- お役立ち記事
- Unveiling Japan’s Pioneering Sustainable Strategy in the Manufacturing Industry
月間76,176名の
製造業ご担当者様が閲覧しています*
*2025年3月31日現在のGoogle Analyticsのデータより
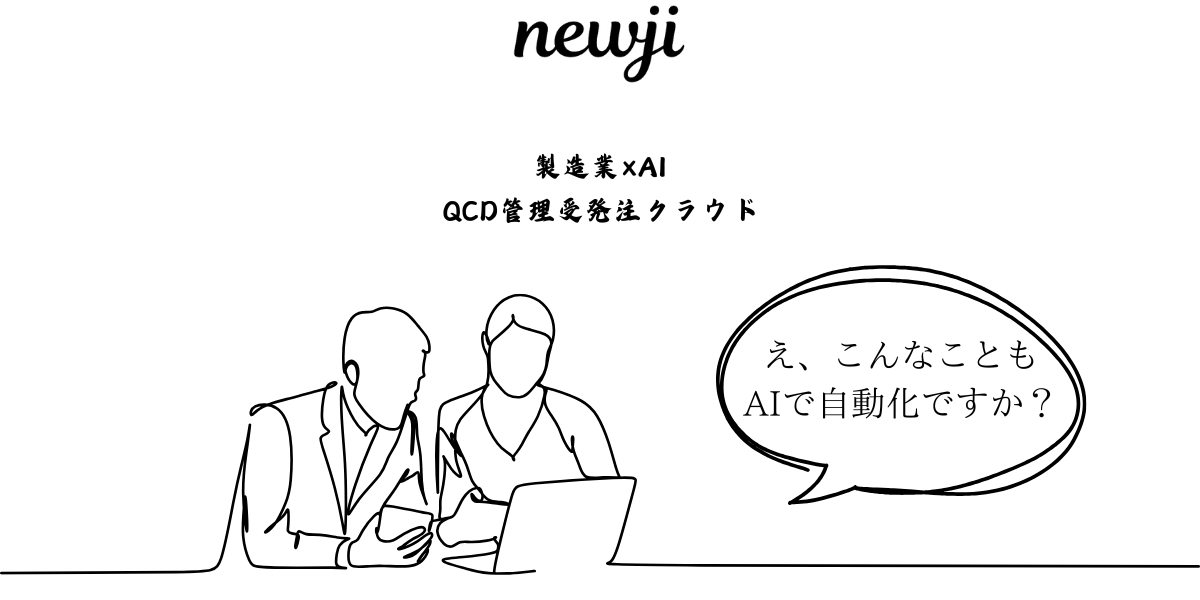
Unveiling Japan’s Pioneering Sustainable Strategy in the Manufacturing Industry
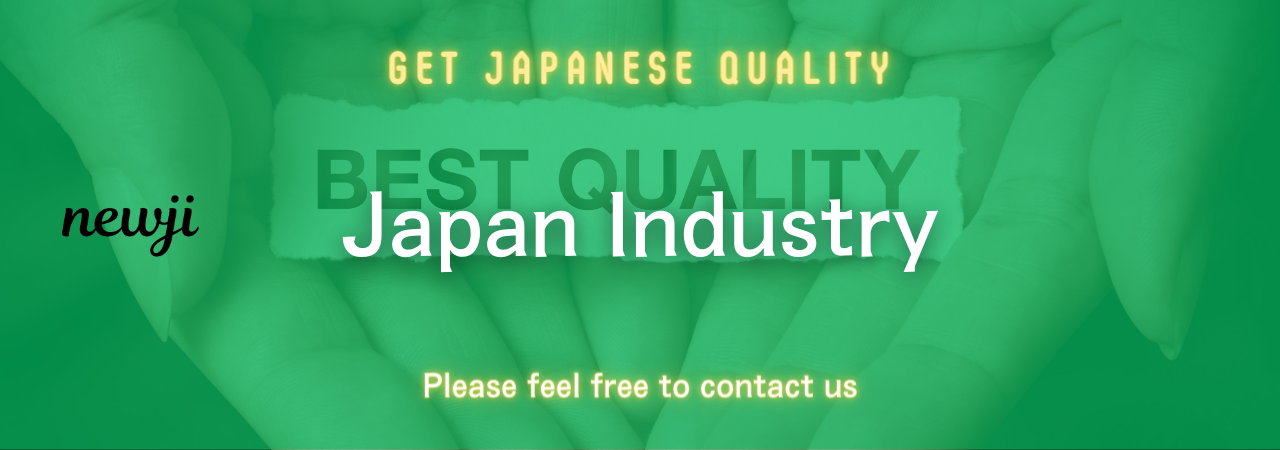
目次
Introduction to Japan’s Sustainable Manufacturing Strategy
Japan has long been recognized as a global leader in manufacturing excellence.
The country’s commitment to sustainability has become a cornerstone of its industrial strategy.
