- お役立ち記事
- Unveiling Japan’s Mastery in Crafting OEM Accessory Cables for Global Markets
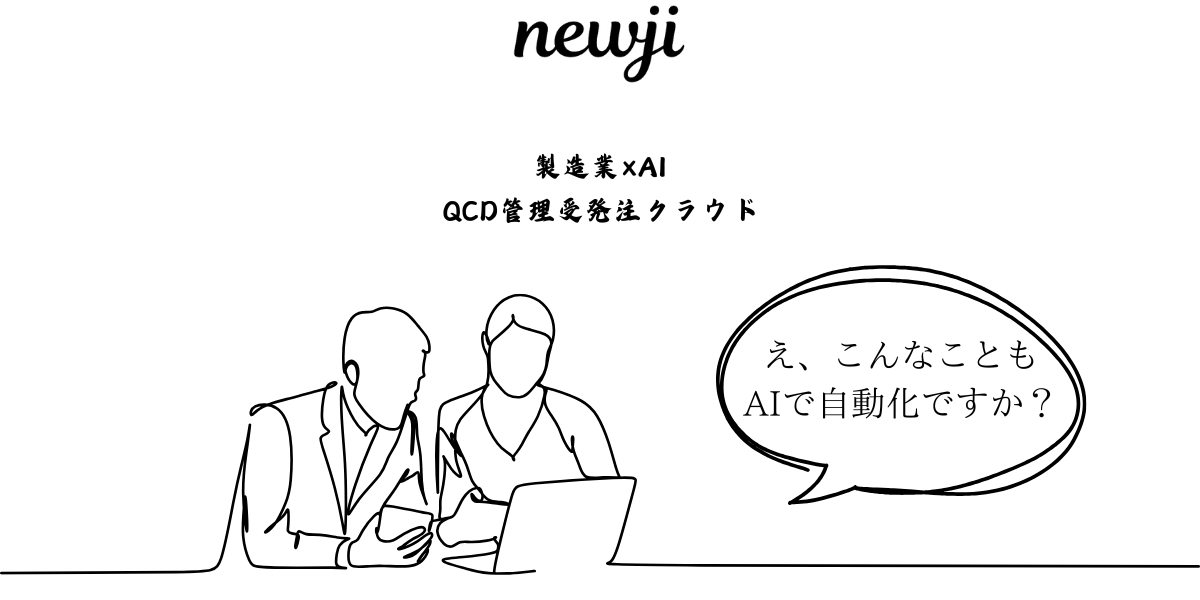
Unveiling Japan’s Mastery in Crafting OEM Accessory Cables for Global Markets
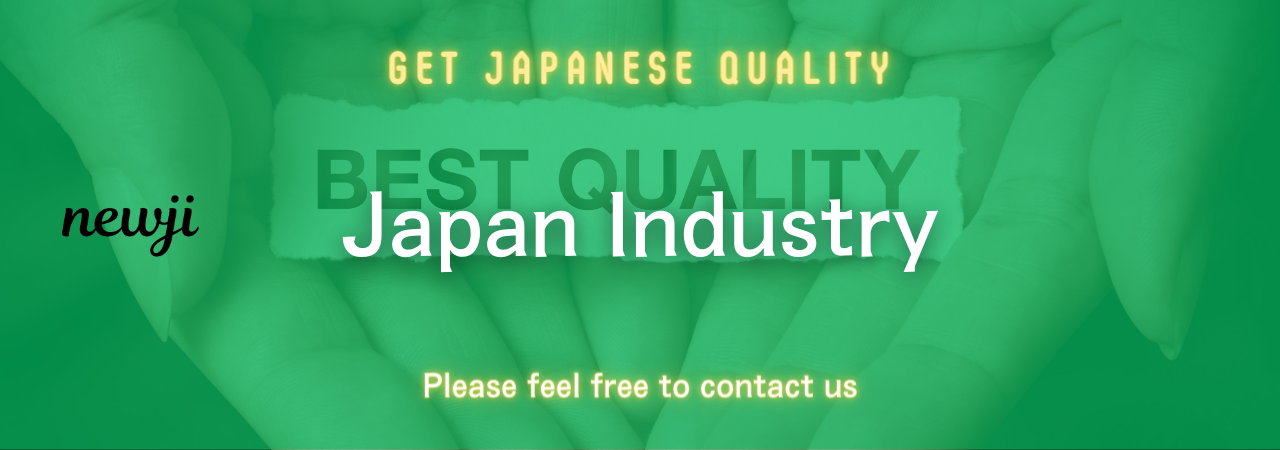
目次
Introduction to Japan’s OEM Accessory Cable Excellence
Japan has long been recognized for its unparalleled expertise in manufacturing, particularly in the realm of Original Equipment Manufacturer (OEM) accessory cables. These cables are integral components in a wide array of industries, from automotive to consumer electronics. Japan’s commitment to precision, quality, and innovation has positioned its OEM accessory cables as staples in global markets. This article delves into the intricacies of Japan’s mastery in crafting these essential components, exploring the advantages, challenges, and best practices that define their success.
