- お役立ち記事
- Utilization of CAE/digital twin for designers and practical points for utilizing it in strength analysis/strength design
月間76,176名の
製造業ご担当者様が閲覧しています*
*2025年3月31日現在のGoogle Analyticsのデータより
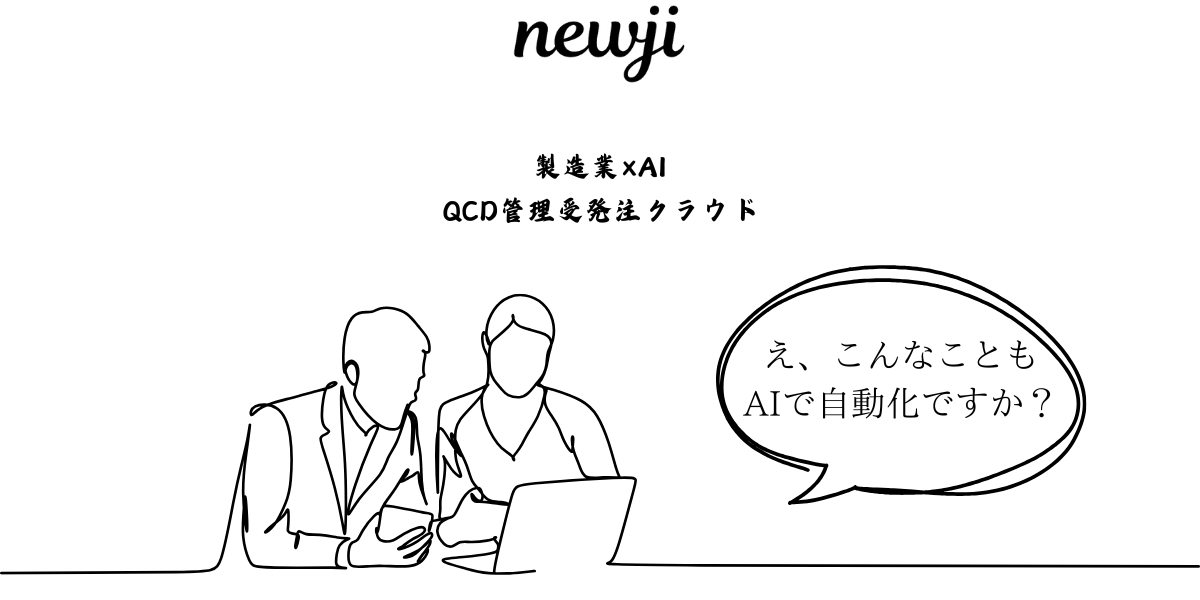
Utilization of CAE/digital twin for designers and practical points for utilizing it in strength analysis/strength design
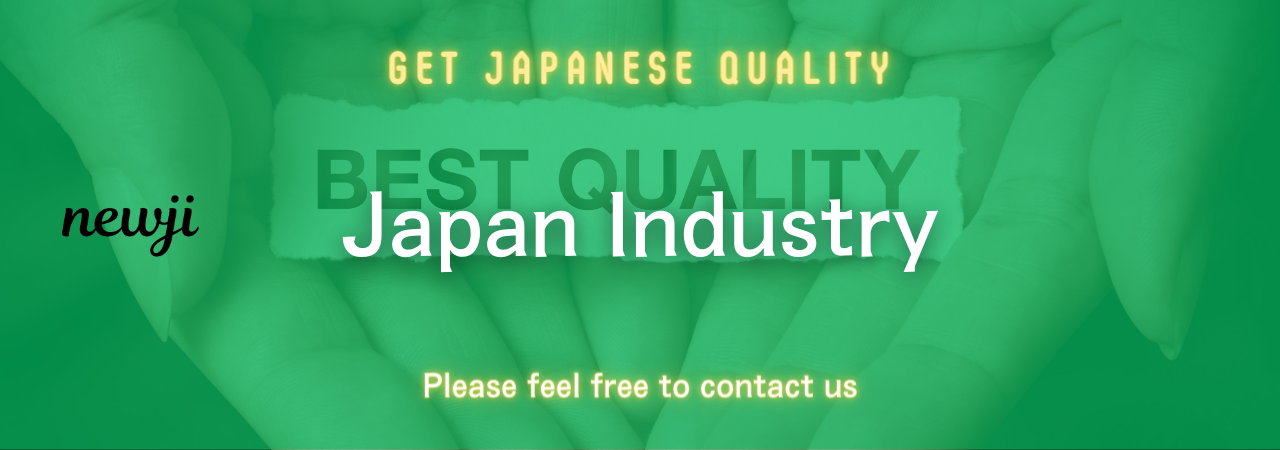
目次
Introduction to CAE and Digital Twin for Designers
In the modern world of design and engineering, Computer-Aided Engineering (CAE) and the concept of Digital Twin offer immense potential.
These technologies are reshaping how products are developed, focusing on simplifying processes and enhancing performance.
