- お役立ち記事
- Unveiling Japan’s Secrets to Cost Reduction: Transforming Manufacturing with “コストダウン”
月間77,185名の
製造業ご担当者様が閲覧しています*
*2025年2月28日現在のGoogle Analyticsのデータより
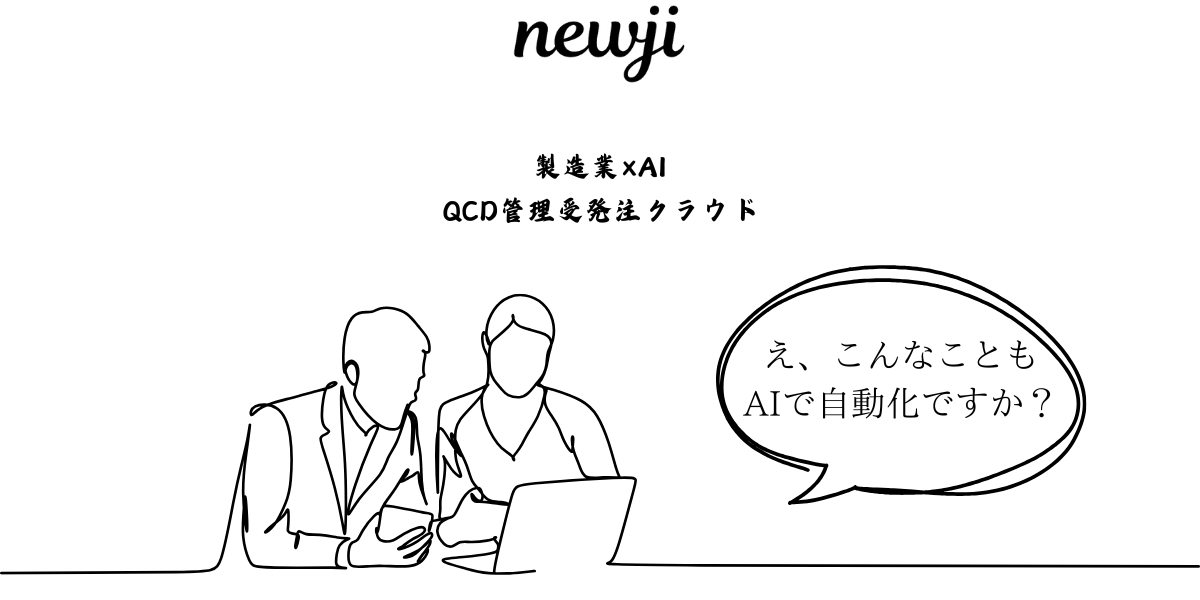
Unveiling Japan’s Secrets to Cost Reduction: Transforming Manufacturing with “コストダウン”
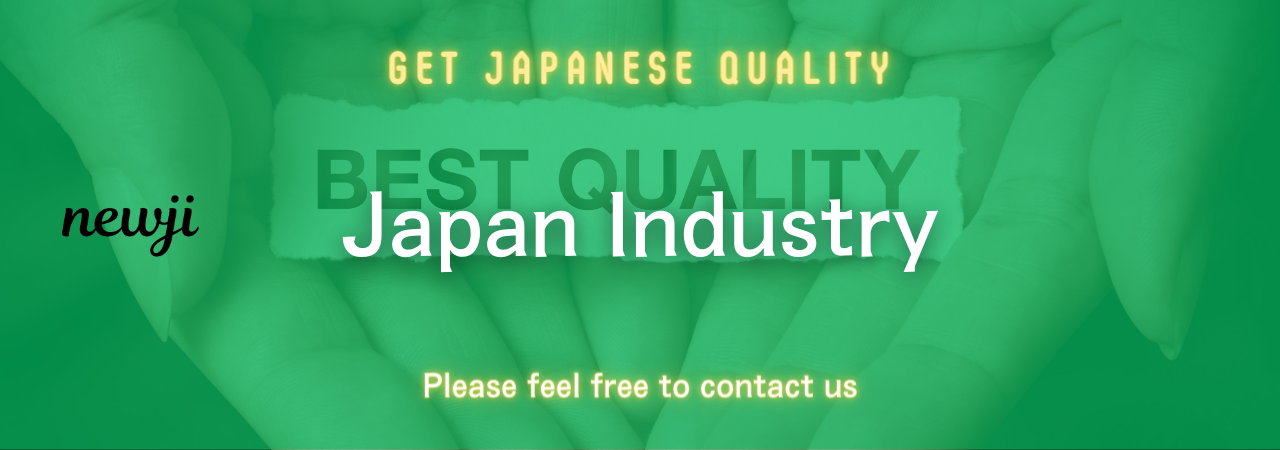
目次
Introduction to コストダウン: Japan’s Approach to Cost Reduction
Achieving cost reduction is a critical objective for manufacturers worldwide.
Japan has long been recognized for its effective cost reduction strategies, collectively known as コストダウン.