Understanding OEM Accessory Cables
OEM accessory cables are specialized cables designed to connect and power various components within devices and machinery. They play a crucial role in ensuring seamless functionality and connectivity across different applications. The quality and reliability of these cables are paramount, as they directly impact the performance and longevity of the end products.
Types of OEM Accessory Cables
There is a diverse range of OEM accessory cables tailored to specific applications. These include:
– **Power Cables:** Designed to supply electrical power to devices.
– **Data Cables:** Facilitate the transfer of data between components.
– **Signal Cables:** Transmit control signals within systems.
– **Hybrid Cables:** Combine multiple functionalities, such as power and data transmission.
Each type demands rigorous quality standards to meet the diverse needs of various industries.
Advantages of Japanese OEM Accessory Cables
Japan’s dominance in the OEM accessory cable market can be attributed to several key advantages that enhance their global competitiveness.
1. Superior Quality Control
Japanese manufacturers adhere to stringent quality control protocols, ensuring that every cable meets high standards of performance and durability. Advanced testing methods are employed to detect and eliminate defects, guaranteeing that only the best products reach the market.
2. Technological Innovation
Japan consistently invests in research and development, driving innovation in cable design and manufacturing processes. This commitment to technology results in products that are not only reliable but also incorporate the latest advancements in materials and engineering.
3. Precision Engineering
The precision engineering practices in Japan ensure that OEM accessory cables are manufactured with exact specifications. This meticulous attention to detail minimizes the risk of errors and enhances the overall functionality of the cables.
4. Efficient Supply Chain Management
Japanese companies excel in managing their supply chains, ensuring timely delivery of components and finished products. This efficiency reduces lead times and allows for better responsiveness to market demands.
5. Strong Supplier Relationships
Long-term partnerships with reliable suppliers enable Japanese manufacturers to maintain consistent quality and secure access to high-grade materials. These relationships foster trust and collaboration, contributing to the overall excellence of OEM accessory cables.
Disadvantages and Challenges
Despite numerous strengths, the Japanese OEM accessory cable industry faces certain challenges that can impact its global standing.
1. High Production Costs
The emphasis on quality and precision results in higher production costs. This can make Japanese OEM accessory cables more expensive compared to those produced in regions with lower manufacturing costs.
2. Limited Flexibility
Japanese manufacturers often operate within well-established processes, which can limit their ability to quickly adapt to changing market trends or customize products to specific customer needs.
3. Language and Cultural Barriers
Engaging with Japanese suppliers may present language and cultural challenges for international buyers. Miscommunications can lead to misunderstandings and delays in procurement processes.
4. Regulatory Compliance
Navigating the complex regulatory landscape in Japan requires expertise and resources. Ensuring compliance with local standards and international regulations can be time-consuming and costly.
Supplier Negotiation Techniques
Effective negotiation with Japanese suppliers is crucial for securing favorable terms and building long-term partnerships. Here are some strategies to enhance negotiation outcomes.
1. Building Trust and Relationships
Japanese business culture places a high value on trust and long-term relationships. Investing time in relationship-building activities, such as face-to-face meetings and regular communication, can facilitate smoother negotiations.
2. Understanding Cultural Norms
Respecting Japanese cultural norms and etiquette is essential. This includes punctuality, formality in communication, and a collaborative approach to problem-solving.
3. Clear Communication
Ensure that all specifications, requirements, and expectations are clearly communicated. Providing detailed documentation and being explicit about your needs can prevent misunderstandings.
4. Flexibility and Compromise
Be prepared to show flexibility and a willingness to compromise on certain aspects. This collaborative mindset can lead to mutually beneficial agreements.
5. Long-Term Commitment
Demonstrating a commitment to a long-term partnership can make Japanese suppliers more inclined to offer favorable terms and prioritize your orders.
Market Conditions and Trends
Understanding the current market landscape is vital for making informed procurement decisions. Several trends are shaping the OEM accessory cable market globally.
1. Increasing Demand for High-Speed Connectivity
The rise of high-speed devices and the Internet of Things (IoT) has surged demand for advanced data and signal cables. Japanese manufacturers are at the forefront of developing cables that meet these evolving needs.
2. Emphasis on Sustainability
Environmental sustainability is becoming a critical factor in procurement. Japanese companies are increasingly adopting eco-friendly materials and sustainable manufacturing practices to align with global sustainability goals.
3. Technological Advancements
Advancements in materials science and cable design are driving the development of cables with enhanced performance characteristics, such as higher bandwidth and greater durability.
