- お役立ち記事
- Unveiling the Secrets of “War Page”: Navigating Warpage in Japanese Manufacturing Industries
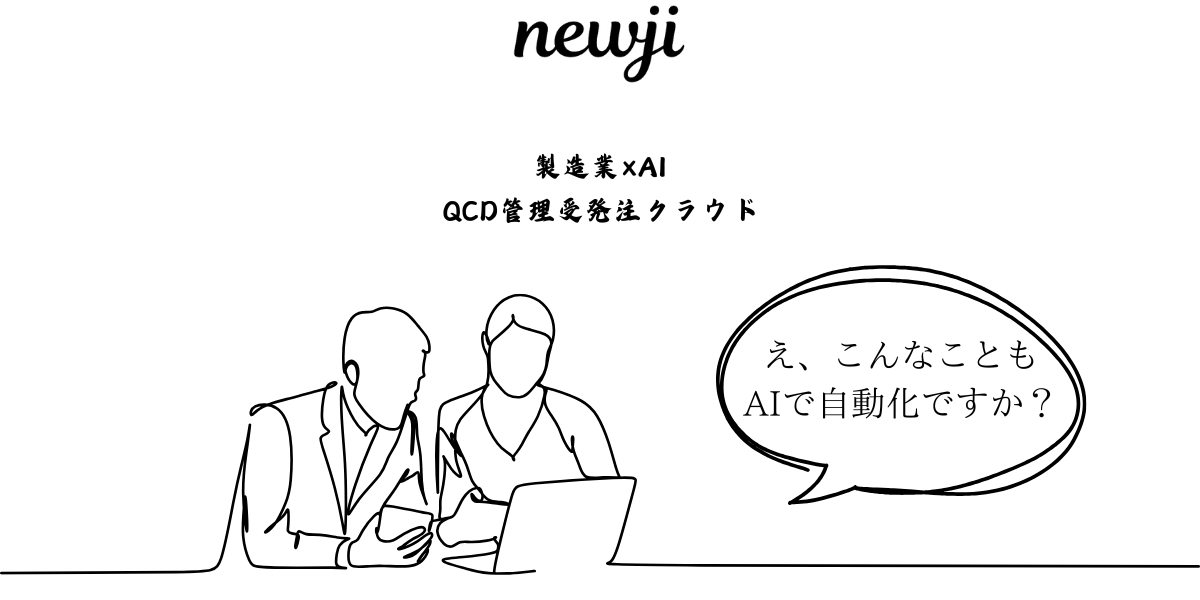
Unveiling the Secrets of “War Page”: Navigating Warpage in Japanese Manufacturing Industries
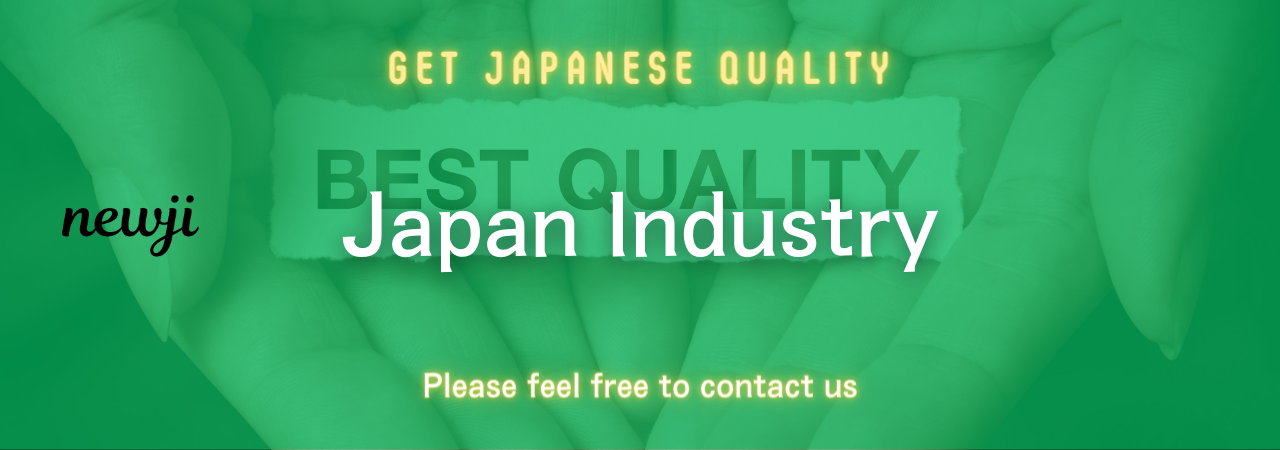
目次
Understanding Warpage in Japanese Manufacturing
Warpage is a critical issue in the manufacturing industry that affects the quality and integrity of products.
