- お役立ち記事
- Utilization of injection molding data and defect detection technology
月間77,185名の
製造業ご担当者様が閲覧しています*
*2025年2月28日現在のGoogle Analyticsのデータより
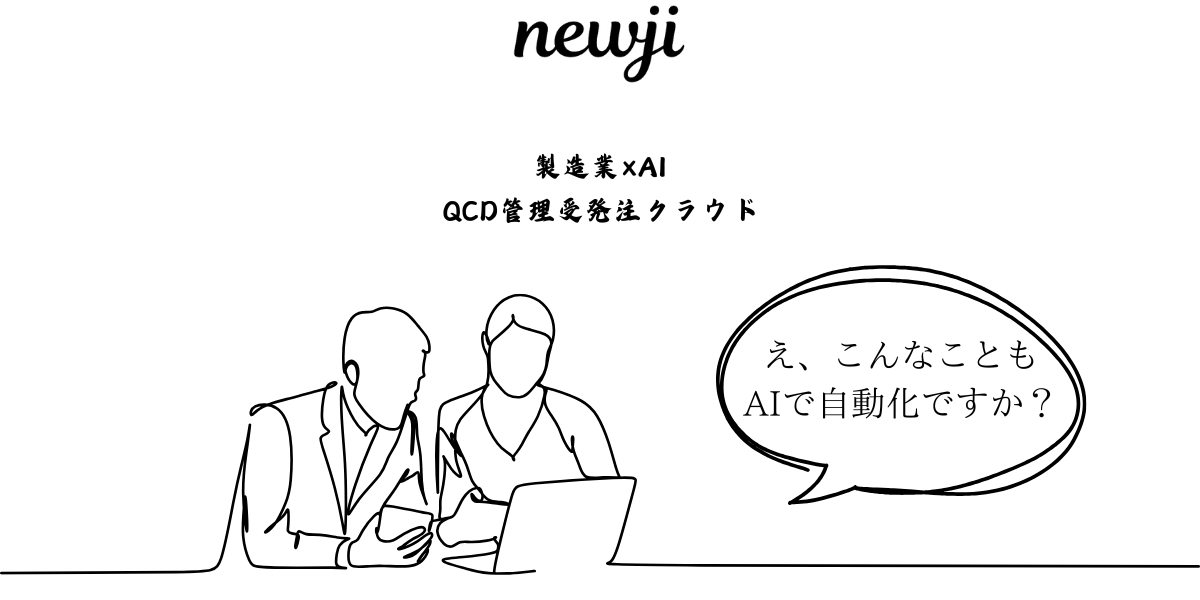
Utilization of injection molding data and defect detection technology
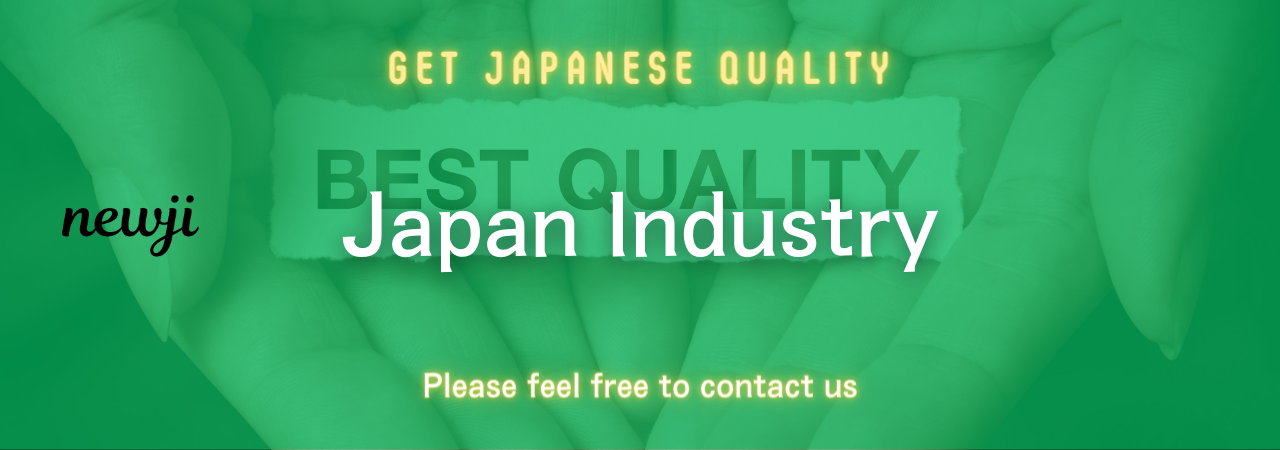
目次
Understanding Injection Molding
Injection molding is a crucial manufacturing process used to produce a wide range of plastic parts and products.
