- お役立ち記事
- Using Management Accounting for Effective Factory Management
月間76,176名の
製造業ご担当者様が閲覧しています*
*2025年3月31日現在のGoogle Analyticsのデータより
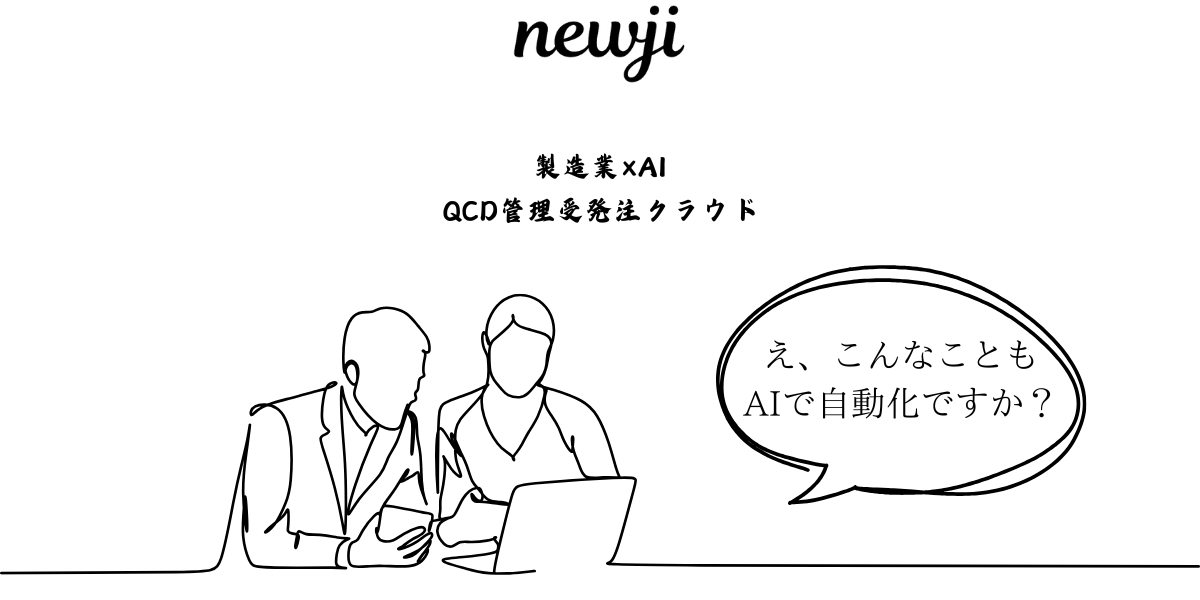
Using Management Accounting for Effective Factory Management
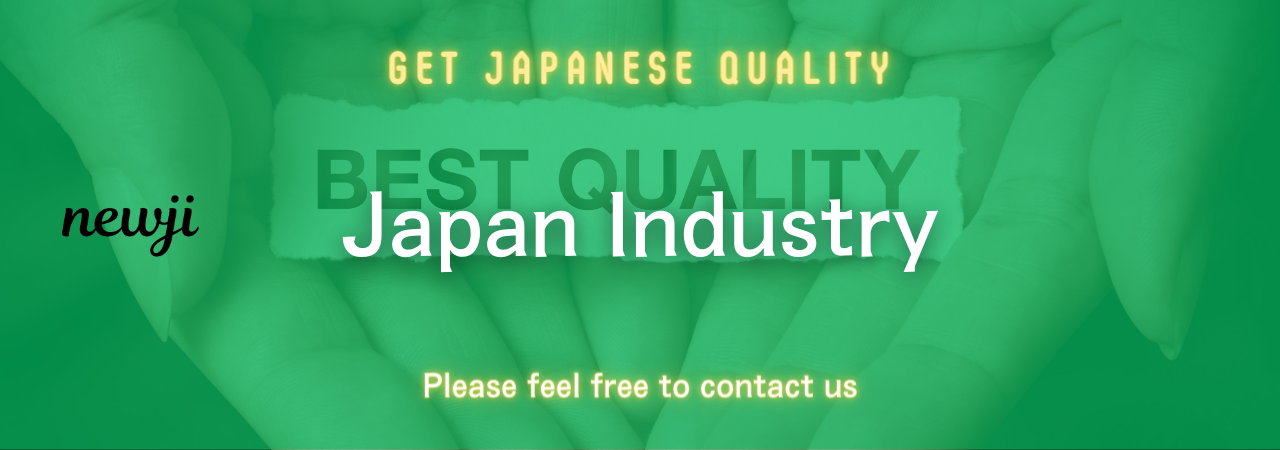
Managing a factory efficiently requires a keen understanding of both production processes and financial metrics. Management accounting plays a critical role in providing the necessary data to make informed decisions. This approach can drive productivity, reduce costs, and enhance overall operational success. Let’s delve into how management accounting can be leveraged for effective factory management.
目次
Understanding Management Accounting
Management accounting differs from financial accounting in that it focuses on internal processes rather than external reporting. Its primary purpose is to supply managers with the information they need to make strategic decisions. While financial accounting is mandated by regulatory bodies and standardized formats, management accounting is more flexible. It customizes reports and data analysis to support the specific needs of management.
