- お役立ち記事
- Unveiling Japan’s Microfabrication OEM Mastery: A Deep Dive into Precision Engineering
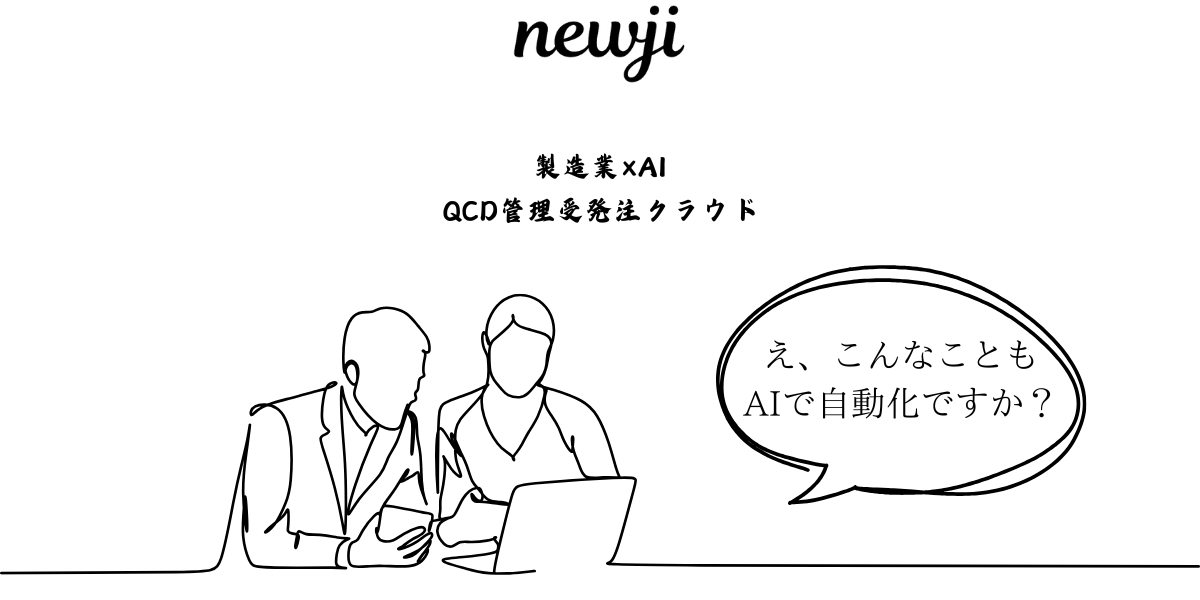
Unveiling Japan’s Microfabrication OEM Mastery: A Deep Dive into Precision Engineering
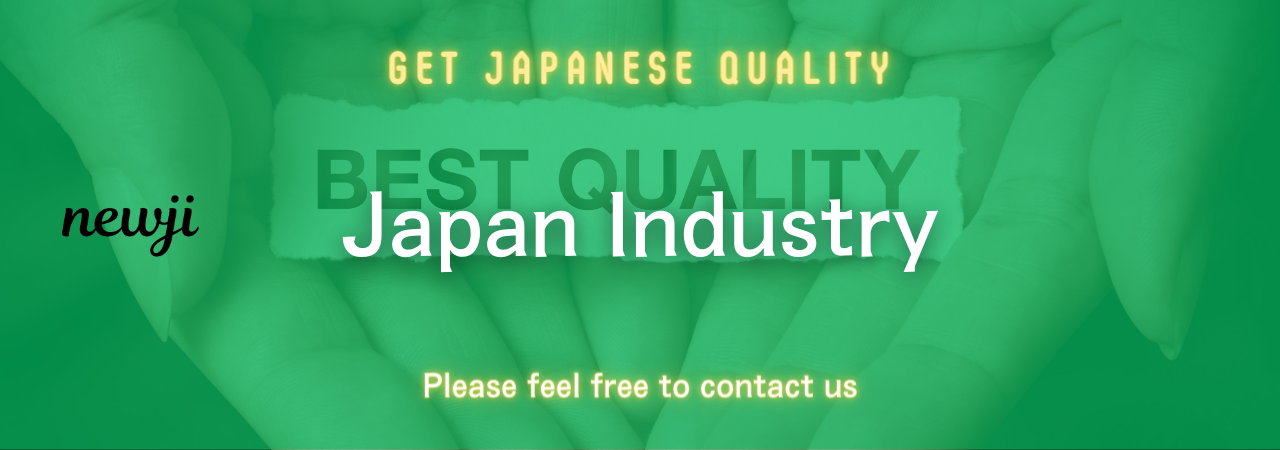
目次
Introduction to Japan’s Microfabrication OEM Landscape
Japan has long been recognized as a global leader in precision engineering and microfabrication. The country’s original equipment manufacturer (OEM) sector excels in producing high-quality components and systems used in a variety of industries, including electronics, automotive, and medical devices. This mastery stems from a blend of advanced technology, meticulous quality control, and efficient manufacturing processes that set Japanese OEMs apart on the international stage.
