- お役立ち記事
- Unveiling the Mystery of Coating Defects: A Deep Dive into Japanese Manufacturing Practices
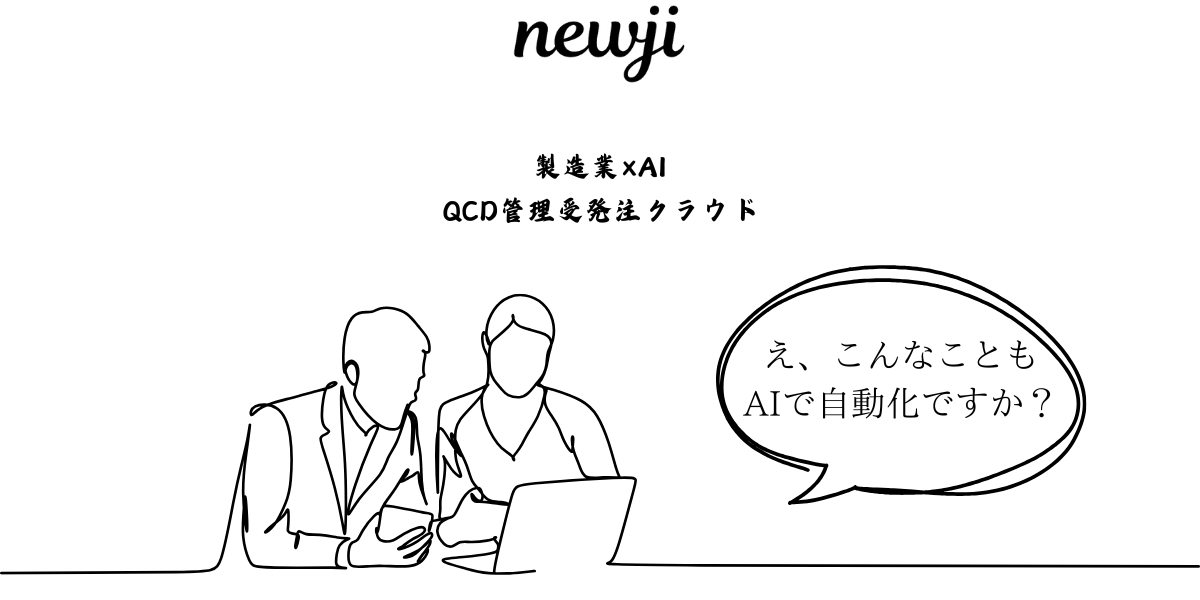
Unveiling the Mystery of Coating Defects: A Deep Dive into Japanese Manufacturing Practices
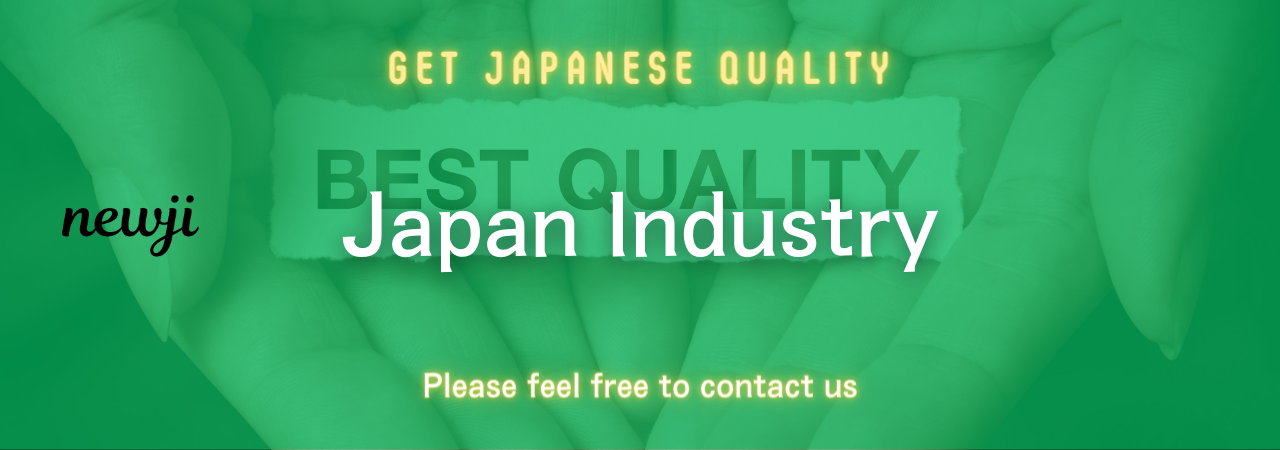
目次
Introduction
Coating defects can significantly impact the quality and durability of manufactured products. Understanding the root causes and effective prevention strategies is crucial for maintaining high standards in production. Japanese manufacturing practices are renowned for their meticulous approach to quality control, making them a valuable source of knowledge for addressing coating defects. This article delves into the intricacies of coating defects, explores Japanese manufacturing methodologies, and provides actionable insights for procurement and purchasing professionals aiming to enhance their processes and collaborate effectively with Japanese suppliers.
