- お役立ち記事
- “Unveiling the Secrets of Japanese OEM Manufacturing: How Art and Innovation Drive Success”
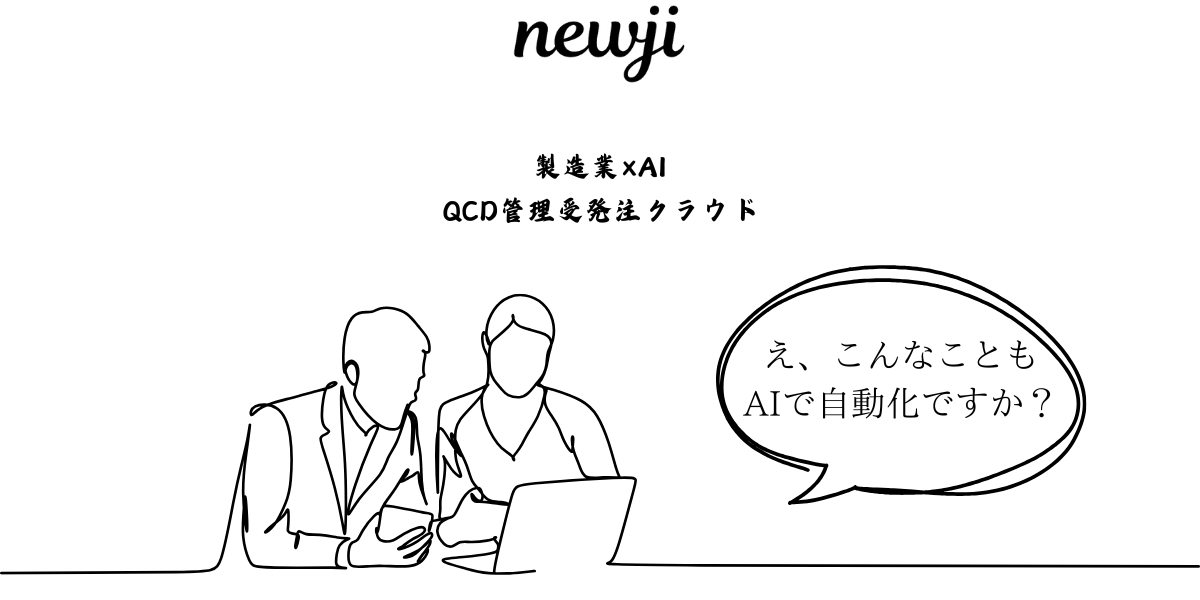
“Unveiling the Secrets of Japanese OEM Manufacturing: How Art and Innovation Drive Success”
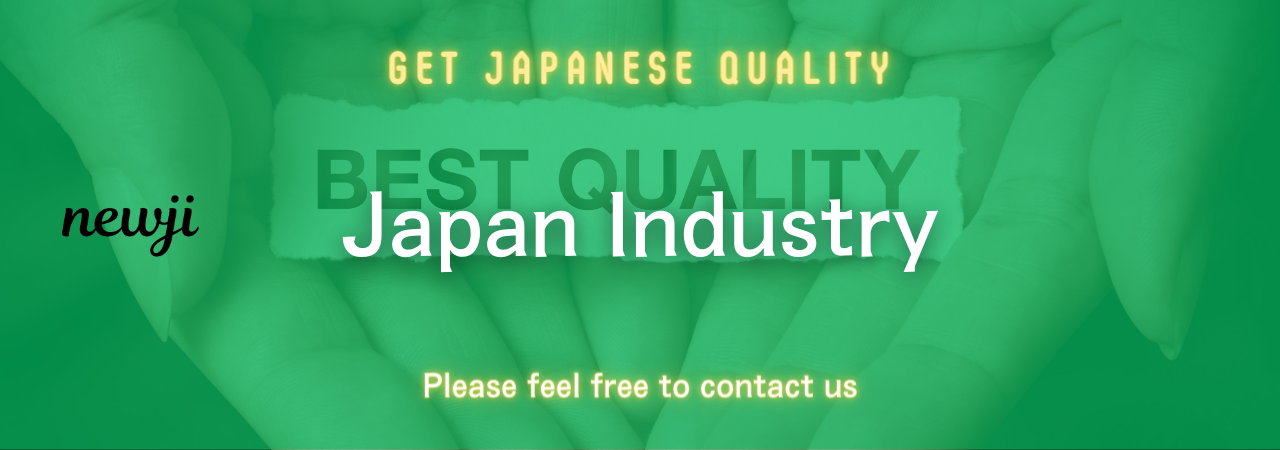
目次
Introduction to Japanese OEM Manufacturing
Japanese Original Equipment Manufacturing (OEM) has long been revered for its precision, quality, and innovation. Companies worldwide seek partnerships with Japanese manufacturers to harness their expertise in producing high-quality components and finished products. This article delves into the secrets behind the success of Japanese OEM manufacturing, exploring how art and innovation intertwine to create industry-leading products.
