- お役立ち記事
- Utilization of simulation in chemical processes and application to effective process design and scale-up
Utilization of simulation in chemical processes and application to effective process design and scale-up
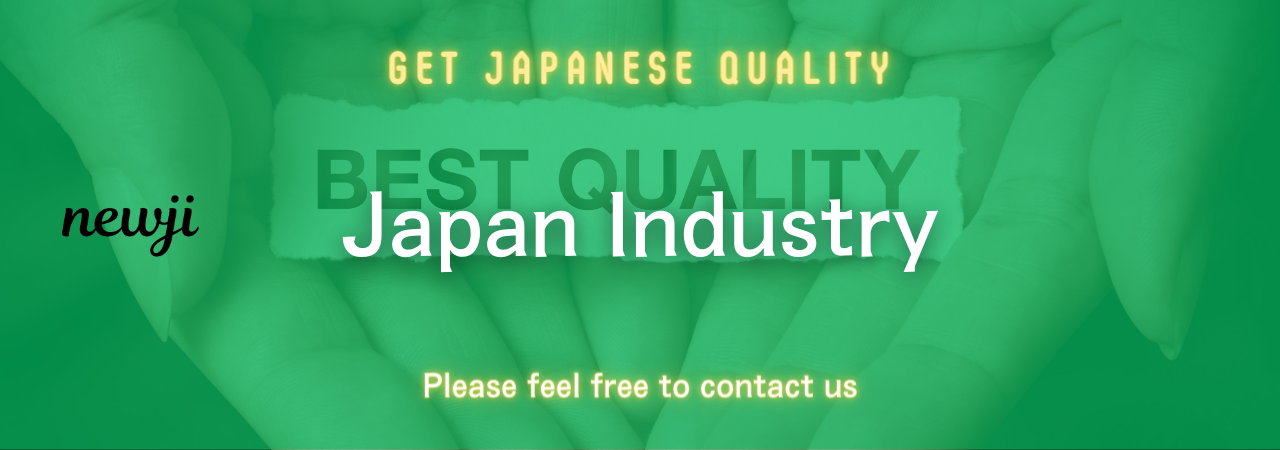
目次
Introduction to Simulation in Chemical Processes
Simulation in chemical processes is a technological marvel that allows scientists, engineers, and researchers to understand complex chemical reactions and systems without physically conducting experiments initially.
This technique involves using computer software to model the physical and chemical processes occurring within a chemical reaction or a manufacturing process.
Such simulations help in predicting the behavior of these systems under various conditions which becomes crucial in terms of planning and optimization.
Why Use Simulations in Chemical Processes?
The main advantage of using simulations in chemical processes is the ability to test various scenarios and conditions without the physical risks and costs associated with real-life experiments.
Simulations save time and resources by allowing researchers to predict the outcomes of their experiments.
Moreover, simulations facilitate understanding of the intricate details of chemical processes, often revealing insights that are hard to obtain through traditional methods.
They also help in identifying safe and efficient ways to scale up processes, leading to improvements in design and operation.
Simulations can reduce the environmental impact by minimizing waste and energy consumption, making them an environmentally friendly option.
Applications in Effective Process Design
One of the primary applications of simulation in chemical processes is in designing efficient systems for manufacturing chemicals.
By utilizing modeling software, engineers can design systems that optimize flow dynamics, heat transfer, and material use, which are fundamental aspects of chemical engineering.
Simulations play a pivotal role in process design as they allow for detailed analysis and testing of different setups, equipment arrangements, and production schedules.
This provides the flexibility to refine designs before the physical prototype is produced, ensuring the final design is both efficient and cost-effective.
Process simulations help in identifying potential bottlenecks and issues in the manufacturing process, which can be addressed before full-scale production, thus saving time and money.
Simulation in Scale-Up Processes
Scaling up a chemical process is a significant challenge that involves transitioning from laboratory (or pilot) scale to industrial scale.
Simulations assist in predicting how a chemical process will behave as it is scaled up, identifying any potential issues that could arise.