Understanding Microfabrication in Japan
Microfabrication refers to the process of fabricating miniature structures and devices, typically on the scale of micrometers. This technology is paramount in the production of semiconductors, MEMS (Micro-Electro-Mechanical Systems), and other advanced components. Japan’s expertise in this field is underpinned by significant investments in research and development, leading to innovations that continually push the boundaries of precision and efficiency.
Key Technologies Driving Japanese Microfabrication
Japanese manufacturers utilize cutting-edge technologies such as photolithography, etching, and deposition techniques to achieve the high levels of precision required in microfabrication. Additionally, the integration of automation and robotics in production lines enhances consistency and reduces the margin for error, ensuring that products meet stringent quality standards.
The Procurement and Purchasing Advantage
Procurement and purchasing are critical functions within manufacturing companies, directly impacting cost efficiency and supply chain reliability. Japan’s OEMs offer distinct advantages in these areas, making them attractive partners for international businesses.
Quality and Reliability
One of the foremost advantages of partnering with Japanese OEMs is their unwavering commitment to quality. Japanese manufacturers adhere to rigorous quality control processes, often exceeding international standards. This dedication ensures that components are not only precise but also reliable over long-term use.
Cost Efficiency
Despite perceptions of higher costs, Japanese OEMs often provide cost-efficient solutions through their optimized manufacturing processes. The focus on minimizing waste, maximizing resource utilization, and implementing lean manufacturing principles contributes to competitive pricing without compromising quality.
Strong Supplier Relationships
Japanese companies emphasize building long-term relationships with their suppliers. This collaborative approach fosters trust, ensuring timely deliveries, and facilitating effective communication. Such relationships are invaluable in maintaining a smooth and efficient supply chain.
Advantages and Disadvantages of Sourcing from Japanese OEMs
When considering sourcing from Japanese OEMs, it’s essential to weigh the benefits against potential challenges to make informed procurement decisions.
Advantages
- High Precision and Quality: Japanese OEMs are renowned for their precise manufacturing capabilities and high-quality outputs.
- Advanced Technology: Access to the latest microfabrication technologies ensures cutting-edge products.
- Reliability: Consistent delivery schedules and dependable supply chains enhance operational stability.
- Innovation: Continuous investment in R&D drives innovation, offering competitive advantages.
- Strong After-Sales Support: Comprehensive support services help in maintaining and troubleshooting products post-purchase.
Disadvantages
- Higher Initial Costs: The premium quality and advanced technologies may come with higher upfront costs.
- Cultural and Language Barriers: Differences in business practices and language can pose communication challenges.
- Longer Lead Times: Depending on the proximity of suppliers, lead times may be longer compared to local sourcing.
- Complex Supply Chains: Navigating the intricate supplier networks requires expertise and effective management.
Supplier Negotiation Techniques with Japanese OEMs
Negotiating with Japanese suppliers requires a nuanced approach that respects cultural norms and business practices. Understanding these techniques can lead to more successful and mutually beneficial partnerships.
Building Relationships
In Japan, business relationships are foundational. Taking the time to establish trust and rapport can lead to more favorable negotiation outcomes. This involves regular communication, face-to-face meetings when possible, and showing genuine interest in the supplier’s operations and challenges.
Understanding Cultural Nuances
Japanese business culture values respect, patience, and indirect communication. It’s crucial to approach negotiations with humility and avoid aggressive tactics. Instead, focus on collaborative problem-solving and demonstrating how both parties can benefit from the agreement.
Emphasizing Long-Term Benefits
Japanese suppliers often prioritize long-term partnerships over short-term gains. Highlighting the potential for ongoing collaboration and mutual growth can make negotiations more successful. Proposals that include future projects or extended agreements are likely to resonate well.
Clear and Detailed Communication
Providing clear, detailed specifications and expectations helps prevent misunderstandings. Ensure that all requirements are documented comprehensively, and be open to discussing any aspects that need clarification or adjustment.
Market Conditions and Trends in Japanese Microfabrication
Staying abreast of market conditions and emerging trends is essential for effective procurement and purchasing strategies. Japan’s microfabrication sector is influenced by several key factors that shape its current landscape.