These strategies have transformed the manufacturing landscape, enabling companies to enhance efficiency and maintain competitiveness.
Understanding Japan’s approach to cost reduction offers valuable insights for businesses aiming to optimize their operations.
The Fundamentals of コストダウン
コストダウン, or cost down, is a systematic approach to reducing production costs without compromising quality.
Rooted in the principles of continuous improvement, コストダウン emphasizes efficiency and waste elimination.
This method integrates various techniques across procurement, production, and logistics, creating a cohesive strategy for cost management.
By focusing on incremental improvements, コストダウン ensures sustainable cost reductions over time.
Key Principles of コストダウン
The foundation of コストダウン lies in several key principles.
First, it prioritizes the elimination of waste, aligning with the Lean Manufacturing philosophy.
Second, it fosters collaboration between suppliers and manufacturers to identify cost-saving opportunities.
Third, it emphasizes data-driven decision-making to ensure that cost reduction efforts are effective and measurable.
By adhering to these principles, companies can achieve meaningful and lasting cost reductions.
Advantages of Implementing コストダウン
Adopting コストダウン strategies offers numerous benefits to manufacturing companies.
One significant advantage is enhanced competitiveness in the global market.
Cost savings enable companies to offer more attractive pricing to customers, thereby increasing market share.
Additionally, コストダウン fosters innovation by encouraging the exploration of more efficient manufacturing processes and materials.
This focus on innovation not only reduces costs but also improves product quality and performance.
Operational Efficiency
Operational efficiency is a direct benefit of コストダウン.
By streamlining processes and eliminating unnecessary steps, manufacturers can reduce production times and lower operational costs.
This efficiency translates to faster turnaround times and the ability to respond more swiftly to market demands.
Improved Supplier Relationships
Implementing コストダウン requires close collaboration with suppliers.
This collaboration leads to stronger relationships, as suppliers become partners in the cost reduction process.
Mutual trust and open communication enhance the ability to negotiate better terms and identify joint cost-saving opportunities.
Challenges and Disadvantages
While コストダウン offers substantial benefits, it also presents certain challenges.
One primary challenge is the potential for reduced flexibility in the supply chain.
Strict cost control measures may limit the ability to adapt to sudden market changes or unforeseen disruptions.
Additionally, the emphasis on cost reduction must not compromise product quality, which is paramount in maintaining customer satisfaction and brand reputation.
Risk of Quality Compromise
Maintaining high-quality standards is essential.
A focus solely on cost reduction can inadvertently lead to the selection of lower-quality materials or processes.
This compromise can have long-term negative effects on product reliability and customer trust.
Implementation Complexity
Implementing コストダウン requires a comprehensive and coordinated approach across multiple departments.
The complexity of integrating cost reduction strategies with existing processes can be a barrier, particularly for larger organizations with established workflows.
Supplier Negotiation Techniques
Effective supplier negotiation is a cornerstone of successful コストダウン.
Japanese suppliers are known for their collaborative approach, which aligns well with the principles of コストダウン.
Several negotiation techniques can be employed to achieve mutual cost reductions.
Building Long-Term Partnerships
Establishing long-term relationships with suppliers fosters trust and cooperation.
This partnership approach encourages suppliers to invest in improvements that benefit both parties, leading to sustainable cost reductions.
Volume Consolidation
Consolidating purchase volumes can provide leverage in negotiations.
By committing to larger order quantities, manufacturers can negotiate better pricing terms, achieving significant cost savings.
Shared Cost-Saving Initiatives
Collaborating on cost-saving initiatives, such as jointly investing in new technologies or optimizing logistics, can lead to shared benefits.
These initiatives enhance efficiency and reduce costs for both the manufacturer and the supplier.
Market Conditions and コストダウン
Understanding current market conditions is vital for effective コストダウン implementation.
Economic fluctuations, material price volatility, and global supply chain dynamics all influence cost reduction strategies.
Economic Factors
Economic downturns often necessitate stricter cost control measures.
Manufacturers must adapt their コストダウン strategies to navigate economic challenges while maintaining operational stability.
Global Supply Chain Dynamics
Global supply chain disruptions, such as those caused by geopolitical tensions or natural disasters, can impact cost structures.
Flexible コストダウン strategies that account for such disruptions are essential for maintaining cost efficiency.
Best Practices for Effective コストダウン
Implementing コストダウン successfully requires adherence to best practices that ensure comprehensive and sustainable cost reductions.
Continuous Improvement Culture
Promoting a culture of continuous improvement encourages all employees to contribute to cost reduction efforts.
Empowering individuals at every level to identify and address inefficiencies fosters a proactive approach to コストダウン.
Data-Driven Decision Making
Utilizing data analytics to monitor cost performance and identify trends is crucial.
Data-driven insights enable informed decision-making and the prioritization of cost-saving initiatives with the greatest potential impact.