The process involves injecting molten material into a mold, where it cools and hardens to the shape of the mold cavity.
This method is widely used for its efficiency and ability to produce high volumes of products with consistent quality.
The materials typically used in injection molding include thermoplastics, thermosetting polymers, and elastomers.
Each material has unique properties that make it suitable for specific applications.
For instance, thermoplastics can be reheated and remolded, making them versatile and widely used across industries.
The Importance of Data in Injection Molding
Utilizing data effectively can significantly enhance the injection molding process.
Data collected during the process can provide insights into machine performance, product quality, and process efficiency.
Analyzing this data allows manufacturers to optimize production parameters, reduce cycle times, and improve product quality.
Data such as temperature, pressure, and injection speed are critical in ensuring that each molded part meets the desired specifications.
By monitoring these parameters, manufacturers can quickly identify and address any deviations that may lead to defects or inefficiencies.
Defect Detection in Injection Molding
Defect detection is a vital component of quality control in injection molding.
Common defects include warping, sink marks, short shots, and flash.
Timely detection and correction of these defects can prevent costly production delays and waste.
Implementing advanced defect detection technologies, such as machine learning algorithms and computer vision, can significantly improve the accuracy and speed of defect identification.
These technologies analyze images of molded parts in real-time, automatically identifying any deviations from the ideal model.
Machine Learning in Defect Detection
Machine learning algorithms are increasingly being used to enhance defect detection in injection molding.
These algorithms can learn from historical data and identify patterns that indicate potential defects.
By analyzing large datasets, machine learning models can quickly and accurately predict when and where defects are likely to occur.
This predictive capability enables manufacturers to take preemptive action to mitigate defects before they impact production.
Over time, machine learning models can improve their accuracy as they are exposed to more data, leading to continual improvement in defect detection.
Computer Vision for Quality Control
Computer vision involves using cameras and image processing algorithms to inspect molded parts for defects.
This technology allows for fast and precise quality assessments without the need for human intervention.
High-resolution cameras capture images of each part, and software algorithms analyze these images to detect any anomalies or defects.
The main advantage of computer vision is its ability to operate continuously and provide consistent and objective quality assessments.
It reduces the likelihood of human error and allows for more frequent and detailed inspections.
Integrating Data and Technology for Better Outcomes
Integrating data analytics and advanced defect detection technologies can lead to significant improvements in the injection molding process.
Real-time data collection and analysis enable manufacturers to make informed decisions that enhance efficiency and product quality.
Predictive analytics can identify potential issues before they arise, allowing for proactive maintenance and process adjustments.
By continuously monitoring and analyzing data, manufacturers can achieve a higher level of operational excellence and competitiveness.
Future Trends in Injection Molding
As technology advances, the injection molding industry is likely to see further innovations.
The integration of the Internet of Things (IoT) and Industry 4.0 technologies will lead to smarter, more automated production processes.
IoT devices can provide real-time data and insights, enabling better monitoring and optimization of the injection molding process.
Additionally, artificial intelligence (AI) and machine learning will continue to play significant roles in enhancing defect detection and process optimization.
These technologies will enable more efficient production lines and create opportunities for customized, on-demand manufacturing.
In conclusion, the strategic utilization of data and defect detection technologies in injection molding offers numerous benefits.
By embracing these advancements, manufacturers can improve quality, reduce waste, and enhance overall productivity.
As the industry continues to evolve, the focus on leveraging data and technology will remain paramount in achieving successful and sustainable manufacturing processes.
資料ダウンロード
QCD管理受発注クラウド「newji」は、受発注部門で必要なQCD管理全てを備えた、現場特化型兼クラウド型の今世紀最高の受発注管理システムとなります。
ユーザー登録
受発注業務の効率化だけでなく、システムを導入することで、コスト削減や製品・資材のステータス可視化のほか、属人化していた受発注情報の共有化による内部不正防止や統制にも役立ちます。
NEWJI DX
製造業に特化したデジタルトランスフォーメーション(DX)の実現を目指す請負開発型のコンサルティングサービスです。AI、iPaaS、および先端の技術を駆使して、製造プロセスの効率化、業務効率化、チームワーク強化、コスト削減、品質向上を実現します。このサービスは、製造業の課題を深く理解し、それに対する最適なデジタルソリューションを提供することで、企業が持続的な成長とイノベーションを達成できるようサポートします。
製造業ニュース解説
製造業、主に購買・調達部門にお勤めの方々に向けた情報を配信しております。
新任の方やベテランの方、管理職を対象とした幅広いコンテンツをご用意しております。
お問い合わせ
コストダウンが利益に直結する術だと理解していても、なかなか前に進めることができない状況。そんな時は、newjiのコストダウン自動化機能で大きく利益貢献しよう!
(β版非公開)