Technological Advancements
Ongoing advancements in nanotechnology, materials science, and automation continue to drive innovation in microfabrication. Japanese OEMs are at the forefront of integrating these technologies to enhance their manufacturing capabilities and product offerings.
Global Supply Chain Dynamics
Global supply chain disruptions, such as those caused by the COVID-19 pandemic, have highlighted the importance of resilient and flexible supply networks. Japanese manufacturers are adapting by diversifying their supplier bases and investing in supply chain optimization.
Sustainability and Environmental Considerations
There is a growing emphasis on sustainable practices and environmental responsibility within the manufacturing sector. Japanese OEMs are increasingly adopting eco-friendly processes and materials, aligning with global sustainability goals and customer preferences.
Economic Factors
Economic fluctuations, including exchange rates and trade policies, impact the cost and feasibility of sourcing from Japan. Understanding these factors is crucial for making informed procurement decisions and mitigating potential risks.
Best Practices for Procuring from Japanese OEMs
Implementing best practices when sourcing from Japanese OEMs can enhance procurement efficiency and foster successful partnerships.
Comprehensive Supplier Evaluation
Before engaging with a Japanese OEM, conduct a thorough evaluation of their capabilities, financial stability, and reputation. Assess their technological expertise, quality control measures, and past performance to ensure they meet your organization’s standards.
Effective Communication Strategies
Maintain open and transparent communication channels with your Japanese suppliers. Regular updates, clear feedback, and prompt responses to inquiries help build a strong working relationship and address issues proactively.
Collaborative Planning
Work closely with your suppliers in planning and forecasting to align production schedules and inventory management. Collaborative planning reduces the risk of delays and ensures that both parties are prepared to meet demand fluctuations.
Implementing Quality Assurance Protocols
Establishing robust quality assurance protocols in collaboration with your supplier ensures that products meet the required specifications. Regular audits, inspections, and testing are essential components of maintaining high-quality standards.
Leveraging Technology and Automation
Utilize digital tools and automation to streamline procurement processes, track orders, and manage supply chains effectively. Technologies such as ERP systems, supply chain management software, and automated procurement platforms can enhance efficiency and accuracy.
Case Studies: Successful Procurement from Japanese OEMs
Examining real-world examples of successful procurement initiatives provides valuable insights into effective strategies and practices.
Automotive Industry Collaboration
A leading automotive manufacturer partnered with a Japanese OEM specializing in precision engine components. Through collaborative design and joint quality control initiatives, the company achieved significant improvements in component reliability and performance, ultimately enhancing the overall vehicle quality.
Electronics Sector Partnership
An electronics firm sourced microfabricated sensors from a Japanese supplier. By integrating the supplier’s advanced technologies and adhering to strict quality standards, the company was able to develop innovative products that gained a competitive edge in the market.
Medical Devices Procurement
A medical device manufacturer worked closely with a Japanese OEM to develop specialized microfabricated parts for surgical instruments. The partnership ensured that the components met the stringent regulatory requirements and contributed to the development of high-precision medical devices.
Overcoming Challenges in Sourcing from Japan
While sourcing from Japanese OEMs offers numerous advantages, navigating potential challenges is essential to ensure successful procurement outcomes.
Language and Communication Barriers
Language differences can impede effective communication. Investing in bilingual staff or utilizing professional translation services can help bridge this gap and facilitate smoother interactions with suppliers.
Cultural Differences
Understanding and respecting Japanese business culture is crucial. Engaging in cultural training and fostering cultural awareness within your procurement team can enhance collaboration and prevent misunderstandings.
Managing Lead Times
Longer lead times can affect inventory management and project timelines. Implementing strategic planning, maintaining buffer stocks, and developing contingency plans can mitigate the impact of extended lead times.
Handling Intellectual Property Concerns
Protecting intellectual property (IP) is vital when collaborating with international suppliers. Establish clear contractual agreements that outline IP rights and implement safeguards to prevent unauthorized use or disclosure of proprietary information.
Strategies for Enhancing Factory Efficiency and Automation
Japanese OEMs excel in factory efficiency and automation, which directly benefit procurement and purchasing functions by ensuring consistent quality and reliable supply.
Lean Manufacturing Principles
Adopting lean manufacturing principles helps minimize waste, optimize processes, and enhance overall efficiency. This approach leads to cost reductions and improved productivity, benefiting both suppliers and purchasers.
