- お役立ち記事
- Unveiling Japan’s Mastery in Stiffness: The Art and Science behind World-class Manufacturing
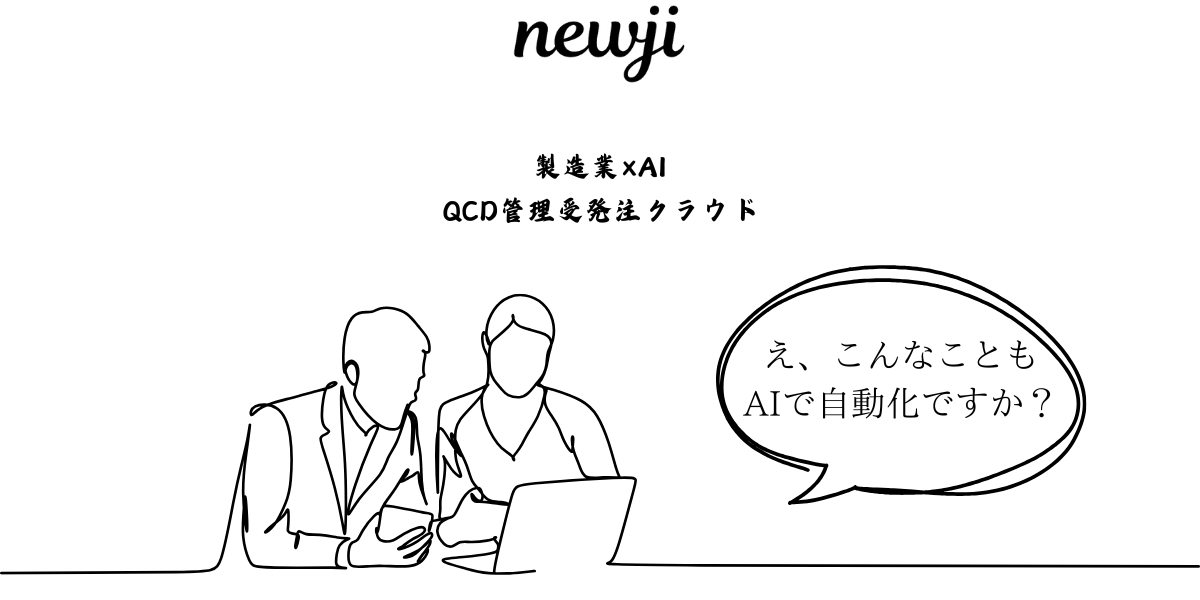
Unveiling Japan’s Mastery in Stiffness: The Art and Science behind World-class Manufacturing
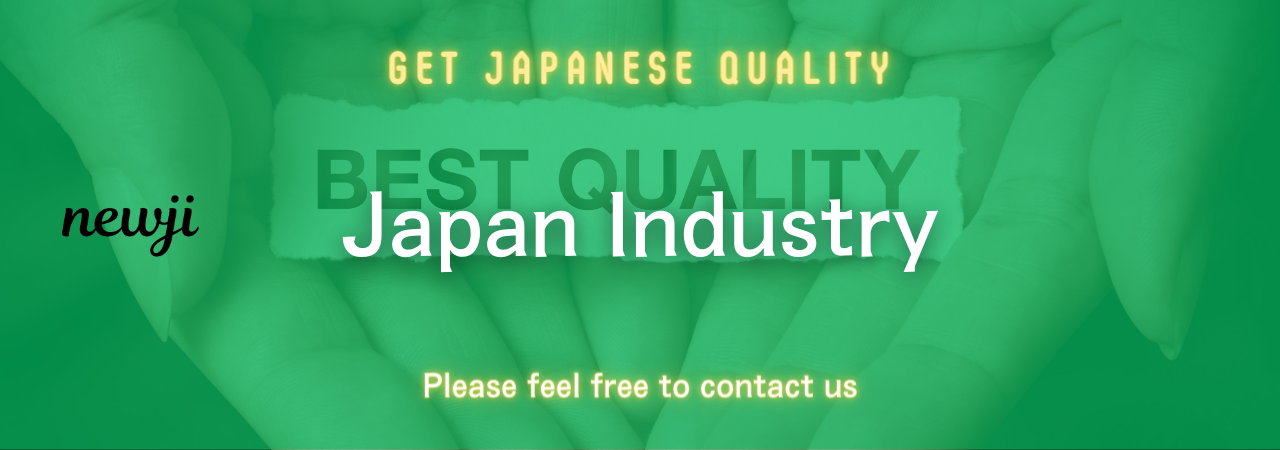
目次
Introduction to Japan’s Manufacturing Excellence
Japan has long been recognized as a powerhouse in the global manufacturing landscape.