The Pillars of Japanese OEM Success
Commitment to Quality
Quality is the cornerstone of Japanese manufacturing. The concept of “Kaizen,” or continuous improvement, is deeply ingrained in the Japanese manufacturing ethos. OEM manufacturers in Japan strive for perfection in every aspect, from the selection of raw materials to the final inspection of products. This unwavering commitment ensures that products meet the highest standards, reducing defects and enhancing customer satisfaction.
Emphasis on Precision and Detail
Japanese OEM manufacturers are known for their meticulous attention to detail. Precision engineering ensures that every component fits perfectly, functioning seamlessly within the larger assembly. This level of detail not only improves product performance but also extends the lifespan of the products, providing value to end-users.
Integration of Art and Innovation
Japanese manufacturing seamlessly integrates artistic design with cutting-edge technology. This fusion results in products that are not only functional but also aesthetically pleasing. Innovation drives the development of new manufacturing techniques and materials, enabling OEM manufacturers to stay ahead of market trends and customer demands.
Advantages of Partnering with Japanese OEM Manufacturers
Superior Quality Control
Japanese OEM manufacturers implement rigorous quality control processes. From the initial design phase to final production, each step is meticulously monitored to ensure adherence to quality standards. This minimizes the risk of defects and ensures that the final product meets or exceeds customer expectations.
Advanced Technology and Automation
Japan is at the forefront of manufacturing technology. OEM manufacturers utilize advanced machinery and automation to enhance production efficiency and precision. This not only increases output but also reduces production costs, making Japanese OEM partnerships economically advantageous.
Strong Supplier Relationships
Japanese OEM manufacturers value long-term relationships with suppliers. This collaborative approach fosters trust and ensures a steady supply of high-quality materials. Strong supplier relationships also enable manufacturers to respond swiftly to market changes and customer needs.
Focus on Sustainability
Sustainability is a key focus in Japanese manufacturing. OEM manufacturers implement eco-friendly practices, such as reducing waste, recycling materials, and minimizing energy consumption. This commitment to sustainability not only benefits the environment but also aligns with the values of increasingly eco-conscious consumers.
Challenges and Considerations in Japanese OEM Manufacturing
Cultural Differences
Navigating cultural differences is essential when partnering with Japanese OEM manufacturers. Understanding Japanese business etiquette, communication styles, and decision-making processes can facilitate smoother collaborations and prevent misunderstandings.
Higher Initial Costs
While Japanese OEM manufacturers offer high-quality products, the initial costs may be higher compared to other regions. However, the long-term benefits of superior quality, durability, and reduced defects often offset the higher upfront investment.
Language Barriers
Language differences can pose challenges in communication and negotiations. It’s crucial to have skilled translators or bilingual representatives to ensure clear and effective communication, preventing misinterpretations and ensuring that project requirements are accurately conveyed.
Lead Times
Japanese OEM manufacturers may have longer lead times due to their meticulous production processes. Planning ahead and establishing clear timelines can help manage expectations and ensure timely delivery of products.
Effective Supplier Negotiation Techniques
Building Trust and Long-Term Relationships
Japanese business culture emphasizes trust and long-term relationships. Investing time in building rapport and demonstrating commitment can lead to more favorable negotiation outcomes and stronger partnerships.
Understanding Mutual Benefits
Successful negotiations involve understanding and addressing the needs of both parties. Highlighting how the partnership can create value for both the buyer and the manufacturer fosters a collaborative negotiation environment.
Focusing on Quality and Value
Emphasizing the importance of quality and value over cost alone resonates with Japanese manufacturers. Demonstrating a commitment to maintaining high standards can lead to better terms and a more collaborative relationship.
Clear Communication of Expectations
Clearly outlining project requirements, quality standards, and timelines ensures that both parties have a mutual understanding. Detailed contracts and written agreements help prevent misunderstandings and set clear expectations.
Market Conditions Influencing Japanese OEM Manufacturing
Global Supply Chain Disruptions
Recent global events have highlighted the vulnerability of supply chains. Japanese OEM manufacturers have adapted by diversifying their supplier base and investing in resilient supply chain strategies to minimize disruptions and ensure continuity.
Technological Advancements
Rapid advancements in technology, such as automation and artificial intelligence, are transforming Japanese OEM manufacturing. Embracing these technologies enhances production efficiency, precision, and the ability to innovate continuously.
