- お役立ち記事
- Utilization and challenges of small-lot production, which holds the key to reducing purchasing costs Practical methods from the purchasing department’s perspective
Utilization and challenges of small-lot production, which holds the key to reducing purchasing costs Practical methods from the purchasing department’s perspective
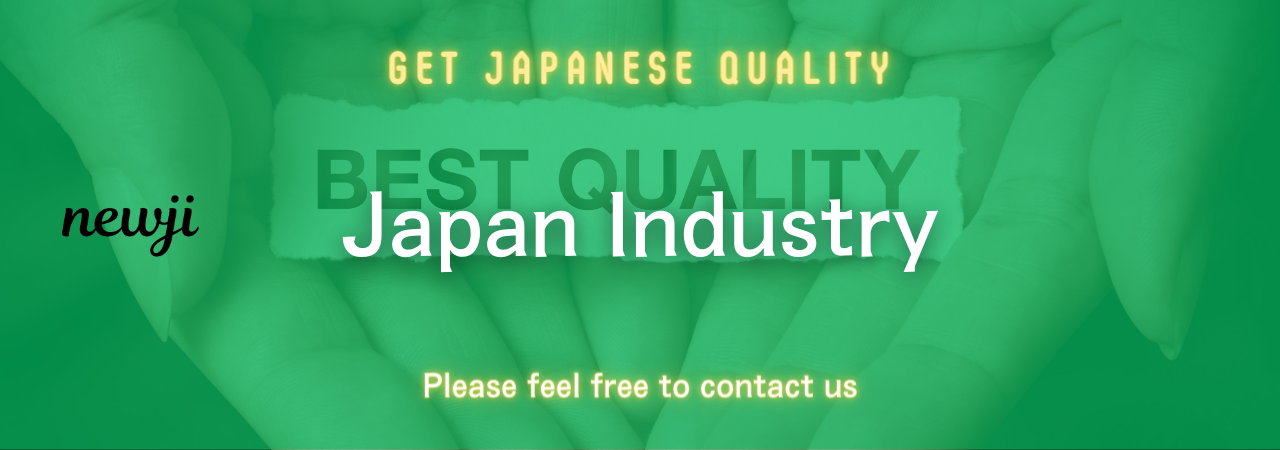
目次
Introduction to Small-Lot Production
Small-lot production is a manufacturing process where products are made in limited quantities, rather than in large volumes.
This method is increasingly gaining attention, especially because it offers various advantages over traditional mass production approaches.
For businesses, understanding and leveraging small-lot production can be a key strategy to reduce purchasing costs effectively.
However, like any other manufacturing strategy, it comes with its own set of challenges that organizations need to address.
Understanding the Benefits
One of the primary benefits of small-lot production is the reduction in inventory costs.
By producing only what is necessary, companies can minimize excess stock and related storage expenses.
This not only aids in improving cash flow but also reduces the risk of holding obsolete inventory.
Additionally, small-lot production can lead to enhanced product quality.
Since production runs are smaller, there is an increased opportunity for quality checks and corrections.
This ensures that the final product meets the desired standards and customer expectations, reducing returns and dissatisfaction.
Furthermore, adapting quickly to market demands is crucial in today’s fast-paced environment.
Small-lot production allows companies to be more flexible, adapting to changing customer needs and preferences rapidly.
This agility in manufacturing can be a significant competitive advantage.
The Role of the Purchasing Department
The purchasing department plays a crucial role in the successful implementation of small-lot production.
By collaborating closely with suppliers, they can negotiate favorable terms that align with the smaller production volumes.
This may involve securing better pricing and flexible delivery schedules to match the production rhythm.
Moreover, the purchasing department must focus on building strong relationships with suppliers.
Trust and effective communication are paramount to ensure suppliers can adjust their production processes accordingly.
Strong supplier relationships provide the purchasing team with strategic advantages like priority deliveries and first-hand information about material availability.
Strategic Sourcing
Strategic sourcing is essential when engaging in small-lot production.
