- お役立ち記事
- Utilization of aluminum deep drawing technology: Collaborative partnership incorporating new manufacturing technology
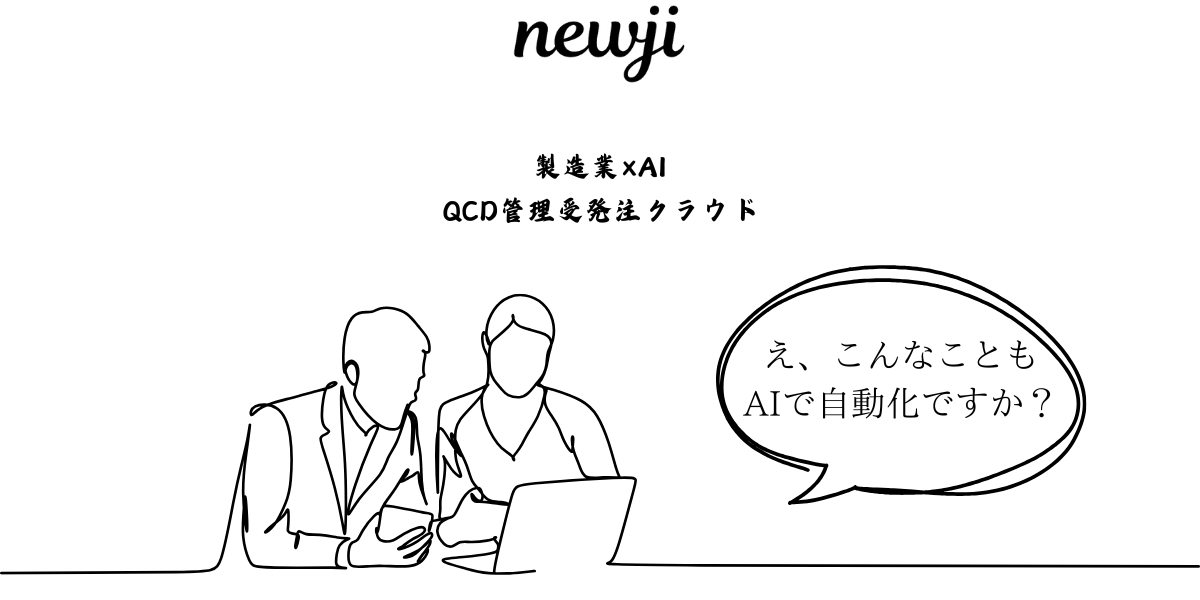
Utilization of aluminum deep drawing technology: Collaborative partnership incorporating new manufacturing technology
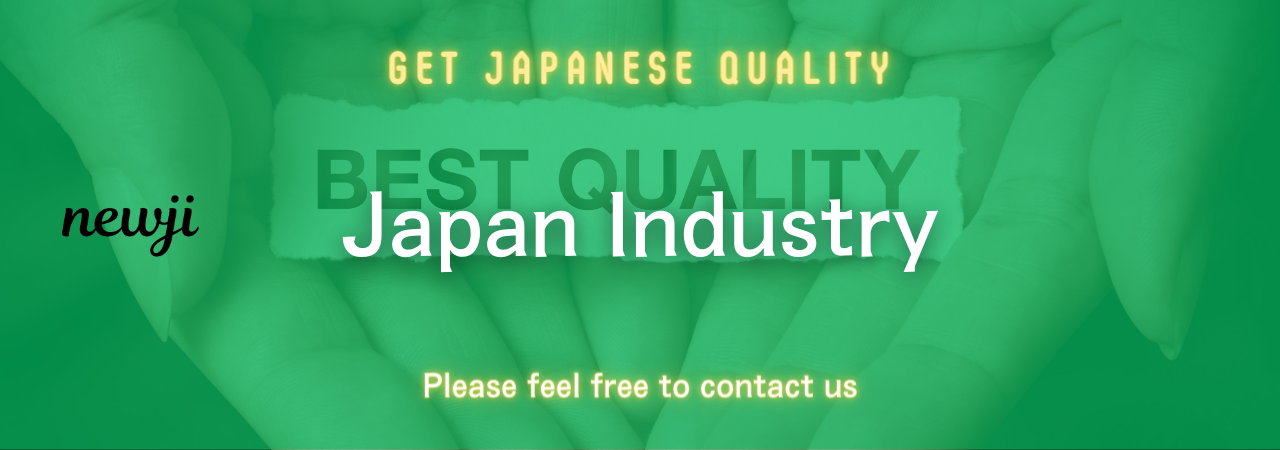
目次
Understanding Aluminum Deep Drawing Technology
Aluminum deep drawing is a highly advanced manufacturing process used to shape metal sheets into intricate forms.
This involves placing a sheet of aluminum into a die, and using a punch to transform it into the desired shape.
The technology is crucial in industries like automotive, aerospace, and electronics due to aluminum’s lightweight yet sturdy nature.
Deep drawing offers several advantages over other metal forming methods.
It allows for the production of strong, seamless parts without welding, minimizing weak spots.
This contributes to the durability of the final product and enhances performance in life-critical applications like automobile parts and aircraft components.
The aluminum deep drawing process is characterized by its cost-effectiveness for high-volume production.