Understanding Coating Defects
Common Types of Coating Defects
Coating defects manifest in various forms, each affecting the final product’s appearance and performance differently. The most common types include:
– **Blistering:** Formation of bubbles or blisters within the coating due to trapped solvents or moisture.
– **Cracking:** Development of cracks in the coating caused by incorrect application techniques or environmental stresses.
– **Peeling:** Detachment of the coating from the substrate, often resulting from poor adhesion or surface contamination.
– **Chalking:** Surface degradation leading to a powdery residue, typically caused by UV exposure or improper formulation.
– **Orange Peel Texture:** Uneven surface appearance resembling the skin of an orange, usually resulting from inconsistencies in application.
Causes of Coating Defects
Several factors contribute to coating defects, including:
– **Surface Preparation:** Inadequate cleaning or roughness of the substrate can hinder proper adhesion.
– **Environmental Conditions:** Temperature and humidity fluctuations during application can affect drying and curing processes.
– **Application Techniques:** Incorrect spray patterns, inconsistent thickness, or improper equipment settings can lead to defects.
– **Material Quality:** Poor-quality coatings or incompatible materials may fail to perform as expected.
– **Curing Processes:** Insufficient or excessive curing times can compromise the coating’s integrity.
Japanese Manufacturing Practices for Quality Control
Kaizen Philosophy
Kaizen, meaning “continuous improvement,” is a fundamental principle in Japanese manufacturing. It emphasizes incremental enhancements in processes, efficiency, and quality. By fostering a culture where every employee is encouraged to suggest improvements, companies can systematically reduce the incidence of coating defects.
Total Quality Management (TQM)
TQM is an all-encompassing approach that seeks to embed quality in every aspect of the manufacturing process. It involves rigorous quality planning, control, assurance, and improvement. In the context of coatings, TQM ensures that each layer meets strict standards, thereby minimizing defects.
Just-In-Time (JIT) Production
JIT production focuses on reducing inventory costs and increasing efficiency by receiving goods only as they are needed in the production process. This approach allows for better control over the materials used in coatings, ensuring that high-quality inputs are consistently available, which helps in reducing defects.
Advantages of Japanese Manufacturing in Coatings
Precision and Attention to Detail
Japanese manufacturers are renowned for their meticulous attention to detail. This precision ensures that every step in the coating process is executed flawlessly, significantly reducing the likelihood of defects.
Advanced Technology and Automation
Japan leads in adopting cutting-edge technologies and automation in manufacturing. Automated coating systems ensure consistent application, precise control of parameters, and real-time monitoring, all of which contribute to minimizing defects.
Strong Supplier Relationships
Japanese companies often foster long-term, collaborative relationships with their suppliers. This partnership approach ensures that suppliers are aligned with quality standards and are proactive in addressing potential issues that could lead to coating defects.
Disadvantages and Challenges
High Initial Costs
Implementing advanced technologies and rigorous quality control measures can entail significant upfront investments. For some companies, the high initial costs may pose a barrier to adopting Japanese manufacturing practices.
Rigid Processes
The structured nature of Japanese manufacturing processes can sometimes lead to rigidity. While this ensures consistency, it may limit flexibility and adaptability in dynamic market conditions.
Cultural and Communication Barriers
Differences in business culture and communication styles can present challenges when collaborating with Japanese suppliers. Misunderstandings or misalignments can potentially impact the effectiveness of quality control measures.
