- お役立ち記事
- “Unveiling Japan’s Mastery in PCB Original Equipment Manufacturing: A Deep Dive into Innovation and Excellence”
“Unveiling Japan’s Mastery in PCB Original Equipment Manufacturing: A Deep Dive into Innovation and Excellence”
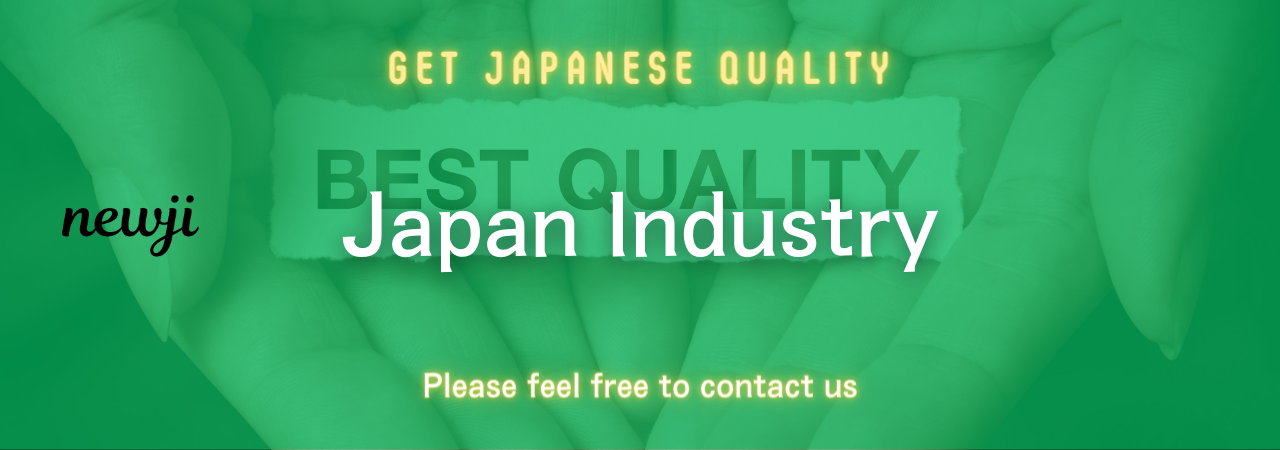
目次
Introduction
In the rapidly evolving landscape of electronics manufacturing, Printed Circuit Boards (PCBs) serve as the backbone of countless devices that power our daily lives. From smartphones to industrial machinery, the demand for high-quality PCBs continues to surge. Among the global leaders in PCB Original Equipment Manufacturing (OEM), Japan stands out for its unwavering commitment to innovation and excellence. This article delves into Japan’s mastery in PCB OEM manufacturing, exploring the factors that set it apart, the advantages and challenges of partnering with Japanese suppliers, and best practices for procurement and purchasing professionals seeking to leverage Japan’s expertise.
Overview of PCB Original Equipment Manufacturing in Japan
Japan has long been synonymous with precision engineering and high-quality manufacturing. The country’s PCB OEM sector exemplifies these attributes, characterized by advanced technological capabilities, stringent quality controls, and a culture of continuous improvement. Japanese PCB manufacturers cater to a diverse range of industries, including automotive, consumer electronics, telecommunications, and industrial automation. Their ability to produce complex, multi-layered PCBs with high reliability makes them preferred partners for global brands seeking top-tier components.
Japanese PCB OEM companies often invest heavily in research and development, striving to stay at the forefront of technological advancements. This focus on innovation enables them to offer cutting-edge solutions that meet the evolving needs of their clients. Additionally, Japan’s robust manufacturing infrastructure and efficient logistics networks facilitate seamless production and timely delivery, further enhancing the appeal of Japanese PCB manufacturers in the global market.
Advantages of Japanese PCB OEM Manufacturing
Quality and Precision
One of the most significant advantages of partnering with Japanese PCB OEMs is their unwavering commitment to quality and precision. Japanese manufacturers adhere to stringent quality management systems, such as ISO 9001 and IPC standards, ensuring that every PCB meets the highest benchmarks for performance and reliability. Advanced inspection and testing procedures are integral to the manufacturing process, minimizing defects and ensuring that each product performs flawlessly in its intended application.
Furthermore, Japanese PCB manufacturers leverage state-of-the-art equipment and technology to achieve unparalleled precision in their manufacturing processes. This focus on accuracy ensures that complex circuit designs are executed flawlessly, reducing the risk of malfunctions and enhancing the overall longevity of electronic devices.
