- お役立ち記事
- Utilization of In-Mold Decoration (IMD) in Injection Molding
月間76,176名の
製造業ご担当者様が閲覧しています*
*2025年3月31日現在のGoogle Analyticsのデータより
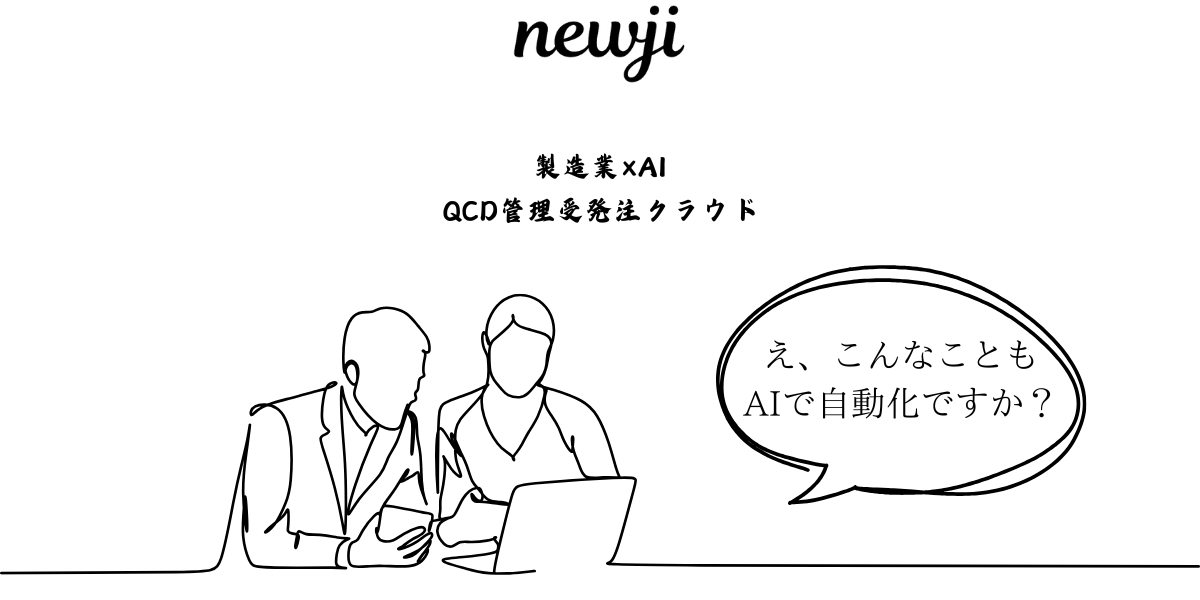
Utilization of In-Mold Decoration (IMD) in Injection Molding
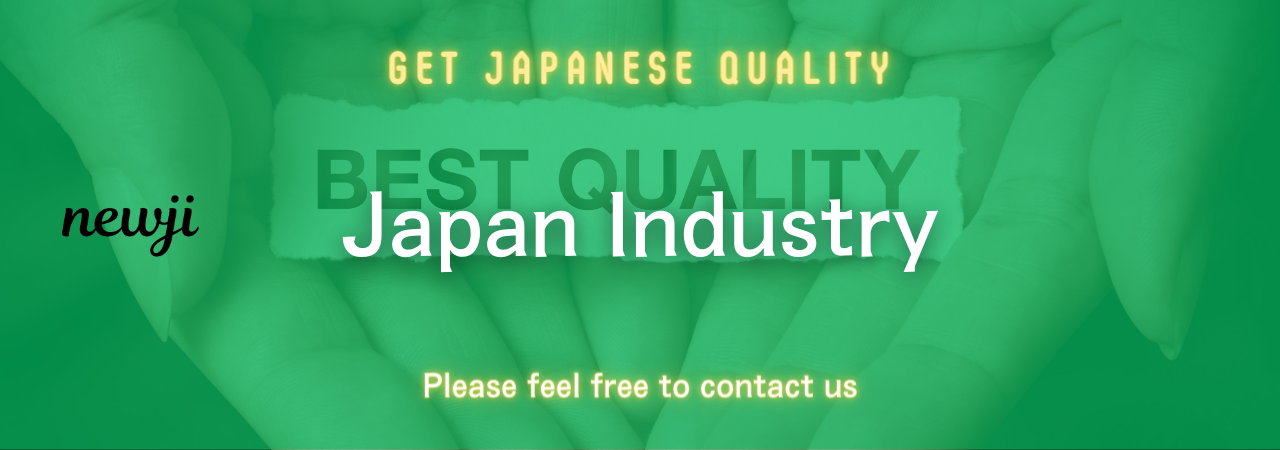
In the fascinating world of manufacturing, In-Mold Decoration (IMD) is quickly becoming a popular method for creating durable and attractive products. This technique is closely related to injection molding, a common process used for making plastic items. With its many benefits, IMD is adding a whole new dimension to how products are designed and produced. Let’s dive deeper into the topic to understand its applications, advantages, and process in injection molding.
目次
What is In-Mold Decoration (IMD)?
IMD, or In-Mold Decoration, is an advanced manufacturing technology that integrates decorative elements into the surface of plastic parts during the injection molding process. It involves placing a pre-printed and pre-formed film into the injection mold. When the plastic is injected into the mold, the decorative film adheres to the plastic, becoming an integral part of the final product’s surface.
The Process of In-Mold Decoration
The IMD process involves several key steps, each critical to achieving high-quality results.
Step 1: Film Printing
The first step in the IMD process is printing the desired design onto a special plastic film. This film is usually made from materials like polycarbonate, polyester, or other durable plastics that can withstand the pressures and temperatures of the molding process. The design might include anything from simple patterns to complex textures and multi-colored images.