Integration of Industry 4.0 Technologies
Incorporating Industry 4.0 technologies such as the Internet of Things (IoT), artificial intelligence (AI), and machine learning enhances manufacturing capabilities. These technologies enable real-time monitoring, predictive maintenance, and smarter decision-making, leading to higher efficiency and reduced downtime.
Flexible Manufacturing Systems
Implementing flexible manufacturing systems allows OEMs to adapt quickly to changing market demands and customize products efficiently. This flexibility ensures that suppliers can meet diverse and evolving customer requirements.
Continuous Improvement Culture
Fostering a culture of continuous improvement encourages ongoing evaluation and enhancement of processes. Regularly reviewing performance metrics and seeking feedback from stakeholders drive sustained efficiency and innovation.
Best Practices in Quality Control and Assurance
Maintaining high-quality standards is paramount in microfabrication. Japanese OEMs employ comprehensive quality control and assurance practices to ensure product excellence.
Total Quality Management (TQM)
TQM is a holistic approach that involves every aspect of the manufacturing process. By embedding quality into every step, from design to production, OEMs ensure that products consistently meet or exceed expectations.
Statistical Process Control (SPC)
SPC utilizes statistical methods to monitor and control manufacturing processes. This technique helps identify and rectify variations, ensuring that the production remains within specified quality parameters.
Supplier Quality Audits
Regular audits of suppliers help verify compliance with quality standards and identify areas for improvement. These audits foster accountability and encourage continuous enhancement of quality practices.
Failure Mode and Effects Analysis (FMEA)
FMEA identifies potential failure points in the manufacturing process and assesses their impact. By proactively addressing these issues, OEMs can prevent defects and enhance product reliability.
Future Outlook: Innovations and Opportunities
The future of Japan’s microfabrication OEM sector is poised for continued growth and innovation, driven by emerging technologies and evolving market demands.
Advancements in Nanotechnology
Nanotechnology advancements will enable the creation of even smaller and more efficient components. Japanese OEMs are investing in research to harness these developments, positioning themselves at the forefront of precision engineering.
Expansion into Emerging Markets
As global demand for high-precision components grows, Japanese OEMs are expanding into emerging markets. This expansion offers new opportunities for partnerships and business growth, diversifying their global presence.
Sustainable Manufacturing Practices
The shift towards sustainability will drive OEMs to adopt greener manufacturing practices. Innovations in eco-friendly materials and energy-efficient processes will not only meet regulatory requirements but also appeal to environmentally conscious customers.
Integration of AI and Machine Learning
AI and machine learning will play a significant role in optimizing manufacturing processes. These technologies can predict maintenance needs, enhance quality control, and streamline operations, further boosting factory efficiency.
Conclusion
Japan’s mastery in microfabrication OEM and precision engineering offers substantial advantages for international procurement and purchasing operations. The combination of high-quality standards, advanced technologies, and efficient manufacturing processes make Japanese OEMs reliable and innovative partners. By understanding the unique benefits and challenges associated with sourcing from Japan, and implementing best practices in supplier negotiation, quality control, and supply chain management, businesses can leverage the strengths of Japanese manufacturers to enhance their own product offerings and market competitiveness. As the industry continues to evolve, staying informed about technological advancements and market trends will be crucial in maintaining successful and sustainable partnerships with Japan’s leading OEMs.
資料ダウンロード
QCD調達購買管理クラウド「newji」は、調達購買部門で必要なQCD管理全てを備えた、現場特化型兼クラウド型の今世紀最高の購買管理システムとなります。
ユーザー登録
調達購買業務の効率化だけでなく、システムを導入することで、コスト削減や製品・資材のステータス可視化のほか、属人化していた購買情報の共有化による内部不正防止や統制にも役立ちます。
NEWJI DX
製造業に特化したデジタルトランスフォーメーション(DX)の実現を目指す請負開発型のコンサルティングサービスです。AI、iPaaS、および先端の技術を駆使して、製造プロセスの効率化、業務効率化、チームワーク強化、コスト削減、品質向上を実現します。このサービスは、製造業の課題を深く理解し、それに対する最適なデジタルソリューションを提供することで、企業が持続的な成長とイノベーションを達成できるようサポートします。
オンライン講座
製造業、主に購買・調達部門にお勤めの方々に向けた情報を配信しております。
新任の方やベテランの方、管理職を対象とした幅広いコンテンツをご用意しております。
お問い合わせ
コストダウンが利益に直結する術だと理解していても、なかなか前に進めることができない状況。そんな時は、newjiのコストダウン自動化機能で大きく利益貢献しよう!
(Β版非公開)