Advanced Technology and Innovation
Japan’s leadership in technological innovation is a key driver of its success in PCB OEM manufacturing. Japanese companies continuously invest in research and development to explore new materials, manufacturing techniques, and design methodologies. This relentless pursuit of innovation enables them to produce high-density interconnect (HDI) PCBs, flexible and rigid-flex PCBs, and other advanced circuitry solutions that cater to the demands of modern electronic applications.
Moreover, Japanese PCB manufacturers are adept at integrating emerging technologies such as automation, artificial intelligence, and the Internet of Things (IoT) into their production processes. This integration enhances manufacturing efficiency, reduces lead times, and allows for greater customization and scalability, providing clients with tailored solutions that meet their specific requirements.
Efficient Production Processes
Efficiency is a hallmark of Japanese manufacturing, and PCB OEM production is no exception. Japanese companies implement lean manufacturing principles to eliminate waste, optimize workflows, and enhance productivity. These practices enable manufacturers to maintain high output levels while minimizing costs and maintaining superior quality standards.
Additionally, the adoption of Just-In-Time (JIT) production methods ensures that materials and components are delivered precisely when needed, reducing inventory costs and preventing production delays. This efficiency extends to the supply chain, where close collaboration with suppliers and logistics partners ensures seamless coordination and timely delivery of finished products.
Strong Supply Chain Management
Japanese PCB OEMs benefit from a well-established and resilient supply chain ecosystem. The country’s robust infrastructure, reliable transportation networks, and strategic geographic location facilitate the efficient movement of materials and components. Furthermore, Japanese manufacturers maintain strong relationships with both domestic and international suppliers, ensuring a steady flow of high-quality materials required for PCB production.
This effective supply chain management not only enhances production efficiency but also provides flexibility in responding to market fluctuations and unforeseen disruptions. As a result, Japanese PCB OEMs can consistently meet delivery deadlines and maintain reliability, even in the face of global supply chain challenges.
Disadvantages of Working with Japanese PCB OEMs
Higher Costs
While the quality and technological prowess of Japanese PCB OEMs are undeniable, partnering with them often entails higher costs compared to manufacturers in other regions. Labor costs in Japan are relatively high, and these expenses are reflected in the pricing of PCB products. Additionally, the emphasis on premium materials and advanced manufacturing processes can further drive up costs.
For businesses operating on tight budgets or seeking cost-effective solutions, these higher expenses may pose a challenge. However, it’s essential to weigh these costs against the long-term benefits of superior quality, reliability, and reduced warranty claims, which can offset the initial investment.
Language and Cultural Barriers
Navigating language and cultural differences can be a hurdle when collaborating with Japanese PCB OEMs. While many Japanese companies conduct business in English, nuances in communication styles, business etiquette, and decision-making processes can lead to misunderstandings or delays. Building effective communication channels requires patience, cultural sensitivity, and sometimes the assistance of bilingual intermediaries or local representatives.
Moreover, Japanese business culture often emphasizes long-term relationships, trust-building, and consensus-based decision-making. Western businesses accustomed to more direct and fast-paced interactions may need to adapt to these practices to foster successful partnerships.
Longer Lead Times
Japanese PCB OEMs typically prioritize quality and meticulousness over speed, which can result in longer lead times compared to manufacturers focused on rapid production. This emphasis on thoroughness ensures that each PCB meets stringent quality standards but may extend the time required to fulfill orders.
For businesses operating under tight deadlines or those requiring quick turnaround times, this aspect can be a disadvantage. However, proactive communication and early planning can help mitigate potential delays by allowing sufficient time for production and addressing any issues that may arise during the manufacturing process.
Supplier Negotiation Techniques
Building Strong Relationships
In Japanese business culture, building strong, trust-based relationships is paramount. Establishing a solid rapport with suppliers fosters mutual respect and cooperation, which can lead to more favorable negotiation outcomes. Take the time to understand the supplier’s values, business practices, and long-term goals. Regular communication and face-to-face meetings, when possible, can strengthen the relationship and facilitate smoother negotiations.
Understanding Cultural Nuances
Awareness of cultural nuances can significantly impact negotiation effectiveness. Japanese negotiations often involve indirect communication and a focus on consensus rather than confrontation. Demonstrating respect, patience, and a willingness to understand the supplier’s perspective can create a more collaborative atmosphere. Avoid aggressive negotiation tactics, as they may be counterproductive and damage the relationship.