4. Global Supply Chain Disruptions
Recent disruptions, including geopolitical tensions and pandemics, have highlighted the importance of resilient supply chains. Japanese manufacturers are investing in strategies to mitigate risks and ensure continuity.
5. Customization and Personalization
There is a growing demand for customized OEM accessory cables tailored to specific applications. Japanese suppliers are leveraging their engineering prowess to offer more personalized solutions.
Best Practices in Procuring Japanese OEM Accessory Cables
Adhering to best practices can significantly enhance the procurement process, ensuring that buyers receive high-quality products efficiently.
1. Comprehensive Supplier Evaluation
Conduct thorough evaluations of potential suppliers. Assess their quality control measures, production capabilities, financial stability, and reputation in the market.
2. Clear Specification Documentation
Provide detailed and precise specifications to suppliers. This includes technical requirements, quality standards, packaging instructions, and delivery timelines.
3. Establishing Communication Channels
Maintain open and consistent communication with suppliers. Utilize multiple channels, such as email, video conferencing, and periodic visits, to stay connected and address issues promptly.
4. Implementing Quality Assurance Processes
Incorporate robust quality assurance protocols throughout the procurement process. Regular inspections, testing, and audits can help maintain high standards.
5. Leveraging Technology
Utilize procurement software and technologies to streamline processes, track orders, and manage supplier relationships effectively.
6. Negotiating Favorable Terms
Ensure that contract terms are clear and favorable. This includes pricing, payment terms, delivery schedules, and clauses for handling potential disputes.
7. Fostering Long-Term Partnerships
Aim to build long-term relationships with suppliers. Consistent collaboration can lead to better pricing, priority in production schedules, and enhanced product quality.
Quality Control and Assurance
Quality control is a cornerstone of Japan’s manufacturing excellence. Implementing rigorous quality assurance measures ensures that OEM accessory cables meet or exceed industry standards.
1. In-Process Inspections
Conduct inspections at various stages of the manufacturing process. This helps identify and rectify defects early, preventing faulty products from reaching the final stages.
2. Final Product Testing
Perform comprehensive testing on finished cables to verify their performance, durability, and compliance with specifications. This includes electrical testing, stress testing, and environmental testing.
3. Certification and Compliance
Ensure that products comply with relevant international standards and obtain necessary certifications. This enhances credibility and facilitates entry into various markets.
4. Continuous Improvement
Adopt a culture of continuous improvement. Regularly review and refine quality control processes to incorporate the latest best practices and technological advancements.
Logistics and Supply Chain Management
Efficient logistics and supply chain management are critical for timely delivery and cost-effectiveness in procurement.
1. Strategic Sourcing
Identify and collaborate with suppliers who offer the best combination of quality, reliability, and cost. Strategic sourcing involves evaluating multiple suppliers to select the most suitable partners.
2. Inventory Management
Implement effective inventory management practices to balance supply and demand. Techniques such as Just-In-Time (JIT) can minimize inventory holding costs and reduce waste.
3. Transportation Optimization
Optimize transportation routes and methods to ensure timely and cost-effective delivery of cables. This may involve selecting the most efficient carriers and consolidating shipments.
4. Risk Mitigation
Develop strategies to mitigate risks in the supply chain, such as diversifying suppliers, maintaining safety stock, and having contingency plans for disruptions.
5. Collaboration and Integration
Foster collaboration between different stakeholders in the supply chain. Integrating systems and sharing information can enhance visibility and coordination, leading to improved efficiency.
Production Management and Engineering
Effective production management and engineering practices are essential for maintaining the high standards associated with Japanese OEM accessory cables.
1. Lean Manufacturing
Adopt lean manufacturing principles to eliminate waste, improve efficiency, and enhance product quality. This approach focuses on optimizing processes and maximizing value.
2. Automation and Advanced Technologies
Utilize automation and advanced manufacturing technologies to increase precision, reduce errors, and boost production capacity. Robotics and AI-driven systems are increasingly being integrated into manufacturing processes.
3. Workforce Training and Development
Invest in training and developing the workforce to ensure they possess the necessary skills and knowledge. A well-trained workforce contributes to higher productivity and quality.
4. Process Standardization
Standardize production processes to ensure consistency and repeatability. Standardization facilitates scalability and simplifies quality control procedures.
5. Continuous Monitoring and Improvement
Implement systems for continuous monitoring of production processes. Use data and analytics to identify areas for improvement and implement necessary changes.
Quality Control Strategies
Maintaining high-quality standards is non-negotiable in the production of OEM accessory cables. Japanese manufacturers employ several strategies to uphold quality.
1. Total Quality Management (TQM)
Adopt TQM practices that involve every member of the organization in the pursuit of quality. This holistic approach ensures that quality is embedded in every aspect of production.
