- お役立ち記事
- Utilization of resin molding technology in joint development of CO2-derived plastic products
月間77,185名の
製造業ご担当者様が閲覧しています*
*2025年2月28日現在のGoogle Analyticsのデータより
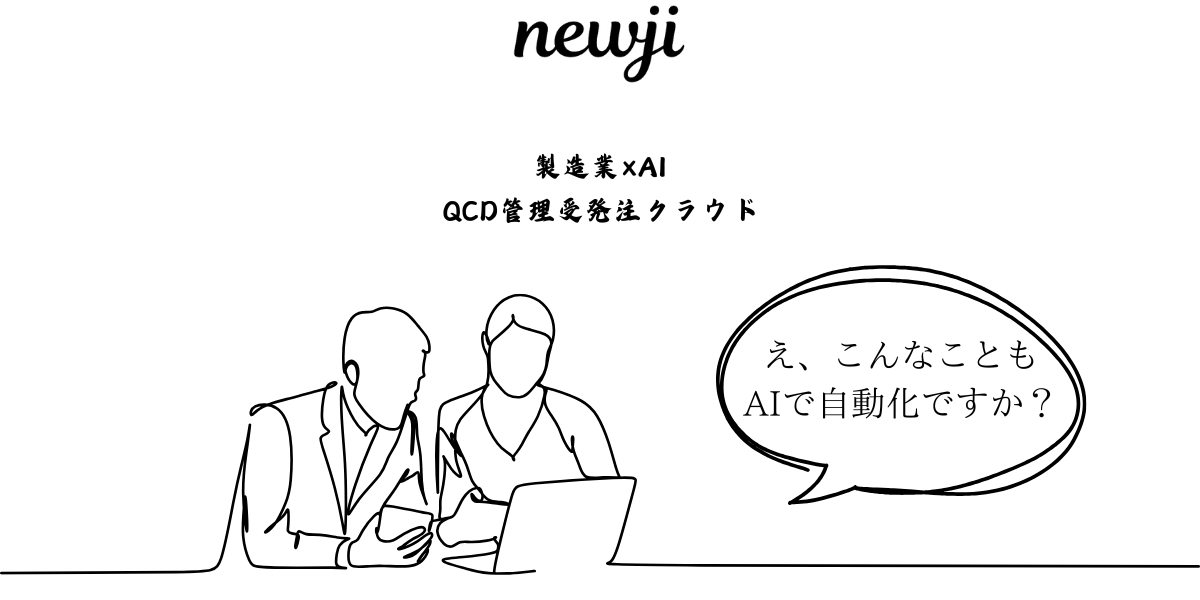
Utilization of resin molding technology in joint development of CO2-derived plastic products
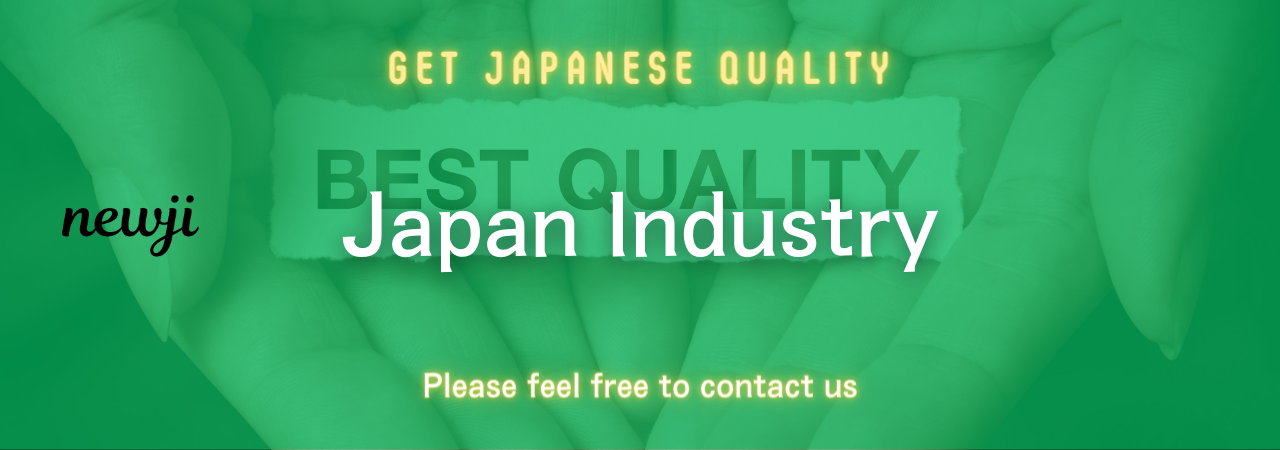
Resin molding technology has charged its way into the future, paving new paths in the world of manufacturing, especially when combined with sustainable materials like CO2-derived plastics.
目次
Understanding Resin Molding Technology
Resin molding involves creating industrial parts or finished products by shaping a resin mixture into a desired form using a mold.
This technique is revered for its versatility, allowing manufacturers to produce complex geometries that traditional manufacturing methods struggle to achieve.
The molds can be made from materials like steel, aluminum, or silicone, depending on the required specifications and end-product purposes.