Changing Consumer Demands
Consumer preferences are evolving towards more sustainable and customizable products. Japanese OEM manufacturers are responding by integrating eco-friendly practices and offering flexible production options to meet diverse customer needs.
Competitive Landscape
The competitive landscape is becoming increasingly intense, with manufacturers worldwide striving to offer superior products. Japanese OEM manufacturers maintain their competitive edge through relentless focus on quality, innovation, and customer satisfaction.
Best Practices for Engaging with Japanese OEM Manufacturers
Conduct Thorough Research
Before entering into a partnership, conduct comprehensive research on potential Japanese OEM manufacturers. Assess their reputation, quality standards, technological capabilities, and financial stability to ensure they align with your business objectives.
Establish Clear Communication Channels
Effective communication is critical for successful collaborations. Utilize clear and consistent communication channels, and consider employing bilingual staff or professional translators to bridge language gaps.
Develop a Detailed Agreement
A well-defined agreement outlines the scope of work, quality standards, timelines, payment terms, and other critical aspects of the partnership. A detailed contract helps prevent disputes and ensures that both parties are aligned in their expectations.
Foster a Collaborative Relationship
Approach the partnership with a collaborative mindset. Engage in regular meetings, share insights, and work together to solve challenges. A strong, cooperative relationship enhances trust and leads to better outcomes.
Invest in Long-Term Partnerships
View the relationship as a long-term partnership rather than a transactional arrangement. Investing in the relationship can lead to mutual growth, continuous improvement, and sustained success for both parties.
Leveraging Japanese Manufacturing Techniques for Success
Implementing Lean Manufacturing
Japanese OEM manufacturers excel in lean manufacturing, which focuses on eliminating waste, optimizing processes, and improving efficiency. Adopting lean principles can enhance your own manufacturing operations, leading to cost savings and improved productivity.
Adopting Just-In-Time (JIT) Production
JIT production minimizes inventory costs by aligning production schedules closely with demand. This approach reduces waste and ensures that resources are utilized efficiently, contributing to a more responsive and agile manufacturing process.
Embracing Total Quality Management (TQM)
TQM is a comprehensive approach to quality management that involves all members of an organization in improving processes, products, and services. Implementing TQM fosters a culture of continuous improvement and excellence.
Utilizing Advanced Automation and Robotics
Japanese OEM manufacturers leverage advanced automation and robotics to enhance precision, consistency, and efficiency in production. Integrating these technologies into your own operations can boost production capabilities and reduce human error.
Fostering Innovation through Cross-Functional Teams
Encouraging collaboration across different departments and disciplines fosters innovation. Cross-functional teams can generate diverse ideas and solutions, driving the development of innovative products and manufacturing techniques.
Conclusion: Embracing the Art and Innovation of Japanese OEM Manufacturing
Japanese OEM manufacturing stands as a testament to the power of combining art and innovation in producing exceptional products. By embracing the principles of quality, precision, and continuous improvement, Japanese manufacturers have set benchmarks in the global market. For businesses seeking to leverage these strengths, forming strategic partnerships with Japanese OEM manufacturers can unlock new levels of quality, efficiency, and innovation. Understanding the advantages, navigating the challenges, and adopting best practices are essential steps toward harnessing the full potential of Japanese OEM manufacturing. As the global market continues to evolve, the integration of art and innovation in manufacturing will remain a key driver of success, exemplified by the enduring legacy of Japanese OEM manufacturers.
資料ダウンロード
QCD調達購買管理クラウド「newji」は、調達購買部門で必要なQCD管理全てを備えた、現場特化型兼クラウド型の今世紀最高の購買管理システムとなります。
ユーザー登録
調達購買業務の効率化だけでなく、システムを導入することで、コスト削減や製品・資材のステータス可視化のほか、属人化していた購買情報の共有化による内部不正防止や統制にも役立ちます。
NEWJI DX
製造業に特化したデジタルトランスフォーメーション(DX)の実現を目指す請負開発型のコンサルティングサービスです。AI、iPaaS、および先端の技術を駆使して、製造プロセスの効率化、業務効率化、チームワーク強化、コスト削減、品質向上を実現します。このサービスは、製造業の課題を深く理解し、それに対する最適なデジタルソリューションを提供することで、企業が持続的な成長とイノベーションを達成できるようサポートします。
オンライン講座
製造業、主に購買・調達部門にお勤めの方々に向けた情報を配信しております。
新任の方やベテランの方、管理職を対象とした幅広いコンテンツをご用意しております。
お問い合わせ
コストダウンが利益に直結する術だと理解していても、なかなか前に進めることができない状況。そんな時は、newjiのコストダウン自動化機能で大きく利益貢献しよう!
(Β版非公開)