By understanding and utilizing these technologies, designers can create more efficient and innovative products.
Understanding CAE
CAE involves the use of computer software to improve engineering analysis tasks.
It includes tools like finite element analysis (FEA), computational fluid dynamics (CFD), and multibody dynamics (MBD).
These tools allow designers to simulate and evaluate a product’s performance before any physical prototype is made.
With CAE, designers can predict and improve the structural, thermal, and fluid behaviors of their products.
It fosters creativity by allowing experimentation without the need for multiple physical models.
This not only saves time but also reduces costs significantly.
The Importance of Digital Twin
The Digital Twin is a virtual model of a real-world object, allowing for interactive simulations and real-time monitoring.
It mirrors a physical asset digitally, capturing its behaviors and states.
By integrating data from sensors and IoT devices, Digital Twins provide a comprehensive overview of a product’s lifecycle.
Digital Twins are crucial in enhancing predictive maintenance, optimizing operations, and improving product designs.
For designers, this means having a near-real-time understanding of how a design will perform in real-world conditions.
This insight leads to more robust and reliable products and better decision-making.
Practical Points for Utilizing CAE in Strength Analysis
Defining Objectives
Before beginning any CAE analysis, it is essential to define the objectives.
Are you looking to optimize for weight, strength, or perhaps durability?
Clear objectives guide the simulation process and ensure the right data is captured and analyzed.
Model Validation
The precision of CAE simulations relies heavily on the accuracy of the initial model.
Before analyzing, ensure that the model represents the actual product accurately.
Utilizing real-world data to validate and refine simulations is crucial in achieving reliable outcomes.
Material Properties and Constraints
In strength analysis, understanding the material properties used in the design is vital.
Materials react differently under stress and deformation, which affects the simulation results.
Apply realistic constraints and loads in the CAE model for more accurate predictions.
Iterative Design Process
CAE allows for an iterative design approach.
Designers should continuously refine their models based on simulation results.
After each analysis, adjust the design parameters, re-evaluate, and iterate until the desired performance is achieved.
Practical Points for Utilizing Digital Twin in Strength Design
Data Integration and Real-Time Monitoring
Digital Twins require real-world data to function effectively.
Integrate sensor data and other relevant information to keep the virtual model up-to-date.
This real-time data feed ensures that the Digital Twin accurately mirrors its physical counterpart.
Simulation and Scenario Planning
Use Digital Twins to simulate different scenarios and stress conditions.
Consider how the product reacts to extreme environments or unusual stress.
Such insights can highlight potential design weaknesses and areas for improvement.
Predictive Maintenance
Digital Twins facilitate predictive maintenance by monitoring the product’s real-time performance.
Identify potential issues before they become real problems and enhance the product’s longevity and efficiency.
This proactive approach minimizes downtime and maintenance costs.
Enhancing Collaboration
Digital Twins offer a collaborative platform for various stakeholders.
Whether designers, engineers, or maintenance teams, everyone can access the same data and insights.
This collaboration ensures everyone is aligned and can contribute to the design’s improvement.
Conclusion
The utilization of CAE and Digital Twin technologies is transforming the landscape of design and strength analysis.
For designers, integrating these tools into their workflow offers profound benefits, from optimizing designs to reducing costs and enhancing product durability.
By understanding the practical points of using CAE and Digital Twins, designers can bring innovative, powerful products to market, ensuring sustainable and reliable performance for end-users.
As technology continues to evolve, embracing these tools is not just wise but essential for staying competitive in the ever-changing field of design and engineering.
Strive to continuously learn and adapt, leveraging CAE and Digital Twin for a sustainable and future-ready design approach.
資料ダウンロード
QCD管理受発注クラウド「newji」は、受発注部門で必要なQCD管理全てを備えた、現場特化型兼クラウド型の今世紀最高の受発注管理システムとなります。
ユーザー登録
受発注業務の効率化だけでなく、システムを導入することで、コスト削減や製品・資材のステータス可視化のほか、属人化していた受発注情報の共有化による内部不正防止や統制にも役立ちます。
NEWJI DX
製造業に特化したデジタルトランスフォーメーション(DX)の実現を目指す請負開発型のコンサルティングサービスです。AI、iPaaS、および先端の技術を駆使して、製造プロセスの効率化、業務効率化、チームワーク強化、コスト削減、品質向上を実現します。このサービスは、製造業の課題を深く理解し、それに対する最適なデジタルソリューションを提供することで、企業が持続的な成長とイノベーションを達成できるようサポートします。
製造業ニュース解説
製造業、主に購買・調達部門にお勤めの方々に向けた情報を配信しております。
新任の方やベテランの方、管理職を対象とした幅広いコンテンツをご用意しております。
お問い合わせ
コストダウンが利益に直結する術だと理解していても、なかなか前に進めることができない状況。そんな時は、newjiのコストダウン自動化機能で大きく利益貢献しよう!
(β版非公開)