In Japanese manufacturing, the approach to managing warpage is both sophisticated and highly efficient.
This section delves into the fundamental aspects of warpage and its implications within Japanese manufacturing industries.
By comprehending these basics, procurement and purchasing professionals can better navigate challenges related to warpage.
Definition and Causes of Warpage
Warpage refers to the deformation of a material or component from its original shape.
This distortion can occur due to various factors during the manufacturing process.
Common causes include uneven cooling, residual stresses from processing, and material inconsistencies.
In Japanese manufacturing, meticulous control over these factors is essential to minimize warpage.
Understanding the underlying causes is the first step in effectively addressing warpage issues.
Impact of Warpage on Product Quality
Warpage can significantly affect the functionality and aesthetic appeal of a product.
In precision industries such as automotive and electronics, even minor warpage can lead to performance issues.
Japanese manufacturers prioritize minimizing warpage to maintain high product standards.
For procurement professionals, ensuring that suppliers adhere to these quality standards is paramount.
High-quality products reduce the risk of returns and enhance customer satisfaction.
Advantages of Japanese Manufacturing Practices in Managing Warpage
Japanese manufacturing is renowned for its efficiency and quality control.
These practices offer numerous advantages, especially in managing warpage.
This section explores the key benefits that make Japanese manufacturers leaders in this area.
Advanced Technology and Automation
Japanese manufacturers invest heavily in cutting-edge technology and automation.
These advancements enable precise control over the manufacturing process, reducing the likelihood of warpage.
Automated systems ensure consistent processing conditions, which are critical in preventing deformation.
For procurement and purchasing, partnering with technologically advanced suppliers translates to higher quality products and fewer defects.
Lean Manufacturing and Continuous Improvement
Lean manufacturing principles are deeply ingrained in Japanese production systems.
This approach emphasizes the elimination of waste and continuous improvement.
By systematically analyzing and refining processes, Japanese manufacturers effectively mitigate warpage issues.
Continuous improvement initiatives ensure that manufacturing processes adapt to new challenges and maintain high standards over time.
Strong Supplier Relationships and Collaboration
Japanese manufacturers value strong relationships with their suppliers.
This collaborative approach fosters open communication and shared goals.
By working closely with suppliers, manufacturers can address warpage concerns proactively.
For procurement professionals, establishing similar collaborative relationships is essential for achieving consistent quality and reliability.
Challenges and Disadvantages in Japanese Manufacturing
While Japanese manufacturing practices offer significant advantages, there are also challenges and potential disadvantages.
Understanding these aspects is crucial for procurement and purchasing professionals to navigate the complexities of working with Japanese suppliers.
High Initial Costs
Japanese manufacturing often involves substantial initial investments in technology and training.
These costs can be higher compared to manufacturers from other regions.
For businesses, this may result in higher procurement costs initially.
However, the long-term benefits of reduced defects and higher quality can offset these initial expenses.
Cultural and Communication Barriers
Cultural differences can pose challenges in communication and business practices.
Understanding and respecting Japanese business etiquette is essential for successful negotiations and partnerships.
Misunderstandings can arise if cultural nuances are not adequately addressed.
Effective communication strategies and cultural training can help bridge these gaps.
Strict Quality Standards
Japanese manufacturers uphold very high-quality standards.
While this ensures superior products, it can lead to stringent requirements from suppliers.
Procurement professionals must ensure that all specifications and quality criteria are consistently met.
Failure to comply can result in delays and increased costs due to the need for rework or replacement.
Supplier Negotiation Techniques with Japanese Manufacturers
Negotiating with Japanese suppliers requires a strategic approach that aligns with their business practices and cultural expectations.
This section outlines effective negotiation techniques to foster successful partnerships.
Building Trust and Long-Term Relationships
Trust is a cornerstone of Japanese business relationships.
Negotiations should emphasize long-term collaboration rather than short-term gains.
Demonstrating reliability and commitment to mutual success helps in establishing a strong foundation.
Building trust can lead to more favorable terms and greater flexibility in negotiations.
Emphasizing Quality and Precision
Japanese manufacturers prioritize quality and precision in their products.
Negotiations should highlight the importance of these factors and how they align with your company’s standards.
Demonstrating an understanding of their quality control processes can facilitate smoother negotiations.
Additionally, discussing how warpage issues will be managed shows a commitment to maintaining high standards.