Its commitment to quality, precision, and innovation has set benchmarks across various industries.
At the heart of this success lies an intricate balance of art and science, particularly evident in the mastery of stiffness in manufacturing processes.
This article delves into the factors that contribute to Japan’s world-class manufacturing capabilities, with a focus on procurement and purchasing strategies, supplier negotiation techniques, market conditions, and best practices.
The Importance of Stiffness in Manufacturing
Stiffness refers to the ability of a material or structure to resist deformation under applied forces.
In manufacturing, maintaining optimal stiffness is crucial for ensuring product durability, performance, and safety.
Japanese manufacturers prioritize stiffness to meet stringent quality standards and exceed customer expectations.
This focus not only enhances product reliability but also contributes to the overall efficiency of the manufacturing process.
Procurement and Purchasing Strategies
Building Strong Supplier Relationships
Japanese companies emphasize long-term relationships with their suppliers.
This approach fosters collaboration, trust, and mutual growth.
By working closely with suppliers, manufacturers can ensure the consistent quality of materials and components, which is essential for maintaining stiffness in their products.
Just-In-Time (JIT) Inventory Management
The JIT system minimizes inventory costs by receiving goods only as they are needed in the production process.
This strategy reduces waste and ensures that materials are fresh and meet quality standards.
For maintaining stiffness, precise timing and quality control are crucial, and JIT supports these objectives by streamlining the supply chain.
Cost Management and Value Creation
Effective procurement strategies focus not only on cost reduction but also on value creation.
Japanese manufacturers negotiate with suppliers to achieve the best prices without compromising quality.
This balance is vital for producing high-stiffness products that are both affordable and reliable.
Supplier Negotiation Techniques
Win-Win Negotiations
Japanese negotiation tactics prioritize mutually beneficial outcomes.
By ensuring that both parties gain from the agreement, manufacturers build strong, enduring relationships with suppliers.
This collaborative approach leads to better terms, improved quality, and greater flexibility in addressing challenges related to product stiffness.
Emphasis on Quality and Continuous Improvement
Negotiations often include discussions on quality standards and continuous improvement initiatives.
Suppliers are encouraged to adopt advanced technologies and processes that enhance the stiffness and overall quality of their products.
This commitment to excellence drives innovation and maintains Japan’s competitive edge in manufacturing.
Transparency and Communication
Effective communication is a cornerstone of successful negotiations.
Japanese manufacturers maintain transparency regarding their requirements, expectations, and feedback.
This openness ensures that suppliers understand the critical aspects of stiffness and work diligently to meet these standards.
Market Conditions and Adaptability
Responsive Supply Chain Management
Japan’s manufacturing sector is highly responsive to market fluctuations.
Manufacturers adapt quickly to changes in demand, ensuring that production schedules and supply chains remain uninterrupted.
This agility is essential for maintaining consistent product stiffness even in dynamic market conditions.
Technological Advancements
Continuous investment in technology allows Japanese manufacturers to stay ahead of industry trends.
Advanced machinery and automation play a significant role in enhancing manufacturing precision and stiffness.
By embracing innovation, manufacturers can produce high-quality, stiff products efficiently.
Sustainability and Environmental Considerations
Sustainable practices are integral to Japan’s manufacturing philosophy.
Eco-friendly materials and processes not only reduce environmental impact but also contribute to the structural integrity and stiffness of products.
Balancing sustainability with performance is a key aspect of Japan’s manufacturing strategy.
Best Practices in Japanese Manufacturing
Kaizen: Continuous Improvement
Kaizen, or continuous improvement, is a fundamental principle in Japanese manufacturing.
By constantly seeking ways to enhance processes, reduce waste, and improve product quality, manufacturers ensure that stiffness and other performance metrics are consistently optimized.
Lean Manufacturing
Lean manufacturing focuses on eliminating inefficiencies and ensuring that every step in the production process adds value.
This methodology enhances productivity and maintains high stiffness standards by streamlining operations and minimizing errors.
Total Quality Management (TQM)
TQM involves a comprehensive approach to quality, encompassing all aspects of production.
From design to final inspection, every stage is carefully monitored to ensure that products meet the highest standards of stiffness and reliability.
Employee Training and Development
Investing in employee skills and knowledge is crucial for maintaining manufacturing excellence.
Japanese companies offer extensive training programs to ensure that workers are proficient in the latest technologies and methodologies.
Skilled employees are better equipped to manage processes that affect product stiffness, leading to superior outcomes.
Advantages of Japanese Manufacturing Practices
High-Quality Standards
Japanese manufacturers are renowned for their commitment to quality.
This dedication ensures that products have optimal stiffness, durability, and performance, making them highly competitive in the global market.