2. Six Sigma
Implement Six Sigma methodologies to reduce variability and defects in manufacturing processes. This data-driven approach enhances precision and reliability.
3. Supplier Quality Assurance
Collaborate closely with suppliers to ensure that the materials and components used meet stringent quality standards. Regular audits and assessments help maintain supplier quality.
4. Customer Feedback Integration
Incorporate customer feedback into quality improvement initiatives. Understanding and addressing customer concerns can lead to better product quality and customer satisfaction.
5. Robust Documentation
Maintain comprehensive documentation of quality control procedures, inspections, and testing results. This transparency ensures accountability and facilitates continuous improvement.
Automation and Factory Efficiency
Automation plays a pivotal role in enhancing factory efficiency and maintaining high production standards.
1. Automated Production Lines
Implement automated production lines to streamline manufacturing processes, increase output, and reduce human error. Automation ensures consistent quality and faster production cycles.
2. Smart Manufacturing
Leverage smart manufacturing technologies, such as the Internet of Things (IoT) and artificial intelligence (AI), to monitor and optimize production in real-time.
3. Energy Efficiency
Adopt energy-efficient practices and technologies to reduce operational costs and minimize environmental impact. This includes using energy-efficient machinery and optimizing production schedules.
4. Predictive Maintenance
Use predictive maintenance techniques to foresee and address equipment issues before they lead to downtime. This proactive approach enhances production reliability and efficiency.
5. Data Analytics
Utilize data analytics to gain insights into production performance, identify bottlenecks, and implement improvements. Data-driven decision-making leads to more effective and efficient operations.
Procurement Best Practices
Implementing best practices in procurement ensures that companies can effectively source high-quality OEM accessory cables from Japanese suppliers.
1. Strategic Planning
Develop a strategic procurement plan that aligns with your company’s goals and objectives. This includes identifying key suppliers, setting procurement priorities, and forecasting demand.
2. Supplier Diversification
Diversify your supplier base to mitigate risks associated with dependency on a single supplier. This ensures continuity in supply and reduces vulnerability to disruptions.
3. Cost Management
Implement effective cost management strategies to balance quality and cost. This includes negotiating favorable pricing, optimizing order quantities, and reducing waste.
4. Ethical Sourcing
Ensure that suppliers adhere to ethical standards, including fair labor practices and environmental sustainability. Ethical sourcing enhances your company’s reputation and compliance with regulations.
5. Performance Monitoring
Regularly monitor supplier performance through key performance indicators (KPIs). This helps in assessing reliability, quality, and service levels, enabling informed decision-making.
6. Contract Management
Manage contracts meticulously to ensure that all terms and conditions are met. This includes monitoring compliance, managing changes, and addressing any contractual issues promptly.
7. Continuous Improvement
Foster a culture of continuous improvement in procurement processes. Seek feedback, analyze performance data, and implement enhancements to optimize procurement efficiency.
Conclusion
Japan’s mastery in crafting OEM accessory cables is a testament to its dedication to quality, precision, and innovation. While there are challenges, such as higher production costs and cultural barriers, the advantages far outweigh the drawbacks. By adhering to best practices in procurement, leveraging advanced manufacturing technologies, and maintaining robust quality control measures, Japanese manufacturers continue to set the benchmark in the global market. For companies seeking reliable and high-quality OEM accessory cables, partnering with Japanese suppliers offers substantial benefits, ensuring that their products meet the highest standards of performance and reliability.
資料ダウンロード
QCD調達購買管理クラウド「newji」は、調達購買部門で必要なQCD管理全てを備えた、現場特化型兼クラウド型の今世紀最高の購買管理システムとなります。
ユーザー登録
調達購買業務の効率化だけでなく、システムを導入することで、コスト削減や製品・資材のステータス可視化のほか、属人化していた購買情報の共有化による内部不正防止や統制にも役立ちます。
NEWJI DX
製造業に特化したデジタルトランスフォーメーション(DX)の実現を目指す請負開発型のコンサルティングサービスです。AI、iPaaS、および先端の技術を駆使して、製造プロセスの効率化、業務効率化、チームワーク強化、コスト削減、品質向上を実現します。このサービスは、製造業の課題を深く理解し、それに対する最適なデジタルソリューションを提供することで、企業が持続的な成長とイノベーションを達成できるようサポートします。
オンライン講座
製造業、主に購買・調達部門にお勤めの方々に向けた情報を配信しております。
新任の方やベテランの方、管理職を対象とした幅広いコンテンツをご用意しております。
お問い合わせ
コストダウンが利益に直結する術だと理解していても、なかなか前に進めることができない状況。そんな時は、newjiのコストダウン自動化機能で大きく利益貢献しよう!
(Β版非公開)