- お役立ち記事
- Utilization of multi-axis machining centers and improvement of machining accuracy that processing engineers in the precision machinery industry should know
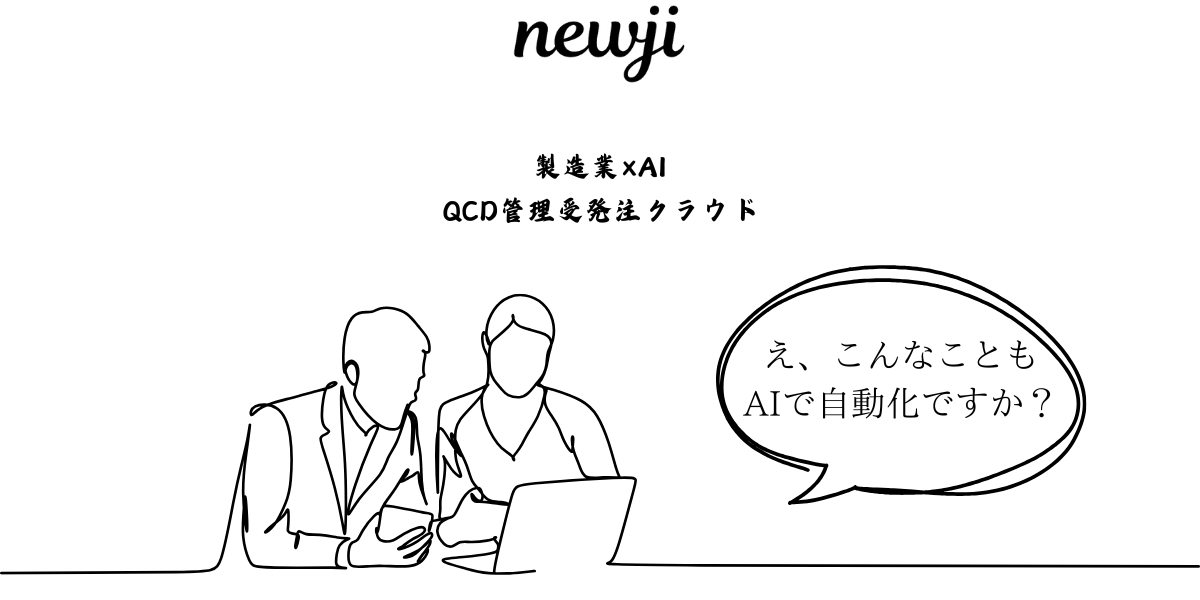
Utilization of multi-axis machining centers and improvement of machining accuracy that processing engineers in the precision machinery industry should know
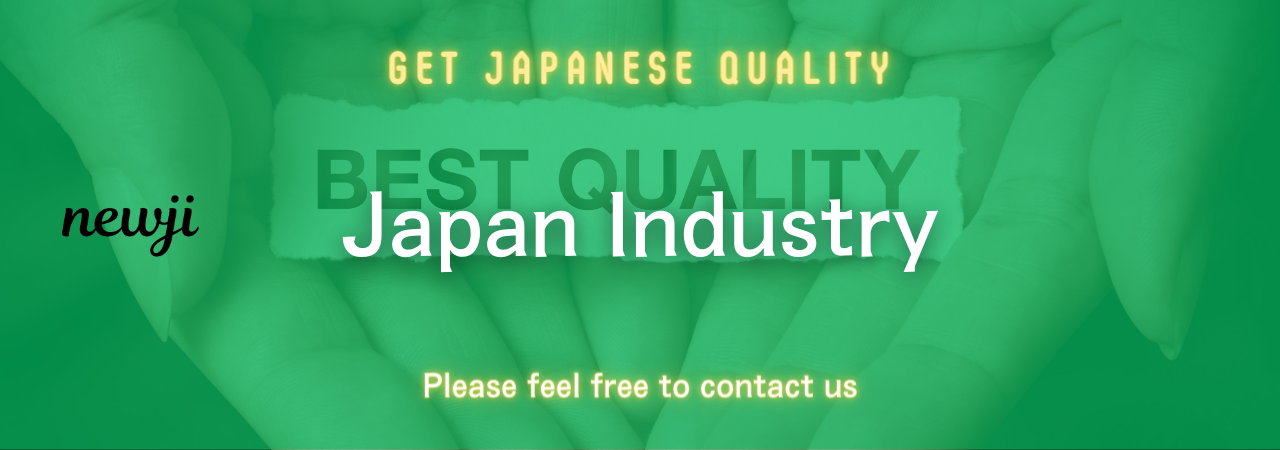
目次
Understanding Multi-Axis Machining Centers
Multi-axis machining centers have revolutionized the precision machinery industry by offering advanced capabilities in terms of precision, speed, and complexity of workpieces produced.
These machines operate on multiple axes, allowing for intricate parts to be created with fewer setups and improved accuracy.