Components of Management Accounting
Several key elements make up management accounting. Cost accounting, budgeting, performance evaluation, and financial forecasting are integral components. Together, they provide a comprehensive picture of a factory’s operational efficiency.
Cost Accounting
Cost accounting involves tracking, recording, and analyzing all costs associated with production. This includes direct costs like raw materials and labor, as well as indirect costs such as overhead. By understanding these costs, managers can identify areas where expenses can be minimized without compromising quality.
Budgeting
Budgeting is crucial for planning and controlling factory operations. A well-prepared budget outlines the expected revenue and expenses over a specific period. It serves as a financial roadmap, enabling managers to allocate resources effectively. Regularly comparing actual performance against the budget can highlight variances and prompt corrective actions.
Performance Evaluation
Key performance indicators (KPIs) are metrics used to gauge the factory’s efficiency. These indicators might include production rates, scrap rates, machine utilization, and labor productivity. Regular performance evaluations ensure that managers stay informed about operational strengths and weaknesses.
Financial Forecasting
Forecasting involves predicting future financial conditions based on historical data and market trends. Accurate forecasts enable managers to anticipate challenges and opportunities, making proactive adjustments to plans and strategies. This predictive capability is vital for long-term sustainability.
Applications of Management Accounting in Factory Management
Effective use of management accounting can transform factory operations. Here are some practical applications that highlight its importance in factory management.
Optimizing Production Processes
Through cost accounting, managers can pinpoint inefficiencies in production lines. For instance, if a particular process is unusually expensive, it could signal the need for process re-engineering or investment in more efficient machinery. Identifying and eliminating bottlenecks leads to smoother operations and reduced waste.
Enhancing Product Pricing
Accurate cost accounting is key to setting appropriate product prices. Managers can determine the cost of production for each unit, including both direct and indirect costs. This information aids in pricing products competitively while ensuring profitability. It also allows managers to assess the financial impact of potential changes in production volume.
Improving Inventory Management
Management accounting helps in maintaining optimal inventory levels. By analyzing inventory turnover ratios, managers can decide when to reorder materials, preventing stockouts or overstock situations. Effective inventory management reduces holding costs and ensures a smoother production flow.
Labor Cost Control
Labor is a significant expense in factory operations. Management accounting tools can track labor costs in real-time and compare them against budgets. This data helps managers adjust staffing levels, reduce overtime, and implement more efficient labor practices.
Challenges in Implementing Management Accounting
While the benefits are substantial, there are challenges associated with implementing management accounting. These challenges must be addressed to fully reap the advantages.
Data Accuracy
The effectiveness of management accounting depends on the quality of the data collected. Inaccurate or incomplete data can lead to flawed analyses and poor decision-making. It’s essential to invest in reliable data collection systems and train staff to maintain high data standards.
Integration with Existing Systems
Factories often use various software and tools for different functions. Integrating management accounting systems with existing production and inventory management systems can be complex and costly. Seamless integration is crucial for comprehensive data analysis and reporting.
Staff Training
Understanding and utilizing management accounting tools requires a certain level of expertise. Adequate training should be provided to ensure that staff can interpret and use the data effectively. Without proper training, the potential benefits of management accounting might not be fully realized.
Conclusion
Management accounting offers invaluable insights that can significantly enhance factory management. By focusing on cost control, budgeting, performance evaluation, and financial forecasting, managers can make informed decisions that drive efficiency and profitability.
Despite the challenges, the strategic implementation of management accounting can lead to improved production processes, better pricing strategies, efficient inventory management, and controlled labor costs. Investing in reliable data collection, integrating systems, and training staff will overcome most obstacles.
Ultimately, embracing management accounting as a fundamental part of factory management will pave the way for long-term operational success and competitiveness.
資料ダウンロード
QCD管理受発注クラウド「newji」は、受発注部門で必要なQCD管理全てを備えた、現場特化型兼クラウド型の今世紀最高の受発注管理システムとなります。
ユーザー登録
受発注業務の効率化だけでなく、システムを導入することで、コスト削減や製品・資材のステータス可視化のほか、属人化していた受発注情報の共有化による内部不正防止や統制にも役立ちます。
NEWJI DX
製造業に特化したデジタルトランスフォーメーション(DX)の実現を目指す請負開発型のコンサルティングサービスです。AI、iPaaS、および先端の技術を駆使して、製造プロセスの効率化、業務効率化、チームワーク強化、コスト削減、品質向上を実現します。このサービスは、製造業の課題を深く理解し、それに対する最適なデジタルソリューションを提供することで、企業が持続的な成長とイノベーションを達成できるようサポートします。
製造業ニュース解説
製造業、主に購買・調達部門にお勤めの方々に向けた情報を配信しております。
新任の方やベテランの方、管理職を対象とした幅広いコンテンツをご用意しております。
お問い合わせ
コストダウンが利益に直結する術だと理解していても、なかなか前に進めることができない状況。そんな時は、newjiのコストダウン自動化機能で大きく利益貢献しよう!
(β版非公開)