Molding provides several benefits such as cost efficiency, time savings, and precision.
These plus-points have made it incredibly popular in industries ranging from automotive and healthcare to electronics and aerospace.
The Science of CO2-Derived Plastics
CO2-derived plastics offer an eco-friendly alternative to conventional plastics by capturing carbon dioxide emissions and reusing them to create polymers.
This cutting-edge approach not only reduces carbon footprints but also diminishes reliance on fossil fuels for plastic production.
Through processes such as catalytic conversion, captured CO2 can be transformed into useful components for creating plastics.
These plastics retain similar qualities to traditional ones, including durability and versatility, making them viable substitutes in most applications.
The development of CO2-derived plastics provides a path toward a more sustainable future by addressing environmental concerns while meeting industry demands.
Joint Development: A Collaborative Approach
The journey of integrating resin molding technology with CO2-derived plastics hinges on collaborative efforts involving multiple stakeholders.
Joint development connects material scientists, engineers, manufacturers, and environmental advocates to consolidate their expertise in refining product design and production processes.
Collaboration allows the combination of resins with CO2-derived components in a way that maximizes the potentials of both technologies.
It enables the development of innovative applications, ensuring that products not only meet industry standards but also adhere to environmental guidelines.
For instance, the automotive sector can leverage these advancements to produce lighter, more fuel-efficient vehicles without compromising strength or safety standards.
Benefits of Joint Development
The partnership between resin molding technology and CO2-derived plastics is not just about combining technology — it’s about redefining the production landscape.
This alliance fosters a culture of innovation, where each contributor’s knowledge propels us toward more effective, sustainable manufacturing solutions.
The benefits of such collaboration are manifold:
– **Reduced Environmental Impact:** By using captured CO2, we alleviate environmental pressures and make headway in combating climate change.
– **Market Expansion:** Products born from this joint development can cater to eco-conscious consumers, opening new markets and enhancing brand reputations.
– **Innovation and Flexibility:** Joint development encourages continuous improvement and adaptation of technologies to fulfill evolving consumer needs.
Addressing Challenges Together
As promising as it sounds, this joint venture comes with its own set of challenges.
The integration of CO2-derived plastics with resin molding technology requires a seamless meld of chemical engineering and industrial design, necessitating precise control over material properties and production processes.
Quality control is another significant aspect where collaboration plays a vital role.
Establishing stringent quality standards ensures that final products consistently meet both performance and environmental criteria.
Moreover, transitioning from conventional materials presents logistical demands such as reconfiguring supply chains and adapting existing manufacturing setups.
Collective problem-solving can help overcome these hurdles, facilitating smoother transitions within the industry.
Real-World Applications and Forward-Thinking Solutions
Several industries are already benefitting from the intersection of resin molding technology and CO2-derived plastics.
In the packaging sector, companies are producing eco-friendly containers and bottles that not only minimize waste but also reduce the overall carbon footprint during production.
These sustainable packaging solutions find their way into consumer goods, impacting everyday lives by promoting green habits.
The aerospace industry is exploring lightweight parts crafted from CO2-derived plastics, enhancing fuel efficiency while maintaining structural integrity.
In healthcare, medical devices and equipment can be manufactured with improved sustainability, reducing costs and environmental impacts without sacrificing functionality.
The future promises more innovations as industries adopt these advanced methods for various applications, harnessing the robust potential of resin molding coupled with carbon capture technologies.
Conclusion
The utilization of resin molding technology in the joint development of CO2-derived plastic products demonstrates the possibilities when innovation meets sustainability.
This collaborative venture is not only a boon to businesses but also to the planet, as it promises to reduce carbon emissions while delivering high-quality products that meet consumer demands and environmental standards.
Looking ahead, as the collaboration deepens and technologies become more refined, we anticipate a transformation across industries.
Adopting these approaches universally can propel us towards a cleaner, greener future — one molded from the very challenges we seek to overcome.
資料ダウンロード
QCD管理受発注クラウド「newji」は、受発注部門で必要なQCD管理全てを備えた、現場特化型兼クラウド型の今世紀最高の受発注管理システムとなります。
ユーザー登録
受発注業務の効率化だけでなく、システムを導入することで、コスト削減や製品・資材のステータス可視化のほか、属人化していた受発注情報の共有化による内部不正防止や統制にも役立ちます。
NEWJI DX
製造業に特化したデジタルトランスフォーメーション(DX)の実現を目指す請負開発型のコンサルティングサービスです。AI、iPaaS、および先端の技術を駆使して、製造プロセスの効率化、業務効率化、チームワーク強化、コスト削減、品質向上を実現します。このサービスは、製造業の課題を深く理解し、それに対する最適なデジタルソリューションを提供することで、企業が持続的な成長とイノベーションを達成できるようサポートします。
製造業ニュース解説
製造業、主に購買・調達部門にお勤めの方々に向けた情報を配信しております。
新任の方やベテランの方、管理職を対象とした幅広いコンテンツをご用意しております。
お問い合わせ
コストダウンが利益に直結する術だと理解していても、なかなか前に進めることができない状況。そんな時は、newjiのコストダウン自動化機能で大きく利益貢献しよう!
(β版非公開)