- お役立ち記事
- Unveiling Japan’s Precision Engineering: The Rise of Machine Tool OEM Giants
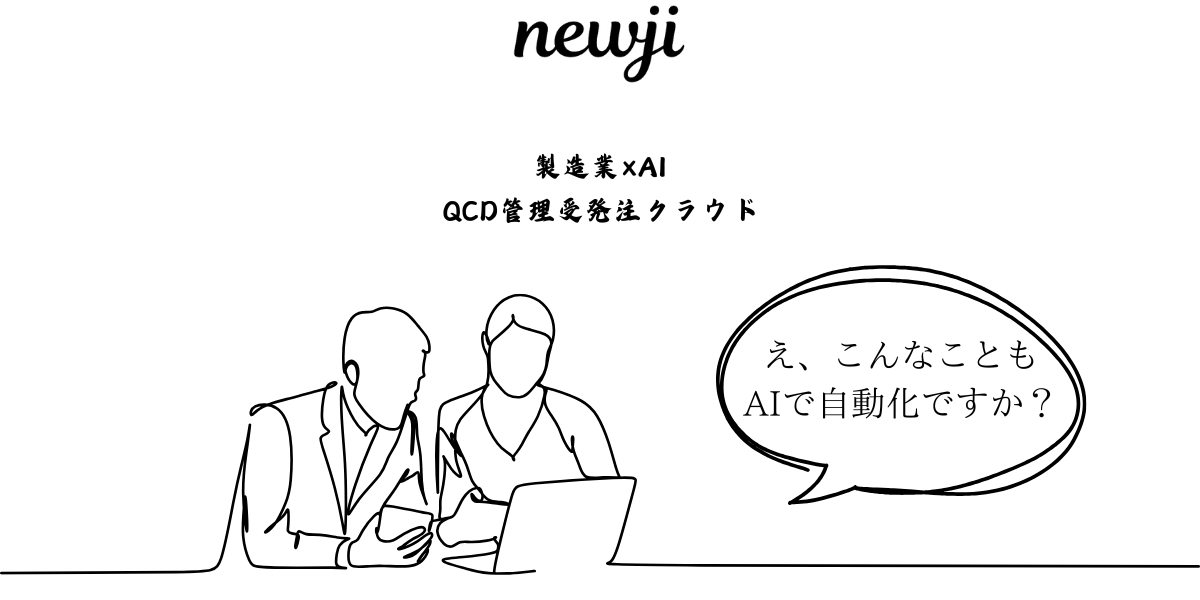
Unveiling Japan’s Precision Engineering: The Rise of Machine Tool OEM Giants
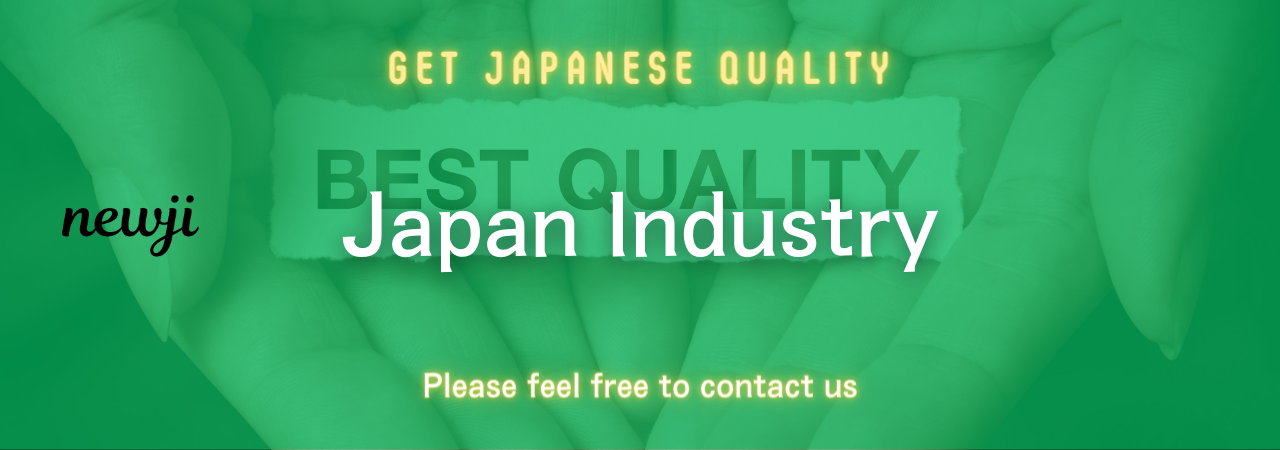
目次
Introduction
Japan’s reputation for precision engineering and manufacturing excellence is known worldwide.
One of the cornerstones of this reputation is the prowess of its machine tool OEM (Original Equipment Manufacturer) giants.
These machine tool manufacturers play a crucial role in diverse industries, such as automotive, electronics, aerospace, and healthcare.