By using detailed computational models, engineers can better understand the thermodynamics, kinetics, and transport phenomena involved in scaling up chemical processes.
For instance, simulations can offer insights into problems such as maintaining temperature and pressure across large reactor volumes or dealing with changes in mixing patterns when the volume increases.
Through simulations, companies can avoid costly errors and delays, ensuring smoother transitions to larger-scale production.
The Process of Simulation
The simulation process begins with gathering and inputting accurate chemical and physical property data into simulation software.
The software then uses mathematical models and equations to emulate chemical reactions and process dynamics based on the input parameters.
For an accurate simulation, the data should include reaction kinetics, material properties, phase equilibria, and thermodynamic properties, among others.
Once the model is built, simulations can be conducted under different scenarios to explore potential outcomes.
Engineers refine the model by comparing simulation results with experimental data, thus ensuring its accuracy and reliability.
Tools and Software
Several software tools are available for chemical process simulation, such as Aspen Plus, PRO/II, and HYSYS.
These tools provide a graphical user interface for building process models and support a wide range of chemical processes and reactors.
They offer built-in libraries with thousands of chemical components and thermodynamic property packages that simplify the simulation setup.
Moreover, these softwares allow for dynamic simulations, where time-dependent changes in processes can be analyzed, offering deeper insights.
Challenges and Limitations
Despite the many advantages, simulation has its own set of challenges and limitations.
Accuracy in simulation heavily relies on the quality and preciseness of the input data and parameters.
Errors or approximations in data can lead to significant discrepancies between the simulation outcomes and real-world results.
Another challenge is the complexity of biological and chemical reactions which sometimes cannot be fully captured by mathematical models.
This can limit the effectiveness of a simulation, necessitating further refinement and validation stages.
Future Outlook
The future of simulations in chemical processes looks promising as technology continues to advance.
With the continual development of more sophisticated and powerful algorithms, simulation software is becoming more accurate and capable of handling more complex systems.
Artificial Intelligence and Machine Learning are also being integrated into chemical process simulations, enhancing predictive capabilities.
These technologies can analyze large sets of data to uncover patterns and insights that traditional methods may not detect.
Additionally, simulations are expected to play a critical role in facilitating sustainable and green chemistry practices by optimizing processes to reduce waste, energy consumption, and environmental impact.
Conclusion
Simulation in chemical processes represents a valuable tool that revolutionizes the way researchers and professionals approach design and scale-up in the chemical industry.
By leveraging simulation, organizations can optimize processes, minimize costs, improve safety, and achieve sustainability goals.
As technology evolves, simulation capabilities will expand, leading to even greater advances in chemical process engineering.
With these advancements, the chemical industry can continue to innovate while addressing global challenges, creating a more sustainable future.
資料ダウンロード
QCD調達購買管理クラウド「newji」は、調達購買部門で必要なQCD管理全てを備えた、現場特化型兼クラウド型の今世紀最高の購買管理システムとなります。
ユーザー登録
調達購買業務の効率化だけでなく、システムを導入することで、コスト削減や製品・資材のステータス可視化のほか、属人化していた購買情報の共有化による内部不正防止や統制にも役立ちます。
NEWJI DX
製造業に特化したデジタルトランスフォーメーション(DX)の実現を目指す請負開発型のコンサルティングサービスです。AI、iPaaS、および先端の技術を駆使して、製造プロセスの効率化、業務効率化、チームワーク強化、コスト削減、品質向上を実現します。このサービスは、製造業の課題を深く理解し、それに対する最適なデジタルソリューションを提供することで、企業が持続的な成長とイノベーションを達成できるようサポートします。
オンライン講座
製造業、主に購買・調達部門にお勤めの方々に向けた情報を配信しております。
新任の方やベテランの方、管理職を対象とした幅広いコンテンツをご用意しております。
お問い合わせ
コストダウンが利益に直結する術だと理解していても、なかなか前に進めることができない状況。そんな時は、newjiのコストダウン自動化機能で大きく利益貢献しよう!
(Β版非公開)