Patience and Respect in Communication
Japanese business culture values patience and respect.
Negotiations may take longer as decisions involve consensus and thorough evaluation.
Maintaining a respectful and patient demeanor can positively influence negotiation outcomes.
Avoiding aggressive tactics and allowing time for deliberation fosters a more cooperative atmosphere.
Market Conditions Affecting Warpage Management in Japan
Understanding the current market conditions in Japan is essential for effective procurement and purchasing strategies.
This section examines factors that influence how Japanese manufacturers manage warpage.
Technological Advancements
Japan is at the forefront of technological innovation in manufacturing.
Ongoing advancements in materials science and manufacturing processes continue to improve warpage management.
Staying informed about these technological trends can help procurement professionals anticipate changes and adapt strategies accordingly.
Regulatory Environment
Japan’s regulatory framework sets high standards for product quality and safety.
These regulations influence how manufacturers approach warpage and other quality issues.
Compliance with these regulations ensures that products meet both domestic and international standards.
Procurement professionals must be aware of these regulatory requirements to ensure that their suppliers are compliant.
Economic Factors
Economic conditions, such as labor costs and supply chain dynamics, impact manufacturing practices.
Fluctuations in these factors can affect how Japanese manufacturers manage warpage.
Understanding the economic landscape helps in predicting potential challenges and sourcing strategies.
Best Practices for Managing Warpage in Procurement and Purchasing
Implementing best practices is crucial for effectively managing warpage in procurement and purchasing.
This section outlines strategies that can help achieve optimal outcomes.
Comprehensive Supplier Evaluation
Conducting thorough evaluations of potential suppliers is essential.
Assess their capabilities in managing warpage, including their quality control processes and technological expertise.
Request detailed information about their manufacturing processes and warpage mitigation strategies.
This evaluation helps in selecting suppliers that can consistently deliver high-quality products.
Clear Communication of Specifications
Clearly communicating product specifications and quality requirements is vital.
Detail the acceptable levels of warpage and the standards to be met.
Providing comprehensive documentation reduces the risk of misunderstandings and ensures that suppliers are aligned with your expectations.
Regular communication also facilitates addressing any issues promptly.
Implementing Quality Assurance Programs
Establishing robust quality assurance programs helps in monitoring and controlling warpage.
Regular inspections and testing can identify warpage issues early in the production process.
Collaborate with suppliers to implement continuous quality improvement initiatives.
These programs contribute to maintaining high product quality and minimizing defects.
Fostering Collaborative Relationships
Building collaborative relationships with suppliers fosters mutual improvement.
Share knowledge and best practices related to warpage management.
Joint problem-solving efforts can lead to innovative solutions and enhanced quality control.
A collaborative approach promotes a shared commitment to excellence and continuous improvement.
Leveraging Data and Analytics
Utilizing data and analytics can significantly enhance warpage management.
Analyze historical data to identify patterns and predict potential warpage issues.
Implementing data-driven strategies allows for proactive measures and informed decision-making.
Advanced analytics can also support continuous improvement initiatives by providing actionable insights.
Case Studies: Successful Warpage Management in Japanese Manufacturing
Examining real-world examples helps illustrate effective warpage management practices.
This section presents case studies of Japanese manufacturers that have successfully navigated warpage challenges.
Automotive Component Manufacturing
A leading Japanese automotive component manufacturer faced significant warpage issues in its plastic parts.
By investing in advanced injection molding technologies and implementing stringent quality control measures, the company reduced warpage rates by 30%.
Collaborative efforts with suppliers to standardize processes and share best practices were instrumental in achieving these results.
This case highlights the importance of technology and collaboration in managing warpage.
Electronics Assembly
A Japanese electronics assembly company struggled with warpage in printed circuit boards (PCBs).
The company adopted comprehensive thermal management strategies and improved material selection.
Regular training programs for staff on warpage prevention techniques also contributed to the reduction of defects.
As a result, the company achieved higher reliability in its products and strengthened its market position.
This example underscores the role of process optimization and employee training in addressing warpage.
Precision Machinery Manufacturing
A precision machinery manufacturer in Japan dealt with warpage in critical machine components.
By implementing a rigorous supplier evaluation process and fostering long-term partnerships, the manufacturer ensured that only suppliers with proven warpage mitigation capabilities were engaged.
The company also utilized real-time monitoring systems to detect and address warpage during production.
These measures led to a significant improvement in product quality and customer satisfaction.
This case demonstrates the effectiveness of supplier management and real-time monitoring in managing warpage.