In this article, we’ll delve into the rise of these Japanese giants, exploring their advantages, challenges, negotiation strategies, and best practices in international procurement and purchasing.
The Rise of Japanese Machine Tool OEMs
Japan’s machine tool industry began to flourish during the post-World War II era.
The country’s emphasis on quality, precision, and innovation laid the foundation for Japanese companies to emerge as leaders in the field.
Names like Mitsubishi Heavy Industries, Okuma, Yamazaki Mazak, and DMG Mori Seiki are now synonymous with cutting-edge technology and reliability.
Historical Context
The seeds of Japan’s machine tool industry were planted in the early 20th century, with the establishment of companies like Toshiba Machine and Okuma Corporation.
However, it wasn’t until the post-war economic miracle that the industry truly blossomed.
Government initiatives, coupled with a relentless focus on quality and efficiency, propelled Japanese machine tool manufacturers to the forefront of global competition.
Technological Advancements
One of the key reasons behind the dominance of Japanese machine tool OEMs is their relentless pursuit of technological innovation.
From the development of CNC (Computer Numerical Control) systems to the integration of IoT (Internet of Things) and AI (Artificial Intelligence), Japanese companies have consistently pushed the boundaries of what’s possible.
For instance, the introduction of 5-axis machining centers revolutionized the capabilities of manufacturing complex parts, allowing for greater precision and efficiency.
Advantages of Japanese Machine Tool OEMs
When it comes to procurement and purchasing, Japanese machine tool OEMs offer several distinct advantages that make them attractive partners for international buyers.
Unmatched Quality and Precision
Japanese machine tool manufacturers are renowned for their impeccable quality standards.
Rigorous quality control processes, coupled with a culture that prioritizes perfection, ensure that each machine tool produced meets exacting specifications.
This level of precision is crucial for industries that demand high tolerances and exceptional accuracy.
Cutting-Edge Technology
As mentioned earlier, Japanese OEMs are at the forefront of technological innovation.
Their ability to integrate advanced features, such as real-time monitoring and predictive maintenance, into their machine tools sets them apart from competitors.
These technological advancements not only improve operational efficiency but also reduce downtime and maintenance costs.
Reliability and Longevity
Japanese machine tools are built to last.
Their robust construction and high-quality materials contribute to their longevity, making them a cost-effective investment for manufacturers.
The reliability of these machines minimizes production interruptions, ensuring smooth and consistent operations.
Strong After-Sales Support
One of the standout features of Japanese machine tool manufacturers is their commitment to customer support.
Comprehensive after-sales services, including timely maintenance, spare parts availability, and technical assistance, ensure that customers can rely on their machines for years to come.
Challenges and Disadvantages
While Japanese machine tool OEMs offer numerous benefits, there are also some challenges and disadvantages to consider when dealing with them.
High Initial Costs
One of the primary drawbacks of Japanese machine tools is their high initial cost.
The emphasis on quality, precision, and advanced technology often translates into a higher price tag.
However, it’s essential to consider the long-term benefits, such as reduced maintenance costs and increased operational efficiency, which can offset the initial investment.
Language and Cultural Barriers
Navigating the intricacies of language and cultural differences can pose a challenge when dealing with Japanese suppliers.
It’s crucial to understand and respect Japanese business etiquette, communication styles, and decision-making processes to foster a successful partnership.
Lead Times and Delivery
Due to the meticulous manufacturing processes and demand for these high-quality machines, lead times can be longer compared to other suppliers.
It’s essential to factor in these lead times when planning production schedules and inventory management.
Supplier Negotiation Techniques
Effective negotiation is key to securing favorable terms when procuring from Japanese machine tool OEMs.
Here are some strategies to consider:
Build Strong Relationships
In Japanese business culture, relationships and trust are paramount.
Invest time in building a strong rapport with your suppliers.
Regular visits to their facilities, attending trade shows, and engaging in social activities can help strengthen these relationships.
Be Prepared and Informed
Before entering negotiations, thoroughly research the supplier’s products, capabilities, and market position.
Being well-informed demonstrates your commitment and seriousness, making it easier to negotiate favorable terms.
Respect Cultural Norms
Understanding and respecting cultural norms can go a long way in negotiations.
Politeness, patience, and humility are highly valued in Japanese business interactions.
Avoid aggressive tactics and focus on collaborative problem-solving.
Leverage Long-Term Contracts
Japanese suppliers appreciate long-term commitments.
Consider negotiating longer-term contracts, which can result in better pricing and more favorable terms.
This approach also signals your intention to build a lasting partnership.
Highlight Mutual Benefits
Emphasize the mutual benefits of the partnership.
Show how the collaboration will be advantageous for both parties, whether through shared technological advancements, market expansion, or improved efficiency.
Market Conditions and Trends
Keeping abreast of market conditions and trends is crucial when dealing with Japanese machine tool OEMs.
Understanding the broader economic landscape and industry developments can help inform your procurement strategy.
Global Economic Factors
The global economic environment plays a significant role in the machine tool industry.