This focus not only enhances environmental stewardship but also drives innovation and efficiency within manufacturing processes.
As international markets increasingly prioritize sustainable practices, Japan’s approach offers valuable insights for global procurement and purchasing professionals.
Key Elements of Japan’s Sustainable Manufacturing Strategy
1. Energy Efficiency
Japanese manufacturers prioritize energy-efficient technologies to minimize environmental impact.
Investments in advanced machinery and automation reduce energy consumption and enhance production capabilities.
These efforts contribute to lower operational costs and a smaller carbon footprint, aligning with global sustainability goals.
2. Waste Reduction and Recycling
Waste reduction is integral to Japan’s manufacturing ethos.
Companies implement rigorous recycling programs and adopt circular economy principles to maximize resource utilization.
By minimizing waste, manufacturers not only comply with environmental regulations but also achieve significant cost savings.
3. Sustainable Supply Chain Management
Japan emphasizes sustainable practices throughout the supply chain.
This includes selecting suppliers who adhere to environmental standards and fostering long-term, collaborative relationships.
Sustainable supply chain management ensures that ethical practices are maintained from raw material sourcing to final product delivery.
4. Innovation and Technological Advancement
Continuous innovation is a hallmark of Japanese manufacturing.
Investment in research and development drives the creation of eco-friendly products and processes.
Technological advancements, such as automation and smart manufacturing, enhance efficiency and reduce environmental impact.
Advantages of Japan’s Sustainable Manufacturing Approach
1. Enhanced Brand Reputation
Adopting sustainable practices enhances a company’s reputation both domestically and internationally.
Consumers are increasingly favoring brands that demonstrate a commitment to environmental responsibility.
This positive perception can lead to increased market share and customer loyalty.
2. Cost Savings
Sustainability initiatives often result in significant cost reductions.
Energy-efficient operations and waste minimization lower operational expenses.
Additionally, sustainable supply chain practices can reduce risks and improve overall financial performance.
3. Regulatory Compliance
Japan’s manufacturing sector proactively adheres to stringent environmental regulations.
By staying ahead of regulatory requirements, companies avoid penalties and maintain smooth operations.
This proactive approach also positions manufacturers favorably in markets with strict environmental standards.
4. Competitive Advantage
Sustainable manufacturing provides a competitive edge in the global market.
Companies that prioritize sustainability are better positioned to meet the evolving demands of international buyers and partners.
This advantage is particularly relevant in sectors where environmental impact is a critical consideration.
Challenges in Implementing Sustainable Manufacturing Practices
1. High Initial Investment
Transitioning to sustainable manufacturing often requires significant upfront investment in new technologies and processes.
This can be a barrier for smaller companies or those operating on tight budgets.
However, the long-term benefits and cost savings typically offset these initial expenditures.
2. Supply Chain Complexity
Ensuring sustainability across the entire supply chain can be complex.
It requires close collaboration and strict adherence to environmental standards among all suppliers.
Managing this complexity demands effective communication and robust monitoring systems.
3. Resistance to Change
Implementing sustainable practices may face resistance from employees or stakeholders accustomed to established methods.
Overcoming this resistance requires comprehensive training, clear communication of benefits, and strong leadership commitment.
Supplier Negotiation Techniques for Sustainable Procurement
1. Establish Clear Sustainability Criteria
Define specific sustainability standards that suppliers must meet.
These criteria should encompass environmental impact, labor practices, and ethical standards.
Clear guidelines facilitate informed decision-making and ensure alignment with corporate sustainability goals.
2. Foster Collaborative Relationships
Build strong, long-term partnerships with suppliers.
Collaborative relationships encourage mutual commitment to sustainability initiatives and facilitate problem-solving.
Regular communication and joint planning strengthen these partnerships and drive continuous improvement.
3. Implement Performance Metrics
Use measurable sustainability metrics to evaluate supplier performance.
Key performance indicators (KPIs) might include energy usage, waste generation, and compliance with environmental standards.
Regular assessments promote accountability and motivate suppliers to enhance their sustainable practices.
4. Provide Incentives for Sustainability
Offer incentives to suppliers who excel in sustainability.
These incentives can include preferential contracts, financial rewards, or public recognition.
Encouraging and rewarding sustainable practices fosters a culture of environmental responsibility.
Market Conditions Influencing Sustainable Manufacturing
1. Increasing Consumer Demand
Consumers are more informed and concerned about the environmental impact of products.
This shift in consumer behavior drives manufacturers to adopt sustainable practices to meet market expectations.
2. Regulatory Pressure
Governments worldwide are enacting stricter environmental regulations.
Compliance with these regulations is essential for market access and avoiding legal penalties.
Japan’s proactive approach to regulation positions its manufacturers favorably in global markets.
3. Technological Advancements
Advancements in technology facilitate the implementation of sustainable manufacturing processes.