For processing engineers, understanding how to leverage these machines effectively is crucial for enhancing productivity and maintaining high standards in manufacturing.
What Are Multi-Axis Machining Centers?
Multi-axis machining centers are advanced CNC machines that typically operate on three or more axes.
While traditional machines like lathes and mills might operate on up to three axes, multi-axis centers can operate on four, five, or even six axes.
This capability allows them to handle complex geometries and intricate designs that would be challenging or impossible with more limited machinery.
Benefits of Multi-Axis Machining
Enhanced Accuracy and Precision
One of the main advantages of using multi-axis machining centers is their potential for increased accuracy.
By reducing the need for multiple setups and repositioning of the workpiece, these machines can achieve tighter tolerances and higher precision.
This is vital in industries where even the slightest deviation can result in significant issues with part functionality or safety.
Increased Efficiency
Multi-axis machines can perform multiple operations in a single setup, saving time and reducing labor costs.
This efficiency leads to faster production times, which can be a significant competitive advantage in a fast-paced manufacturing environment.
By minimizing the number of setups required, manufacturers can reduce downtime and enhance throughput.
Complex Geometries
With the ability to move and rotate a workpiece along multiple axes, these machines excel at creating complex shapes and features.
This capability is particularly beneficial in industries such as aerospace, automotive, and medical devices, where intricate and precise components are standard.
Improving Machining Accuracy
Regular Calibration
To maintain the utmost accuracy, regular calibration of the machining centers is essential.
Calibration ensures that all axes operate correctly and precisely, reducing the risk of errors during the manufacturing process.
Routine checks should be part of the maintenance schedule to ensure consistent performance.
Precision Tooling
The quality of the tools used in machining can significantly impact the accuracy of the final product.
Processing engineers should ensure that they use high-quality, well-maintained tools.
Investing in precision tooling can improve the surface finish and dimensional accuracy of the parts produced.
Optimizing Thermal Stability
Thermal fluctuations can cause material expansion or contraction, affecting machining accuracy.
Engineers should manage the thermal environment around the machining centers to minimize its impact.
This can be achieved by controlling the ambient temperature, using coolants judiciously, and ensuring machines are not operating beyond their optimal thermal range.
Implementing Advanced Software
Modern multi-axis machining centers often come with sophisticated software that can optimize machining paths and improve efficiency.
By leveraging these tools, engineers can simulate the machining process to identify potential issues and make necessary adjustments before actual production.
This can significantly enhance the accuracy and quality of the parts produced.
Challenges and Considerations
High Initial Investment
The advanced technology and capabilities of multi-axis machining centers come at a cost.
For some companies, the initial investment may be substantial.
However, the long-term benefits in terms of efficiency, precision, and reduced labor costs often justify this expenditure.
Skill Requirements
Operating multi-axis machining centers requires a skilled workforce familiar with CNC programming and machine operations.
Investing in training and development is crucial to ensure that operators can make the most of the machine’s capabilities without compromising accuracy or productivity.
Maintenance and Upkeep
To keep multi-axis machining centers functioning at their best, regular maintenance and upkeep are necessary.
Preventative maintenance can help identify and address issues before they become significant problems, thus avoiding unnecessary downtime.
Conclusion
Utilizing multi-axis machining centers is transformative for the precision machinery industry, offering unmatched precision, efficiency, and the ability to tackle complex manufacturing challenges.
For processing engineers, embracing these machines and understanding their operation can lead to significant improvements in productivity and product quality.
By focusing on key areas like calibration, tooling, and thermal management, engineers can further enhance machining accuracy, ensuring the production of superior components in any industry.
資料ダウンロード
QCD調達購買管理クラウド「newji」は、調達購買部門で必要なQCD管理全てを備えた、現場特化型兼クラウド型の今世紀最高の購買管理システムとなります。
ユーザー登録
調達購買業務の効率化だけでなく、システムを導入することで、コスト削減や製品・資材のステータス可視化のほか、属人化していた購買情報の共有化による内部不正防止や統制にも役立ちます。
NEWJI DX
製造業に特化したデジタルトランスフォーメーション(DX)の実現を目指す請負開発型のコンサルティングサービスです。AI、iPaaS、および先端の技術を駆使して、製造プロセスの効率化、業務効率化、チームワーク強化、コスト削減、品質向上を実現します。このサービスは、製造業の課題を深く理解し、それに対する最適なデジタルソリューションを提供することで、企業が持続的な成長とイノベーションを達成できるようサポートします。
オンライン講座
製造業、主に購買・調達部門にお勤めの方々に向けた情報を配信しております。
新任の方やベテランの方、管理職を対象とした幅広いコンテンツをご用意しております。
お問い合わせ
コストダウンが利益に直結する術だと理解していても、なかなか前に進めることができない状況。そんな時は、newjiのコストダウン自動化機能で大きく利益貢献しよう!
(Β版非公開)