Strategies for Continuous Improvement in Warpage Management
Continuous improvement is essential for maintaining high standards in warpage management.
This section explores strategies that support ongoing enhancements in procurement and purchasing practices.
Adopting Lean Six Sigma Methodologies
Lean Six Sigma provides a structured approach to process improvement.
Applying these methodologies can help identify root causes of warpage and implement effective solutions.
For procurement professionals, integrating Lean Six Sigma practices enhances the ability to manage quality and efficiency in the supply chain.
Investing in Training and Development
Ongoing training for both procurement teams and suppliers ensures that best practices are understood and implemented.
Educational programs on warpage prevention techniques and quality control methods contribute to sustained improvements.
Investing in human capital fosters a culture of excellence and continuous learning.
Enhancing Cross-Functional Collaboration
Encouraging collaboration between different departments, such as procurement, engineering, and quality control, facilitates comprehensive warpage management.
Cross-functional teams can address complex challenges more effectively by leveraging diverse expertise.
This holistic approach supports the development of integrated solutions that enhance overall product quality.
Utilizing Advanced Monitoring Tools
Implementing advanced monitoring and diagnostic tools aids in the early detection of warpage issues.
Real-time data collection and analysis enable proactive management and timely interventions.
These tools not only improve quality but also provide valuable insights for continuous process optimization.
Future Trends in Warpage Management within Japanese Manufacturing
Staying ahead of future trends is crucial for maintaining competitive advantage in warpage management.
This section explores emerging developments that will shape the landscape of Japanese manufacturing.
Integration of Artificial Intelligence and Machine Learning
AI and machine learning are revolutionizing warpage management by enabling predictive analytics and automated quality control.
These technologies can analyze vast amounts of data to identify patterns and predict potential warpage issues.
Integrating AI-driven solutions enhances the ability to prevent defects and improve overall manufacturing efficiency.
Sustainable Manufacturing Practices
Sustainability is becoming increasingly important in manufacturing.
Japanese manufacturers are adopting eco-friendly materials and processes that also contribute to reducing warpage.
Sustainable practices not only minimize environmental impact but also enhance product quality and reduce costs in the long term.
Customization and Flexibility in Production
The demand for customized products requires flexible manufacturing systems.
Japanese manufacturers are developing adaptable processes that can quickly adjust to varying specifications without compromising on quality.
This flexibility is crucial for managing warpage in diverse product lines and meeting the evolving needs of the market.
Enhanced Supply Chain Integration
Advanced supply chain integration facilitates better coordination and information sharing among all stakeholders.
This seamless connectivity enables more effective management of warpage by ensuring consistency and quality throughout the supply chain.
Enhanced integration supports faster response times and more efficient problem-solving in the face of warpage challenges.
Conclusion
Navigating warpage in Japanese manufacturing industries requires a comprehensive understanding of both the technical and strategic aspects involved.
By leveraging advanced technologies, fostering strong supplier relationships, and implementing best practices, procurement and purchasing professionals can effectively manage warpage challenges.
Moreover, staying informed about market conditions and embracing continuous improvement strategies ensures sustained success.
The expertise demonstrated by Japanese manufacturers in handling warpage serves as a model for achieving high-quality standards and operational excellence.
Adopting these insights can lead to significant benefits in procurement efficiency, product quality, and overall business performance.
資料ダウンロード
QCD調達購買管理クラウド「newji」は、調達購買部門で必要なQCD管理全てを備えた、現場特化型兼クラウド型の今世紀最高の購買管理システムとなります。
ユーザー登録
調達購買業務の効率化だけでなく、システムを導入することで、コスト削減や製品・資材のステータス可視化のほか、属人化していた購買情報の共有化による内部不正防止や統制にも役立ちます。
NEWJI DX
製造業に特化したデジタルトランスフォーメーション(DX)の実現を目指す請負開発型のコンサルティングサービスです。AI、iPaaS、および先端の技術を駆使して、製造プロセスの効率化、業務効率化、チームワーク強化、コスト削減、品質向上を実現します。このサービスは、製造業の課題を深く理解し、それに対する最適なデジタルソリューションを提供することで、企業が持続的な成長とイノベーションを達成できるようサポートします。
オンライン講座
製造業、主に購買・調達部門にお勤めの方々に向けた情報を配信しております。
新任の方やベテランの方、管理職を対象とした幅広いコンテンツをご用意しております。
お問い合わせ
コストダウンが利益に直結する術だと理解していても、なかなか前に進めることができない状況。そんな時は、newjiのコストダウン自動化機能で大きく利益貢献しよう!
(Β版非公開)