Supplier Negotiation Techniques with Japanese Suppliers
Building Trust and Long-term Relationships
Japanese business culture places a high value on trust and long-term relationships. Building a strong rapport with suppliers involves consistent communication, reliability, and demonstrating a commitment to mutual success.
Understanding Cultural Nuances
Awareness of Japanese business etiquette and cultural practices is crucial. This includes respectful communication, understanding the importance of hierarchy, and being patient during negotiations.
Effective Communication Strategies
Clear and transparent communication is key. Utilizing bilingual professionals or translation services can help bridge language gaps, ensuring that quality requirements and expectations are clearly conveyed and understood.
Market Conditions Impacting Coating Defects
Global Supply Chain Issues
Disruptions in the global supply chain, such as delays in material shipments or shortages of raw materials, can affect the quality of coatings. Ensuring a resilient supply chain is essential for maintaining consistent quality.
Raw Material Quality and Availability
The availability and quality of raw materials directly influence the performance of coatings. Collaborating with reliable suppliers who prioritize high-quality materials is vital for reducing defects.
Technological Advancements
Continuous advancements in coating technologies offer new solutions for preventing defects. Staying abreast of technological developments can provide opportunities to enhance coating processes and quality.
Best Practices in Procurement and Purchasing for Quality Coatings
Supplier Selection and Evaluation
Selecting suppliers who adhere to stringent quality standards is paramount. Implementing a robust evaluation process that assesses suppliers’ capabilities, certifications, and quality control mechanisms ensures that only the best partners are chosen.
Regular Quality Audits
Conducting regular quality audits helps in monitoring suppliers’ compliance with quality standards. Audits can identify potential issues early, allowing for timely interventions to prevent defects.
Collaborative Development with Suppliers
Working collaboratively with suppliers in the development phase can lead to improved coating formulations and processes. Joint innovation initiatives foster shared responsibility for quality outcomes, reducing the incidence of defects.
Case Studies: Successful Japanese Practices in Reducing Coating Defects
Automotive Industry
In the automotive sector, Japanese manufacturers like Toyota have implemented stringent quality control measures. By integrating advanced automated coating systems and adopting Kaizen principles, Toyota has minimized coating defects, ensuring high-quality finishes on their vehicles.
Electronics Manufacturing
Japanese electronics companies, such as Sony, leverage TQM to maintain exceptional quality standards. Regular training programs for employees and continuous monitoring of coating processes have resulted in minimal defects and enhanced product reliability.
Conclusion
Addressing coating defects requires a comprehensive understanding of the factors that contribute to them and the implementation of effective quality control measures. Japanese manufacturing practices, with their emphasis on continuous improvement, precision, and strong supplier relationships, offer valuable lessons for procurement and purchasing professionals. By adopting best practices in supplier selection, fostering collaborative relationships, and leveraging advanced technologies, companies can significantly reduce coating defects and enhance the overall quality of their products. Embracing these methodologies not only improves product outcomes but also strengthens the competitive edge in the global market.
資料ダウンロード
QCD調達購買管理クラウド「newji」は、調達購買部門で必要なQCD管理全てを備えた、現場特化型兼クラウド型の今世紀最高の購買管理システムとなります。
ユーザー登録
調達購買業務の効率化だけでなく、システムを導入することで、コスト削減や製品・資材のステータス可視化のほか、属人化していた購買情報の共有化による内部不正防止や統制にも役立ちます。
NEWJI DX
製造業に特化したデジタルトランスフォーメーション(DX)の実現を目指す請負開発型のコンサルティングサービスです。AI、iPaaS、および先端の技術を駆使して、製造プロセスの効率化、業務効率化、チームワーク強化、コスト削減、品質向上を実現します。このサービスは、製造業の課題を深く理解し、それに対する最適なデジタルソリューションを提供することで、企業が持続的な成長とイノベーションを達成できるようサポートします。
オンライン講座
製造業、主に購買・調達部門にお勤めの方々に向けた情報を配信しております。
新任の方やベテランの方、管理職を対象とした幅広いコンテンツをご用意しております。
お問い合わせ
コストダウンが利益に直結する術だと理解していても、なかなか前に進めることができない状況。そんな時は、newjiのコストダウン自動化機能で大きく利益貢献しよう!
(Β版非公開)