Once the initial tooling and setup costs are incurred, the process becomes economical for batch production, delivering consistent and high-quality outputs.
Additionally, aluminum’s ability to withstand corrosion adds to the longevity and reliability of items produced through deep drawing.
Benefits of Collaborative Partnerships in Manufacturing
Incorporating new manufacturing technologies can be challenging.
However, collaborative partnerships simplify this process, fostering innovation and accelerating development.
Companies can join forces, share resources, and leverage each other’s expertise to push the boundaries of current capabilities.
Collaboration allows access to skills and technologies that might be too costly or time-consuming to develop independently.
Collaborative partnerships serve as platforms for pooling resources and reducing costs.
Shared investments in research and development, as well as manufacturing facilities, make high-tech endeavors more feasible.
Partnerships can also streamline the supply chain, enhance operational efficiencies, and lead to cost savings for all parties involved.
Moreover, working together with partners creates opportunities for stakeholder integration.
This integration ensures that there is a smooth transition from concept to product realization.
Partners can also co-create solutions, ensuring the customization of products to meet specific client needs and market demands.
Implementing New Technologies in Aluminum Deep Drawing
Integrating emerging technologies is vital for the evolution of aluminum deep drawing.
Innovations such as computer-aided design (CAD) and computer-aided manufacturing (CAM) are becoming standard practices.
These technologies enable precise designs and simulations, ensuring that potential defects are minimized before actual production begins.
Another emerging technology in the field is artificial intelligence (AI), which is increasingly used for predictive maintenance and process optimization.
AI systems can analyze data from the manufacturing line to predict equipment failures and optimize operations.
This results in reduced downtime and increased efficiency, benefiting both cost management and productivity.
Additionally, 3D printing is starting to make waves in aluminum manufacturing.
Though traditionally used for prototyping, it is now being explored for the manufacturing of unique tooling and bespoke components, offering flexibility that was previously unavailable.
By incorporating these technologies into aluminum deep drawing, manufacturers can improve product quality and reduce turnaround times, which are critical in a market where speed and precision matter immensely.
Challenges of Adopting New Technologies
The adoption of new technologies in aluminum deep drawing, while advantageous, also brings several challenges.
One of the primary obstacles is the initial setup cost.
Investments in new machinery, software, and training can be high, sometimes acting as a deterrent for small to medium-sized companies.
Another challenge is the steep learning curve associated with new technology adoption.
Training personnel to adeptly use advanced systems requires time and effort.
Without adequate training, there’s a risk of underusing the technology or, worse, making errors that could lead to costly production setbacks.
Furthermore, aligning new technologies with existing systems can present integration difficulties.
Ensuring compatibility between old and new machinery, software programs, and operational protocols is crucial to prevent disruptions and maintain productivity.
Despite these challenges, the benefits of technology adoption often outweigh the initial costs and effort.
The key is strategic planning, ensuring that new technologies align with company goals and bring value beyond their novelty.
The Future of Aluminum Deep Drawing
Looking ahead, the future of aluminum deep drawing is promising.
With consistent advancements in technology, the process will continue to become more efficient and flexible.
Increased automation and AI integration are likely to dominate the industry, bringing about faster adaptations to changing market needs.
Sustainability is also a growing focus in manufacturing, and aluminum deep drawing is no exception.
Efforts are underway to reduce waste, improve energy efficiency, and utilize recycled materials within the process.
These initiatives not only protect the environment but can also lead to cost reductions, further supporting the economic sustainability of the industries involved.
Collaborative partnerships between manufacturers and technology providers will remain critical in this evolution.
These partnerships will facilitate shared learning, drive innovation, and support the continued development of more advanced and sustainable manufacturing processes.
In conclusion, aluminum deep drawing technology, when paired with collaborative partnerships, represents a significant opportunity for modern manufacturing.
By adopting new technologies and working together, industries can create quality products efficiently and sustainably, meeting future market demands head-on.
資料ダウンロード
QCD調達購買管理クラウド「newji」は、調達購買部門で必要なQCD管理全てを備えた、現場特化型兼クラウド型の今世紀最高の購買管理システムとなります。
ユーザー登録
調達購買業務の効率化だけでなく、システムを導入することで、コスト削減や製品・資材のステータス可視化のほか、属人化していた購買情報の共有化による内部不正防止や統制にも役立ちます。
NEWJI DX
製造業に特化したデジタルトランスフォーメーション(DX)の実現を目指す請負開発型のコンサルティングサービスです。AI、iPaaS、および先端の技術を駆使して、製造プロセスの効率化、業務効率化、チームワーク強化、コスト削減、品質向上を実現します。このサービスは、製造業の課題を深く理解し、それに対する最適なデジタルソリューションを提供することで、企業が持続的な成長とイノベーションを達成できるようサポートします。
オンライン講座
製造業、主に購買・調達部門にお勤めの方々に向けた情報を配信しております。
新任の方やベテランの方、管理職を対象とした幅広いコンテンツをご用意しております。
お問い合わせ
コストダウンが利益に直結する術だと理解していても、なかなか前に進めることができない状況。そんな時は、newjiのコストダウン自動化機能で大きく利益貢献しよう!
(Β版非公開)