relationships that can lead to mutual growth and success.
Disadvantages of Sourcing from Japanese Suppliers
While there are significant benefits to partnering with Japanese suppliers, there are also challenges that manufacturers may face.
Higher Costs
Japanese OEM battery chargers often come at a premium price compared to those from other regions. The higher cost is a reflection of the superior quality, advanced technology, and meticulous manufacturing processes. Manufacturers need to balance these costs with the value provided to ensure profitability.
Longer Lead Times
Shipping products from Japan can result in longer lead times, especially for international orders. Delays in shipping can affect production schedules and inventory management. Manufacturers need to plan accordingly to mitigate the impact of extended lead times on their operations.
Cultural and Language Barriers
Working with Japanese suppliers may involve navigating cultural and language differences. Effective communication is essential for successful collaboration, and misunderstandings can arise if not properly managed. Manufacturers may need to invest in language support or cultural training to enhance communication with their Japanese partners.
Complex Import Regulations
Importing products from Japan involves navigating various regulations and compliance requirements. Manufacturers must ensure that the OEM battery chargers meet the necessary standards and certifications for their target markets. This can add complexity and require additional resources in the procurement process.
Supplier Negotiation Techniques
Successful negotiation with Japanese suppliers is key to securing favorable terms and building strong partnerships. Here are some effective techniques:
Building Trust and Rapport
Japanese business culture places a high value on trust and relationship-building. Investing time in establishing trust and rapport with suppliers can lead to more favorable negotiations. Regular communication, respect for cultural norms, and showing genuine interest in the partnership contribute to a strong foundation.
Understanding Their Needs
Successful negotiations require understanding the supplier’s needs and constraints. By identifying what is important to the supplier, manufacturers can find mutually beneficial solutions. This approach fosters collaboration and can lead to more flexible and accommodating terms.
Long-Term Partnership Focus
Japanese suppliers often prefer long-term relationships over one-time transactions. Emphasizing a commitment to a long-term partnership can make suppliers more willing to offer better terms. Demonstrating plans for sustained collaboration can enhance the negotiation process.
Flexibility and Patience
Patience and flexibility are essential when negotiating with Japanese suppliers. Decisions may take longer as they require consensus and careful consideration. Being patient and flexible with timelines and terms can lead to more successful outcomes.
Market Conditions and Trends
Understanding the current market conditions and trends is crucial for effective procurement and purchasing from Japanese suppliers.
Increasing Demand for Sustainable Solutions
There is a growing demand for sustainable and energy-efficient battery chargers. Japanese manufacturers are responding by developing eco-friendly solutions that reduce energy consumption and use sustainable materials. Staying informed about these trends allows manufacturers to align their offerings with market expectations.
Technological Advancements
The rapid pace of technological advancements in battery technology influences the design and functionality of OEM battery chargers. Features such as wireless charging, smart connectivity, and enhanced safety features are becoming standard. Manufacturers must keep abreast of these advancements to ensure their products remain competitive.
Global Supply Chain Dynamics
Global supply chain disruptions, such as those caused by geopolitical tensions or natural disasters, can impact the availability of OEM battery chargers. Manufacturers need to develop strategies to mitigate these risks, such as diversifying their supplier base or increasing inventory levels to buffer against potential disruptions.
Regulatory Changes
Changes in regulations related to electrical safety, environmental standards, and import/export laws can affect the procurement of OEM battery chargers. Manufacturers must stay informed about relevant regulations to ensure compliance and avoid potential legal issues.
Best Practices in Procurement and Purchasing
Implementing best practices in procurement and purchasing can enhance the efficiency and effectiveness of working with Japanese suppliers for OEM battery chargers.
Comprehensive Supplier Evaluation
Conducting thorough evaluations of potential suppliers is essential. Criteria should include quality standards, technological capabilities, track record, financial stability, and compliance with regulations. A detailed assessment ensures that only reliable and capable suppliers are selected.
Clear Communication of Requirements
Clearly articulating product specifications, quality standards, and delivery expectations is crucial. Providing detailed documentation and maintaining open lines of communication helps prevent misunderstandings and ensures that suppliers can meet the manufacturer’s needs effectively.
Establishing Robust Contracts
Developing clear and comprehensive contracts that outline terms and conditions, delivery schedules, quality standards, and payment terms is vital. Contracts should also include provisions for handling disputes and addressing potential issues that may arise during the partnership.
Implementing Quality Assurance Processes
Integrating quality assurance processes, such as regular inspections and testing, ensures that OEM battery chargers meet the required standards. Collaborating with suppliers to implement quality control measures can lead to continuous improvement and higher product standards.
Leveraging Technology for Supply Chain Management
Utilizing technology, such as procurement software and supply chain management tools, can streamline the procurement process. These tools enhance visibility, improve communication, and facilitate better decision-making by providing real-time data and analytics.
Continuous Improvement and Feedback
Establishing a system for continuous improvement and regular feedback with suppliers fosters a culture of excellence. Sharing performance metrics, discussing challenges, and collaboratively developing solutions can lead to ongoing enhancements in product quality and supplier performance.
Quality Control in Japanese OEM Battery Charger Production
Quality control is a cornerstone of Japanese manufacturing excellence, particularly in the production of OEM battery chargers.
Lean Manufacturing Practices
Japanese manufacturers often employ lean manufacturing techniques to minimize waste and maximize efficiency. This approach ensures that production processes are streamlined, reducing costs and enhancing product quality. Implementing lean practices can lead to more consistent and reliable outputs.