Efficiency and Productivity
Through practices like JIT and lean manufacturing, Japanese companies achieve high levels of efficiency and productivity.
These practices reduce waste, lower costs, and enhance the overall manufacturing process, contributing to superior product stiffness.
Innovation and Technology
A strong emphasis on research and development fosters innovation.
Japanese manufacturers often lead in adopting new technologies that enhance product stiffness and performance, maintaining their position at the forefront of the industry.
Challenges and Disadvantages
High Production Costs
Maintaining high-quality standards and advanced technologies can lead to increased production costs.
While the focus on stiffness and quality offers significant advantages, it may also result in higher prices compared to competitors from regions with lower manufacturing costs.
Rigid Structures
The emphasis on long-term supplier relationships and established processes can sometimes result in rigidity.
This may hinder flexibility and adaptability, making it challenging to respond swiftly to sudden market changes or disruptions.
Dependency on Skilled Labor
Japanese manufacturing heavily relies on skilled labor for maintaining high stiffness and quality.
A shortage of skilled workers can impact production efficiency and the ability to uphold rigorous standards.
Market Conditions Affecting Japanese Manufacturing
Global Competition
Japanese manufacturers face intense competition from other global players who also prioritize quality and innovation.
Staying ahead requires continuous improvement and adaptation to maintain their competitive edge in stiffness and other performance metrics.
Economic Fluctuations
Economic instability can affect demand, supply chains, and production costs.
Japanese companies must navigate these fluctuations carefully to sustain their manufacturing excellence and product stiffness.
Technological Disruptions
Rapid technological advancements can disrupt traditional manufacturing processes.
Japanese manufacturers must continually invest in new technologies to ensure that their products remain stiff and meet evolving industry standards.
Best Practices for Achieving High Stiffness in Manufacturing
Material Selection and Testing
Choosing the right materials is fundamental to achieving necessary stiffness levels.
Japanese manufacturers invest in thorough material testing to ensure that only the highest quality materials are used in production.
Precision Engineering
Accurate and precise engineering processes are essential for maintaining product stiffness.
Advanced machinery and skilled technicians ensure that every component meets the specific stiffness requirements.
Continuous Monitoring and Quality Control
Implementing robust quality control systems allows for continuous monitoring of stiffness during the manufacturing process.
This proactive approach helps identify and address issues promptly, ensuring that the final product meets desired stiffness standards.
Collaborative Design Processes
Involving suppliers and stakeholders in the design process fosters a collaborative environment.
This collaboration ensures that stiffness requirements are clearly communicated and met throughout the production cycle.
The Future of Japanese Manufacturing
As the global market evolves, Japanese manufacturing faces both opportunities and challenges.
Technological advancements, shifting consumer preferences, and environmental considerations will shape the future landscape.
Japanese manufacturers are well-positioned to leverage their expertise in stiffness and quality to navigate these changes.
By continuing to embrace innovation, invest in skilled labor, and uphold their commitment to excellence, Japan will remain a leader in world-class manufacturing.
Conclusion
Japan’s mastery in stiffness is a testament to its broader manufacturing prowess.
Through strategic procurement and purchasing, effective supplier negotiations, and a relentless focus on quality and efficiency, Japanese manufacturers produce products that stand the test of time.
While challenges exist, the adoption of best practices and a commitment to continuous improvement ensure that Japan remains at the forefront of the global manufacturing industry.
By understanding and implementing these strategies, other manufacturers can aspire to achieve similar levels of excellence in stiffness and overall product quality.
資料ダウンロード
QCD調達購買管理クラウド「newji」は、調達購買部門で必要なQCD管理全てを備えた、現場特化型兼クラウド型の今世紀最高の購買管理システムとなります。
ユーザー登録
調達購買業務の効率化だけでなく、システムを導入することで、コスト削減や製品・資材のステータス可視化のほか、属人化していた購買情報の共有化による内部不正防止や統制にも役立ちます。
NEWJI DX
製造業に特化したデジタルトランスフォーメーション(DX)の実現を目指す請負開発型のコンサルティングサービスです。AI、iPaaS、および先端の技術を駆使して、製造プロセスの効率化、業務効率化、チームワーク強化、コスト削減、品質向上を実現します。このサービスは、製造業の課題を深く理解し、それに対する最適なデジタルソリューションを提供することで、企業が持続的な成長とイノベーションを達成できるようサポートします。
オンライン講座
製造業、主に購買・調達部門にお勤めの方々に向けた情報を配信しております。
新任の方やベテランの方、管理職を対象とした幅広いコンテンツをご用意しております。
お問い合わせ
コストダウンが利益に直結する術だと理解していても、なかなか前に進めることができない状況。そんな時は、newjiのコストダウン自動化機能で大きく利益貢献しよう!
(Β版非公開)