Automation, artificial intelligence, and data analytics enable more efficient operations and better resource management.
4. Global Supply Chain Dynamics
Global supply chains are becoming more complex and interconnected.
Sustainable practices within the supply chain are crucial for mitigating risks and ensuring resilience against disruptions.
Best Practices for Sustainable Procurement and Purchasing
1. Conduct Comprehensive Sustainability Assessments
Evaluate the sustainability of potential suppliers through thorough assessments.
Consider factors such as environmental impact, labor practices, and ethical standards.
These evaluations ensure that suppliers align with your company’s sustainability objectives.
2. Integrate Sustainability into Procurement Policies
Incorporate sustainability criteria into all procurement policies and procedures.
This integration ensures that sustainability is a fundamental consideration in every purchasing decision.
3. Leverage Technology for Transparency
Utilize technology solutions to enhance supply chain transparency.
Tools like blockchain and supply chain management software provide real-time visibility into supplier practices and performance.
4. Engage and Educate Stakeholders
Educate internal and external stakeholders about the importance of sustainable procurement.
Encourage a culture of sustainability through training programs, workshops, and regular communications.
5. Continuously Monitor and Improve
Regularly monitor supplier performance and sustainability metrics.
Implement continuous improvement programs to address gaps and enhance sustainable practices over time.
Case Studies: Successful Implementation of Sustainable Strategies in Japanese Manufacturing
1. Toyota’s Green Manufacturing Initiatives
Toyota has been at the forefront of sustainable manufacturing with its “Toyota Environmental Challenge 2050.”
The company focuses on reducing CO2 emissions, conserving water, and minimizing waste throughout its production processes.
Toyota’s initiatives have not only enhanced its environmental performance but also set industry standards for sustainability.
2. Panasonic’s Eco-Smart Supply Chain
Panasonic has developed an eco-smart supply chain strategy that emphasizes resource efficiency and waste reduction.
The company collaborates closely with suppliers to implement energy-efficient technologies and sustainable practices.
Panasonic’s approach has led to significant reductions in environmental impact and improved supply chain resilience.
3. Hitachi’s Innovative Recycling Programs
Hitachi has implemented innovative recycling programs that convert manufacturing waste into valuable resources.
By adopting circular economy principles, Hitachi maximizes resource utilization and minimizes waste disposal.
These programs demonstrate Hitachi’s commitment to sustainability and its ability to innovate beyond traditional manufacturing practices.
The Future of Sustainable Manufacturing in Japan
Japan’s dedication to sustainable manufacturing is poised to shape the future of the global manufacturing landscape.
As environmental concerns continue to rise, Japan’s strategies offer a blueprint for integrating sustainability into industrial practices.
Future advancements may include increased adoption of renewable energy sources, further automation and digitalization of manufacturing processes, and enhanced global collaboration on sustainability initiatives.
Conclusion
Japan’s pioneering sustainable strategy in the manufacturing industry exemplifies the intersection of environmental responsibility and industrial excellence.
Through energy efficiency, waste reduction, sustainable supply chain management, and continuous innovation, Japanese manufacturers lead the way in sustainable practices.
Despite challenges such as high initial investments and supply chain complexities, the advantages of enhanced brand reputation, cost savings, regulatory compliance, and competitive advantage make sustainability a pivotal component of modern manufacturing.
By adopting best practices in procurement and purchasing, fostering collaborative supplier relationships, and leveraging technological advancements, global manufacturers can emulate Japan’s success.
As the world moves towards a more sustainable future, Japan’s strategies offer invaluable lessons for achieving environmental and economic sustainability in the manufacturing sector.
資料ダウンロード
QCD管理受発注クラウド「newji」は、受発注部門で必要なQCD管理全てを備えた、現場特化型兼クラウド型の今世紀最高の受発注管理システムとなります。
ユーザー登録
受発注業務の効率化だけでなく、システムを導入することで、コスト削減や製品・資材のステータス可視化のほか、属人化していた受発注情報の共有化による内部不正防止や統制にも役立ちます。
NEWJI DX
製造業に特化したデジタルトランスフォーメーション(DX)の実現を目指す請負開発型のコンサルティングサービスです。AI、iPaaS、および先端の技術を駆使して、製造プロセスの効率化、業務効率化、チームワーク強化、コスト削減、品質向上を実現します。このサービスは、製造業の課題を深く理解し、それに対する最適なデジタルソリューションを提供することで、企業が持続的な成長とイノベーションを達成できるようサポートします。
製造業ニュース解説
製造業、主に購買・調達部門にお勤めの方々に向けた情報を配信しております。
新任の方やベテランの方、管理職を対象とした幅広いコンテンツをご用意しております。
お問い合わせ
コストダウンが利益に直結する術だと理解していても、なかなか前に進めることができない状況。そんな時は、newjiのコストダウン自動化機能で大きく利益貢献しよう!
(β版非公開)