Six Sigma Methodology
The Six Sigma methodology is commonly used to improve quality by identifying and eliminating defects. By using data-driven approaches and statistical analysis, Japanese manufacturers can achieve high levels of precision and consistency in their OEM battery chargers.
Total Quality Management (TQM)
Total Quality Management is a holistic approach that involves all members of an organization in improving processes, products, and services. TQM fosters a culture of continuous improvement and accountability, ensuring that quality is maintained at every stage of production.
Supplier Quality Assurance
Japanese suppliers often implement stringent quality assurance measures not only within their facilities but also across their supplier networks. This comprehensive approach ensures that all components and materials used in OEM battery chargers meet the highest quality standards.
Logistics and Supply Chain Efficiency
Efficient logistics and supply chain management are critical for the successful procurement of OEM battery chargers from Japan.
Optimized Inventory Management
Effective inventory management strategies, such as Just-In-Time (JIT) inventory, help minimize holding costs and reduce the risk of overstocking or stockouts. Japanese suppliers are adept at managing inventories to ensure timely delivery without excess.
Advanced Logistics Solutions
Utilizing advanced logistics solutions, including automated warehousing and real-time tracking systems, enhances the efficiency of the supply chain. These technologies provide greater visibility and control over the movement of OEM battery chargers from Japan to their final destination.
Risk Management Strategies
Implementing robust risk management strategies helps mitigate potential disruptions in the supply chain. This includes diversifying suppliers, establishing contingency plans, and regularly assessing and addressing vulnerabilities within the supply chain.
Collaboration with Logistics Partners
Working closely with reliable logistics partners ensures that OEM battery chargers are transported efficiently and safely. Collaborative relationships with logistics providers can lead to better service levels and more responsive supply chain operations.
Production Management and Engineering Excellence
Effective production management and engineering are essential for maintaining the high standards of Japanese OEM battery chargers.
Precision Engineering
Japanese engineering is known for its precision and attention to detail. In the production of OEM battery chargers, precise engineering ensures that each component functions correctly and integrates seamlessly, resulting in high-performance products.
Automation and Factory Efficiency
Automation plays a significant role in Japanese manufacturing, enhancing factory efficiency and reducing the potential for human error. Automated production lines and robotics contribute to consistent quality and increased production capacity.
Continuous Improvement (Kaizen)
The principle of Kaizen, or continuous improvement, is integral to Japanese production management. By constantly seeking ways to enhance processes and eliminate inefficiencies, manufacturers can achieve higher levels of productivity and product quality.
Lean Production Techniques
Implementing lean production techniques helps reduce waste, streamline operations, and optimize resource utilization. These techniques contribute to more efficient manufacturing processes and better overall factory performance.
Strategic Procurement and Purchasing Practices
Strategic procurement and purchasing are crucial for leveraging the benefits of Japanese OEM battery chargers while mitigating potential challenges.
Cost-Benefit Analysis
Conducting a thorough cost-benefit analysis helps manufacturers evaluate the financial implications of sourcing from Japanese suppliers. This analysis should consider not only the initial costs but also long-term benefits such as product quality, reliability, and supplier support.
Supplier Diversification
To reduce dependency on a single supplier and mitigate risks, manufacturers should consider diversifying their supplier base. Partnering with multiple Japanese suppliers or incorporating suppliers from other regions can enhance supply chain resilience.
Negotiating Favorable Payment Terms
Negotiating favorable payment terms, such as extended payment periods or flexible financing options, can improve cash flow management. Clear understanding of payment expectations and negotiating terms that align with the manufacturer’s financial strategy are essential.
Collaborative Product Development
Engaging in collaborative product development with Japanese suppliers can lead to innovative solutions and improved product performance. Sharing insights and working together on design and engineering can result in OEM battery chargers that better meet market needs.
Conclusion: Leveraging Japanese Precision for Competitive Advantage
Partnering with Japanese suppliers for OEM battery chargers offers significant advantages in terms of quality, technology, and reliability. While there are challenges such as higher costs and longer lead times, the benefits often outweigh the drawbacks for manufacturers committed to excellence.
By employing effective supplier negotiation techniques, understanding market conditions, and implementing best practices in procurement and purchasing, manufacturers can harness the craftsmanship of Japanese OEM battery chargers to enhance their product offerings and gain a competitive edge in the global market. Embracing the precision and dedication inherent in Japanese manufacturing can lead to sustained success and long-term growth for manufacturing companies worldwide.
資料ダウンロード
QCD管理受発注クラウド「newji」は、受発注部門で必要なQCD管理全てを備えた、現場特化型兼クラウド型の今世紀最高の受発注管理システムとなります。
ユーザー登録
受発注業務の効率化だけでなく、システムを導入することで、コスト削減や製品・資材のステータス可視化のほか、属人化していた受発注情報の共有化による内部不正防止や統制にも役立ちます。
NEWJI DX
製造業に特化したデジタルトランスフォーメーション(DX)の実現を目指す請負開発型のコンサルティングサービスです。AI、iPaaS、および先端の技術を駆使して、製造プロセスの効率化、業務効率化、チームワーク強化、コスト削減、品質向上を実現します。このサービスは、製造業の課題を深く理解し、それに対する最適なデジタルソリューションを提供することで、企業が持続的な成長とイノベーションを達成できるようサポートします。
製造業ニュース解説
製造業、主に購買・調達部門にお勤めの方々に向けた情報を配信しております。
新任の方やベテランの方、管理職を対象とした幅広いコンテンツをご用意しております。
お問い合わせ
コストダウンが利益に直結する術だと理解していても、なかなか前に進めることができない状況。そんな時は、newjiのコストダウン自動化機能で大きく利益貢献しよう!
(β版非公開)