It involves selecting suppliers who can offer high-quality materials at competitive prices while being adaptable to changing order volumes.
Purchasing professionals must assess supplier reliability, lead times, and their capacity to scale production up or down as needed.
By leveraging strategic sourcing, the purchasing department can significantly reduce costs while maintaining or enhancing product quality.
This approach requires continuous market research to identify alternative suppliers who can provide better value.
Challenges of Small-Lot Production
While the advantages are clear, small-lot production presents several challenges that must be addressed.
One of the main hurdles is the potential for increased per-unit costs.
Producing smaller quantities may reduce the efficiency of scale, leading to higher individual product costs.
This makes it imperative for organizations to carefully calculate and manage production expenses to ensure profitability.
Additionally, managing frequent production setup changes can be complex and time-consuming.
This requires detailed planning and coordination to minimize disruptions and maintain operational efficiency.
Every change in production setup must be meticulously managed to prevent errors and delays.
Another challenge is maintaining supplier relationships under the pressure of fluctuating order sizes.
Some suppliers may prefer larger, consistent orders.
Thus, it’s crucial to maintain clear communication and negotiate terms that are mutually beneficial.
Quality Control
Quality control can be more demanding in small-lot production due to the higher frequency of design and process changes.
Continuous quality checks are necessary to ensure consistency and adherence to standards.
Implementing robust quality assurance procedures can mitigate the risk of defects and maintain product quality.
Practical Methods for Overcoming Challenges
To overcome the challenges associated with small-lot production, several practical methods can be employed.
First, investments in technology can streamline and optimize the production process.
Automation and data analytics can increase efficiency, reduce manual errors, and provide insights into production performance.
Second, fostering a culture of continuous improvement within the organization encourages employees to identify areas of inefficiency and suggest improvements.
This proactive approach can enhance operational processes and quality.
Third, cross-functional collaboration is essential.
Departments such as production, purchasing, and sales must work closely to align strategies and ensure that the entire supply chain is optimized for small-lot production.
Effective Communication
Effective communication within and outside the organization is crucial.
Regular meetings with suppliers to review performance and discuss future plans can strengthen relationships and improve collaboration.
Internally, ensuring that all teams are aligned with the strategic goals of small-lot production will enhance coordination and execution.
Conclusion
Small-lot production offers a pathway to reduced purchasing costs and increased flexibility.
While it presents challenges like per-unit cost increases and supplier management complexities, these can be effectively managed with strategic planning and innovative approaches.
By empowering the purchasing department with the right tools and methodologies, and fostering collaboration across the organization, businesses can fully leverage the potential of small-lot production.
This approach not only enhances cost efficiency but also positions companies to respond swiftly to market changes and consumer demands.
資料ダウンロード
QCD調達購買管理クラウド「newji」は、調達購買部門で必要なQCD管理全てを備えた、現場特化型兼クラウド型の今世紀最高の購買管理システムとなります。
ユーザー登録
調達購買業務の効率化だけでなく、システムを導入することで、コスト削減や製品・資材のステータス可視化のほか、属人化していた購買情報の共有化による内部不正防止や統制にも役立ちます。
NEWJI DX
製造業に特化したデジタルトランスフォーメーション(DX)の実現を目指す請負開発型のコンサルティングサービスです。AI、iPaaS、および先端の技術を駆使して、製造プロセスの効率化、業務効率化、チームワーク強化、コスト削減、品質向上を実現します。このサービスは、製造業の課題を深く理解し、それに対する最適なデジタルソリューションを提供することで、企業が持続的な成長とイノベーションを達成できるようサポートします。
オンライン講座
製造業、主に購買・調達部門にお勤めの方々に向けた情報を配信しております。
新任の方やベテランの方、管理職を対象とした幅広いコンテンツをご用意しております。
お問い合わせ
コストダウンが利益に直結する術だと理解していても、なかなか前に進めることができない状況。そんな時は、newjiのコストダウン自動化機能で大きく利益貢献しよう!
(Β版非公開)