Cross-Functional Collaboration
Encouraging collaboration across departments ensures that cost reduction strategies are integrated and aligned with overall business objectives.
Cross-functional teams can address cost challenges from multiple perspectives, leading to more effective solutions.
Case Studies: Success Stories in コストダウン
Examining real-world examples of successful コストダウン implementation provides valuable lessons and inspiration for other manufacturers.
Automotive Industry
A leading Japanese automotive manufacturer implemented コストダウン by optimizing its supply chain and renegotiating supplier contracts.
Through these efforts, the company achieved a 15% reduction in production costs while maintaining high quality standards.
This success allowed the company to reinvest savings into research and development, further enhancing its competitive edge.
Electronics Manufacturing
An electronics manufacturer employed コストダウン strategies by adopting lean manufacturing techniques and automating key processes.
These initiatives resulted in a 20% increase in operational efficiency and a significant decrease in labor costs.
The company’s ability to swiftly adapt to changing market demands improved, contributing to sustained growth.
Tools and Technologies Supporting コストダウン
Advanced tools and technologies play a crucial role in facilitating コストダウン initiatives.
From data analytics platforms to automation systems, the right technology can significantly enhance cost reduction efforts.
Lean Manufacturing Software
Lean manufacturing software assists in identifying and eliminating waste within production processes.
These tools provide real-time insights into operational performance, enabling timely interventions to optimize efficiency.
Enterprise Resource Planning (ERP) Systems
ERP systems integrate various business functions, providing a unified view of operations.
This integration facilitates better decision-making and resource allocation, essential for effective コストダウン.
Automation and Robotics
Automation and robotics streamline production processes, reducing labor costs and minimizing errors.
Implementing these technologies supports コストダウン by enhancing precision and increasing production capacity.
Measuring the Impact of コストダウン
To ensure that コストダウン efforts are effective, it is essential to measure their impact systematically.
This involves tracking key performance indicators (KPIs) and assessing the outcomes of cost reduction initiatives.
Key Performance Indicators
Common KPIs for measuring コストダウン effectiveness include cost per unit, production time, and waste reduction metrics.
Monitoring these indicators provides a clear picture of how cost reduction strategies are performing and identifies areas for further improvement.
Regular Audits and Reviews
Conducting regular audits and reviews of cost reduction initiatives ensures that they remain aligned with business goals.
These assessments help in identifying any deviations from desired outcomes and allow for timely adjustments to strategies.
The Future of コストダウン in Japanese Manufacturing
As the global manufacturing landscape evolves, so too will the principles and practices of コストダウン.
Emerging technologies, shifting market dynamics, and changing consumer expectations will shape future cost reduction strategies.
Embracing Digital Transformation
Digital transformation will continue to drive コストダウン, with advancements in artificial intelligence, machine learning, and the Internet of Things (IoT).
These technologies enable more precise and efficient operations, paving the way for further cost reductions.
Sustainability and コストダウン
Sustainable manufacturing practices are becoming increasingly important.
Integrating sustainability with コストダウン not only reduces costs but also addresses environmental concerns, aligning with global sustainability goals.
Global Collaboration
Expanding global collaboration will enhance コストダウン efforts.
Leveraging international partnerships and knowledge exchange can lead to innovative cost reduction techniques and shared best practices.
Conclusion: Leveraging Japanese コストダウン for Global Manufacturing Success
Japan’s コストダウン strategies offer a robust framework for achieving cost reduction in manufacturing.
By embracing the principles of continuous improvement, fostering strong supplier relationships, and leveraging advanced technologies, manufacturers can transform their operations.
Adapting these strategies to fit specific business contexts will enable companies to enhance efficiency, maintain quality, and achieve sustained competitiveness in the global market.
資料ダウンロード
QCD管理受発注クラウド「newji」は、受発注部門で必要なQCD管理全てを備えた、現場特化型兼クラウド型の今世紀最高の受発注管理システムとなります。
ユーザー登録
受発注業務の効率化だけでなく、システムを導入することで、コスト削減や製品・資材のステータス可視化のほか、属人化していた受発注情報の共有化による内部不正防止や統制にも役立ちます。
NEWJI DX
製造業に特化したデジタルトランスフォーメーション(DX)の実現を目指す請負開発型のコンサルティングサービスです。AI、iPaaS、および先端の技術を駆使して、製造プロセスの効率化、業務効率化、チームワーク強化、コスト削減、品質向上を実現します。このサービスは、製造業の課題を深く理解し、それに対する最適なデジタルソリューションを提供することで、企業が持続的な成長とイノベーションを達成できるようサポートします。
製造業ニュース解説
製造業、主に購買・調達部門にお勤めの方々に向けた情報を配信しております。
新任の方やベテランの方、管理職を対象とした幅広いコンテンツをご用意しております。
お問い合わせ
コストダウンが利益に直結する術だと理解していても、なかなか前に進めることができない状況。そんな時は、newjiのコストダウン自動化機能で大きく利益貢献しよう!
(β版非公開)