Factors such as trade policies, currency exchange rates, and economic growth in key markets can impact demand and pricing.
For example, fluctuations in the yen’s value can affect the cost of Japanese machine tools for international buyers.
Technological Advancements
The rapid pace of technological advancements is a defining feature of the machine tool industry.
Stay informed about emerging technologies, such as additive manufacturing (3D printing), automation, and Industry 4.0.
Understanding these trends can help you identify opportunities for process improvements and cost savings.
Sustainability and Environmental Regulations
Sustainability is becoming increasingly important in the manufacturing sector.
Japanese machine tool OEMs are at the forefront of developing environmentally friendly technologies.
Compliance with environmental regulations and the adoption of sustainable practices can enhance your company’s reputation and reduce operational costs.
Industry-Specific Trends
Different industries have unique requirements and trends.
For example, the automotive sector is moving towards electric vehicles (EVs), which necessitates new manufacturing processes and equipment.
Stay informed about industry-specific trends to ensure your procurement strategy aligns with the evolving needs of your sector.
Best Practices in Procurement and Purchasing
To maximize the benefits of working with Japanese machine tool OEMs, consider implementing the following best practices:
Conduct Thorough Supplier Assessments
Before entering a partnership, conduct comprehensive assessments of potential suppliers.
Evaluate their financial stability, production capabilities, quality control processes, and compliance with industry standards.
Supplier audits and site visits can provide valuable insights into their operations.
Implement Collaborative Planning
Collaborate closely with your suppliers on production planning and forecasting.
Sharing production schedules, inventory levels, and market forecasts can help optimize supply chain efficiency and reduce lead times.
This collaborative approach also fosters a sense of partnership and mutual benefit.
Focus on Total Cost of Ownership (TCO)
When evaluating the cost of machine tools, consider the total cost of ownership (TCO) rather than just the initial purchase price.
TCO includes factors such as maintenance costs, energy consumption, downtime, and the machine’s lifespan.
A machine with a higher initial cost may prove more cost-effective over its lifetime.
Emphasize Quality and Precision
Prioritize quality and precision in your procurement decisions.
Selecting high-quality machine tools may have a higher upfront cost, but it ensures consistent production, reduces defects, and minimizes rework.
Quality and precision directly impact your company’s reputation and customer satisfaction.
Adopt Lean Manufacturing Principles
Implement lean manufacturing principles to enhance efficiency and reduce waste.
Techniques such as Just-In-Time (JIT) inventory management, continuous improvement (Kaizen), and value stream mapping can streamline operations and improve overall productivity.
Lean practices align well with the high standards of Japanese machine tool OEMs.
Maintain Open Communication
Effective communication is vital for successful supplier relationships.
Maintain regular and transparent communication with your suppliers.
Share feedback, address issues promptly, and collaborate on problem-solving.
Open communication builds trust and ensures that both parties are aligned in their objectives.
Invest in Training and Development
Invest in training and development programs for your workforce.
Properly trained operators and maintenance personnel can maximize the performance and longevity of your machine tools.
Collaborate with your suppliers to provide training sessions and technical support when needed.
Conclusion
The rise of Japanese machine tool OEM giants is a testament to Japan’s commitment to precision engineering, quality, and innovation.
By understanding the advantages and challenges of working with these suppliers, employing effective negotiation techniques, and staying informed about market conditions and trends, companies can harness the full potential of Japanese machine tools.
Implementing best practices in procurement and purchasing ensures that you maximize the benefits of your investment, leading to improved efficiency, reduced costs, and enhanced competitiveness.
In the ever-evolving landscape of manufacturing, partnering with Japanese machine tool OEMs can be a strategic decision that propels your company towards success.
資料ダウンロード
QCD調達購買管理クラウド「newji」は、調達購買部門で必要なQCD管理全てを備えた、現場特化型兼クラウド型の今世紀最高の購買管理システムとなります。
ユーザー登録
調達購買業務の効率化だけでなく、システムを導入することで、コスト削減や製品・資材のステータス可視化のほか、属人化していた購買情報の共有化による内部不正防止や統制にも役立ちます。
NEWJI DX
製造業に特化したデジタルトランスフォーメーション(DX)の実現を目指す請負開発型のコンサルティングサービスです。AI、iPaaS、および先端の技術を駆使して、製造プロセスの効率化、業務効率化、チームワーク強化、コスト削減、品質向上を実現します。このサービスは、製造業の課題を深く理解し、それに対する最適なデジタルソリューションを提供することで、企業が持続的な成長とイノベーションを達成できるようサポートします。
オンライン講座
製造業、主に購買・調達部門にお勤めの方々に向けた情報を配信しております。
新任の方やベテランの方、管理職を対象とした幅広いコンテンツをご用意しております。
お問い合わせ
コストダウンが利益に直結する術だと理解していても、なかなか前に進めることができない状況。そんな時は、newjiのコストダウン自動化機能で大きく利益貢献しよう!
(Β版非公開)