- お役立ち記事
- Usage and Maintenance Procedures of Lapping Technology in Manufacturing
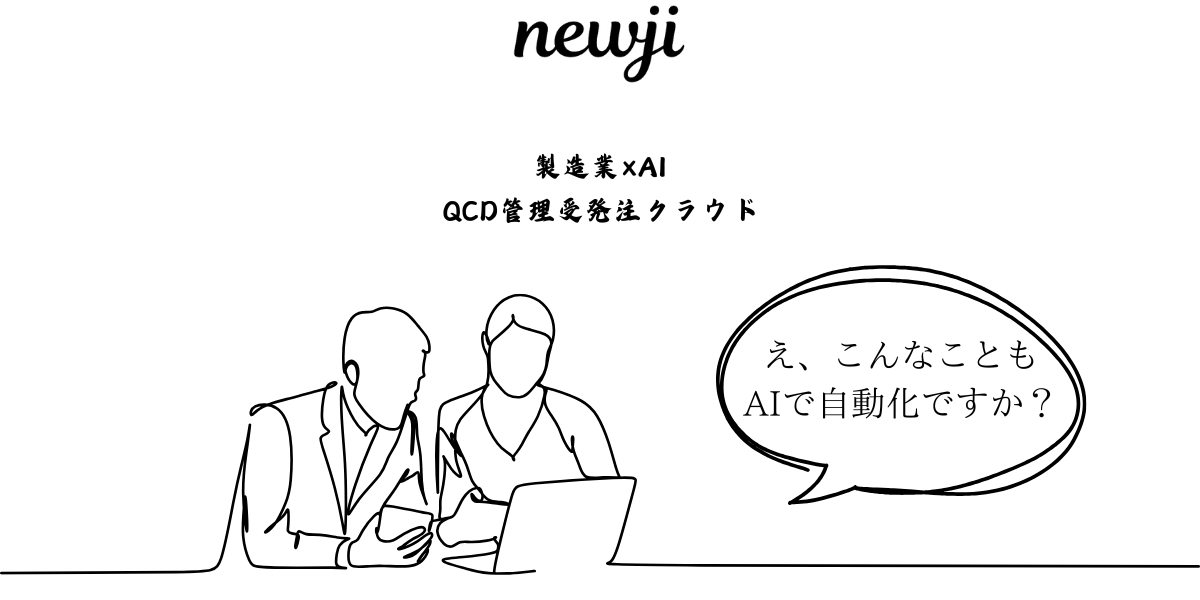
Usage and Maintenance Procedures of Lapping Technology in Manufacturing
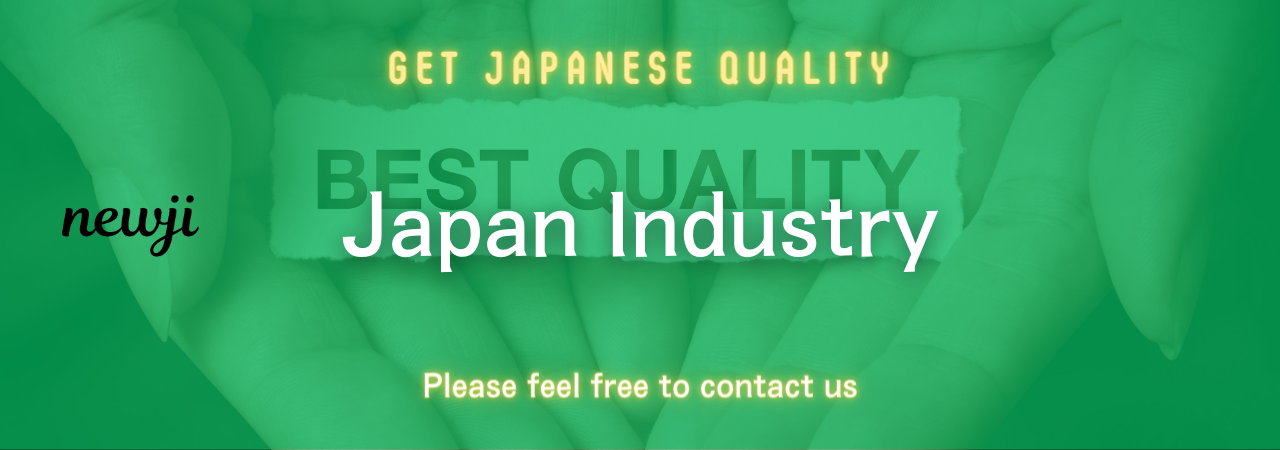
Lapping technology plays a crucial role in the manufacturing industry.
It helps in producing extremely precise and smooth surfaces on various materials.
Understanding the usage and maintenance procedures of lapping technology is essential for maintaining efficiency and achieving the desired quality in manufacturing processes.
目次
Understanding Lapping Technology
Lapping is a finishing process that involves the abrasive machining of a surface using a lap, which is typically made of soft material like cast iron, copper, or a similar soft metal.
The lap is infused with abrasive particles that remove material from the workpiece through friction.
This process allows for unparalleled precision in surface flatness and surface finish.
Applications of Lapping Technology
Lapping technology is employed in numerous industries, including automotive, aerospace, electronics, and semiconductor manufacturing.