Leveraging Local Expertise
Engaging local experts or hiring personnel with experience in Japanese business practices can be invaluable during negotiations. These individuals can provide insights into cultural expectations, appropriate negotiation strategies, and effective communication techniques. Their expertise can help bridge cultural gaps and ensure that negotiations proceed smoothly and respectfully.
Negotiating Payment Terms and Contracts
Clear and mutually agreeable payment terms are crucial for successful negotiations. Japanese suppliers may prefer payment methods that balance security and convenience for both parties, such as letters of credit or installment payments tied to specific milestones. Discuss and agree upon terms that protect your interests while accommodating the supplier’s needs.
Additionally, contracts should be detailed and precise, outlining all aspects of the agreement, including specifications, delivery schedules, quality standards, and dispute resolution mechanisms. A comprehensive contract minimizes misunderstandings and provides a clear framework for the partnership.
Market Conditions for Japanese PCB OEM Manufacturing
Current Trends in the PCB Industry
The PCB industry is experiencing rapid advancements driven by the proliferation of electronic devices and the integration of cutting-edge technologies. Trends such as miniaturization, high-density interconnects (HDI), flexible and rigid-flex PCBs, and the growing demand for environmentally friendly manufacturing processes are shaping the market. Japanese PCB OEMs are at the forefront of these trends, continuously developing innovative solutions to meet evolving industry demands.
Moreover, the rise of the Internet of Things (IoT), 5G technology, and advancements in electric vehicles (EVs) are creating new opportunities and challenges for PCB manufacturers. Japanese companies are leveraging their technological expertise to develop PCBs that can handle the increased complexity and performance requirements of these emerging applications.
Impact of Global Supply Chain Dynamics
Global supply chain disruptions, such as those caused by geopolitical tensions, natural disasters, or pandemics, can significantly impact the PCB OEM sector. Japanese manufacturers are highly attuned to the importance of supply chain resilience and employ strategies to mitigate risks. Diversifying suppliers, maintaining strategic inventories, and fostering strong relationships with key partners are common practices that help ensure continuity in production.
Additionally, Japan’s strategic initiatives to enhance regional supply chain integration, particularly within Asia, aim to reduce dependency on any single source and promote more flexible and robust supply networks. These efforts enhance the ability of Japanese PCB OEMs to respond swiftly to changing market conditions and maintain reliable operations.
Technological Advancements
Continuous technological advancements are a driving force behind the competitiveness of Japanese PCB OEMs. Innovations in materials science, such as the development of advanced substrates and conductive inks, improve PCB performance and durability. Automation and digitalization in manufacturing processes enhance precision, reduce errors, and increase production efficiency.
Furthermore, the adoption of Industry 4.0 principles, including the integration of smart sensors, data analytics, and connected machinery, enables Japanese PCB manufacturers to optimize processes, predict maintenance needs, and achieve higher levels of customization. Staying abreast of these technological trends ensures that Japanese PCB OEMs remain leaders in the global market.
Best Practices in Procurement and Purchasing from Japanese Suppliers
Thorough Supplier Evaluation
Before entering into a partnership with a Japanese PCB OEM, conduct a comprehensive evaluation of the supplier’s capabilities, reputation, and track record. Assess factors such as manufacturing capacity, technological expertise, quality certifications, and financial stability. Request samples and visit manufacturing facilities if possible to gain firsthand insight into their operations.
Additionally, seek feedback from existing clients to understand their experiences and satisfaction levels. A thorough evaluation ensures that you partner with a reliable supplier that can consistently meet your quality and delivery expectations.
Clear Communication and Specifications
Effective communication is essential for successful procurement and purchasing. Provide detailed and precise specifications for your PCB requirements, including design schematics, material specifications, tolerances, and performance criteria. Use clear and unambiguous language to minimize the risk of misunderstandings.
Establish regular communication channels to discuss project progress, address any issues, and make timely decisions. Utilize project management tools and collaborative platforms to facilitate information sharing and ensure that both parties are aligned throughout the manufacturing process.
Establishing Long-term Partnerships
Building long-term partnerships with Japanese PCB OEMs can lead to numerous benefits, including better pricing, priority access to advanced technologies, and enhanced collaboration on innovation projects. Demonstrate your commitment to the partnership by providing consistent business, timely payments, and active engagement in joint planning and problem-solving.