Step 2: Film Forming
Once the design is printed on the film, it needs to be shaped to fit the contours of the mold. This step, known as thermoforming, involves heating the film and then pressing it into a mold to create a three-dimensional shape that matches the eventual product. Thermoforming helps to ensure that the design will fit perfectly within the injection mold without wrinkling or tearing.
Step 3: Placement in the Mold
After the film has been formed, it is carefully placed into the injection mold. The film needs to be aligned precisely so that the design is positioned correctly on the final product. Accurate placement is essential for achieving a high-quality appearance.
Step 4: Injection Molding
Now comes the injection molding part of the process. Molten plastic is injected into the mold under high pressure. As the plastic flows into the mold, it bonds with the decorative film, embedding the design onto the surface of the product. After the plastic has cooled and solidified, the mold can be opened, and the decorated part can be removed.
Advantages of In-Mold Decoration
IMD offers numerous advantages that make it an attractive option for manufacturers and designers.
Enhanced Durability
One of the most significant benefits of IMD is the enhanced durability it provides. Since the decorative elements are embedded within the plastic part, they are protected from scratches, wear, and fading. This makes IMD products ideal for applications where the surface is likely to encounter frequent use or harsh conditions.
Stunning Aesthetics
IMD allows for highly detailed and vibrant designs that can greatly enhance the visual appeal of a product. Whether it’s a smartphone cover with intricate patterns or an automobile dashboard with elegant textures, IMD enables manufacturers to create stunning aesthetics that stand out in the market.
Cost-Effective Production
By incorporating decoration directly into the molding process, IMD can reduce the need for additional finishing steps, such as painting or adhesive application. This streamlining of production helps to lower manufacturing costs and increase efficiency. The reduction in production steps also minimizes the likelihood of defects, leading to higher yield rates and less waste.
Design Flexibility
Another advantage of IMD is the flexibility it offers in terms of design options. Manufacturers can easily modify designs by simply changing the printed film. This adaptability allows for quick customization and updating of product designs to meet market trends and customer preferences.
Eco-Friendly Option
IMD can contribute to more sustainable manufacturing practices. By eliminating the need for additional surface finishing processes that often involve toxic chemicals and by reducing waste, IMD aligns with eco-friendly production methodologies.
Applications of In-Mold Decoration
IMD is finding applications in various industries due to its versatility and benefits.
Consumer Electronics
In the consumer electronics industry, IMD is widely used for products like smartphones, tablets, and remote controls. The ability to produce high-quality, scratch-resistant surfaces is particularly beneficial for these items, which tend to experience a lot of wear and tear.
Automotive Industry
The automotive sector utilizes IMD for both interior and exterior components. Dashboard panels, air vents, and even exterior trims can be decorated using IMD processes. The technology’s ability to withstand harsh environmental conditions makes it suitable for automotive applications.
Appliances
Home appliances, such as washing machines, microwaves, and refrigerators, often feature IMD technology. The durability and aesthetic appeal of IMD make it an ideal choice for these high-use items.
Medical Devices
In the medical field, IMD is used for creating user-friendly interfaces and durable parts for various devices. The anti-microbial properties can also be incorporated into the films, making them more suitable for medical applications.
Challenges and Considerations
Despite its many advantages, IMD also presents some challenges that manufacturers must consider.
Cost of Initial Setup
The initial setup cost for IMD can be higher compared to traditional methods. Specialized equipment for printing, forming, and aligning the decorative films is required. However, the long-term benefits, including reduced production costs and enhanced product durability, often outweigh these initial expenses.
Complex Design Alignments
Ensuring precise alignment of the decorative film within the mold can be challenging, especially for complex designs or multi-part assemblies. Advanced techniques and careful calibration are required to achieve accurate placement consistently.
Material Compatibility
Compatibility between the plastic used for the product and the decorative film must be ensured. Not all plastics work well with all types of films, which can limit material choices. Selecting the right combination of materials is crucial for achieving the best results.
In conclusion, In-Mold Decoration (IMD) is a powerful technology that adds value to injection-molded products. By integrating decorative elements directly into the manufacturing process, IMD offers enhanced durability, stunning aesthetics, and cost-effective production. Although it presents certain challenges, the benefits make it a compelling choice for industries ranging from consumer electronics to automotive and medical devices. With continued advancements in materials and techniques, the future of IMD in injection molding looks bright.
資料ダウンロード
QCD管理受発注クラウド「newji」は、受発注部門で必要なQCD管理全てを備えた、現場特化型兼クラウド型の今世紀最高の受発注管理システムとなります。
ユーザー登録
受発注業務の効率化だけでなく、システムを導入することで、コスト削減や製品・資材のステータス可視化のほか、属人化していた受発注情報の共有化による内部不正防止や統制にも役立ちます。
NEWJI DX
製造業に特化したデジタルトランスフォーメーション(DX)の実現を目指す請負開発型のコンサルティングサービスです。AI、iPaaS、および先端の技術を駆使して、製造プロセスの効率化、業務効率化、チームワーク強化、コスト削減、品質向上を実現します。このサービスは、製造業の課題を深く理解し、それに対する最適なデジタルソリューションを提供することで、企業が持続的な成長とイノベーションを達成できるようサポートします。
製造業ニュース解説
製造業、主に購買・調達部門にお勤めの方々に向けた情報を配信しております。
新任の方やベテランの方、管理職を対象とした幅広いコンテンツをご用意しております。
お問い合わせ
コストダウンが利益に直結する術だと理解していても、なかなか前に進めることができない状況。そんな時は、newjiのコストダウン自動化機能で大きく利益貢献しよう!
(β版非公開)