In the automotive industry, for instance, lapping is used to achieve precise tolerances in engine components like valves and gears.
In the electronics field, it is used to produce flat surfaces for semiconductor wafers and optical components.
The versatility of lapping makes it indispensable in producing high-quality components with exact specifications.
How Lapping Technology Works
Lapping involves several key components: the lap, the abrasive slurry, and the workpiece.
The interaction between these components ensures the removal of material and the creation of a fine surface.
Below are the steps typically followed in a lapping process:
1. Preparation of the Workpiece
Before lapping, the workpiece must be prepared.
This involves cleaning and ensuring that it is free from debris and contaminants, which could interfere with the lapping process.
Proper preparation helps in achieving a uniformly smooth surface.
2. Selecting the Suitable Lap
Choosing the appropriate lap material is critical.
The material should be soft enough to hold the abrasive particles but also durable enough to withstand the process.
Common lap materials include cast iron, copper, and glass.
3. Application of Abrasive Slurry
A slurry containing abrasive particles is applied to the lap.
The choice of abrasive material and its grit size depends on the desired surface finish and material removal rate.
Common abrasives used in lapping include diamond, aluminum oxide, and silicon carbide.
4. Execution of the Lapping Process
The workpiece is placed on the lap, and pressure is applied.
The lap moves in a circular or figure-eight motion to ensure even material removal.
The process continues until the desired surface flatness and finish are achieved.
Frequent checks are performed to measure progress and make adjustments as needed.
Maintenance Procedures for Lapping Technology
Proper maintenance is critical to ensure the longevity and efficiency of lapping machines.
Regular maintenance not only helps in maintaining the quality of the finished products but also extends the lifespan of the equipment.
1. Regular Cleaning
Lapping machines should be cleaned regularly to remove any residual abrasive slurry and debris.
This prevents contamination and ensures consistent performance.
Use appropriate cleaning agents that do not damage the machine components.
2. Lap Maintenance
The condition of the lap is paramount.
Inspect the lap regularly for wear and tear.
If the lap surface becomes uneven, it may need to be resurfaced or replaced to maintain the quality of the lapping process.
3. Checking Abrasive Slurry
The abrasive slurry should be monitored for consistency and effectiveness.
Over time, the abrasive particles can break down and lose their effectiveness.
Replace the slurry as necessary to maintain optimal performance.
4. Machine Calibration
Regular calibration of the lapping machine ensures that it operates within its specified parameters.
Check and adjust the pressure settings, motion paths, and other controls to ensure precision and accuracy.
5. Scheduled Inspections
Implement a schedule for routine inspections of the entire lapping system.
Check for any signs of wear, misalignment, or other issues that could affect the machine’s performance.
Early detection of problems allows for timely repairs and prevents costly breakdowns.
Benefits of Proper Usage and Maintenance
Adhering to proper usage and maintenance procedures offers several benefits for both the manufacturing process and the end product.
Enhanced Product Quality
Proper lapping ensures that the final product meets the required specifications for surface finish and flatness.
This results in higher-quality products that perform better and have longer service lives.
Increased Efficiency
Maintaining the lapping equipment in peak condition reduces downtime and increases productivity.
Efficient machines can complete tasks more quickly and accurately.
Cost Savings
Regular maintenance and proper usage extend the lifespan of the lapping equipment.
This reduces the need for frequent replacements and repairs, leading to significant cost savings over time.
Improved Safety
Well-maintained machines are safer to operate.
Regular inspections and timely repairs prevent accidents and ensure the safety of the operators.
Conclusion
Lapping technology is essential in various manufacturing industries for achieving precise and smooth surfaces.
Understanding its applications, operational steps, and maintenance procedures is crucial for maximizing its benefits.
By following proper usage and maintenance practices, manufacturers can ensure high product quality, increased efficiency, cost savings, and improved safety.
Embracing these practices will contribute to the continued success and reliability of lapping technology in manufacturing processes.
資料ダウンロード
QCD調達購買管理クラウド「newji」は、調達購買部門で必要なQCD管理全てを備えた、現場特化型兼クラウド型の今世紀最高の購買管理システムとなります。
ユーザー登録
調達購買業務の効率化だけでなく、システムを導入することで、コスト削減や製品・資材のステータス可視化のほか、属人化していた購買情報の共有化による内部不正防止や統制にも役立ちます。
NEWJI DX
製造業に特化したデジタルトランスフォーメーション(DX)の実現を目指す請負開発型のコンサルティングサービスです。AI、iPaaS、および先端の技術を駆使して、製造プロセスの効率化、業務効率化、チームワーク強化、コスト削減、品質向上を実現します。このサービスは、製造業の課題を深く理解し、それに対する最適なデジタルソリューションを提供することで、企業が持続的な成長とイノベーションを達成できるようサポートします。
オンライン講座
製造業、主に購買・調達部門にお勤めの方々に向けた情報を配信しております。
新任の方やベテランの方、管理職を対象とした幅広いコンテンツをご用意しております。
お問い合わせ
コストダウンが利益に直結する術だと理解していても、なかなか前に進めることができない状況。そんな時は、newjiのコストダウン自動化機能で大きく利益貢献しよう!
(Β版非公開)