Long-term relationships foster trust and mutual understanding, enabling both parties to work together more effectively and navigate challenges collaboratively.
Continuous Quality Monitoring
Maintaining high quality standards requires continuous monitoring and collaboration with your Japanese PCB supplier. Implement stringent quality control measures, including regular inspections, testing, and audits, to ensure that the PCBs meet your specifications and industry standards.
Establish clear protocols for addressing quality issues, including corrective actions and preventive measures. Collaborate with the supplier on process improvements and share feedback to drive ongoing enhancements in product quality and manufacturing efficiency.
Case Studies: Success Stories in Japanese PCB OEM Partnerships
Automotive Industry Collaboration
A leading global automotive manufacturer partnered with a Japanese PCB OEM to develop advanced PCBs for electric vehicles (EVs). The collaboration focused on creating high-density interconnects capable of handling the complex electronics systems in EVs. The Japanese supplier’s expertise in HDI technology and commitment to quality ensured that the PCBs met stringent performance and safety standards. The partnership resulted in improved vehicle performance, increased reliability, and accelerated time-to-market for the automotive manufacturer.
Consumer Electronics Innovation
A prominent consumer electronics company sought to enhance the compactness and functionality of its latest smartphone model. Collaborating with a Japanese PCB OEM, they developed flexible and rigid-flex PCBs that allowed for sleeker device designs without compromising on performance. The Japanese supplier’s innovative approach and advanced manufacturing capabilities enabled the creation of highly efficient PCBs, contributing to the smartphone’s success in the competitive market.
Industrial Automation Advancement
An industrial automation firm partnered with a Japanese PCB manufacturer to develop robust PCBs for harsh operating environments. The collaboration focused on creating PCBs with enhanced durability and resistance to extreme temperatures and vibrations. The Japanese supplier’s expertise in quality control and materials science ensured that the PCBs met the demanding requirements of industrial applications. This partnership led to the deployment of more reliable and efficient automation systems, boosting the firm’s market reputation and customer satisfaction.
Conclusion
Japan’s mastery in PCB Original Equipment Manufacturing is a testament to the country’s enduring commitment to quality, precision, and innovation. Partnering with Japanese PCB OEMs offers significant advantages, including access to advanced technology, efficient production processes, and a robust supply chain. However, challenges such as higher costs and cultural barriers must be carefully navigated to realize the full benefits of these partnerships.
For procurement and purchasing professionals, adopting best practices such as thorough supplier evaluation, clear communication, and continuous quality monitoring is essential for successful collaboration with Japanese suppliers. By understanding and leveraging Japan’s expertise in PCB manufacturing, businesses can enhance their product offerings, achieve greater reliability, and maintain a competitive edge in the global market.
As the demand for sophisticated and high-performance PCBs continues to grow, Japan’s role as a leader in PCB OEM manufacturing is poised to strengthen. Embracing the opportunities and overcoming the challenges of partnering with Japanese manufacturers will unlock significant value, driving innovation and excellence in the ever-evolving electronics industry.
資料ダウンロード
QCD調達購買管理クラウド「newji」は、調達購買部門で必要なQCD管理全てを備えた、現場特化型兼クラウド型の今世紀最高の購買管理システムとなります。
ユーザー登録
調達購買業務の効率化だけでなく、システムを導入することで、コスト削減や製品・資材のステータス可視化のほか、属人化していた購買情報の共有化による内部不正防止や統制にも役立ちます。
NEWJI DX
製造業に特化したデジタルトランスフォーメーション(DX)の実現を目指す請負開発型のコンサルティングサービスです。AI、iPaaS、および先端の技術を駆使して、製造プロセスの効率化、業務効率化、チームワーク強化、コスト削減、品質向上を実現します。このサービスは、製造業の課題を深く理解し、それに対する最適なデジタルソリューションを提供することで、企業が持続的な成長とイノベーションを達成できるようサポートします。
オンライン講座
製造業、主に購買・調達部門にお勤めの方々に向けた情報を配信しております。
新任の方やベテランの方、管理職を対象とした幅広いコンテンツをご用意しております。
お問い合わせ
コストダウンが利益に直結する術だと理解していても、なかなか前に進めることができない状況。そんな時は、newjiのコストダウン自動化機能で大きく利益貢献しよう!
(Β版非公開)